Since being rolled out by the Sumerians in around 3500 BC, the wheel has been constantly re-invented. Styling flexibility, reduced weight and high quality are just some of the requirements automakers expect from their wheel suppliers today, writes Matthew Beecham.
A wheel story
Although the North American and European aluminium wheel market has grown over the past decade, the pace of growth has slowed recently and is set to stabilise over the next few years. Advances in the use of steel, supported by industry groups such the American Iron and Steel Institute (AISI), has meant that manufacturers of steel wheels can meet alloy wheel designs head on. According to the AISI, steel wheels are making a comeback as automakers realise they can save up to US$200 per vehicle without sacrifice to quality or performance. Ford, DaimlerChrysler, General Motors are among those switching to steel wheels thanks to the development of new high-strength steels and improved design and simulation technology, says the AISI. “Our market research surveys indicate that consumers like steel wheel designs as much as aluminium designs,” said Jim Cran, Project Manager, AISI. “The consumer does not differentiate between steel and aluminium. They don’t know the difference. They just know a good looking wheel.”
Among the reasons for the comeback of steel wheels are high strength steels and new designs that offer large ventilation openings that mimic the thin-spoke appearance of some alloy wheels. “The use of high strength steel, plus high-ventilation area wheels design, increases steel wheel market opportunities,” said Edson Yamashita, Director, Quality, Engineering & Technology, ArvinMeritor Inc. “Lighter weight, high-strength steel has opened up increased opportunity to mimic the thin-spoke appearance of some alloy wheels. Additionally, the use of high-strength steel has drastically reduced the weight penalty normally associated with steel wheels.”
Nelson Gosser, Director, Sales & Marketing, Wheels, ArvinMeritor Inc, added: “ArvinMeritor’s wheels business strives to provide a strong set of solutions balancing cost with benefits in the wheel market. By utilising our advanced design and manufacturing processes combined with reduced weight and increased design flexibility offered by the new steels, we can be quite competitive against certain alloy wheels designs.” ArvinMeritor is a major producer of steel wheels for the light vehicle OEM market, principally in North and South America.
How well do you really know your competitors?
Access the most comprehensive Company Profiles on the market, powered by GlobalData. Save hours of research. Gain competitive edge.
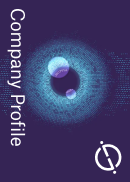
Thank you!
Your download email will arrive shortly
Not ready to buy yet? Download a free sample
We are confident about the unique quality of our Company Profiles. However, we want you to make the most beneficial decision for your business, so we offer a free sample that you can download by submitting the below form
By GlobalDataFor its part, Accuride Corp used the 2007 Mid America Trucking show to reveal its Accu-Lite steel wheels, proclaiming them as the lightest available version of the industry standard two and five hand hole 22.5 by 8.25-inch steel wheels. Weighing eight pounds less than Accuride’s previous industry-standard steel wheels, the two hand hole Accu-Lite weighs 70lbs, while the five hand hole design weighs 68lbs. “Accu-Lite’s eight pounds of weight reduction per wheel translates to a saving of at least 144 pounds for tractor / trailer combinations,” said Larry Taylor, Accuride’s Senior Vice President of Sales & Marketing. “When you compare the weight savings of Accu-Lite to the competition, the competition doesn’t offer comparative savings. Accu-Lite is 11 pounds lighter than domestic competitors and anywhere from 14 to 23 pounds lighter than overseas competitors.” Accuride’s engineers used high-strength, low-alloy steel coupled the latest welding and metal forming technology to produce this wheel set. Accuride Wheels is the largest North American manufacturer and supplier of wheels for heavy- and medium-duty trucks and commercial trailers.
In addition to lower weight, there are a number of other benefits of steel wheels over aluminium. Along with lower costs, steel wheels offer better pothole resistance and improved corrosion resistance in the bead-seat area.
Still on a roll
Since being rolled out by the Sumerians in around 3500 BC, the wheel has been constantly re-invented. Today, the main development trends are moving beyond bigger, lighter and brighter wheels toward scaleable and flexibility in design. Yamashita said: “The idea is that the base model will be offered with a painted steel wheel, that same steel wheel will have a chrome and/or painted clad affixed to it for a mid-level appearance on the model, and then a larger, more design intensive wheel for use on the premium level. Several vehicle classes in North America, pick-ups and SUVs in particular, are developing a sub-premium or psuedo-premium wheel option. This is a market between the smaller clad wheel and the large premium chromed cast aluminium wheel. This niche is not only relevant for steel wheels market as the cast aluminium wheel suppliers are also using a chrome cladding in many cases.”
Alcoa Forged Specialty Wheels recently introduced its so-called Dura-Bright technology, a novel wheel surface treatment available on aftermarket truck and SUV wheels that gives a shiny, long-lasting appearance. It is not a coating or a finish, says Alcoa, “but a proprietary surface treatment that penetrates and reacts with the aluminium.” In other words, it helps prevent peeling, cracking and corrosion. Like ArvinMeritor, Alcoa is particularly innovative in terms of wheel styling, finishing and surface treatments. “In terms of wheel finishings, we assist the OEM by offering smart forged wheels for inclusion in their luxury/performance packages for certain vehicles,” said Brian Thomas, Marketing Communications Manager, Alcoa Forged Specialty Wheels.
“That enables them to generate more revenue in the market place. Our Alcoa Technical Centre is continually coming-up with new innovations in wheel treatments and finishes that allow the introduction of different colours and treatments. Different surface treatments can radically alter the appearance of the wheel. Our CAD software can also help reduce the unsprung weight before it reaches the production process.”
Headquartered in Cleveland, Ohio, Alcoa Wheel Products employs 3,000 people at seven locations worldwide. The Alcoa business unit manufactures cast and forged aluminium wheels for the heavy truck, automotive and motorcycle industries.
Wheel appeal
Although the stamping process used in manufacturing steel wheels has some limitations in terms of design, ArvinMeritor’s engineers are working hard to have designs that allow it to address wheel designs and styling cue needs. “When coupled with claddings,” said Yamashita, “this adds even more styling options for the OEMs and provides a high degree of flexibility, especially when an OEM approaches wheel design early in the development and decision process. ArvinMeritor is investing heavily in engineering capacity to bring more flexibility to steel wheel design. We also work with suppliers and industry partners investigating new materials and manufacturing processes that allow our customers more design freedom while reducing the design-cost compromise. There is no limit to wheel design; the limiting factors are material strengths and the cost of alternatives. As ArvinMeritor increases wheel design options to meet styling requirements we ensure the steel wheel will continue as a viable option for consideration on he cars of tomorrow.”
While the focus on wheels is centred on weight and appearance, the spare wheel is a little more basic. “Over 90% of spare wheels are made of steel,” added Cran. “But with CAFÉ limits, sometimes vehicles are so close to their weight limit that they don’t want to get into the next class with the higher requirements so if they need to save a few pounds then believe it or not they will throw in an aluminum wheel in the truck. It can be that close. What happens in most of those cases is that the pressure is on to get the pounds out of the vehicle somewhere else so that they can put a steel wheel back in there because they do not want to pay the extra for the aluminum spare. So there is that one anomaly.”
Other trends in wheel design include larger diameter wheels. There are two main reasons for that. The first is appearance; people like the highly styled wheels with low profile tyres. There has been a steady tendency, during the last 10-15 years, for cars to be fitted with wheels which are both larger in diameter and wider than those seen in cars of 1990 and earlier. At that time, the average wheel rim diameter was around 13-inches for B/C segment products, increasing to 15- or 16-inches for high-end and luxury models. Today the equivalent figures are 15- to 16-inches in the C-segment and up to 20-inches in luxury models. Although larger wheels are a mixed blessing for chassis engineers, they are welcomed by brake engineers as they offer more space for larger discs.
Wheels of fortune
Putting wheel innovations to one side, the European and North American wheels industry must still balance escalating raw material and energy costs with cutthroat pricing together with a steady flow of low-priced wheels from Asia. It is therefore hardly surprising to see a number of manufacturers hitting hard times. Hayes Lemmerz emerged from Chapter 11 in 2003 with a strong balance sheet and ample liquidity to support its operations and future growth. Four years later, the company is in good shape. “If you look at the first quarter of 2007, we were off to a good start,” said Fred Bentley, Chief Operating Officer, President of the Global Wheel Group, Hayes Lemmerz International, Inc.
“We had year-over-year earnings improvement. Our first quarter was strong. We have given guidance for the full year that looks like we are going to have a pretty good year. The most important thing is that a lot of action that we have taken over the past six years has put us in a much stronger position today. For example, we closed most of our North American aluminium wheel capacity over the last several years. We have divested some of our lower performing businesses and invested in some of the lower cost regions. The result of these actions are beginning to show-up in our financial result. This year we have spent a lot of time on re-financing the Company and working on our balance sheet to improve the health of our company going forward. In Europe, the aluminium wheel market is currently in a tough market, but we have been ahead of this so far, although realize that there is still a lot of work to do.”
Over the last decade, Hayes Lemmerz has expanded geographically, broadened its product range and branched out to supply heavy truck makers. In addition, the company has strengthened its presence in Brazil, South Africa, Thailand, Japan, Czech Republic, Turkey, Mexico and India. Last year, Hayes Lemmerz’s North American Wheel and International Wheel Groups were merged into the newly-formed Global Wheel Group. Bentley added: “The main driver behind the merger is that most of our customers today look at sourcing strategy as a global decision. They would like us to have one voice, whether it is in Asia, Europe, South America or North America. It made sense for us to have alignment in our global business, to have our technical development going the same way and most importantly, to respond to what the customer is asking us to do.”
See also: Global market review of road wheels – forecasts to 2013