The market for body panels is driven by a number of considerations—styling, low cost and reduced weight. The myriad of plastic and metal body components securing the various panels in place is also being scrutinised by manufacturers in an effort to reduce the car’s weight. Matthew Beecham reports on some trends in the use of certain materials to meet all of these requirements.
Body language
For some time, the automotive industry has been under pressure to change the way it designs and builds vehicles, due to factors such as the increasing impact of passenger and pedestrian safety requirements and the competitive intensity caused by globalisation and manufacture in low cost economies. Governmental pressure in Europe and North America to reduce the CO2 emissions has also prompted automakers and their supply base to develop automotive technology to meet those strict emission limits. Consequently, more and more vehicles are incorporating components aimed at mass reduction, parts consolidation to reduce assembly costs and more efficient recycling. The automaker’s need to improve overall fuel economy in vehicles has led to the trend toward minimising vehicle weight. The use of performance materials such as high strength steel and aluminium is on the rise and heavier traditional materials, such as steel and iron, are being replaced whenever possible.
While the aluminium industry claims that usage of its material has grown to an average of 130kg per car, Professor Jon King, director, Corus Automotive believes that this assertion is mainly based upon cast aluminium in engine blocks and not increased use of aluminium in body structure and panels. He told us: “However, there are a few panels on a vehicle capable where conversion to aluminium makes sense in higher cost vehicles. For example, in Europe 20% of new vehicles now have an aluminium bonnet. In the future, we believe that cars will be more multi-material in content than today, but that the economics of steel use — its comparative cost with reference to other metals, the fact that steel is well-understood by the world’s automotive engineers, the fact that there is a massive existing installed equipment base used to shape it, and its ease of recyclability — means that steel will remain the material of choice amongst carmakers for many years to come.” Corus is Europe’s second largest steel producer with annual revenues of some £12 billion and crude steel capacity of about 20 million tonnes.
Stadco is a major supplier of body-in-white panels and assemblies to automakers, including Ford, BMW, Jaguar, Land Rover, Aston Martin, GM and Toyota. Among other things, Stadco specialises in stamping aluminium panels for its customers. Paul Jaggers, product engineering director, Stadco, believes that aluminium in body structures is still mainly in the luxury car sector and rarely makes an appearance in the smaller car sector due to the incremental cost of the raw material. He said: “It is also difficult to introduce aluminium components into steel structures because of the corrosion problems, different expansion rates and the differing joining methods. If aluminium is added to a steel structure it would normally be as a “hang-on” part such as a door, hood or tailgate. I do not see evidence of the use of aluminium in body structures increasing at present and feel it is unlikely in the near future.”
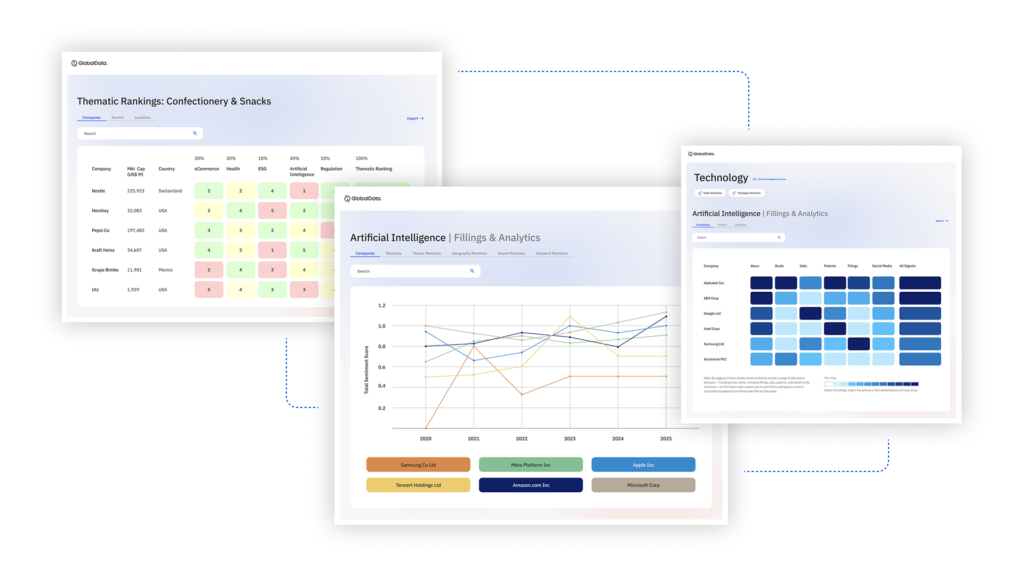
US Tariffs are shifting - will you react or anticipate?
Don’t let policy changes catch you off guard. Stay proactive with real-time data and expert analysis.
By GlobalData
Weightwatchers
The environmental and economic requirements for reduced fuel consumption have also led to an increase in the use of lightweight materials for components that bolt on to a conventional steel vehicle, but at a cost. King maintains that all weight savings add up to fuel savings, but not as big as suggested in the press. “Our own research to predict steel demand, shows that roughly every 100kg saved in vehicle weight offers 4% in fuel economy and the potential to save around one tonne of CO2 over the life of the car. It is true that cars have been getting heavier over the last few decades, but perhaps surprisingly, this is due largely to the increase in general vehicle dimensions, large increases in strength and stiffness and the wider addition of features and devices such as air conditioning. More recently, new car introductions are beginning to show that this increase is peaking, with many launches demonstrating weight savings, in many cases due to successful deployment of advanced high strength steels (Mazda 2, Mercedes C-Class, Renault Laguna). Most vehicle manufacturers will be able to get very close to the 2012 legislative target of 130g/km of CO2 without big changes to their material strategies, as their current focus on engine and transmission technologies provide major gains.”
Meanwhile, we continue to see more use of high tensile steels. The trend in the increased use of higher strength steels such as 600 and 800 MPa material and ultra-high strength steels such as boron steel is clear, says King, as are the weight-saving benefits. “The challenge for industry is for better collaboration of OEMs and their supply chain to exploit these materials. We will certainly see lighter all-steel vehicles, especially in the highly cost driven A, B and C segments.”
Although the manufacture of body panels and various assemblies have historically formed part of the automaker’s in-house activities, these parts are increasingly being outsourced. “We see a range of strategies in this field and it is difficult to see any clear trend emerging in the outsourcing of sheet metal forming,” said King. “Whilst it is true that Western Europe faces a particular challenge from Eastern Europe and even further afield, rigour in quality has yet to catch up with the enthusiasm for cost reduction in many cases. However, there are now increasing opportunities for tier1/2 suppliers to develop modular assemblies such as doors and walk-in-front-ends. The rapid growth of die quenched (boron steel) pressings has been mainly due to tier 1 supply. Carmakers prefer to press the full-finish exterior body panels in-house to reduce the potential for transport damage and control quality.”
Jaggers added: “As the volumes have taken a downturn, the OEMs have had to juggle with the requirements of their own organisation and capacity with the requirements of the suppliers to stay in business. Long term we see no shift away from body-in-white being outsourced due to the massive investment required to add capacity in-house.”
Plastics make the grade
While the use of aluminium, magnesium and different grades of steel are all under scrutiny by automakers in a bid to optimise certain factors, the use of plastics in vehicles has significantly increased over the last decade. The trends toward the increased use of plastics in exterior and structural/functional/powertrain components have been driven by innovations in material, moulding and painting technologies, which have improved the performance and appearance of moulded plastic components as well as lowering their costs. The design freedom that plastic offers is also key to its increased use. Not only does plastic allow for the manufacture of products that cannot be manufactured with other materials, plastic makes it possible to combine several parts, saving weight and cost. Additionally, recently introduced plastics that can withstand the hot, corrosive environment of the engine compartment are becoming more prevalent.
On the flipside, says Jaggers, structural plastic components are difficult to integrate with the rest of the structure and so at present they are generally restricted to parts that can be added after the steel structure has been completed. There are some restrictions with regard to durability and repairability if they are used in some areas of the vehicle.
Organic cars
The use of organic materials in cars is not new. For some time, component suppliers and automakers have focused on promoting environmentally friendly technologies in all product segments. In the area of seating, for example, coconut fibre seat pads have been used in order to meet manufacturers’ economic and ecological objectives while contributing to sustainability. For example, Mercedes-Benz uses coconut matting, crushed olive stones and even sawdust in certain vehicles.
Meanwhile, Toyota is using plastic components made from plants for its new-generation Prius. Known as ecological plastic, the plant-based foam and injection-moulded parts are found in several locations throughout the new car including the scuff plates, deck trim and seat cushions. The plant based plastics replace conventional plastics made using petrochemicals, cutting CO2 emissions over the life of the product (from manufacture to disposal) and helping to reduce petroleum use. Ecological plastic emits less CO2 during a product’s life cycle because most of the CO2 emitted at disposal was originally captured during photosynthesis while the plant was growing.
Finally, BMW is looking at improving efficiency by using solar energy. In Central Europe a square metre of photovoltaic (PV) solar cells can produce around 200W of electricity. PV modules could be incorporated into roof, or the whole surface of the car. The automaker says these could be used to help pre-warm engine fluids to reduce emissions during the cold-start phase, where emissions are high. BMW says that 1 kilowatt-hour of electricity produced from the sun rather than from the engine would reduce fuel consumption by 0.3l/100km.
Matthew Beecham
‘Beechy’
See also: Global market review of vehicle body material trends – forecasts to 2016 (download)