Emissions legislation, weight, packaging, safety and cost are the main factors driving fuel tank innovation, writes Matthew Beecham.
By the 1980s, air pollution in California had become so intolerable that legislators and the California Air Resources Board (CARB) began to establish increasingly tighter emission standards. This itself forced automotive fuel system manufacturers to push back the technical boundaries. More than 50% of California’s smog pollutants were found to come from a combination of vehicle exhaust/tailpipes and evaporative emissions (passive/evaporative emissions – while parked).
Sharon Lemieux, manager, Emission Research Section, Mobile Source Control Division at CARB, explained the work of the CARB today. She said: “Since we adopted the LEVII [Low Emission Vehicle II] evaporative standards, we have been testing evaporative emissions from fuel systems and have verified that their emissions are indeed very low. We are also exploring where we can further reduce evaporative emissions. We have a proposal that is still under discussion to see if we should reduce the current LEVII evaporative standards down to the “whole vehicle” zero evaporative standards. If adopted, the conventional LEVII evaporative control systems would need to use the advanced PZEV [Partial Zero Emission Vehicle] evaporative control technologies.”
When CARB revamped its ZEV (Zero Emission Vehicle) programme in 2004, it created the PZEV class to address the increasing number of new vehicle models that carry some zero emissions technology but still release emissions via the tailpipe.
CARB estimates that about 462,000 PZEVs will be sold in 2008. In 2003, annual sales were about 110,000 in California, rising to 129,000 units in 2004, 245,000 units in 2005 and nearly 226,000 units in 2006. This year, CARB expect sales of vehicles complying with PZEV to reach 357,000. They include models ranging from the BMW 325Ci, Ford Focus, Honda Civic, Kia Spectra, Mazda 3, Mercedes-Benz E350, Mercury Milan, Nissan Altima and VW Golf. Most of these use steel fuel tanks.
Lemieux points out that more and more states are opting into the Clean Air Act section 177. “Right now, there are a number of states which are opting into California’s programme, including Connecticut, Maine, Maryland, Massachusetts, New Jersey, New York, Oregon, Pennsylvania, Rhode Island, Vermont and Washington. In addition, there are four more (Colorado, Illinois, New Hampshire and North Carolina) that have indicated that they would like to adopt California’s motor vehicle programme.”
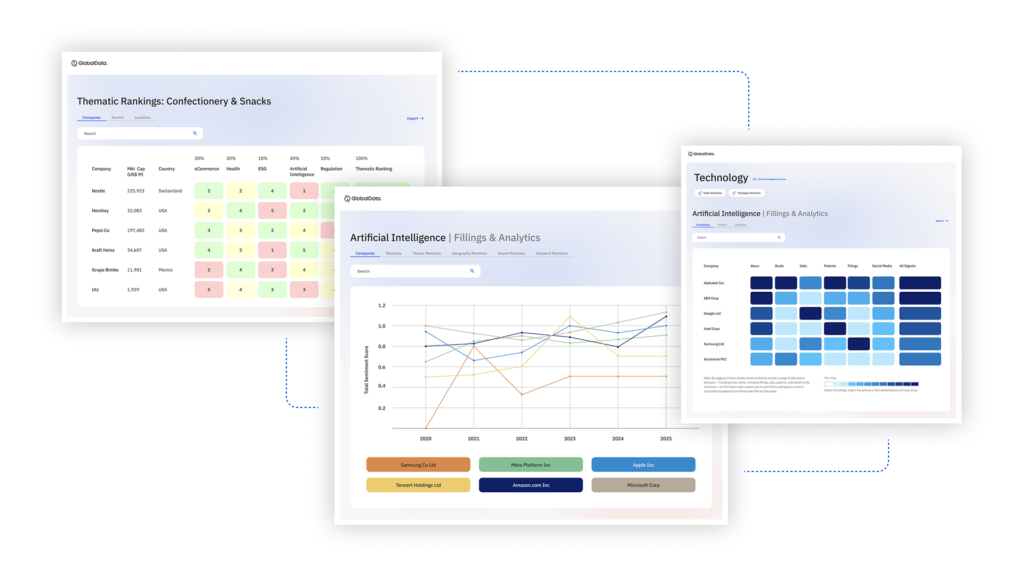
US Tariffs are shifting - will you react or anticipate?
Don’t let policy changes catch you off guard. Stay proactive with real-time data and expert analysis.
By GlobalDataAs far as future emission standards under discussion, Lemieux says that although not evaporative related, the CARB have been exploring the issue of the composition of certification fuel. “Those specifications for our certification fuel are not consistent with what is currently being sold commercially. We are also looking into on-road motorcycle evaporative emissions. Those evaporative emission standards have been unchanged since the 1983 model year. That process will take us about two years to test and consider the direction we should go with motorcycles, given that most people like to modify their motorcycles. For instance, we shall have to address how to crack down on tampering motorcycles if we require additional emission controls.”
Plastic tanks fuel growth
Until the implementation of the LEV1 legislation in the US, blow-moulded monolayer fluorinated fuel tanks were the preferred technology in the US market. However, the long-term performance of the fluorinated tanks was a major concern at the time. In addition, the fluorination process was relatively difficult and used hazardous chemicals. As a result, new barrier technologies were introduced. The development of the slosh test in the US led to the use of six-layer fuel tanks. In Europe, however, fluorination is still popular because manufacturers can use their monolayer machines with these technologies and do not need to invest in new equipment. In Japan, three-material, five-layer plastic fuel tanks using nylon as a barrier resin have been used for more than 15 years.
Although multilayered plastic certainly appears to have become the material of choice for automakers, there are still some concerns over its recyclability. Yet plastic tank manufacturers argue that their products can be 100% recycled, reused and revalorised during the manufacturing process or at the end of the vehicle’s life. Dr Paul Wouters, vice president, research at Inergy Automotive Systems, said: “In 1995-1998, we completed a study that was partly financed by the European Commission with different partners. We demonstrated that we could incorporate a significant proportion of end-of-life recycled plastic tanks. We also demonstrated that we were able to pass all the requirements in terms of mechanical properties.”
Yet steel fuel tank manufacturers reckon that producing a multilayered plastic tank with different barriers in it makes it virtually impossible to recycle. Peter Mould, programme manager of SASFT (Strategic Alliance for Steel Fuel Tanks), said: “There are processes capable of recycling plastic tanks but are they commercially viable? Frankly, in North America, virtually all of the plastic tanks are land-filled. And we don’t see any infrastructure developing here to change that.” SASFT is an international alliance of companies specialising in the various areas of fuel tank production.
Material matters
Mould also argues that the cost of materials and availability are the major issues. He told us: “The increasing price of oil will make the price of polyethylene more expensive. So there is concern among those who are buying plastic tanks about what that overall increase will look like over the next few years. Consequently, our SASFT members are seeing more enquiries and interest for steel tanks in future vehicles. OEMs are taking a strong look at steel. The other issue, of course, is the environmental impact. We know that evaporative emission regulations are here to stay. The CARB is the main driver here. We expect CARB will soon demand that people test to the different fuels rather than 100% gasoline. And the other broader issue there is, of course, life after use, i.e. recycling. In engineering terms, weight is becoming even more important than ever because of the pressure to increase fuel economy. The durability issue there – external and internal corrosion – has not been in steel’s favour for a long time but I think that with all the new materials and coatings that have been developed by the world’s steel industry. That is a non-issue nowadays. Fuel capacity is also going to become more important as we go to alcohol-containing fuels which don’t have as much driving range. So trying to get as many gallons into a confined space is going to become important. Those are the main issues as I see them. And those go some way to debunk those myths that are being spread about steel in its competition with plastics.”
But plastic tanks still maintain the edge over steel tanks, argues Wouters. “The benefits of plastic tanks [compared to steel] are flexibility, cost and weight. These days, weight is a feature is becoming more and more an important issue in terms of CO2 emissions. In that respect, plastic tanks have a clear advantage… Although the steel forming processes has improved, plastic still has an advantage over steel. When you look at the weight and cost of plastic tanks then the balance tips in favour of plastic tanks.”
“There are applications where steel tanks weigh more than plastic and vice versa,” said Ray Sheffield, director, fuel tanks, Martinrea International. “Generally speaking, it is a fair to say that a steel tank shell tends to weigh a little more than plastic although steel tanks typically weigh in the order of about 5% more than a plastic tank shell, but this will vary widely depending on wall thickness and specific design features.” This Canadian manufacturer designs and produces fuel tank and sender assemblies; fuel lines and hoses; fuel line feed and return assembly systems; fuel filler necks; capless refuelling systems; fuel rail crossover tubes; and vapour assemblies and canister hoses. Its customers include Ford, GM and DaimlerChrysler.
Mould added: “There is also this issue that included in the weight of plastic tanks is often the heat shield. If you then compare that with steel tanks – which don’t usually need the heat shield – then we can be very competitive. For example, one of SASFT’s recent design studies for a major OEM in North America involved taking a plastic design and then being given the challenge to come up with an alternative steel design. Our saddle tank design came in with about 2lbs less weight and slightly more fuel capacity. Additionally, had we re-sized the steel tank to provide the same capacity as the plastic tank, we would have saved even more weight.”
Although we do not expect to see the tide turning in favour of steel tanks, market demand remains steady across Europe, North America and Japan. While steel industry sources concede a shrinking steel tank market, they argue that, in the long-term, the environmental and cost issues will win back a larger share of the fuel tank business. They reckon that they can make steel tanks with the same amount of design flexibility as plastic. Modern fabricating methods such as hydroforming, allow steel to be manipulated into equally complex shapes. They believe that as zero emission legislation spreads beyond Californian borders, demand for steel tanks could increase.
In terms of tomorrow’s fuel tank designs, SASFT’s Mould concluded: “I see more coming in the future evolution rather than from revolution. I think that we shall see more formable steels that will enable complex shapes to be made and associated with that will be improved manufacturing techniques. People have looked at hydro-forming but there is a cost issue especially at low volumes. But hydro-forming may come along in the future. So with these two improvements – materials and enabling manufacturing techniques – we shall see more complex steel tanks which will be better able to take advantage of that limited engineering space underneath the vehicle. Bearing in mind that fuel tank tends to be the last thing to get designed and it gets ‘squeezed’ into more and more restricted space.”
‘Beechy’
Footnotes:
Following a 5 November 1998, hearing, the Air Resources Board (ARB) amended California’s Low-Emission Vehicle (LEV) regulations. The new amendments, known as LEV II, advance the state’s clean air goals through improved emission reduction standards for vehicles. These amendments were formally adopted by the ARB on 5 August 1999, and, after approval by the California Office of Administrative Law on 28 October 1999, became operative 27 November 1999.
The ARB first adopted LEV standards in 1990. These first LEV standards run from 1994 through 2003. LEV II regulations, running from 2004 through 2010, represent continuing progress in emission reductions. As the state’s passenger vehicle fleet continues to grow and more sport utility vehicles and pickup trucks are used as passenger cars rather than work vehicles, the new, more stringent LEV II standards are necessary for California to meet federally-mandated clean air goals outlined in the 1994 State Implementation Plan (SIP).
The SIP is the state’s ‘road map’ to attain federal clean air standards by 2010 and includes among its measures strategies to further reduce air pollution from vehicles and other mobile sources. When LEV II is fully implemented in 2010, it is estimated that smog-forming emissions in the Los Angeles area will be reduced by 57 tons per day, while the statewide reduction will be 155 tons per day.