Stricter emission standards, new pedestrian safety laws and the relentless push for reduced fuel consumption have triggered a flow of engine cooling innovations. Matthew Beecham reports on what’s in the pipeline.
Packaging space further squeezed–
“In addition to cost reduction pressures and engine down-sizing, new emission regulations are forcing us to make changes to the product and technology,” said Dr Uwe Krueger, Vice President, Product and Process Development, Engine Cooling, North America, Behr Group. “There is also a trend for more compact engine cooling modules in order to solve the space constraints under the hood. On the one hand, there is pressure to introduce new technologies in order to meet the cleaner emissions yet on the other side the cost pressure is still there. We must achieve both. Our customers want the best performance for the lowest price.”
It is certainly true engine cooling systems must fit into ever smaller spaces under the bonnet. “In general, packaging space is being increasingly squeezed in the vehicle front-end, prompting the need to develop more efficient, smaller heat exchangers,” added Graeme Stewart, Technical Fellow, Powertrain Cooling Heat Exchangers, Visteon Corp. “We are responding by looking at all aspects of fins and tube geometries in order to increase heat transfer while meeting higher pressure cycles. Other factors regarding the pressure cycle relate to changes from engine outlet side thermostats to inlet side thermostats in order to give better, more uniform control of cylinder head temperatures.”
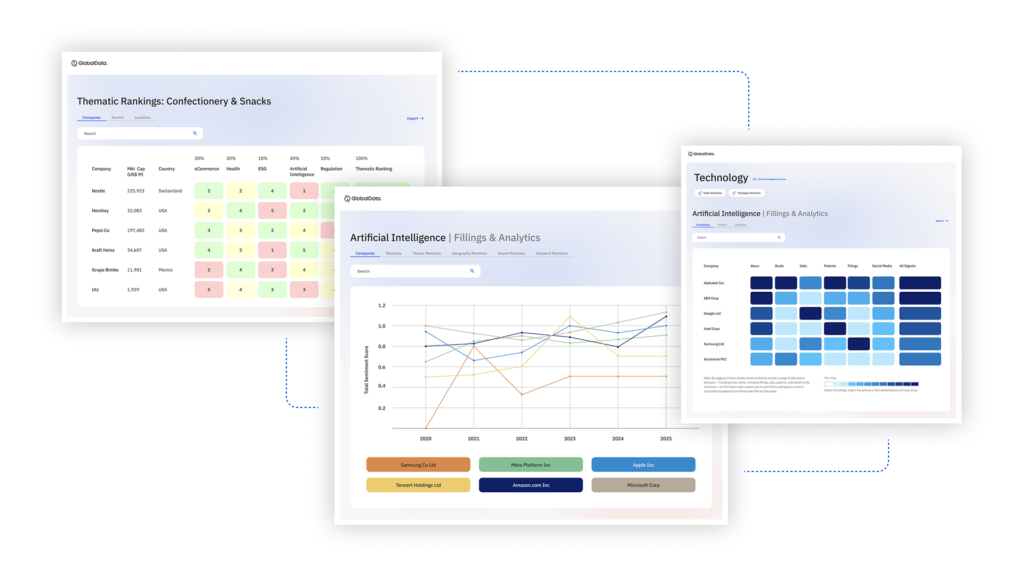
US Tariffs are shifting - will you react or anticipate?
Don’t let policy changes catch you off guard. Stay proactive with real-time data and expert analysis.
By GlobalDataGiven the pressure on suppliers to squeeze higher performing products and systems into a smaller space under the bonnet, radiators have gradually shrunk. For example, a modern aluminium radiator is about two-thirds the size of a unit produced in the late 1970s. The high cost of fuel, particularly in Europe, means that designers are seeking ways of reducing the airflow in the car, which is leading towards the use of smaller heat exchangers. Not only are auto engine cooling parts becoming smaller but there is a clear trend toward more component integration. For example, combining the condenser and radiator can save space and help cut costs. Modularity plays an important role in packaging engine cooling systems. This approach can, of course, help cut costs and simplify the entire installation on the assembly line.
–as pedestrian safety laws swing into force
Further pressure on suppliers to consider the packaging space available to fit engine cooling parts has come from a new set of laws which swung into force in October 2005 across the European Union countries aimed at protecting pedestrians and cyclists involved in a collision with a vehicle (European Directive 2004/102/EC). To date, the European Commission has devised four pedestrian-safety tests, two that measure impact on the lower leg and head of a child and two that measure upper leg impact and impact on an adult’s head. The new laws are designed to reduce the 8,000 European pedestrian and cyclist fatalities per year by half.
All in all, these changes impact on engine system design, creating the need for manufacturers to re-think the location and packaging of certain components. “We are working on ways in which to improve the performance density of the engine cooling module so that we can achieve the same performance from a smaller unit,” said Uwe. “In addition, we are actively working with our partners, Hella and Plastic Omnium in the front-end, looking at ways in which to mount the engine cooling module taking into account the pedestrian safety requirements yet achieve an optimised solution for our customers, too. In fact, crash management is one of the core competences of the Hella Behr Plastic Omnium [HBPO] joint venture.”
Stewart added: “[The pedestrian safety laws are influencing] the top edge of the heat exchangers, reducing its height thereby squeezing the package. In addition, the mounting system is changing. In addition, low speed crash requirements are becoming increasingly important. That means we need to minimize or eliminate the damage to the cooling pack under low speed incidents thereby reducing the repair bill and improve the insurance cost. During low speed crashes, insurers want to protect engine cooling parts from any significant damage but also ensure the customer can drive away from the crash in order to get the repair carried out.”
In Japan, the innovation drivers are similar albeit with some subtle differences. “To sustain sufficient engine performance, engine cooling performance is needed to satisfy severe conditions such as when climbing roads or during hot weather,” said Shinichi Oda, Senior Manager of Denso Corp’s Cooling Systems & Components Engineering Department.
Hybrid vehicles bring fresh challenges–
Although hybrid vehicles have not yet really created a substantial change in the heat transfer philosophy of the engine, Behr believes that they spell good news for developers of thermal management, as they demand new techniques in battery cooling and electronic cooling. “As soon as we see greater demand for these cars then we shall see more innovation in this area,” added Uwe.
Visteon believes that hybrid vehicles, depending on the design and architecture, may need some additional cooling for batteries, electronics or electric motors. Bernd Kirmse, Manager, Product Marketing, Visteon Climate Control Systems Europe, said: “We have been developing various solutions to achieve this based on the cooling fluids: refrigerant, engine coolant or air. When developing such solutions, we always keep in mind the need to maximise re-usability of existing heat exchanger technologies in order to achieve a cost attractive solution. We are helping that effort by re-using technologies wherever possible and adapting it to best effect.”
Developing engine cooling systems for fuel-cell vehicles is another main thrust of product development. Given that fuel cells emit a higher heat rejection to the cooling system than conventional gas or diesel engines, they pose a far bigger challenge to suppliers. For instance, around 50% of the energy fed into a fuel cell vehicle is emitted as heat rejection, compared to just 30% for a gasoline or diesel engine. Manufacturers see fuel cells as the next major challenge for powertrain cooling.
Another challenge facing suppliers is the relentless push by vehicle makers to downsize engines for diesel as well as gasoline engines. Upgraded engine cooling modules capable of handling more heat rejection in a smaller space are being introduced.
– along with new regulations
Until recently, vehicle air-con engineering circles believed that their products were environmentally sound as during the 1990s they had replaced the conventional CFC refrigerant, R12 with the environmentally-friendly hydrofluorocarbon (HFC) refrigerant, R134a. The switch was necessary given the fact that one pound of R12 released into the atmosphere was equivalent to a whopping 15,000 tons of CO2 (carbon dioxide). The same amount of R134a releases just 1,300 tons of CO2 and being chlorine free has no affect whatsoever on the ozone layer. However, as the installation of air-con permeates all new car segments as standard fitment, environmental lobbyists have raised concerns about the increasing use of R134a. The EU has therefore been pushing for an even more environmentally-friendly cooling systems that use CO2 as alternative refrigerant. Legislation finally came to pass in August 2003 requiring that R134a be phased out from 2009, with a complete ban on its use from 2016. Compared with R134a, the thermodynamics of R744 allows for better cooling capacity as well as reduced fuel consumption.
“When this switch [from R134a to R744] was first debated, most industry observers believed that significantly higher system pressures would result in larger and heavier componentry,” said Kirmse. “But the reverse is happening. The higher density of the refrigerant allows for the required mass flow in reduced cross-sections. To cope with the pressure the wall-thicknesses are increased but at the end we have smaller components and the system weight is about awash. For the gascooler we work along the same front face of an R134a condenser but the component depth is reduced.”
Stewart added: “We have made all of the R744 components compatible with the R134a. That means if customers wish to switch mid-cycle, the rest of the cooling package does not have to change.”
Kirmse concluded: “This parallel use of R134a and R744 components in the same vehicle could be a scenario as long as only Europe mandates a ban of R134a. So it might be that with global vehicle platforms, automakers may decide to use one refrigerant for one market and another one for another market.”
On balance, it is clear that the demands on modern engine-cooling systems are complex. Although increased performance, reduced fuel consumption, longer durability and cleaner emissions may appear to be at odds with each other, the engine-cooling supplier must address them to stay in the game and go with the flow.
See also: Global market review of automotive engine cooling systems – forecasts to 2013