It may not look like it but the door is one of the most complex systems on a vehicle. It must look good, incorporate crash stability and, above all, be fit for the purpose, typically opening and closing more than 50,000 times during the vehicle’s life, writes Matthew Beecham.
Automakers are increasingly outsourcing their requirements for larger complex modules and systems, including doors. A door module typically consists of a rubber-sealed carrier plate made from plastic or metal. A variety of door components — such as the window lift mechanism, locks, electric motor to operate the wing mirror, wiring harness, various switches, loud speaker and a cable that connects the latch to the inner release handle — are then fitted onto the carrier, forming a ‘cassette’. The carrier plate is then tested and sealed to the outer door.
In outsourcing a door module, an automaker could typically gain in the region of 5%-10% weight savings, 10% for parts and 10%-20% in cost savings. Of course, the actual cost saving depends on the vehicle programme and materials used in the module. Jean-Marc Belmond, director of product engineering for ArvinMeritor’s door systems business, points out two distinct benefits that the automaker can derive from sourcing door module business. “Firstly as the supplier of the world’s very first sealed door module in 1968, ArvinMeritor has a proven and unparalleled level of experience that allows us to properly manage the total cost optimisation of the product. Our understanding of door design and of modular applications on OEM production lines allow us to design exactly the type of module required, in either steel or plastic, to realise cost savings. The second benefit is that ArvinMeritor has a unique level of systems expertise in the industry as we design and manufacture all the key components within the module. Our full portfolio of window regulator, electric motor, door latch and electronics products gives us the knowledge to integrate them intelligently, robustly and for the maximum cost effectiveness.”
Magna Closures also competes in the door module market. This business has evolved from a cable supplier to a window regulator supplier to a door module supplier with capabilities in electronics and system integration. “With unmatched depth of product expertise, Magna Closures adds value through the integration of door hardware components into complete module systems,” said Hugh Downey, director of portfolio planning at Magna Closures. “By outsourcing door modules to Magna, OEM customers increase their manufacturing flexibility by reducing the required floor space to build each door variant, which allows more door and vehicle variants to be built within their facilities. By outsourcing the complete module system, Magna improves the quality of the door by testing many of the fully assembled systems rather the components only.”
While the majority of door modules use a steel carrier, plastic solutions are becoming increasingly popular. Brose GmbH reckons that using door systems with plastic carriers makes them lighter than conventional steel carrier modules, resulting in weight savings of up to 3 kilograms per car. In addition to weight savings, better noise absorption and increased design possibilities make using plastic for the door system carrier appealing for automakers. The company recently set up an injection molding machine at its factory in Hallstadt, Germany. This new equipment has a clamping force of 1,650 tons allowing it to produce the large-surface plastic parts. The first door systems with plastic carriers produced at this plant will go into series production in late 2007.
How well do you really know your competitors?
Access the most comprehensive Company Profiles on the market, powered by GlobalData. Save hours of research. Gain competitive edge.
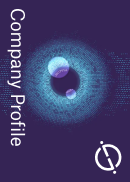
Thank you!
Your download email will arrive shortly
Not ready to buy yet? Download a free sample
We are confident about the unique quality of our Company Profiles. However, we want you to make the most beneficial decision for your business, so we offer a free sample that you can download by submitting the below form
By GlobalDataIn explaining the company’s decision to invest in an injection molding machine at its factory in Hallstadt, Germany, Kurt Sauernheimer, head of Brose’s door business, told us: “While we already have modular door systems with plastic carriers in production, we wanted to do the next step of integration. In order to achieve that, door manufacturers need the experience of putting together material, setting-up machine tools, doing the injection molding process and undertaking it all in close co-operation with the design engineers. This is why we put that huge machine which, including infrastructure costs about €3 million, very close to our where are design engineers are based. That has allowed the interaction of our door development engineers, tool engineers, material and machine experts to come up with the best possible integrated solutions. For example, one investigation involved how to place glass fibre in the door structure in such a way that offers the rigidity in places where it is required yet flexibility in other place. That investigation involved us developing a complex in-molding compounding operation which ensured the correct distribution of the glass fibre.” Brose has a fine pedigree in supplying window regulators and door systems for some 40 vehicle brands and 179 different car models. Sauernheimer adds: “OEMs are already aware that Brose is a clear market leader in terms of technology and product performance. We have never had any serious ramp-up or technical problems. That is partly why customers choose Brose.” Last year, Brose posted sales of some €2.3 billion, of which its door system business generated sales revenues of about €1.64 billion.
While the trend for doors is strongly towards modular – and lightweight – designs, ArvinMeritor sees a number of other trends emerging in the automotive door market today. Mark Lawrie, chief engineer for ArvinMeritor’s door products and systems, told us: “Firstly, plastic door module products will certainly become more prevalent in the drive for weight saving. There is also a growing requirement to address global markets with modular solutions even at the product level. The different functional requirements of world regions can make this a challenge for suppliers without the necessary system or global supply experience. Finally, vehicle crash management is also leading to changes in the door structure with one leading European platform recently raising the load specification of the door waist beam by 50%. This increased reinforcement dramatically reduces the packaging space available for door components at a time when the growing functionality is driving product size up. Radical new technologies such as the LER latch are required to answer this challenge.”
The use of natural materials in doors is also topical. “We see a number of advantages to using natural fibers and especially wood chip fibers,” said Heinz Josef Rüsche, product director for Faurecia’s door business. “First, there is a plentiful stock which results in stable pricing independent from the harvest results of a one year’s plant. Second, the use of natural materials helps reduce weight of the door panels and other components like front seat back panels. Third, we have found that wood fiber has good manufacturing process characteristics. Wood chip fibers are currently used inside the door panel carrier of various Mercedes-Benz models like SLK, S Class, Ford vehicles like Fiesta, Fusion, Opel cars like Corsa and others. OEMs are also becoming increasingly interested in the use of natural wood decoration surfaces on the vehicle’s dashboards and door panels. The trend is a more ‘back to nature’ look inside the cabin.” Faurecia produces door panels, modules and complete doors for the automakers worldwide.
The more popular door modules become, the more likely we will see manufacturers extend their capabilities to include latching capabilities and window regulator mechanisms. However, we don’t see the mechanism side of the business crossing with the wire harness side but we could see a body-in-white structure, lock and latch capability and window regulator mechanism capabilities under one roof. In pursuing that situation, manufacturers could become more competitive, controlling more of the commodities rather than just being a system integrator and buying in from the outside.
Some analysts forecast that the demand for ‘complete door’ modules – sometimes referred to as ‘Level 3’ doors — will gain greater application as soon as the paint, fit and finish problems are resolved. Yet Belmond says that the largest obstacle to complete door supply is the requirement for increased vertical integration at the supplier. “Any stamping facility would also need to be very close to the OEM facility in order to minimise shipping costs. One solution to this may seem to be plastic doors but with today’s technology the fit and finish will never be as good as steel due to expansion requirements. Therefore the OEM would need to rethink door design completely whilst still facing the larger challenge of crashworthiness. Another issue concerns the question over who would take responsibility for the complete aperture system. The OEM would be losing their leader role but the fit and finish, sealing, door release, glass movement, quality of car body side, door structure, etc. would all need to be managed.”
While demand for door modules is increasing, the potential of the total market, however, should not be confined to side doors but sliding doors and rear liftgates. Some manufacturers see a number of opportunities in liftgate modules, especially when combined with power product technologies and advancements in lighter materials, such as aluminium and plastics. “Although the minivan market is not increasing in North America, the sliding door module market is growing,” concluded Downey. “With a higher level of complexity on a sliding door compared to a conventional hinge door – with front and rear latching systems, the power sliding door system and now with window systems – most OEMs have either already introduced a module or are considering it for the next-generation vehicles.”