The importance of DC electric motors in the automotive industry continues to grow, writes Matthew Beecham. The driving force behind market growth is motorists’ insatiable demand for safety, comfort, economy, a clean environment and overall quality of driving.
Electric motors perform a variety of functions that were formerly consigned to cranks, gears and levers. They are typically found in anything that has an electrical movement or solenoid function—such as window-lifts, fuel pumps, mirror and headlamp adjusters, ABS, clutches, automated manual transmissions, parking brakes and steering systems.
Defining the elements
According to Nidec, there are two kinds of DC motors: brush and brushless. Brushless DC motors differ from conventional, brush DC motors in that the current which produces mechanical energy is applied to stationary coils via electronic switches without physical contact with the rotor, rather than stationary rods brushing against the rotating coil. Nidec points out that conventional brush DC motors have several limitations: brush life, brush residue, maximum speed and electrical noise. By avoiding friction, sparks and the wearing and fragmenting of the brush rods, brushless DC motors provide cleaner, faster, more efficient and quieter operation and longer maintenance-free life than conventional rush DC motors. Although brushless DC motors have many advantages over brush DC motors, Nidec says the use of brushless DC motors is still mainly confined to precision applications in disc drives and industrial motion equipment that require high efficiency, smooth operation and precise speed control.
Besides standard brushless DC motors, mainly found in body and convenience areas of the vehicle, manufacturers report that permanent magnet brushless DC motors are already standard (for power steering and drives for hybrid vehicles) or will gain major importance (such as for gearbox actuation).
Growth markets
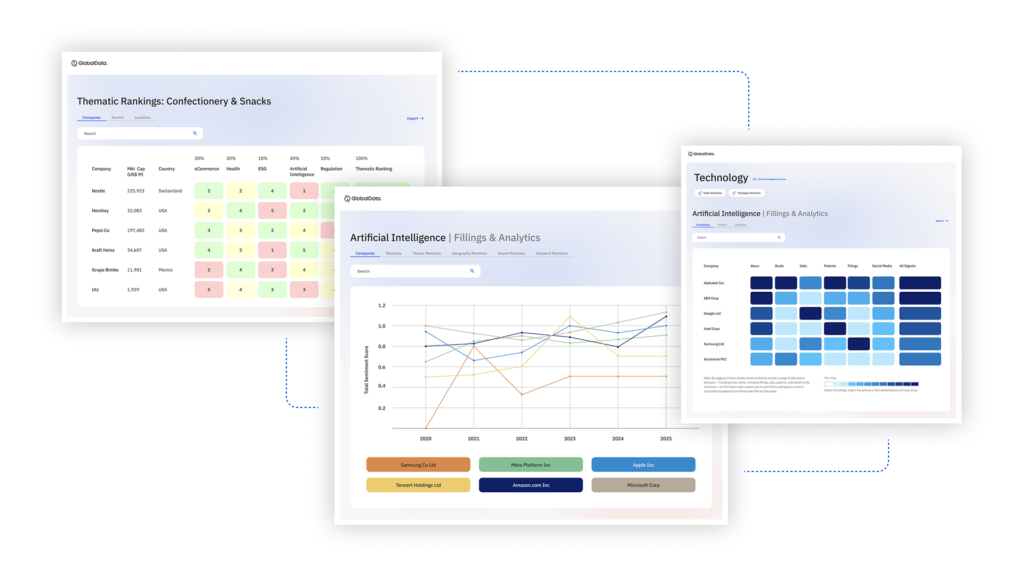
US Tariffs are shifting - will you react or anticipate?
Don’t let policy changes catch you off guard. Stay proactive with real-time data and expert analysis.
By GlobalDataAlthough electric motors have long since been used to power certain vehicle componentry, such as wiper systems, these markets have matured. Meanwhile, growth markets are appearing. For example, manufacturers predict significant growth with gearbox actuators (used for double clutch automated transmissions, actuation for transfer cases and torque distribution differential gears), power steering motors and electric machines for hybrid vehicles.
Manufacturers also expect to see more DC electric motors used in automotive interiors in the future, since there is a general trend towards more electrification. This means that many manual functions, even in the lower vehicle segments, will increasingly be electrically operated. Meanwhile, the use of actuators is also on the rise. Particularly when it comes to convenience features, such as backrest adjusters, the new electric actuators are becoming increasingly prevalent.
Consumer demand for power-folding rearview mirrors is also high in Italy which also has narrow streets. Across Europe, power-folding mirrors have long been popular in the luxury segment, not only helping to prevent damage from passing vehicles in congested streets and assist parking but also serving partly as a deterrent to vandals. “The power folding mirror market is still growing in Europe,” said an automotive executive. “In fact, it is exceeding our expectations. I would say that it has increased by more than 100% compared to three years ago. At this moment, we are strongly investing to increase our capacity to meet demand.”
Power window concerns
In the power window department, manufacturers report a growing need for smaller, lighter motors to fit in the increasingly slim doors of modern cars. In 1963, Germany’s Brose began mass production of electric window regulators for the European market. The BMW 3200 CS coupé was the first vehicle to be equipped with this product. Since then, a number of innovations have been added to power windows including anti-pinch and one-touch operation.
Today, power lift windows are now a standard feature on most passenger cars, so only systems that offer outstanding benefits attract special attention. However, there are still concerns about the safety of powered windows The charity, Kids and Cars, recently said that data collected in a poll administered by Harris Interactive refutes National Highway Traffic Safety Administration’s (NHTSA) approximated power window-related injuries with statistics that differ not by thousands, but by millions of incidents in the US. The charity claims that this data supports their own claim that automatic reversing (ARS) windows should be standard on all vehicles.
While current legislation in the US mandates “pull-up to close” switches on all vehicles manufactured after 1 October 2010, the charity believes that it does not address third-party accidents, which occur when a driver operates the window switch but cannot see rear-seat passengers.
“We’ve known for a long time that millions of people are injured by power windows. When you bring up the topic, everyone has a story about an incident they are familiar with,” said Janette Fennell, Kids and Cars founder and president. “And even though the NHTSA believes mandated ‘pull-up’ switches will rectify this issue by eliminating injuries caused by inadvertent activation of the window, our data proves that it is someone else in the vehicle that causes the majority of the injuries. Common sense, life-saving technology exists and can be easily implemented, as it has been on garage doors and elevators, to prevent senseless child deaths and injuries.”
Most power windows exert an upward force of 30-80 pounds; it takes only 22 pounds of force to suffocate or injure a child. The charity estimates that the ARS feature costs about US$6 per window. The technology is already standard on most vehicles in Europe, including American cars sold there. However, the charity estimates that the technology is on less than half of General Motors, Ford and Chrysler models in the US.
Wiper motors become lighter and smaller
On the wiper motor front, manufacturers note that reductions in weight and size as well as the improvement of exterior appearance are priorities for windscreen washer systems. Bosch was the first manufacturer to offer an electrically powered windshield wiper system in September 1926. Until then, windshields had to be cleaned manually using a ‘cleaning ruler’, and later by means of a pneumatically operated wiper, which wiped more slowly as the vehicle drove faster.
A clear trend today is the fact that more and more wiper blades are being controlled by electronic drive units. An auto executive told us: “Most electric motors – even conventional motors – fitted to move the wipers have some intelligence built into them to control the arc of wipe, speed, etc. And the rain sensor has to interact with the motor as well. So there aren’t really many dumb motors fitted that simply move the wiper blades back and forth although you may find them on the low-end cars. But once you get to a sort of a C-segment vehicle upwards then generally there has to be some intelligence built in. It goes back to the fact that windscreen size and shape is increasing so the arc of wipe gets critical on those windscreens particularly on the wrap-around areas.”
Denso has developed a compact rear wiper motor that allows placement in the top of a vehicle’s rear door. The rear wiper is concealed using the spoiler, which gives the driver an unobstructed rear view.
Pedal power
Meanwhile, Continental has developed a new electric accelerator pedal, known as its accelerator force feedback pedal (AFFP). The company says that its AFFP uses haptic feedback signals – such as a discreet double ‘ticking’ interval or a counterforce in the accelerator pedal – to assist the driver. It adds that trials have shown that drivers are far more responsive to such signals than to warning lights or audible alerts. In addition, claims Continental, by signalling the optimal gearshift point, this human machine interface can lead to fuel savings of up to 7%, depending on the type of vehicle. The central mechanical feature of the AFFP is an electric motor which is linked to the accelerator and which can generate a haptic signal in the form of a counterforce in the pedal. The pedal’s active and passive functions are designed in such a way that it is not possible for the active function to counteract – let alone negate – the effect of the return springs of the passive pedal. This means that the actuator cannot cause the vehicle to accelerate and the required passive pedal return force is maintained at all times.
Steering solutions
Electric motors used in steering systems provide power to the steering wheel necessary to assist power steering systems (EPS). In comparison to hydraulic systems, this system places a lower load on the engine and helps improve fuel efficiency. In North America, GM was the first vehicle maker to electric power steering with its Saturn Vue SUV in 2001, followed by a high-volume vehicle in 2002. In March 2010, TRW Automotive produced its 15 millionth electrically powered hydraulic steering (EPHS) unit and its 10 millionth EPS unit worldwide. TRW’s EAS systems have been in production for ten years and, most recently, the company launched its most innovative EPS belt drive technology on a range of vehicles, including the Ford Fusion, Flex, Taurus, Mercury Milan, Lincoln MkT and MkS.
Matthew Beecham