Value-added glazing products are becoming increasingly important in the automotive market, delivering greater functionality and adding a further growth dimension at a time when the industry needs it most. Matthew Beecham reports on some of the latest developments.
Solar control
The California Air Resources Board (CARB) recently voted to adopt regulations that will require new cars sold in California, starting with the 2012 model year, to have windows that reflect or absorb the sun’s heat-producing rays. Glassmakers applauded this regulation, saying it could present an opportunity for the glass industry to sell more value-added products.
Tom Cleary, Carlite research and development manager, Zeledyne LLC believes that if the CARB regulation goes nationwide, could it stimulate innovation within the automotive glass industry and provide another level upon which competitors can differentiate themselves. He told us: “From the perspective of intent, the legislation is a good thing and for glazing, it gives us the opportunity to add value to our products.
“My concern is in the cost-benefit analysis, particularly with some of the rules that will come into place in the 2016 model year which, with current available technologies, essentially drives you to laminate the entire car set. So that is going to be pretty costly to the end consumer.
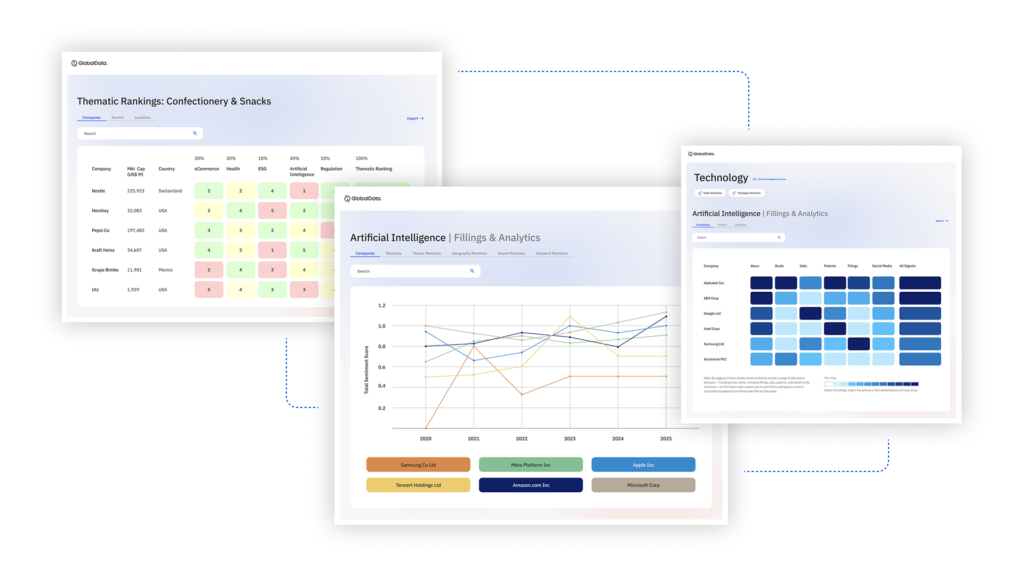
US Tariffs are shifting - will you react or anticipate?
Don’t let policy changes catch you off guard. Stay proactive with real-time data and expert analysis.
By GlobalData“Additionally, laminating the entire car set means that you need to use twice as many pieces of glass and a sheet of petroleum based PVB for each part. This, of course equates to more energy consumption and emissions from manufacturing which need to be accounted for from an environmental impact perspective.”
Mukesh Rustagi, director, strategic product management at Pittsburgh Glass Works (PGW), told just-auto: “I think this [CARB regulation] is great for the industry because the challenge is now out there to come up with more cost effective and better performing value added products. Certainly, it is an opportunity for the glass industry to innovate and provide a more competitive product in the marketplace.”
Pete Dishart, PGW’s global product manager, added: “Some of the overall drivers for laminated glass are the added value benefits of lighter weight and, in particular, reducing sound levels in the vehicle and for security, too. So I think by this regulation driving the use of laminated glass, it will go to help with the acoustics and security. So I believe that it will create a lot of innovation inside the automotive and glass industry as a whole.”
The technologies required for such solar management are already available, as Marijke Bekken of the CARB told just-auto. “The initial standard that we selected was based on the average of these solar controlled glazings that are in use right now in Europe and elsewhere.”
Smaller cars, larger windshields
Higher and wider windshields have also led to the quantity of glass used in vehicle manufacture to gradually increase. The trends in MPVs, for instance, have seen bulky A-pillars become obtrusive for forward vision. Consequently, some car designers are focusing more and more on windshields that wrap around at the sides pushing the A-pillar back towards the front door.
The Citroen C3 had its ‘world premiere’ at the Frankfurt motor show this year. The car is currently offering the largest windshield and smallest roof on a hatchback. Saint-Gobain Sekurit developed and manufactures the windshield, known as the Zenith windshield. Representing a break with the past, there were inevitably certain challenges to design and fit such a windshield as executives of Saint-Gobain Sekurit told us: “The difficulty was to bend such a part because of its size as well as respect the standard specifications for safety comfort and acoustic. This Zenith windshield addresses all the requirements from regulation and costumer expectations.”
The shade band on the Zenith is unique, measuring 600mm compared to a standard band of 250mm.
Saint-Gobain Sekurit executives added: “The design of the shade band was probably the most difficult in order to achieve the TL/TE and shaded aspect required by Citroën. The target was to have a shade perfectly fitting with the car design.”
Glassmakers report that such small cars with large windshields is a clear trend for the future.
Chris Bolton, Pilkington Automotive’s global product manager for automotive products, trims and antenna told us: “Once people start to appreciate the feeling of light in their car then it is very difficult to reverse that trend. Consequently, we have seen some OEMs introducing larger windshields such as those featured on the Opel Astra GTC and Citroën C3 while others, such as Peugeot, are extending the rooflite downwards. Both glazing designs represent challenges to the glassmaker because you are either shaping the front of the glass or a very big windscreen.”
Andy Richards, Pilkington Automotive’s global product manager for automotive products, sidelights, backlights and rooflights added: ”The shape of the glazing on its own does not really represent the product. You need to bring in the other customer product requirements to make a total product. Additional functionality like solar control are absolutely key. For instance, the large shade band on the new C3 offers two main benefits: glare reduction and good solar control. Bringing these products together is what we need to be looking at as we develop tomorrow’s complex glazing in vehicles.”
Carlite’s Cleary added that in North America, the market is seeing larger, more complex windshields with separate glass roofs. “We are seeing a lot more of that on some of the larger cross-over vehicles where we see, say, two glass panelled roofs. And with that design, you can paint the glass so that you can have different sections visible from the inside of the vehicle. We are excited about that from the aftermarket perspective, too. “
Kevin Reynolds, Butacite product manager, DuPont says that most car designers like the ability to open up the cockpit to offer that feeling of driving a convertible. “That trend will continue,” he said. “The question then becomes: how do you protect the occupant in the event of a rollover? And how do you make it so that there is not too much heat build-up? And then how do you make sure that the glass does not become a very expensive part?
“Also, if the glass cracks then it becomes expensive to replace. I think that you will see that happening more on smaller cars. Generally speaking, however, growth in larger sunroofs and more vehicle glass will continue. You will see more all-glass canopies.”
Meanwhile, the boundary between the windshield and the glass roof on some vehicles is decreasing all the time. Rod Watson, Carlite’s technical services manager, Zeledyne LLC, points out that there can be a fairly small margin between the windshield and the roof glass nowadays.
“One of the reasons why you may not want to have the windshield glass go into the roof is the issue with glass replacement cost,” said Watson. “Very tall and complex bend windshields would be difficult to make and expensive to package and ship. Additionally, there would be optics issues that would have to be overcome due to the amount of bend required to transition from the normal windshield rake angle to the roof. Of course, some of the distortion could be hidden with ceramic paint but still represents some fairly big challenges.”
Laminated side glazing
For some time, Europe has led with the adoption of laminated side glass for increased vehicle comfort and security. The first North American vehicle with laminated sidelights was launched in 2002 with market demand catching-up Europe.
Watson told us: “We are seeing a clear upward trend for the products that we are providing for Ford, especially for front door applications due to the acoustical benefit that comes with that value-added product.”
Dishart added that the recessionary climate has certainly reduced the total number of builds which, of course, has reduced the volume of all glass provided. “But we are continuing to see a strong interest in offering laminated side glass on new vehicles based primarily upon the acoustic attributes of the product. So I do expect that to continue to grow. The question then becomes how much additional growth will be driven by the CARB regulation for 2016?”
Polycarbonate glazing
Although the idea of replacing glass with lighter weight plastic sounds like an obvious innovation, it is not new. For over thirty years, auto glass experts have explored the potential for polycarbonate as a replacement to glass.
Compared to the shape limitations of glass, plastic (polycarbonate) glazing is highly versatile. It is also lighter by as much as 50% and has high impact resistance. Suppliers claim that a total weight reduction of more than 20kg (50%) is possible when replacing all glass windows (except the windshield) for a standard minivan. Vehicle manufacturers can now consider 3D-shaped windows, innovative designs and locations and new opening and closing mechanisms.
Richards told us: “The high profile surrounding polycarbonate glazing today is probably a bit lower than it has been historically. But we have still yet to see a strong introduction in the vehicle industry. I think certain barriers to using this technology have been overcome. However, cost remains an issue. Also, reliance on where the material has come from, i.e. is it sustainable or not? That said, we believe that polycarbonate will feature in the future but market penetration is yet be determined. It offers very clear styling advantages in some areas over glass.”
In terms of integrating antennae into polycarbonate, Bolton points out that getting any sort of conductor onto polycarbonate glazing is a challenge. He said: “You can certainly use antennae on plastics but the issue is about finding a cost-effective way of laying a conductive heating grid down onto plastic.”
Head-up displays
Head-up displays – or HUDs — are gradually becoming popular. A HUD is a system which projects a visual image at a distance of about 2-metres in front of the driver. A projector located in the dashboard projects an image which, when reflected on the windshield, appears like a virtual image on top of the bonnet. There are, however, some special characteristics of the PVB interlayer fitted into the windshield in order to realise this function. DuPont claims market leadership as far as the PVB interlayer is concerned.
“We have a patented product called The Wedge™,” commented Jeff Jirak, global business manager, DuPont Safety Glass Business. The wedge angle is dependent on a series of factors, namely the position of the driver, the mounting angle and the shape of the windshield and the glass thickness. This means that there is a specific wedge angle for each car model. For a HUD, the layer has to be designed to be thicker thinner at the bottom and narrower thicker at the top to focus a projected image from the instrument panel.”
Sealing systems
For some time, there has been a desire for an overall smooth aerodynamic style to the vehicle. Glazing systems have been fulfilling this desire by having smooth curved windows with flush seals.
In particular, the use of single-side window attachment systems such as encapsulation together with the hardware mounted on one side of the glass has grown in response to this need. Such systems reduce drag and noise, improve fuel economy and provide a good aesthetic appeal.
In terms of the trends in encapsulated glass, three types of materials are used in the process, namely PVC, PUR or RRIM, and TPE. For some time, Magna Sealing and Glass Systems has honed its expertise in all three materials. So what determines the use of one material over another? Bruce Warren, division general manager, Magna Sealing and Glass Systems, told us: “PUR used to be the technology of choice. However, due to the cost of those materials, it has been really relegated to specialised applications, specifically certain encapsulations where you need some structure to attach a piece of metal to a glass or just to form the structure around the glass itself.
“The PUR technology is also used for very large and complex windows that styling designers at the OEMs have decided that they would like encapsulated. A windshield or a backlite would be a good candidate for this technology. This technology is best suited for these large pieces of glass because by being able to encapsulate under the low pressure that PUR or RIM utilise, there is a much smaller chance that you would break the glass in the mould.
“PVC is the lowest cost option. PVC unfortunately is not the most environmentally friendly material and because of that, some OEMs have made a move to TPE. TPE is used for a couple reasons. One is because it is a “green” material. The other is that TPE has sealing characteristics that PVC doesn’t have. PVC is essentially just a plastic but TPE allows you to mould sealing features onto the glass as well.”
The vehicle designers drive the choice of adhesive and moulding processes used.
Warren added:”What we found is that it really depends on what they are trying to do with the glass itself. For example, backlites in some applications integrate the trunk seal as well. In a case like that, it would require an encapsulation. But the other reason is really driven by design. Some vehicle styling studios prefer the PVC look versus the flush look. That drives almost everything right now. We can accomplish really almost anything with a flush glass look if you want it.”
As far as glass run channels are concerned, Chris Bitsakakis, group general manager, Magna Sealing and Glass Systems says there are no significant technical differences in requirements between automakers. In Europe, however the rubber industry is a little more entrenched and set on a specific set of materials.
Bitsakakis told us: “There are some people in the traditional rubber sealing industry who feel that this particular change is not required. I think this perception is more about past practice than true concerns about the technology. Some people in the industry have been using EPDM rubber exclusively for 20 – 30 years and don’t really see the need to change yet.
“Some of the German automakers, for example, are also looking at glass run channels to act as a trim component. This approach makes the glass run channel more visible to the end consumer. Due to this added visibility, the German OEMs prefer a low gloss rubber appearance. They compliment this low gloss rubber appearance with a brushed aluminium or anodised greenhouse moulding as part of the overall styling theme on these vehicles. In contrast, the North American OEMs will migrate towards higher gloss black material and bright stainless steel trim. The Japanese automakers are trending towards styling themes that are more similar to the North American theme, but the requirements for wind noise reduction and ease of glass travel is quite similar amongst all the OEMs.”