Demands on powertrain cooling product performance, packaging and cost are continually increasing. As automakers expect economical solutions that help reduce emissions from cars and trucks, Matthew Beecham reports on how the leading suppliers are responding.
Drivers of change
Arnaud Gandon, chief engineer, global powertrain cooling and heat exchangers, Delphi Thermal, believes that there are several factors driving changes in the powertrain cooling sector.
“From a technology standpoint, the increasing demand for more diesel, turbo-charged engines and hybrids is driving new and improved technology along with more efficient transmissions that sometimes require heating as well as cooling.
“From a packaging point of view, Delphi expects that there will be a need to combine heat exchangers like the combicooler as well as wider use of charge air coolers. There is a legislative push to capture the heat from the exhaust and use it for cabin heating or transmission heating. For hybrids, there is also a need for a new heating source like an immersion PTC heater which drives electronics for operation and safety.”
Packaging concerns
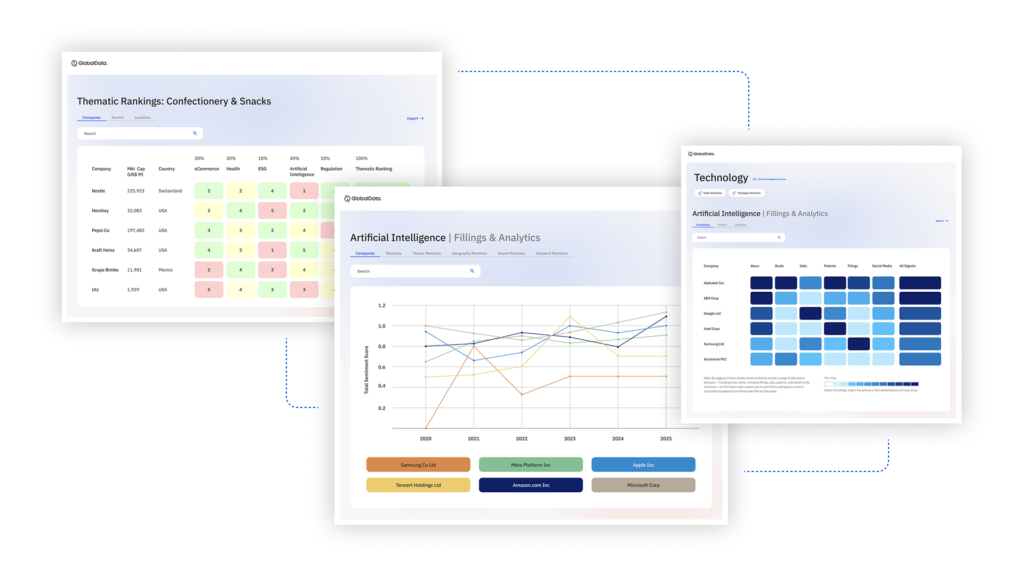
US Tariffs are shifting - will you react or anticipate?
Don’t let policy changes catch you off guard. Stay proactive with real-time data and expert analysis.
By GlobalDataPackaging the cooling system is certainly a major driver of innovation. Given the pressure on suppliers to squeeze higher performing products and systems into a smaller space under the bonnet, radiators have gradually become smaller in size. For example, a modern aluminium radiator is about two-thirds the size of a unit produced in the late 1970s. The high cost of fuel, particularly in Europe, means that designers are seeking ways of reducing the airflow in the car, which is leading towards the use of smaller heat exchangers.
“Pedestrian impact regulations and insurance tests are becoming ever more stringent,” said Gabriele Maione, R&D manager, engine cooling systems and components, Denso Thermal Systems SpA.
“Car manufacturers and suppliers therefore have to join efforts to fit the increasing number of components under the bonnet, and meet European regulations. To do so, Denso is studying new heat exchangers with higher specific heat rejection, i.e. higher heat exchanged per surface unit. This may lead to smaller heat exchangers that can be more easily fitted into the front-end. Engine module fixations also have to be changed to aid damage reduction and serviceability. Moreover, Denso is developing indirect exchangers (e.g. water-cooled CAC) that can be positioned under the bonnet to make the front end module simpler and lighter.”
Not only are auto powertrain cooling parts becoming smaller but there is a clear trend toward more component integration. For example, combining the condenser and radiator can save space and help cut costs. Modularity plays an important role in packaging engine cooling systems. This approach can, of course, help cut costs and simplify the entire installation on the assembly line.
For its part, Visteon has optimised its fin and tube geometry to increase heat dissipation per unit core depth enabling weight reduction, vehicle package reductions and giving an increased output for a smaller package. The reduced core thickness also leads to lower airside pressure drops allowing low power cooling fans and less electrical load. Visteon claims that all of these are key factors in helping reduce overall vehicle weight, improving fuel economy and reducing emissions.
“A good example of the success of this activity,” says Nigel Seeds, senior application engineer for Visteon, “is our 10 mm radiator core recently launched in the Ford Fiesta. This replaces the significantly deeper core found on the previous model, reducing package space and component weight. This radiator has the smallest core depth currently in production on a passenger car and can be up to 25% lighter than a competitor’s equivalent product.”
Other changes regarding the increasing pressure cycle has led to design changes to the radiator itself. Richard Armsden, senior application engineer for Visteon points points out that standardised and enhanced designs have been refined so products can withstand the increased component durability requirements. He told us: “In addition to the drive for higher pressure cycle resistance we have also seen increased interest in thermal shock resistance of radiators. Specifically, Visteon has developed and patented two technologies which we believe give us a competitive advantage.
“The first we call a trapezoidal header: The joint between the header and the tube is generally the area of weakness for both pressure and thermal cycle tests. Illustrated in the graphics below, a normal header is flat and the highest stress regions are concentrated around the nose of the tube. The trapezoidal form moves the highest stress away from the nose and distributes it more evenly across the tube to the header joint, significantly reducing the maximum stresses seen in the joint. The result is a more robust joint which will extend the life of the part in service.
“The second technology we call ‘strong fin’. This is directed more towards pressure cycle testing, providing more support to the tube by reducing deflection in the tube itself and, as a result, reducing the stress. Adding form to a flat surface significantly increases its ability to resist compressive forces, and that is the essence of the concept.”
More use of electronics to help maximise fuel efficiency
Generally speaking, in respect of fuel economy, there a trend toward more use of electronics to try to more closely monitor engine temperature for maximum efficiency i.e. using electronic thermostats and electronic water pumps to completely take control of the heat rejection itself. But there is always a trade-off the carmaker must make between adding weight and cost (through electronics) and saving fuel.
Guillaume Hebert: There was a lot of interest in the industry for electronically controlled cooling systems five or so years ago,” said Guillaume Hebert, EGR product development manager for Visteon. “Visteon has previously demonstrated a system on both a petrol and diesel application. The system includes an electronic valve, electric water pump as well as a control model and associated software. Fuel consumption benefits of up to 5% were demonstrated but there was only limited interest at the time from the vehicle manufacturers – primarily due the additional cost to the vehicle associated with the required hardware.”
Maione adds that fuel economy is attracting more and more interest from carmakers. “This is largely due to the new environmental laws that fix limits on pollutant emissions and incur fines for any transgression. Carmakers and suppliers are considering a very wide range of devices to reduce fuel consumption. Electronics can help the engine temperature to warm up faster, for example, to reduce friction and cold start problems. Working together, carmakers and suppliers are evaluating the effects of such devices to understand both the benefits and the costs. This is not only related to fuel economy; use of these devices has also some indirect benefits. For example, the electrical water pump can avoid overheating at engine shutdown.”
On balance, we should expect to see further innovation in cooling systems and components due to the trends noted here. The challenge for suppliers will be to meet demands from automakers for improved engine efficiency and output, as well as respond to rising production of diesel vehicles and direct-injection and turbocharged gasoline vehicles. In terms of social trends and legal regulations, the supply sector will continue to face demands for improved fuel efficiency due to surging gasoline prices and stricter fuel consumption regulations, as well as for more compact and thinner radiators and other parts in response to the more stringent legislation designed to protect pedestrians.