Ignition system technology has taken a number of twists and turns over the past 50 years. Matthew Beecham reports on some market and technical trends.
In the late 1940s and 1950s, the ignition unit consisted of an ignition coil and distributor that delivered the voltage generated by the ignition coil to the ignition plugs. Following this product, mechanical power distribution evolved into electronically distributed power. By the early 1980s, the integrated ignition assembly appeared, combining the distributor, ignition coil and driving circuit (igniter). This basically eliminated the need for a high-voltage cable between the ignition coil an distributor, thereby further improving product reliability. During the mid-1980s, distributor-less ignition appeared.
High-voltage generated by the ignition coil was directly applied to the ignition plug. The distributor was eliminated resulting in a lighter unit. Product reliability was further improved by electrically controlling high-voltage distribution and ignition timing. By the mid-1990s, the stick coil began to appear featuring a smaller igniter. Today, there are basically three categories of ignition systems: coil ignition, capacitive discharge ignition, and other types such as AC-Ignition. Coil ignition is the most popular system.
An executive from Bosch told us: “Over recent years the trend has been for the combination of ignition and fuelling systems into integrated Engine Management Systems (EMS). These share common sensor inputs, partially common electronics but obviously separate output functions. These EMS systems which offer fully mapped ignition parameters have now been virtually universally adopted for the control of gasoline engines.”
In terms of ignition coil performance, carmakers continue to demand reliable, smaller units. Multi-valve engines in particular place even greater size limitations on coil design. “The European trend towards down-sizing gasoline engines is prompting the need for smaller, narrower and longer spark plugs,” said Dr Rainer Podeswa, member of the executive board, responsible for R&D with Sales OEM, Beru AG. “Spark plugs must last longer, too. Ignition coils are also becoming smaller and lighter despite the requirement for increased energy content. This has led to more use of so-called plug top ignition coils which typically have higher energy content compared to pencil coils. We see the US and Asian markets following this trend.”
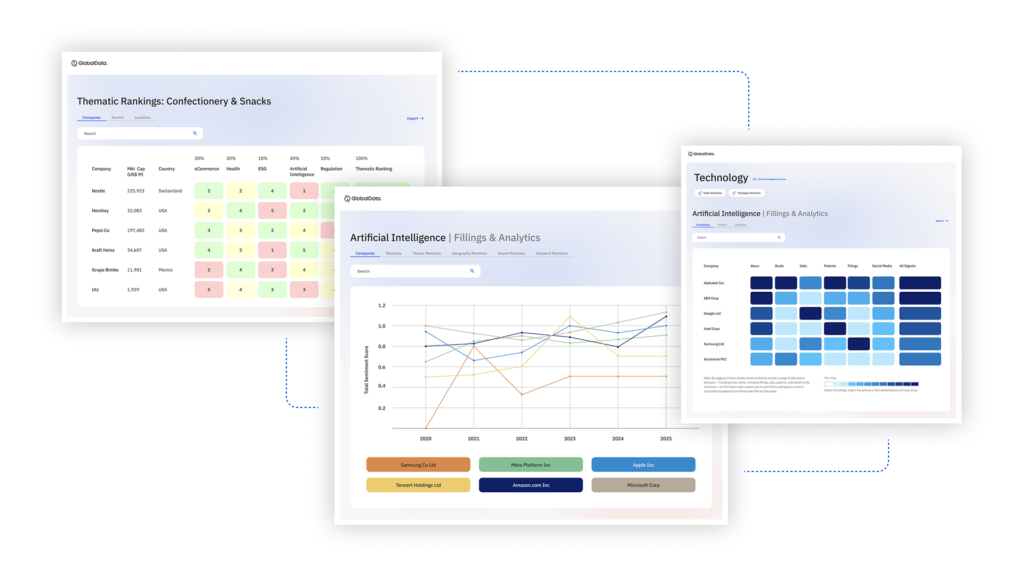
US Tariffs are shifting - will you react or anticipate?
Don’t let policy changes catch you off guard. Stay proactive with real-time data and expert analysis.
By GlobalDataBeru AG’s ignition technology division designs and produces a variety of parts in the ignition chain, from spark plugs, ignition cables and connectors to ignition coils. The company supplies ignition coils to a number of carmakers, including DaimerChrysler, Fiat, Hyundai-Kia, Porsche, Renault and Volkswagen. In outlining Beru’s ambitions in the ignition coil market, Podeswa said: “Beru is considering the ignition coil market as strategic and important. Our engineers are working on the further development of plug-top and pencil ignition coils, as demand for single-ignition coils is expected to increase in the next two years.”
Beru works closely with a number of carmakers to develop novel ignition coils. For example, Beru developed especially for the Maybach pencil-type ignition coils that are tightly packed in groups in 12 in electronic ignition rails with diagnostic functions. Beru also developed pencil-type ignition modules with integrated electronics for the Porsche Cayenne V8 engine. This module is lighter and provides 25% greater spark energy and combustion duration compared to other sports car ignition coils. It is also used in the V10 engine of the Porsche Carrera GT. Beru’s engineers are currently working on the further development of plug-top and pencil ignition coils, as demand for single-ignition coils is expected to increase over the next few years.
For some time, manufacturers have packed increasing amounts of electronics into the ignition coil. The Japanese suppliers led the trend followed by the Europeans although it is not universal. It depends on the philosophy of each carmaker in terms of where they want to put their igniter electronics.
“In recent years, ignition coils with built-in igniters has become more common and most ignition coils in Japan have built-in igniters,” said Akimitsu Sugiura, chief engineer of the Engine Control Components Engineering Department of Denso Corporation.
“In Europe, on the other hand, there is a mixture of types with igniters integrated with ignition coils or engine ECUs. With the ECUs becoming more advanced, it is seen better to integrate igniters with ignition coils to hold down the ECU’s size, radio noise and heat generated.
“Although in Europe, we think that the ignition coils with built-in igniters have not become so common because the engine ECUs with built-in igniters diffused in the market first, and because igniters are required to have higher reliability [heat and noise resistance] to be integrated with ignition coils than ECUs.”
Denso Corp’s gasoline engine-related product portfolio includes ignition coils. The company manufactures ignition equipment at its factories in Japan, the US, Brazil, and China.
Another trend is toward increasing energy requirements. For example, the trend toward direct injection gasoline applications is driving the need for higher levels of ignition energy. As a result, those levels of ignition energy can only be delivered by coil and plug type applications. An executive from Bosch told us: “With the constant demands for increasingly fuel efficient engines it naturally means that we are looking to ignite ever weaker fuel/air mixtures this has resulted in increasing ignition energy requirements. Gasoline Direct Injection (GDI) does not in itself necessitate higher energy levels, but since direct injection is being used as a tool to improve fuel economy and meet increasingly stringent emission regulations then of necessity we are seeing a trend of increased ignition energy going hand in hand with the development of GDI.”
Denso also sees a clear trend for more energy requirements being driven by direct injection gasoline applications and emissions regulations. Sugiura added: “For gasoline direct injection, the energy requirements are increasing, especially at lean combustion. For a spray-guide engine, it is said that 80 to 100 mJ energy will be required. Besides the gasoline direct injection, several technologies including Port Fuel Injection homogeneous lean combustion and Exhaust Gas Recirculation have been developed to comply with fuel consumption regulations. For both these systems, the energy required increases to improve ignitability at lean combustion.”
As far as the aftermarket is concerned, ignition systems in modern cars require very little maintenance. “It is generally accepted that the traditional ignition components are part of a dying breed,” said an executive from Bosch.
“This is certainly true when looking at OE technology, but there are still a lot of cars on the UK roads still using these older parts. The ignition distributor, its spare parts (caps, rotor arms) and electronic ignition components and control units still account for a large proportion of our ignition business. In fact the demand for many obsolete distributors means that these units form a part of the thriving exchange programme, allowing us to be able to supply parts that are now out of series production but also at an economically viable price.”
As direct ignition systems enter the replacement cycle, there is likely to be greater demand for coils and engine control units. “For the past few years the emphasis on ignition coils has grown,” said Bosch. “They are seen as a real opportunity area. Bosch has identified the importance of these parts and over the past few years has been developing the aftermarket range beyond our excellent OE coverage to become a genuine all makes range, whilst still retaining the all important OE specification and OE quality for all part numbers offered.”
Future design challenges for ignition coils will focus on developing even smaller units, while continuing to meet extremely high insulation and temperature requirements. In addition, they will incorporate electronic circuits. An executive from Bosch told us: “In 2005 the world market share of ignition coils with integrated power stage was about 31%. In 2010, [we expect] the world market share of ignition coils with integrated power stage will be about 52%. It depends on customer strategy.”
Sugiura, believes that with the trend in recent years of more stringent EMC regulations, there is greater demand for ignition coils to integrate noise resistance and/or condensers in order to reduce the radio noise generated and transmitted from ignition coils. He added: “With the more stringent regulations on fuel consumption and emissions, research has progressed for ionic current detection to accurately detect the combustion condition of the engine. This detection method has been put to practical use for detections such as ignition failure. The ionic current detection, however, has several issues to be solved to diffuse in the market. In the future, we could expect an ignition system that supplies appropriate energy that changes in accordance with driving conditions.”
Electronic ignition also means that the traditional ignition cylinder is no longer necessary. So could we see the conventional ignition cylinder gradually phase-out? “Yes,” said Winfried Menge, director of marketing electronics, Hella KGaA Hueck & Co.
“The mechanical ignition cylinder could disappear in future, but the mechanical key as an emergency and back up option will be maintained for the reasons you’ve mentioned for a couple of years. From a system point of view, if a general electrical or electronic failure prevents cranking, starting the engine or activating the transmission system – why should we need a mechanical backup for the key? It would be useless. Either we trust the electronic or we don’t. Consumers have to get used to technical progress and we, the automotive industry, have to prove that our innovations are not just gimmicks but meaningful products which provide a visible and valuable benefit.”
See also: Global market review of ignition systems – forecasts to 2012