Fueled by the need to save weight and reduce evaporative emissions, a great deal of innovative design and materials work is going into vehicle fuel tank systems. Matthew Beecham reports on the ongoing plastic versus steel tanks debate.
In the early 1970s, all fuel tanks were of steel. Since then plastic fuel tanks have superseded steel to the point where more than 90% of all light vehicles built for the European market are made of plastic. Plastic fuel tank manufacturers are quick to point out the benefits of plastic over steel, including lighter weight, non-corrosive and geometric flexibility. They believe that the trend in favour of plastic fuel tanks will continue to grow until the market is saturated.
On the flipside, steel makers argue that some carmakers are re-evaluating plastic tanks in favour of steel. The steel giant Corus is already supplying Ford with its Neotec steel for fuel tanks in the Ka. The lead-free metallic-coated steel was launched in February 2003 just in time for the ELV directive, which swung into force six months later. Neotec has been specifically designed to help carmakers meet future environmental legislation that requires emission-free fuel tanks, and sets recycling targets for vehicles at the end of their life.
Neotec is a hot-dip tin-zinc alloy coated steel available in sheet or coil. Its properties allow it to be formed into complex shapes using conventional stamping and welding processes. The ELV directive requires that manufacturers reduce or remove certain hazardous materials including lead from vehicle components. ELV material recovery or re-use rates must be over 85% of the whole vehicle from January 2006, and over 95% from January 2015. With an average vehicle life of 14 years, new cars should reflect this requirement today. Corus says its new steel for fuel tanks stands up well to corrosion, with an expected service life of 15 years.
Although plastic tanks are superseding steel tanks in the European automotive market, Corus reports good prospects for its Neotec in North America. Jonathan Parkes, commercial manager for Corus Strip Products UK, told us: “We are in discussions with major OEM’s and their suppliers in North America regarding coming programmes for steel tanks with biodiesel fuel. However, these vehicle manufacturers are concerned about the material they currently use for fuel tanks, typically plastic or a zinc-nickel based steel with a post paint treatment. This can have performance problems with biodiesel fuels, especially when water is present in the fuel. If water is somehow mixed in with biodiesel, it turns into a nasty brew. These vehicle manufacturers are also concerned about the use of biodiesel in plastic tanks since the fuel can actually soften plastic due to the way in which common rail fuel injectors operate by warming-up the fuel.” Corus is also looking at applying Neotec to vehicle radiators and motorcycle tanks in the Far East.
How well do you really know your competitors?
Access the most comprehensive Company Profiles on the market, powered by GlobalData. Save hours of research. Gain competitive edge.
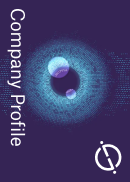
Thank you!
Your download email will arrive shortly
Not ready to buy yet? Download a free sample
We are confident about the unique quality of our Company Profiles. However, we want you to make the most beneficial decision for your business, so we offer a free sample that you can download by submitting the below form
By GlobalDataOn the other hand, plastic fuel tank manufacturers argue that there are no serious issues with storing biodiesel in plastic tanks. Jean-Francois Berard, vice president, R&D, marketing and industrial, Inergy Automotive Systems, told us: “We are having more and more discussions with OEMs in Europe about biodiesel and the impact on fuel systems. Apart from just a few precautions – like ensuring certain materials are used for some parts — we can say that there is no impact whatsoever. For the past five years, we have stored biodiesel in tanks under different conditions and can confirm that the product did not deteriorate.”
Above all, Keith Leadbeater, business development manager, Delphi Diesel Aftermarket, believes that that there is a general lack of awareness of how biodiesel can deteriorate if left for too long. He told us: “Biodiesel is not as stable as traditional diesel fuel. Although the recommendation is to use biodiesel within three to four weeks, a large tank of biodiesel may not be emptied for several months and will degrade more than the owner anticipates.”
Despite these issues, there still doesn’t seem to be any basic research into fuel storage and its effects. Leadbeater added: “Although the EN590 is a base level standard for fuel, when stored some changes in the fuel can occur. For example, temperatures can affect the condition of the fuel. There is also concern among fleet operators that if they don’t look after their fuel tanks properly this can result in a build-up of water and algae, particularly in diesel which can affect a vehicle’s fuel injection systems.”
In an attempt to make carmakers reconsider steel fuel tanks, the American Iron and Steel Institute formed SASFT (Strategic Alliance for Steel Fuel Tanks). As the name suggests, SASFT is an international alliance of companies specializing in the various areas of fuel tank production. SASFT’s programme manager, Peter Mould, told us: “When we founded SASFT in 2000, steel tanks were certainly not perceived to be as durable as plastic tanks. Since then, we have managed to convince the user community that steel tanks represents a viable option to meet the 15-year durability requirements demanded by the Californian Air Resources Board. Given that driving range is important for the vehicle manufacturers, fuel tank capacity remains a big issue. So we are currently looking at ways in which to modify steel tank design in order to optimize its capacity. One way of doing that is to reduce or eliminate the flange around the tank thereby completely filling the allowable engineering space. If we can develop methods to make flangeless tanks then that will further improve steel’s position.”
Although steel industry sources acknowledge the benefits of plastic tanks, they believe that the tide is turning in their favour. They argue that, in the long-term, the environmental and cost issues will win back a larger share of the steel fuel tank business. They reckon that they can make steel tanks with the same amount of design flexibility as plastic. Mould added: “When we look back at what happened in terms of the development of plastic tanks initially in the late 1970s and early 1980s, the trends at that time favoured plastics. The biggest issue back then was the very low cost mono-layer plastic tanks that were being introduced. These tanks were also seen to be more design flexible, lighter, and more durable than steel tanks. But we believe that those advantages have since been nullified. So we are expecting to see a turn-around over the next few years toward the increased greater use of steel tanks because of the PZEV requirements, increased cost competitiveness, improved performance of steel tanks and their sustainability.”
While multi-layered plastic certainly appear have become the material of choice for carmakers, there are still some concerns over its recyclability. Yet plastic tank manufacturers argue that their products can be 100% recycled, re-used and revalorised during the manufacturing process or at the end of the vehicle’s life. Inergy Automotive Systems’ Berard added: “Plastic fuel tanks and all the constituent parts can be 100% recycled. There are some studies that have been done over the last year by Solvay and Renault. We have presented those on a number of occasions. So for us, the question whether or not plastic tanks can be recycled is not an issue.”
PZEV (partially zero evaporative emissions vehicles) is one of the most stringent Californian environmental regulations. Adopted in 2003, it requires vehicles to reduce their fuel emissions by a factor of ten, to under 54 mg of hydrocarbons per vehicle per day, from an equivalent of 600 mg in 2001. Although plastic seems to have become the material of choice, steel makers raise concerns that such tanks cannot actually meet the PZEV requirements. So could steel tanks really make a comeback? “No,” said Inergy Automotive Systems’ Berard. “In terms of the Californian regulations, we have already developed a plastic fuel tank which satisfies the PZEV requirements. This tank design will go to production in June 2006 for Nissan and General Motors. Given that plastic fuel tanks are more price competitive than steel tanks, we expect to see more of them passing the PZEV requirements.”
In the steel tanks corner, SASFT’s Mould reckons such fuel tanks are already making a comeback. He told us: “In our opinion, steel tanks are the material of choice to meet the PZEV standards. Virtually all of the PZEV fuel tanks are steel. Although plastic tanks can meet these requirements, plastic tank producers are dialing in more cost into their tanks. So that can only increase the competitiveness of our steel tanks.
Additionally, rising oil prices are likely to increase the price of plastic tanks still further.” In backing-up SASFT, Ray Sheffield, director, fuel tanks, Martinrea International, added: “As far as the California-led PZEV emissions standards are concerned, one thing that we consistently hear from those close to the Californian Air Resources Board is that their next revisions after 2010 may make PZEV-level evaporative emissions pretty much the norm. We also hear that from some OEMs. They are making contingency plans for that.”
On balance, although plastic appears to have almost eclipsed steel as the material of choice by carmakers when sourcing fuel tanks, we see the market beginning to plateau. In North America, just-auto estimate installation rates of plastic tanks are about 77% increasing to 81% by 2012. In Western Europe, just-auto estimates that installation rates of plastic tanks are currently at 91% with potential to reach 97% by 2012. Although the use of plastic tanks is dominant in Europe and North America, Japan still favours the steel tanks mainly for its lower cost. Today, just-auto estimates that installation rates of plastic tanks in Japan are at 26% with potential to reach 31% by 2012.
Matthew Beecham