From humble beginnings, the modern exhaust system has become a hotbed of expensive technologies, playing a decisive role in controlling emissions and acoustic comfort. Matthew Beecham reports.
Technical developments in the hot-end of the exhaust — the section closest to the engine, linking the manifold, catalytic converter and particulate filter — are highly influenced by the new emissions legislations. Consequently, we are seeing the emergence of new exhaust system technologies for both gasoline and diesel engines.
“The main forces driving the automotive exhaust systems industry are the emission and fuel economy targets,” said Mauro Occhetti, marketing and sales director, Magneti Marelli Exhaust Systems. “Exhaust suppliers are requested to support the carmakers to reach these targets and assure comfortable noise attenuation without over-design in order to guarantee a low system cost.”
As each new emissions regulation swings into force, more and more content is added to the exhaust in order to comply. “We already have all the technology required to make the diesel engine really clean,” said Oliver Pfirrmann, marketing manager, Emission Control Europe, Tenneco Inc. “Our predictive tools and virtual design and development capabilities allow us to accelerate the development of leading edge products for our OEM customers.”
The European Commission’s plans for Euro 5 emission targets would cut particulates from new diesel engines by a factor of five, make permitted NOx limits much tougher for gasoline and diesel models and raise the durability requirements for emission control systems like catalytic converters and particulate traps. Maximum particulate levels under the latest Euro 4 standards are already 90% tougher than they were 15 years ago. Under the new proposals, limits would be cut further, from 25 to five milligrams per kilometer.
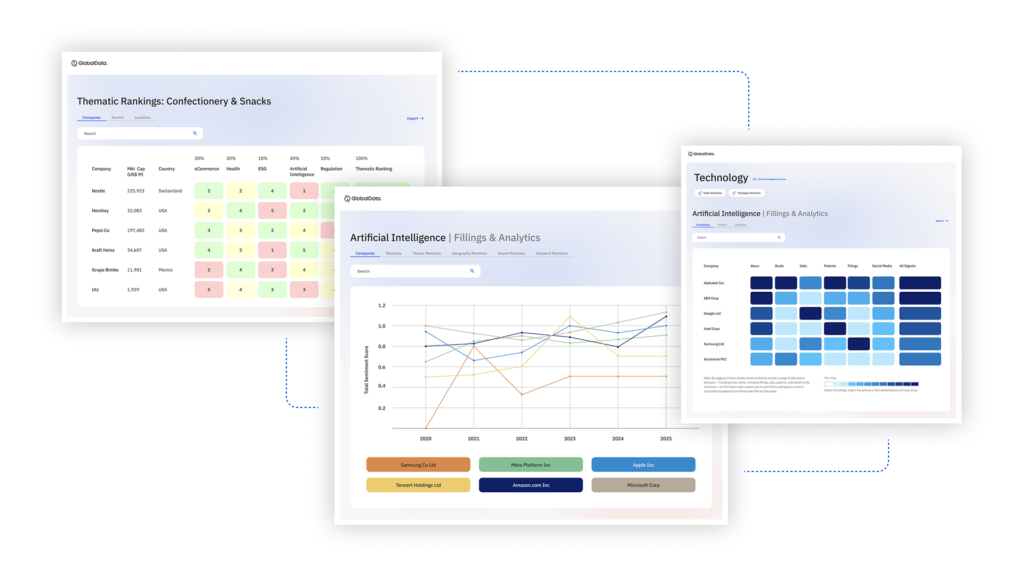
US Tariffs are shifting - will you react or anticipate?
Don’t let policy changes catch you off guard. Stay proactive with real-time data and expert analysis.
By GlobalDataThese levels mean new diesel cars and vans will need particulate traps, increasing their prices. Trade bodies warn that tighter emission controls will cost vehicle buyers. The UK’s Society of Motor Manufacturers and Traders (SMMT) said this could make diesel less attractive to potential buyers and halt the diesel car sales boom seen over the last six years.
“The price trends for exhaust systems depend on the specific chosen technology to after-treat NOx,” added Occhetti. “For example, for the SCR technology it is necessary to add the cost of the urea tank, its dosing equipment and refill. However, similar to diesel particulate filters (DPFs), initial costs are progressively reduced by new technical solutions entering the market. From our side, we are exploring a new solution based on the evolution of the classical EGR effect, which could avoid the introduction of NOx after-treatment for Euro 5/6 limits.”
A particulate trap collects soot particulates flowing through the exhaust and burns them off periodically. Cars fitted with these filters have been proven to produce 10,000-times fewer particulates than cars without the filters. “In the run-up to the introduction of Euro 5, diesel particulate filter equipment will be state-of-the-art for most of the OEMs and all big vehicle markets,” said Mathias Keck, vice president, global engineering, Eberspächer.
“Close-coupled filters will continue to be preferred to under-floor position. The coated filters, like those Eberspächer brought to full scale production with some of its customers, will be the state-of-the-art technology than uncoated filters using additives.
“For cost reasons, cordierite substrates will become the main alternative to more expensive substrates. We are working on the improvement of filter efficiency by optimizing the gas flow. We are intensifying our simulation capabilities, allowing us to better predict gas flow, soot deposit and ash storage in the filter as well as the extension of the regeneration process in the filter. This leads to an optimal gas flow and maximal efficiency of the filter volume by design of the inlet an outlet cones and the form of the filter. This could result in a reduction of the filter size.”
Tenneco has been a forerunner in developing and producing particulate traps. “We were one of the first to participate in the DPF market,” said Pfirrmann. “That gave us an advantage. Given that we supply emission control technologies to virtually all the major European carmakers, that gives us greater access and scope to expand our DPF business.” Tenneco recently expanded its capabilities in DPFs and won new business in Europe. It currently supplies DPFs to OEMs including PSA Peugeot Citroen, Mercedes-Benz and Audi.
Tenneco also recently began offering retrofit DPFs for the European independent aftermarket ahead of the introduction of the European Union legislation and tax incentives on retrofit units that have swung into force in some European countries. The sheer size of the European diesel car parc makes the retrofit DPFs a significant new aftermarket business opportunity.
Pfirrmann added: “We already have our own retrofit DPF technology available. We also have an aftermarket catalogue available covering most engines in Europe. We believe that the government incentives for motorists across certain European countries to equip their vehicles with DPFs will result in a huge market opportunity until such a time as DPFs become a standard feature on all new vehicles.”
Meanwhile in the recording studio, Eberspächer’s exhaust engineers are also busy hitting the right note for OEMs, developing exhaust acoustical solutions. Keck added: “We are very well positioned with a range of tools and methods in virtual development; partly with proprietary software applications. This, and our own sound studio, enables us to predict a result very close to the end product in a short timeframe with a minimum of hardware prototypes using our own sound laboratory.”
Eberspächer has designed a semi-active flap to tune the outlet noise and the exhaust back-pressure according to the driving situation. At low engine speeds, the exhaust flap closes one of two exhaust tailpipes. Consequently, about two-thirds of the low-tone exhaust noise disappears. At high engine speeds, the pitch of the exhaust noise rises. In this situation, the exhaust back-pressure is reduced by opening the flap allowing the gas to flow through both tailpipes. The exhaust flap is controlled by a vacuum transducer that is installed outside on the tailpipe. A hose line, run in the cable harness, supplies the necessary suction pressure. The engine control unit controls the exhaust flap according to engine speed, load and temperature by an electric switching valve.
Tenneco has also used it expertise in developing exhaust systems that generate desired engine sounds to help OEMs differentiate their vehicle brands. These sound and engineering capabilities were applied on the VW Golf GT and BMW 1 Series. “Our approach is to apply so-called asymmetrical separated manifolds to the down pipe in order to modify the sound,” said Pfirrmann. “Pipe length, diameter and junction are important ways in which to modify the sound. We use our prediction tools to find the best combination of measured parts. On the rear pipe, we also modify the sound using different techniques. For example, we can apply special inlets/valves along the rear pipe.”
Turning to catalytsic converters, although Emitec concedes acknowledges alternatives/threats to catalyst technology like fuel cell technology, substrates and catalytically active coating are still required. “When fuel cells [become] competitive, hydrogen must be available as fuel itself,” said Wolfgang Maus, CEO, Emitec GmbH.
“This would allow the earlier adoption of competitive hydrogen fuelled internal combustion engines. As far as today’s emissions technologies and legislations are concerned, aftertreatment by catalytic converter will be needed.” Emitec was founded in 1986 as a joint venture between Siemens and GKN. Although the company generally has a low profile, this has not stopped it becoming one of the world’s largest catalyst manufacturers. The company is especially interested in the challenges of emissions reduction for diesel engines and sees major business potential there, both in Europe and eventually the US.
Maus also sees a highly competitive aftermarket for catalytic converters. He said: “Over the past 30 years, catalysts have been significantly optimized with regard to mechanical and chemical durability. During that time, the car’s useful life has been greatly extended. As a result, the aftermarket did not develop like the OEM business volumes. Also, because of the generally reduced retrofit lifetime requirements the market is highly competitive with a range from OE quality technology to low-tech-quality products.”
Bosal believes that the major driver of innovation is weight reduction. Bosal’s lightweight complete exhaust system is the result of a return to first design principles, and consists of fastening each exhaust system component independently to the car, with very little relative movement. Such a system no longer needs to be self-supporting, so can be made thinner and lighter, while a new mechanical device de-couples the system from the engine, reducing vibration by a factor of 10.
Last year, Bosal joined forces with Delphi to offer complete exhaust systems for the global OE market. While Delphi brings expertise in the hot end of the exhaust (from manifold to the catalyst), Bosal’s know-how lies in the cold end (from muffler to tailpipe). The non-equity based alliance, known as Bosal Delphi Complete Exhaust Systems, brings together the specific expertise, facilities and resources of each party to offer a total customer solution around the globe for any vehicle programme and all current fuel options. Prior to the deal, Bosal and Delphi operated medium-sized exhaust businesses in a sector increasingly dominated by larger companies.
Just over a year into the partnership, Karel Bos, CEO of Bosal told us: “We have landed some contracts together which is the acid test in seeing whether this works. It has opened some doors for that previously had been difficult to open. We had been knocking on Chrysler’s door in the US for a very long time without much success but with the help of Delphi, we have a contract to manufacture. We are now in the start-up phase manufacturing the exhaust system the Jeep Wrangler. We have also landed some contracts for General Motors in the US and some Renault contracts here in Europe. So the alliance is of mutual benefit.”
Bos leads the alliance along with John Fuerst, Delphi Corp’s business line executive for exhaust systems. In terms of plans to grow this alliance, Fuerst said: “We are going to grow in line with financial and technical abilities to execute flawlessly for our customers. We currently have the capacity to grow significantly. Bosal Delphi has a 5-7% share of the global exhaust market. Long term, I don’t see any reason why we can’t grow significantly from that level.”
On balance, vehicle emission control products and systems play a critical role in safely conveying noxious exhaust gases away from the passenger compartment and reducing the level of pollutants and engine exhaust noise to an acceptable level. Precise engineering of the exhaust system – from the manifold that connects an engine’s exhaust parts to an exhaust pipe, through the catalytic converter that eliminates pollutants from the exhaust, to the muffler – leads to a tuned engine sound, reduced pollutants and optimised engine performance.
“Exhaust aftertreatment continues to be a growing and challenging business,” concludes Fuerst. “It is part of the automotive industry that is really protecting the environment and improving standards of living. It’s an exciting part of the business to be in.”
Matthew Beecham
See also: Global market review of exhaust systems – forecasts to 2012