For years, wiper blade engineers have concentrated on improving two performance characteristics: operational noise and wiping quality. Matthew Beecham runs the rule over some recent innovations.
Superficially, wiper blades appear the same today as they did when the first electrically powered windscreen wiper system appeared in 1926. Yet appearances can be deceptive. Lack of space under the bonnet, cost constraints, product reliability, aero-dynamic drag, looks, pedestrian impact legislation, and technical innovations in the rest of the control system such as CAN Bus are the main forces driving innovation in wiper systems.
A Bosch executive told us: “Due to the ever present requirement for drag reduction, the windscreens of many cars are becoming ever more inclined. This presents the problem of requiring larger and larger legal swept areas; this in turn requires a longer blade and a longer arm with a more powerful motor driving it but in a smaller space and with a lower overall weight.”
As the height and width of windscreens increase, the length of a driver-side wiper becomes longer than the passenger-side blade to provide a wider view for the driver. “Blade lengths are becoming longer due to longer windshields,” said Yuuji Watanabe, general manager of the wiper and washer system engineering department at Asmo Co Ltd. “Moreover, the blade lengths differential between the driver side and passenger side is becoming larger, with the driver side getting longer and passenger-side getting shorter.”
Over the past few years, the so-called flat wiper blade market has blossomed. Flat blades have a lower profile than conventional wiper blades, making them more aesthetically pleasing as well as giving them better wind resistance, especially at high speeds. In addition, the fact that flat wiper blades don’t clog with ice and snow causing them to bend and break also leads to fewer warranty claims for manufacturers.
How well do you really know your competitors?
Access the most comprehensive Company Profiles on the market, powered by GlobalData. Save hours of research. Gain competitive edge.
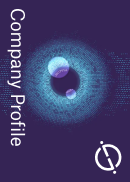
Thank you!
Your download email will arrive shortly
Not ready to buy yet? Download a free sample
We are confident about the unique quality of our Company Profiles. However, we want you to make the most beneficial decision for your business, so we offer a free sample that you can download by submitting the below form
By GlobalDataBosch launched its first flat blade, known as the Aero-Twin, in Europe on the 2000 model-year Mercedes SL Class. Since then, Bosch has been extending its range offered through the aftermarket. To make it easier for motorists to fit these flat blades onto the conventional hooked wiper arms, Bosch offers its so-called Quick-Clip Adapter, which slips onto the wiper arm.
A Bosch executive told us: “Many manufactures have opted to use Beam blades. We at Bosch call them Aerotwin blades. That’s mainly because of aesthetic-styling, pedestrian impact, aerodynamic drag issues, with definite benefits in these areas when designed into the vehicle.” Bosch points out that Alfa Romeo, Audi, BMW, Citroen, Fiat, Ford, Honda, Lamborghini, Maybach, Mercedes-Benz, Peugeot, Renault, Volvo and Volkswagen are fitted with its Aerotwin wiper blades as standard equipment.
The flat blade market is also booming in North America. “Our Beam Blade aftermarket business in the US is going fantastic,” said James Croston, marketing director for Trico Products. “We are selling millions of them all the time. We expect it to represent a continuing significant portion of our business in the future. At the OE level, you cannot quote on a new car or platform for future years without quoting a flat blade. All the OEMs are requesting it. We are definitely the market leader in the flat blade market. Trico was the first to market with an aftermarket retrofit replacement model l2 years ago.” Trico was the first to ship flat blades to North American OEMs, followed by Federal-Mogul, Bosch and Valeo.
While the average useful life of a wiper blade is six months, the average replacement interval is much longer. Research into the habits of motorists in Europe and North America and the replacement of their wiper blades has revealed a marked difference. All the major manufacturers recommend that motorists change their wiper blades every six months for safe driving vision. While Americans typically change their blades every two-and-a-half years, Europeans change their blades every one-and-a-half years although it varies from one country to the next. In Japan, however, driver habits are a little different.
“In Japan, regulated vehicle inspection is mandatory after the first three years followed by every two years. Most users replace blades at the inspection timing. We assume that users replace the rubber elements on an average of 2-3 years and the blades less frequently,” said Watanabe.
Trico Products has also launched a number of initiatives aimed at reminding motorists to replace their wiper blades more frequently. For example, Trico uses the bi-annual clock changing as a timely cue to motorists to change their blades under the mantra: ‘change you clocks, change your wiper blades.’ “In studies we have done, once people have been reminded to change their wipers then it takes three weeks for them to actually do it,” said Croston.
“We provide a lot visual reminders in-store. People can register their vehicle on our site. Twice a year we send them an email in April and October to tell them the wiper blades they need and where to buy them and install them. So I think it helps. Anything you can do to help remind people is a positive for them and us.”
Historically, replacing wiper blades has been not only difficult for the motorist to remember the procedure it has also been difficult to do. A Bosch executive told us: “As the blades are now quite often parked in a position where they are out of the air flow and possibly out of sight under the trailing edge of the bonnet it is becoming more difficult to access the arms to allow you change the blade [to raise them off the screen].
“In many new cars there is a procedure that requires you select a mode in the wiper control prior to removing the ignition key to raise the arms to a position specifically for changing the blades, notably VW’s Golf Mk5. The blades themselves however are becoming easier to change with the modern Aerotwin side lock format requiring only a 90º rotation of the blade to allow removal from the arm or with the hook type of attachment a simple squeeze rotate and push to release them and a similar operation to refit.”
Meanwhile PIAA’s top three blade products are Super Graphite, Super Silicone and Super Sporza. Its Super Graphite Wipers incorporates molybdenum graphite bonding agent that improves durability, smoothness and noise-free operation. PIAA claims this blade outperforms conventional rubber blades, while the wiper frame itself features a powder coat finish over zinc plating to prevent rust. Claimed benefits of its Super Silicone wiper blades include resistance to heat, ozone and ultra-violet for extended product life.
Its curved silicone wiper is especially engineered to fit aerodynamic windscreens found on European and Japanese vehicles. The company also offers the Super Sporza, which incorporates an aerodynamic spoiler to reduce lift at high speeds. “Because our blades are made of 100% silicone rubber, they last a lot longer,” said Chris Hutchings, sales director of PIAA UK Ltd. “The silicone makes the wipers run a lot quieter, too. So in terms of long distance driving, you notice a lot less fatigue and irritation of your wipers tramping or making those annoying squeaks. The beauty of silicone is that it tends to find its own area and doesn’t need so much pressure to make it effective on the screen.”
Turning to the rear of the vehicle, a lot of rear wiper blades are becoming integrated into the wiper arm. An executive from Bosch told us: “The trend in the system is for an integrated arm and blade normally in a plastic material. However due to the fact that only hatchbacks and estates tend to have rear systems the volumes are much lower.
If you take the fact that a car may have the same system for the front windscreen but could be produced in three different body formats, and out of these only hatch and estate will have a wiper therefore the systems tend to be low cost.” For its part, Valeo has developed a new generation of rear windscreen wiper arms. Valeo says its so-called BBI range compliments current vehicle design trends towards unique, often narrower, rear windscreens with varying curvatures and variety of vehicle body shapes.
In the wiper motor department, Valeo has also developed a dual reversing front wiper system. Two reversing motors with alternating rotation are placed on the windscreen (one motor for each wiper blade) and electronically synchronised. One motor is installed at each end of the windscreen, replacing the bulky wiper linkage of the two wiper motor system currently used.
The system has been specifically designed for use on vehicles with large windscreens requiring an opposed (instead of tandem) wiper system. The new features include ‘depressed park’, automatic wipe angle control, speed control and obstacle detection. It also offers new positions for inactive wiper blades. For example, the blades could be set to a vertical position at either end of the windscreen thereby improving the integration of the wipers in the overall look of the vehicle. Valeo’s system can be specified with either two direct drive motors, or alternatively, two motors with integrated linkages. Wiper arms are attached directly to both types of motor.
Last but not least, US-based supplier Microheat Inc claims to have a winning product with its system that heats windscreen-washer fluid and controls wipers to more effectively clean grease, dead insects and frost from the glass. The system, dubbed HotShot, was launched on the automotive market in 2002.
Gary Pilibosian, CEO, Microheat Inc, reckons that HotShot will become standard equipment on all cars soon. He said: “The market acceptance continues to increase. The product was introduced into the aftermarket in over 50 countries. Microheat is active with over 20 OEMs globally, in various stages of development. Upon successful testing of the HotShot product — all of which have been successful — the OEMs realise the ease of installation and that no components in the wiper/washer or any system are affected, the product is quickly specified for use across all of the respective OEM’s vehicle lines.”
Matthew Beecham
Research link: Global market review of automotive wiper systems – forecasts to 2012