Demands by automakers for more braking performance with minimal cost or weight penalties are pressurising manufacturers to come up with new ideas. Although advances in friction materials and caliper designs have helped improve braking performance, the main improvements in braking in recent years have come from electronic control, firstly ABS (anti-locking braking system), then ESP (electronic stability programme) and now brake-by-wire. Matthew Beecham reports.
ABS is the first slip control technology. The aim of ABS is to limit the pressure to any wheel which decelerates too rapidly, allowing maximum stopping force to be applied without lock-up. When the brakes are applied, the tyres begin to slip. ABS measures the degree of slip to determine when wheel lock will occur, reducing the hydraulic pressure to prevent it. The clear design trend is for smaller, lighter, quieter and more efficient units.
While ABS prevents the wheels from locking during braking, and traction control stops the wheels from spinning on acceleration, ESP goes one step beyond the functions of both these systems. It reduces the risk of skidding in all traffic situations.
Ever since the first ESP system appeared on a Mercedes-Benz model in 1995, braking system manufacturers have been predicting significant demand as appreciation of ESP among drivers of the middle and lower segments of the car market grows. Although ESP is already standard equipment on many luxury cars, an increasing number of mid-range and small cars are being fitted with the unit as optional fitment.
Meanwhile, all the main electronic brake system integrators are developing their own solution to electric park brake systems or EPB (also known as the electromechanical parking brake). An EPB system replaces mechanical parking brakes and the bulky mechanisms associated with them such as hand levers or foot pedals in the interior of the vehicle, and cable mechanisms and cables running through the vehicle. A car equipped with an EPB can also be a big plus for those older drivers or those with a physical disability. Manufacturers see the technology as a stepping stone to full non-hydraulic electric braking systems.
How well do you really know your competitors?
Access the most comprehensive Company Profiles on the market, powered by GlobalData. Save hours of research. Gain competitive edge.
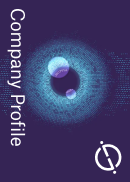
Thank you!
Your download email will arrive shortly
Not ready to buy yet? Download a free sample
We are confident about the unique quality of our Company Profiles. However, we want you to make the most beneficial decision for your business, so we offer a free sample that you can download by submitting the below form
By GlobalDataIn terms of the adoption rate of EPB systems, Continental Automotive Systems sees slow growth. James Remfrey, head of technology benchmarking and placement, advanced development department, Continental Automotive Systems, said: “Although the OEMs are heading in this direction, it is not easy to sell comfort systems. While the electric parking brake is a comfort system, there is still a safety advantage.
For instance, parking a heavy prestige vehicle on an incline will have higher operational safety utilizing an electric parking brake compared to a conventional hand-lever system. In that situation, the driver can be sure there is enough force on the brake to keep the vehicle stationary. A further advantage is packaging in the vehicle for the vehicle manufacturer. The fitment rates are increasing, especially in the compact vehicle class.”
Delphi’s electric brake – codenamed DEB 3.0 — is a halfway house system with hydraulic front brakes and electro-mechanical rear brakes. It should be ready by 2010. The company’s fully electric by-wire brake — dubbed DEB 4.0 — could be ready by 2012. “Delphi doesn’t currently offer a stand-alone electric parking brake,” said Nick Jones, chief engineer at Delphi’s Innovation Centre. “Our electric parking brakes are integral to our electric caliper. In the case of the DEB 3.0, it is buried in the rear actuator. It has the advantage of operating directly, making it very much quicker and smoother than some of the other systems that are available today. We can do a lot more with our parking brake, however, the market has not yet demanded that level of refinement. The same is true of the DEB 4.0 system. The only difference here is that we effectively have parking brake capability on all four wheels with which you can do the parking functions on a far greater slope using less force per wheel thereby extending pad life.”
For some time, Australian-based PBR International has also been developing EPB and brake-by-wire systems, pushing back the technical boundaries in the electronic braking systems arena. So what distinguishes its electric park brake technology from competing designs? “We have incorporated [our] ePark technology into two electric park brake design variations,” said Adrian Boden, group vice president, engineering, PBR International. “One is a ‘cable puller’ which operates the existing park brake mechanism (either drum-in-hat, mechanical caliper or drum brake) while replacing the hand or foot actuating mechanism. The other is integrated into a rear caliper, completely replacing the existing park brake mechanism. The principle advantages of both systems are compact size, light weight, packaging flexibility, low noise and, most importantly, the speed at which you can apply and release full parking torque. Most system requirements reflect an apply time of less than 1 second and a release of less than 0.7 seconds. PBR’s ePark systems can apply and release in less than 0.7 seconds!” Boden anticipates that the first application will be in 2008/9, most likely at the heavier end of the vehicle range.
“This reflects another of PBR’s advantages, the fact that ePark can be applied to vehicles with GVWs up to about 4,500kgs. We can therefore apply ePark, in its present forms, to almost any passenger vehicle. We can modify our design to cover heavier vehicles up to about 7,500kgs which would allow us to cover most light commercial vehicle applications. We are, in fact, currently discussing with a European LCV manufacturer for the application of ePark in 2010.”
Like steer-by-wire, brake-by-wire technology has already been offered, specifically by Mercedes in some of its top-range models and in a hybrid electro-hydraulic braking (EHB) form, with electric signaling but hydraulic brake application. The alternative, seen as a longer-term prospect, is electro-mechanical braking (EMB) in which the brake calipers are applied electrically, via a highly geared linkage, and the hydraulics are eliminated altogether (which is presented as a notable advantage).
It has long been accepted that EHB would precede EMB into production since some aspects of EMB clearly needed basic development as well as refinement – most notably robust and reliable mechanisms not only for applying braking at the caliper, but also for positively withdrawing it, with a need for high-frequency operation to meet the needs of anti-locking and traction control intervention.
What was not foreseen was that Mercedes’ experience with the first-generation EHB system would lead to its being abandoned for the new flagship S-class, launched at last year’s IAA Frankfurt motor show. It appears that EHB failed to deliver visible consumer benefits to balance its high cost and complication, especially in the face of the recently improved performance of conventional systems and add-ons. It therefore became a target for the programme of rationalisation and cost containment carried out by Mercedes within the last two years.
Although brake-by-wire systems can provide more effective and safer braking, eliminating bulky hydraulic technology, releasing space and reducing maintenance, its development path has not been all that smooth. Steve Montgomery, director, control systems software, Ricardo, told us: “In terms of system development, we are some way down the road towards full electric braking. However, early vehicles with electro-hydraulic braking have not been accepted as well as hoped. For example, the Mercedes E-class with an EHB system suffered from recalls which have dented customer confidence in the technology and have led Mercedes to phase EHB out and revert to a hydraulic braking system at least for the E-class and possibly all vehicles.”
So what can the industry has learnt from this? “It is always going to be expensive to develop a new system. I think the lesson we need to learn is to analyse the benefits of such systems in relation to the costs before embarking on development. We also need to understand risks associated with customer perception of the system and factor those into the analysis.”
Where are we now? James Remfrey, head of technology benchmarking and placement, advanced development department, Continental Automotive Systems, said: “Although we’ve seen some use of by-wire systems, we believe that the market is not yet ready for this type of technology. Generally speaking we’re seeing some vehicle manufacturers back-pedaling in this arena, preferring to source reliable, market-proven technology enhancing comfort features.”
“Most OEMs believe that the [brake-by-wire] technology will come,” said Delphi’sJones. “What is in doubt, however, is the exact timing. There are many factors encouraging it yet many discouraging it. It has been a roller coaster ride.”
In terms of brake-by-wire for commercial vehicle applications, Dr Eduard Gerum, vice president, brake systems, Knorr Bremse GmbH, told us: “Today, commercial vehicles fitted with electronically-controlled braking systems have a pneumatic back-up. So if the electronic system fails, a conventional brake control system kicks in. Eventually, we shall see the pneumatic back-up deleted from the system altogether. But we don’t see that occurring over the next ten years although there might be some niche applications that go down this route. Overall, however, I do not see a commercial driver for the by-wire system for passenger vehicles or commercial vehicles. However, I do see niche applications in both fields for by-wire systems. We also see electro-mechanical actuation soon becoming a reality for hybrid vehicles. Hybrid vehicles use a far more powerful electric and electronic infrastructure. It makes more sense for such vehicles to realize a full by-wire system and even electro-mechanical actuation in order to save the efforts for a hydraulic or a pneumatic infrastructure.”
Knorr Bremse designs and develops braking systems for trucks and semi-trailer tractor units, buses, trailers and special vehicles. Its electronic braking system range includes ABS, ASR, EBS, and ESP.
When full electro-mechanical brake technology is introduced, some say there will the issue of consumer acceptance, i.e. are we ready to brake by wire? On the other hand, some believe that the consumer will be either unaware or not interested in the technologies unless there is a warranty issue.
Ricardo’s Montgomery added: “I would draw a parallel with gasoline electronic throttle control and electronic diesel engine control. Many consumers are unaware that there is no mechanical linkage between the accelerator pedal and the throttle plate or fuel injection equipment. They don’t see the technology but the do benefit from improved driveability and functionality such as cruise control and provided it’s reliable, they are happy. Braking is perhaps a more emotive issue but the same principles apply. If the system is as reliable and as safe as the mechanical alternative, there is no reason for it not to be adopted. After all, how many passengers on a high-speed train or airliner are concerned with the technology behind them? ,,, Cost of the system is going to be an issue. A modern hydraulic system can be configured to provide the same effective functions as an EHB system so the EHB has to offer a cost benefit to the customer.”
For all the development we are seeing in the automotive industry on electric brakes, hydraulic brakes still has a long life ahead. Peter Miller, director, electrical/electronic engineering, Ricardo, told us: “Given that we can achieve a lot of functionality with a hydraulic system something else has to change to drive electric braking systems. For example, if the environmental cost of hydraulic systems renders them unacceptable then electric brakes will be in favour.”
Matthew Beecham