More power from lighter, smaller starter motors and alternators is the consistent request from automakers. Matthew Beecham reports on how rotating electric suppliers are responding.
Power to the people
The increasing use of power-hungry options in modern passenger cars is placing unprecedented demands on automotive charging systems. “Whether it’s heated seats, electrically powered brakes, air conditioning equipment, power windows or multi-media systems, the rising number of electrical options in modern passenger vehicles all places extra demands on vehicle charging systems,” said Marko Wowczyna, manager of Denso UK Aftermarket Sales. “In response, original equipment manufacturers and their automaker customers are continually seeking technological advances to boost rotating machine performance and reliability whilst minimising impact on the environment. There are also far-reaching practical considerations on design: many automakers now have exceptionally demanding engine bay packages that require ever smaller parts – yet somehow still ensuring that power output is maintained.”
Wowczyna believes that balancing engine space constraints with the continual demand for extra power makes efficiency the top priority so achieving a smaller, space-efficient size and lighter weight without power loss is always at the forefront of designers’ minds. He adds: “Overall, the common drivers for rotating machine improvement tend to be improved technical performance, alongside reduced size, weight and cost. In many cases this has resulted in a series of relatively fractional physical alterations, but each making an important small step towards optimal part design.”
The traditional Lundell-type alternator is unable to handle loads of this scale. New units emerging are capable of generating between 90% and 100% of their rated amperage at idle speeds. In terms of design, the accent is on lightweight construction with higher outputs and better reliability than ever before. Manufacturers must also address environmental, noise and high underbonnet temperature concerns.
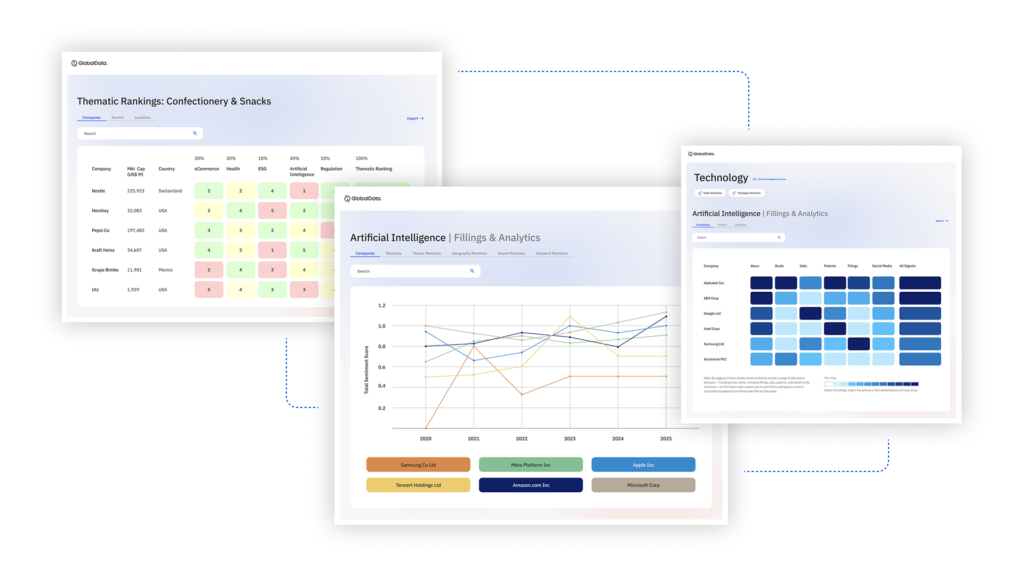
US Tariffs are shifting - will you react or anticipate?
Don’t let policy changes catch you off guard. Stay proactive with real-time data and expert analysis.
By GlobalData“In 2000, Denso introduced the world’s first SC [segment conductor] alternator using a rectangular conductor for its stator coil,” said Wowczyna. “By raising the winding density (space factor) from 45% to 70%, Denso succeeded in making the SC alternator 20% lighter whilst increasing the output to 50% higher than a conventional alternator. In 2005, Denso Corporation announced the development of a new range of OEM alternators that provide higher output currents of 165, 180, 200 and 220 amps – which, as with all Denso alternators, are the smallest and lightest in the world for their output. Denso’s 220-amp alternator is also the first air-cooled alternator to offer this kind of power level. This enables large vehicles – which traditionally required a larger, more expensive water-cooled alternator or two air-cooled alternators – to have one compact air-cooled alternator.”
It is clear that the technology and specifications for the components used in alternators as well as starter motors have become more advanced in response to the installation in vehicles of an increasing number of electrical components. As a result of this increased electrical demand, rotating electrics require more advanced technology and higher grade components. Consequently, per unit sales prices have increased.
On the aftermarket side of the business, the increasing complexity of cars and light trucks and the number of different makes and models of these vehicles have resulted in a significant increase in the number of different starter motors and alternators required to service cars and light trucks. In response, manufacturers have had to increase the number of stocked items year-on-year.
All quiet on the urban front
Another major trend has been the gradual emergence of eco-friendly vehicles, which have systems that automatically switch off vehicle engines during idling. According to various research studies, vehicles are at a standstill for one-third of the time while in urban areas. Stop-start systems could help make cities quieter, boost fuel efficiency and reduce exhaust pipe emissions.
“Integrated Starter Generators [ISGs] are now being seen on a few vehicle models,” added Wowczyna. “In contrast with traditional technology, ISGs combine two components – the alternator and the starter – into one integrated system. This creates a ‘stop-start’ effect that operates by cutting the engine when the driver comes to a complete halt. The engine is switched back on when the driver releases the brake pedal. ISG technology can offer fuel savings, reduced noise pollution and lower emissions; but is a costly technology requiring additional components and reorganised engine design. This is a field currently being explored by Denso at OE level that could ultimately filter through to aftermarket customers.”
Some recent examples of stop-start systems applied to vehicles include:
- From March 2007, Bosch has supplied stop-start systems to BMW for series production. The technology is fitted as standard on the 1 Series as part of BMW’s Efficient Dynamics collection of technologies that also includes regenerative braking.
- In August 2007, BMW’s Mini hatchback was fitted with brake energy regeneration, auto start-stop function and switch point display. Its brake energy regeneration works by using an intelligent alternator control (IAC) and an absorbent glass mat battery to recycle previously lost energy, which saves fuel. The IAC reduces drag on the engine by only engaging when required to charge the battery, whereas a traditional alternator is always taking power from the engine.
- Kia Motors, with European headquarters in Germany, is following western rivals like BMW and General Motors by adding special ‘eco’ versions to its Slovak-built Ceed model line though they won’t be available until early in 2009. The economy versions will have a new ISG (Idle Stop&Go) system, including smart battery power management. This system, similar to that recently added to BMW and Mini models, has regenerative braking, which automatically recharges the battery during deceleration, and switches the engine off when the car is stopped and the engine is at idle, cutting both fuel consumption and emissions during typical stop-start city driving.
- In late 2007, the Smart Fortwo also became available with stop-start technology. The most frugal gasoline-powered Smart currently emits an average of 112g of CO2 per kilometre. The most frugal diesel emits just 88g. PSA’s Citroën was an early pioneer of stop-start technology.
- Land Rover is to fit a stop-start system as standard to all Freelander 2 TD4 manual vehicles from early 2009. The prevention of unnecessary idling is claimed to cut CO2 emissions by over 7% from 194 g/km to 179 g/km.
All the major manufacturers of rotating electrics are involved in developing combined starter motors and alternators. For example, Valeo’s StARS starter-alternator uses the system’s capacity to stop and then restart the engine immediately, silently, and without specific action on the driver’s part. The vehicle restarts quietly and automatically as soon as a gear is engaged or, for automatic vehicles, when the foot is released from the brake. Mounted in place of a conventional alternator, the system combines the functions of an alternator and starter motor in a single unit operating at 14 volts (conventional vehicle voltage).
Valeo launched the first product in 2004 on the C3 of Citröen. Since then, the company has been working on the next steps in what it calls its ‘hybrid roadmap’. A spokesperson for the Valeo told us that the company is working to improve the stop-start function through integrating the electronics onto the machine and adding functions such as energy recovery using the machine. In pointing out the main benefits of StARS, the spokesperson added: “The machine efficiency is higher than a normal alternator so the user gains any time the engine is running. Other benefits include the ability to perform “change of mind” re-starts, that is to say as the engine is stopping…we can re-start it without any issues as there are no gears or pinions in our system. It also has a quick noiseless re-start and with the same front end architecture, the system could evolve further along the hybrid roadmap adding functions like energy recover — using ultracapacitors — without significant change.”
For its part, ZF Sachs has been developing a crankshaft-mounted starter-alternator generator. The company believes that its so-called Dynastart will revolutionise the drivetrain and power supply of cars at a stroke, combining the function of generator and starter and would be positioned between the engine and transmission. The Dynastart is more efficient than the conventional belt and alternator, delivering 10% potential fuel savings by allowing the vehicle to recover braking energy and release it as an engine booster function. During braking, the system can regenerate electrical current and feed it into the vehicle’s electrical system. When the driver puts his/her foot on the accelerator pedal, DynaStart operates as an engine booster. By means of the braking energy already stored, the crankshaft starter-generator – now working as an electric motor – helps the combustion engine to put out more torque.
“The attractiveness of the ZF Sachs’ Dynastart product may be divided into two categories,” said Martin Sattler, general manager of ZF Sachs’ electric drives business. “First, ZF Sachs has developed a unique electric machine specifically adapted to the requirements for powertrain integration. The main features are: best power and torque density; large diameter and short axial length; large air gap; and permanent magnet excitation. The operational performance of these machines is top of the class. Second, the USP we offer to our customers is the competence of powertrain integration. The benefits for our customers are excellent packaging solutions. For example, by combining the electric machine with other powertrain components such as clutches, dual mass flywheels or special hybrid clutches.”