Gasoline direct injection (GDI) continues to be a weapon in the technology armoury of automakers in their fight to reduce CO2. Manufacturers believe that homogeneous applications of GDI will be dominant over the next five years and will become more closely associated with boosting (turbo or supercharged) to achieve high levels of engine capacity downsizing. Matthew Beecham reports.
Direct injection means injecting fuel directly into the cylinder instead of premixing it with air in separate intake ports. Although this allows for controlling combustion and emissions more precisely, it also demands more advanced engine management technologies.
Gasoline injection is not a new concept. In 1952, the Gutbrod Superior 600 and the Goliath 700 GP were the first vehicles world-wide to feature a direct-injection system (manufactured by Bosch) as standard equipment. Compared to earlier models fitted with carburetors, this technology reduced fuel consumption by 20% while increasing the engine output by 20%. Bosch had borrowed this idea from the aerospace industry; the company had been developing gasoline injection pumps for aircraft since 1937. The manifold injection system gradually replaced the conventional carburetor. In 1967, the D-Jetronic system by Bosch was the first electronically controlled gasoline injection system world-wide, and was installed in the VW 1600 TL. By 1972, 18 automakers were installing this system. Four years later, Bosch introduced a gasoline injection system with oxygen control providing the basis for effective exhaust-gas control using a three-way catalytic converter.
In Japan, Mitsubishi Motors was the first to introduce GDI technology, launching it on the Galant/Legnum’s 4G93, which was later rolled out in Europe in 1998. In 1999, PSA Peugeot Citroen borrowed (under license) the GDI technology from Mitsubishi Motors and introduced a GDI engine. This was subsequently withdrawn from the market in 2001. VW and BMW subsequently introduced their own finely-tuned GDI engines, marketing their high performance.
Going forward, according to Dr Sebastian Schilling, engineering director, Europe, Gasoline EMS & Powertrain Products, Delphi, the main drivers to introduce GDI are reduction in fuel consumption and improved vehicle performance. He said: “The cooling effect caused by in-cylinder evaporation significantly reduces the knocking tendency and allows an increase in efficiency of the engine via an increased compression ratio. Especially for turbocharged engines this helps to reduce enrichment requirements significantly. The compression ratio on these new GDI engines can now be increased with less knocking tendency, which leads again to very efficient engines by using the benefits of the low-end torque like diesel engines. Running the engine in lean stratified mode like diesel engines, it is possible to reduce the pumping losses and increase the thermal efficiency, enabling very low fuel consumption. In addition, any new alternative gasoline combustion system, like controlled auto ignition or homogeneous charge compression ignition, will need a direct control of the combustion by direct injection of fuel into the combustion chamber. So GDI is clearly the preferred solution for future gasoline engines offering a broad range of different applications.”
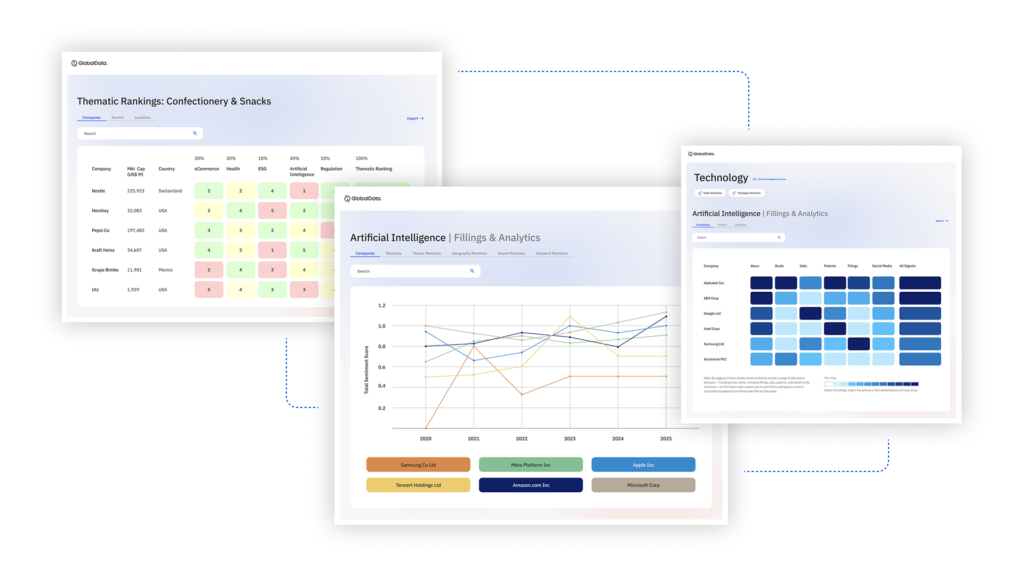
US Tariffs are shifting - will you react or anticipate?
Don’t let policy changes catch you off guard. Stay proactive with real-time data and expert analysis.
By GlobalDataDelphi used the 2007 IAA show in Frankfurt to launch its new gasoline direct injection system that is optimised for the increasing use of turbochargers and bio-fuels. At the centre of the company’s system, dubbed Multec 10, is a new multi-hole injector, designed for homogeneous lambda combustion. It is available with spray preparation options optimised for a variety of combustion chamber shapes and static flow requirements.
“In the past, stricter emission legislation always triggered the development and introduction of new technologies,” said Schilling. “The main driver for GDI is the reduction of fuel consumption and CO2 emissions, while maintaining or improving the engine performance. Especially while there are different competitors already on the market, it is an exciting challenge for Delphi. Delphi has a two-GDI injector strategy in order to fulfil the market demands for both homogeneous [with the Multec 10 injector] and as stratified engines [with the Multec 20 injector].”
Schilling believes that there are several synergies between diesel direct injection systems and gasoline direct injection systems. He said: “The GDI technology for gasoline engines is using today injection pressures up to 200 bar, while in the meantime the diesel injection systems, depending on application, are around 2,000 bar. Independent of the differences in working pressure range, there are synergies in the area of production processes, especially for injector and pump manufacturing. In addition, the sensing and the control software can offer some additional synergies following a consequent systems approach.”
Bosch designs and develops injection systems which allow vehicles to run on diesel, gasoline, gasoline and natural gas or gasoline and ethanol, either alternatively or as a mixture. This year, Bosch will deliver about 900,000 gasoline direct injection systems, and estimates for 2010 exceed 2 million. The company believes that its new generation of the GDI systems makes combustion more efficient and increases overall engine efficiency. Dr Steffen Berns, executive vice president Engineering Gasoline Systems, Bosch, told us: “With DIG [direct injection gasoline] it is possible to reduce fuel consumption and CO2 [carbon dioxide] emission by about 15% and to meet current and future emission regulations. That’s the reason why car manufacturers are more and more interested in using DIG. For Bosch this opens up significant market potential.”
Bosch claims that its current, second generation gasoline direct injection system, known as DI-Motronic, contributes to improved mixture preparation and further reduces emissions of carbon dioxide, hydrocarbons and nitrous oxides. The main elements of the DI-Motronic system include the HDP5 high-pressure pump, which is characterized by compact dimensions and low weight. The magnetically controlled high pressure injection HDEV5 valve permits a spraying pattern with up to seven individual jets depending on the application. “The second-generation DI-Motronic contributes to improved mixture preparation and provides for considerably reduced emissions of CO2, hydrocarbons and NOx [nitrous oxides],” added Berns. “Using optimised cold-starting combustion processes which provide for faster heat-up of the catalytic converter, emission values are even below the strictest SULEV (super ultra low emission vehicle) limits in the U.S. And the DI-Motronic even has the potential to fulfil future emission regulations. At the same time our second generation of gasoline direct injection system provides the basis for a whole series of new approaches to reduce consumption and CO2: the spray-guided combustion process, control of intake and exhaust valves, and above all turbocharging, which allows engines to be smaller. This ‘downsizing’ has now been adapted in several series-manufactured engines – and further projects are set to follow.”
Meanwhile, Denso’s engineers are developing high-pressure fuel injection (2,000 bar) technology, precision fuel injection technology and sensors for auxiliary control. Their aim is to reduce exhaust gas emissions and create systems that contain total costs by simplifying after-treatment processes. The company is developing various after-treatment systems for exhaust gas, including cordierite-based diesel particulate filters, lean NOx traps, and urea selective catalytic reduction systems. Denso used the 2007 IAA show in Frankfurt to reveal its latest generation common rail system. In a speech to journalists, Koichi Fukaya, president and CEO of Denso Corp, said: “Our 200 Mega Pascal diesel common rail system will be introduced to the market next year. [It] achieves the world’s highest fuel injection pressure – up to nine injections during each combustion cycle. In addition, the injector for the new system features a unique mechanism that reduces the amount of leakage fuel returning to the tank. In turn, this reduces the amount of fuel supplied from the pump to the injector, decreasing the pump’s workload.”
Denso Corp also believes that there is a large amount of commonalities and synergy effect between GDI and diesel. “To realise low-costs, reduced development time and high quality, we partly commonise production processes and structures of GDI and diesel components, such as injectors, pumps and sensors, and their control software,” said Osamu Fukasawa, senior manager, Powertrain Management Systems Engineering department, Denso Corp. “But the balance between flexibility and commonality is important.” In responding to stricter emission regulations, Denso has continued to develop and provide high quality performance products. Fukasaw added: “The key point is to realise low cost after treatment systems for NOx and PM reduction. We believe that this will lead to business expansion.”
Despite the initial forecasts for a booming GDI market, the reality is that the adoption of the technology has been slower. Going forward, however, just-auto expects to see an increasing adoption of GDI for gasoline engines over the next few years. However, if the fuel economy benefits can be truly demonstrated and gasoline direct injection can be proven to be a better solution over competing technologies, the potential market could be much higher. In North America, however, the relatively low fuel price has resulted in little incentive to introduce fuel saving technologies, whether GDI or diesel. Emission legislation, however, could change that and lead to the future expansion of GDI technology.
See also: Global market review of fuel injection systems – forecasts to 2013 (download)