For many years, power steering technology was focused on hydraulic systems but demand is now favouring electric power steering (EPS) mainly due to fuel consumption and logistical benefits, writes Matthew Beecham.
There are basically four types of EPS:
- Column-assist type?the power assist unit, controller and torque sensor are attached to the steering column. It can be applied to fixed steering columns, tilt-type steering columns and other types. It is suitable for small cars.
- Pinion-assist type—the power assist unit is attached to the steering gear’s pinion shaft. The power assist unit is outside the vehicle’s passenger compartment, allowing assist torque to be significantly increased without causing more interior noise. It is also suitable for small cars.
- Rack-assist type—the power assist unit is attached to the steering gear rack. Its high reduction gear ratio enables very low inertia. It can be applied to mid- and full-sized vehicles.
- Direct-drive type—the steering gear rack and power assist unit form a single unit, enabling low friction and inertia.
An EPS system can effectively change the assist force for steering operation depending on information such as steering angle, steering angle velocity, speed and acceleration of the vehicle and each wheel, and yaw rate. The EPS system can therefore not only reduce the steering load but also optimise the assist force depending on the driving situation.
“There are basically four drivers [to implement EPS]: driving dynamics; reduced noise levels; energy efficiency; and active safety, comfort and convenience features,” says Wolfgang Bongarth, supervisor, steering car technology & CI steering, Ford-Werke GmbH.
“The customer still expects excellent agility and driving dynamics. By using latest generation electrically power assisted steering systems, we can now achieve the driving dynamics the customer wants. We can also achieve the noise level the customer expects of the vehicle. As far as energy efficiency is concerned, the focus these days is on CO2 reduction rather than only fuel economy. In terms of active safety, the steering system can actively interact with the driver’s input.
“The steering system can also offer some additional comfort and convenience features. Another important consideration is vehicle affordability and cost of ownership. There are, of course, many other drivers we consider to be an advantage from an OEM perspective. These include things like the reduction in the manufacturing assembly time versus hydraulic systems. By installing electrically assisted steering systems over a hydraulic system, the OEM can effectively reduce the number of components in the engine and passenger compartment. For instance, a hydraulic system takes several minutes longer to install than a EPS system due to the fact that installing a hydraulic system involves lines, couplings, attachment of the hoses in the engine compartments, filling etc.”
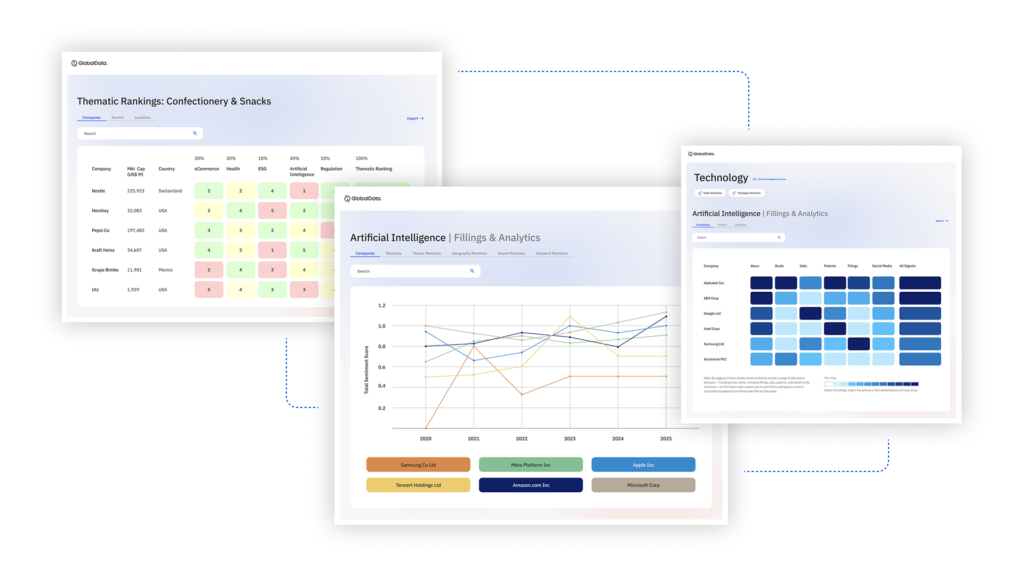
US Tariffs are shifting - will you react or anticipate?
Don’t let policy changes catch you off guard. Stay proactive with real-time data and expert analysis.
By GlobalDataThere is no doubt, therefore, that EPS systems are headed for the mass-market worldwide, helped by their potential to save manufacturers money, reduce customers’ fuel bills and save designers valuable space.
In the meantime, electro-hydraulic power steering (EHPS) appears to be holding ground despite the early assumptions that this was a ‘transition technology’ before it went to full electric. Back in the late 1990s when the technology was introduced, many people closely involved in the steering sector viewed as a stop-gap technology until EPS could get fully established. Yet since then, EPHS has found its place. Its packaging benefits and adaptability for use in hybrid vehicles has given it an extended life.
Charlie Cregeur, director of product planning for steering, TRW Inc, told us: “We are advocating EPHS as a great way to take a vehicle already fitted with hydraulic steering with minimal intrusion and convert that to a hybrid capable product. We have actually had good interest from all regions about the product. We also have hybrid programmes going in Europe and North America.” TRW Automotive says its EPS belt drive system will launch on North American vehicle models in 2008 and European models in 2009. TRW points out that the same system can be used on hybrid electric vehicles without modification, if the rack load of the vehicle is within the given power range of the EPS belt drive system. This enables vehicle manufacturers to put the same type of steering system on a conventional and HEV version of the same platform.
Bongarth added: “Clearly EHPS systems are a bridging technology, the question is only how long do you define that transition period? Will that period reach into 2015 or 2020 or will it end in two years time? I think that it will be somewhere in the middle. It pretty much depends on the platform that you have been introducing that technology. So there might be good reasons to keep electro-hydraulics or to even swap to electro-hydraulics still as an intermediate step towards EPS.”
At one time it was felt that the limitations of 14/12V electrical systems would mean that EPS would be applicable only to smaller cars and that wider application would have to await the adoption of 42/36V systems. However, the general abandonment of the 42V concept has led to the development of more compact and powerful 14/12V EPAS and systems are certainly now suitable for D-segment cars, such as the BMW 5 Series.
Dr Markus Lemmen, development engineer, vehicle dynamics and x-carline steering, Ford-Werke GmbH, agrees with the observation that this observation that we are starting to see these EPS systems appear in more powerful and heavier cars but argues that it is not only a question regarding weight but also a question on how agile the absolute response is supposed to be. He told us: “So if you have a heavy front axle weight then you can still use the EPAS system if you are willing to buy into an indirect steering ratio. So it is always a question about power demand rather than just segments or front axle weight. You have to look into great detail to see whether or not the application is feasible for EPAS.”
While estimates of future penetration levels of EPS by region vary, there is complete agreement that the trend is upwards. The only disagreements concern the slope of the trend and at what level it might plateau. “Currently we see a tiered market trend toward EPS systems, caused by the overall demand for fuel efficient cars,” said Eberhard Kübler, chief engineer, car steering Systems, ZF Lenksysteme GmbH.
“Although we see nearly all OEMs trending toward EPS for their next generation cars, there is a broad variety in terms of how those OEMs want to get there. I think that those OEMs who already have experience of EPS will apply it to their next generation cars more or less for all of their platforms. On the other hand, some OEMs who have used hydraulic systems to date are under constant pressure from the market to reduce fuel consumption. That in turn is prompting them to look for ways in which they can introduce EPS technology into their cars. So that is the ‘bandwidth’ in terms of the future fitment of EPS.”
Although the electrically-assisted steering market is relatively small in North America, manufacturers say this market will grow, albeit gradually. “We see the EPS growing in the US, but perhaps not as fast as we have seen in Europe,” added Kübler. “We expect to see an intermediate period where American carmakers offer HPS systems but they will perhaps then try to reduce the fuel consumption by some additional measures. For example, energy-saving pumps, especially our “Varioserv”, enable those carmakers stay with hydraulic steering systems for perhaps one more generation.”
Going forward, Cregeur expects to see a mix of steering technologies out there, including hydraulics, EPHS and EPS. He said: “Although the North American market has lagged Europe and Asia markets on the emissions and fuel economy improvements at a federal level, as fuel prices continue to increase and emission issues across the globe continue to get more focused, the North American market will start to respond and come into alignment.”
While there is increasing demand for EPS in developed nations, the appetite from some emerging markets is less clear, says Kübler. “We see different tendencies with the carmakers. There is a broad range of steering systems for those markets, ranging from mechanical steering through to hydraulic power assisted steering systems and EPS. For example, we are seeing applications of low-cost column EPS systems in emerging markets, equivalent to the first generation of column EPS systems introduced in the Japanese market.”
Although we have seen EPS systems become popular among automakers, what’s round the corner? The attraction of steer-by-wire (SBW) is the ability to modulate the steering signal. At its most basic, this would allow the steering characteristic to be tuned to combine good straight stability with enhanced cornering response—something which is only achieved mechanically at significant cost and complication. Yet SBW remains a vision that engineers steer towards but never materializes in the mass vehicle market.
“SBW is still an advanced technology with limited application potential,” added Bongarth. “You can prove and realise all sorts of advanced features with it but to bring it into the vehicle will cost the OEM an immense amount of money. The question here is if the [end] customer is willing to pay for it because he could get nearly the same functionality with an AFS [active front steering] and EPAS combined.”
In terms of tomorrow’s steering systems, TRW believes that there will be an even stronger link with advanced driver assistance systems. “The integration of braking technologies and steering and other sensors around the vehicle to improve the safety and driveability is certainly an important topic,” concluded Cregeur. “We are uniquely positioned because we offer both active and passive technologies. For example, we have the ability to link the brakes, steering and active control retractor seatbelt technology into one system.”
Matthew Beecham
See also: Global market review of automotive steering systems – forecasts to 2013