The manufacture of automotive components on demand directly from digital data promises to be the manufacturing solution of the future, at least for those companies that can afford it. Not surprisingly, Formula 1 has been one of the first to embrace the new processing systems. AWKnowledge’s Automotive Components Analyst newsletter reports.
The manufacture of automotive components on demand directly from digital data promises to be the manufacturing solution of the future, at least for those companies that can afford it. Not surprisingly, Formula 1 has been one of the first to embrace the new processing systems. On 24 February, the Mild Seven Renault F1 Team and 3D Systems formally opened an Advanced Digital Manufacturing (ADM) Centre at the team’s Enstone facility in motorsport’s Oxfordshire valley. The ADM Centre concentrates on the design of components for the Renault F1 Team car.
3D technology is nothing new to Renault, which has been using the systems for several years. With the addition of the new facility, Renault now boasts four stereolithography apparatus (SLA) 7000 Systems, an OptoForm paste system and a ThermoJet printer. These tools allow rapid production of the enormous number of components required for aerodynamic testing. Tests conducted in the facility’s wind tunnel evaluate the components’ aerodynamics. Design adjustments are then made and a new component is tested. Up to 50 versions of every single component on the car may be needed before optimal design is achieved.
Digital manufacturing allows Renault to test many more components for the same budget. Each test car (a 50 percent scale model) contains thousands of components. Manufacturing such an enormous number of components in the traditional method would consume vast amounts of money and take an excessive amount of time. In Formula 1, this time is simply not available, as race cars regularly go from an idea on paper to a physical vehicle on the track within a number of months.
Not only can components be built a hundred times faster, but they are also much more accurate. In fact, the team’s new race car is expected to cut 1.5 seconds off every lap thanks to a new aerodynamic package developed with ADM technology. “What’s that worth in motor racing terms? You can’t put a price on it,” said Mike Gascoyne, technical director of Renault F1 Team UK.
How well do you really know your competitors?
Access the most comprehensive Company Profiles on the market, powered by GlobalData. Save hours of research. Gain competitive edge.
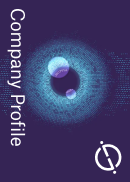
Thank you!
Your download email will arrive shortly
Not ready to buy yet? Download a free sample
We are confident about the unique quality of our Company Profiles. However, we want you to make the most beneficial decision for your business, so we offer a free sample that you can download by submitting the below form
By GlobalData3D Technology
The SLA 7000 systems comprise an ultraviolet laser, optical scanning system, a vat of photosensitive epoxy plastic material and an elevator platform. It also contains software that controls the exposure and position of the laser and elevator. To construct a part, the laser traces a cross section of a component. This cross section is then lowered into the liquid bath of photopolymer and recoated. The laser then traces the next slice on top of the previous one, turning a thin layer of the liquid material to solid. Layer by layer, the material is solidified in the defined pattern and in a matter of hours, a completely functional component has been formed.
3D also offers a selective laser sintering (SLS) system, which Renault plans to add to its ADM facility. At the moment, the company outsources production of components produced on the SLS system. The si2 SLS creates components directly from a CAD file using a CO2 laser to fuse together layers of plastic or metal powders. Again, durable, fully functioning components are produced in a matter of hours.
Quite a high percentage of components can be manufactured with this technology, though Gascoyne could not give a specific figure. To some extent, the size of the SLS will dictate the size of the component, but a component can be manufactured piecemeal and the pieces later bonded together.
Gascoyne did not reveal the total cost of Renault’s investment in 3D technology, but 3D president Grant Flaharty gave a rough estimate of prices. According to Flaharty, a printer ranges from about US$40,000 to US$90,000 and a steriolithoscope machine starts out at about US$200,000 and can exceed US$1m. As Gascoyne repeatedly mentioned, “Money is no object – performance is the object.”
Not all manufacturers can claim that money is no object, however. Those companies who do not have their own 3D imaging facilities can easily outsource the work to companies like QuinetiQ. QuinetiQ recently extended its Stereolithography Rapid Prototying facility to provide both design and modelling services to manufacturers. QuinetiQ uses an SLA-5000 to produce plastic components in the same concept used by the SLA-7000. Ford, Audi and Bentley are just some of the manufacturers who have worked with the company in this area.
To learn more about this and other world vehicle markets, and download your free sample of AWKnowledge’s “Automotive Components Analyst” newsletter, please click here.