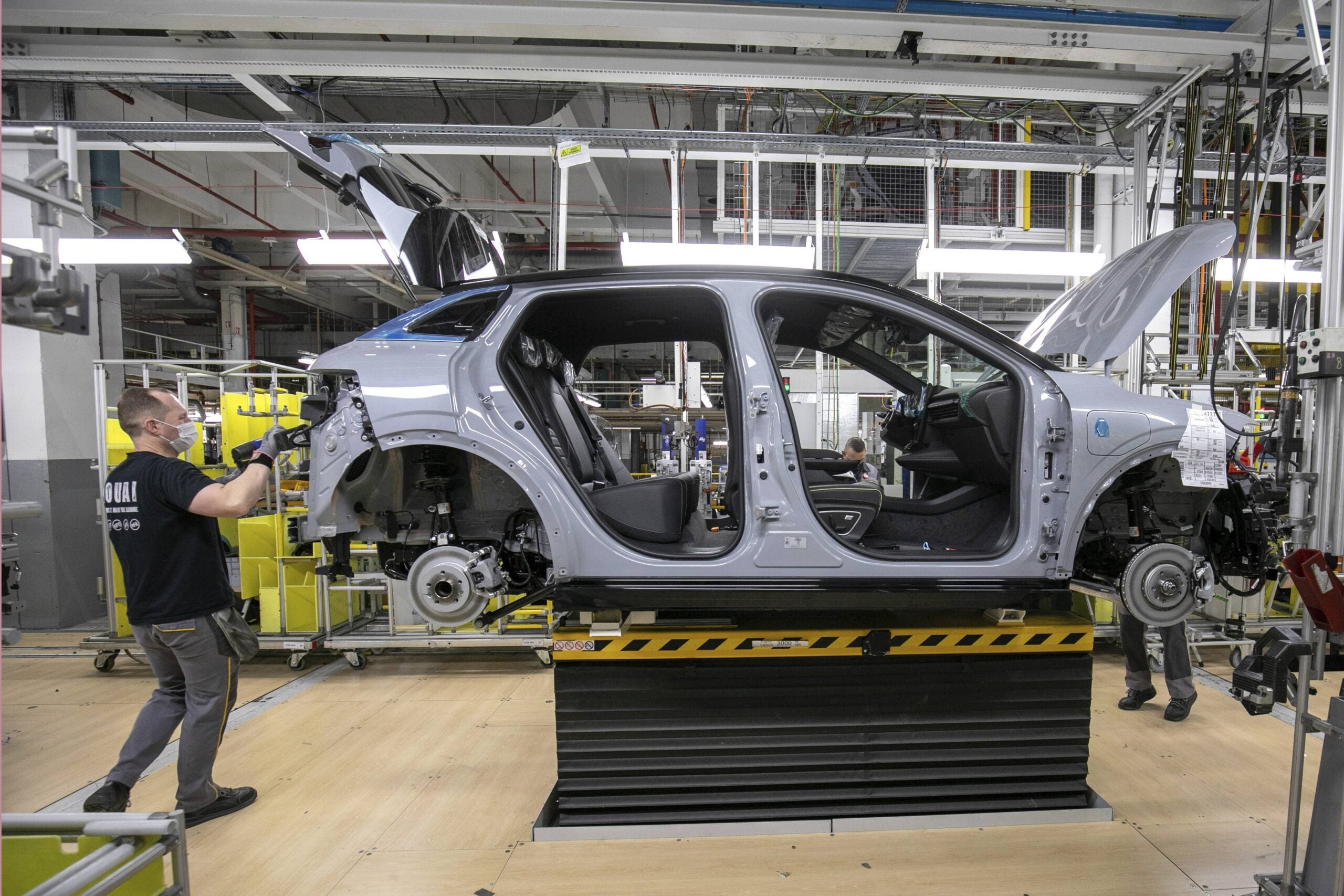
Seven weeks of construction, 38,000 square metres of emptied space, 100 heavy machinery units (robots and assistance equipment), and 400 redeployed workstations were required, giving some insight into the extent of the challenge of installing the new Alliance Standard Line assembly line at Douai, which, since 1975, has made 10m Renault model line staples such as the 5, 14, 19, 21, Megane and Scenic, to produce the new EV.
“We are extremely proud to have been part of this adventure, because a project of such magnitude, in France no less, is a once in a lifetime opportunity!”
Nicolas (capacity mounting project manager) and Vincent (Megane EV electric assembly project manager)
“In a factory, more than anywhere else, time is precious. We couldn’t tolerate a single delay,” said Nicolas.
The tone was set – any day lost to downtime was to be avoided at all costs.
“One exception: any necessary repairs and improvements are done at the weekend, or at night… or in August during the summer holidays. If each section of the old assembly line were put end to end, the assembly line, with all 400 workstations, would be nearly 1,700 metres long’. The line’s gigantic size can be explained by its age: the last time it was fully modernised was back in 1986,” he recalled.
“It’s not as if the assembly division at Douai was old and dated. Prior to the recent work, the factory’s production capacity was very good. The line had to be replaced in order to produce both ICE and EV models. We kill two birds with one stone by bringing the whole line up to the highest level of European standards,” said Vincent.
How well do you really know your competitors?
Access the most comprehensive Company Profiles on the market, powered by GlobalData. Save hours of research. Gain competitive edge.
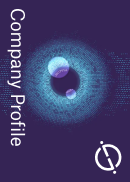
Thank you!
Your download email will arrive shortly
Not ready to buy yet? Download a free sample
We are confident about the unique quality of our Company Profiles. However, we want you to make the most beneficial decision for your business, so we offer a free sample that you can download by submitting the below form
By GlobalDataIf each section were put end to end, the assembly line, with 400 workstations, would be nearly 1,700 metres long – or over a kilometre.
On paper, the objective was clear: create a brand new assembly line using technology from within the Renault Nissan Mitsubishi Alliance while keeping anything that could be kept. That meant completely emptying out the assembly building and removing the first floor and then replacing 100 pieces of heavy machinery (robots and assistance equipment) plus 400 workstations and associated equipment.
“It took a year to get the job site ready. After close analysis, we determined that 20% of the old production line could be kept,” recalled Nicolas.
The Douai factory sheet metal and assembly lines are now Alliance Standard Line-compliant – the most advanced production standard within the alliance. The highly versatile factory can now produce both ICE and EV vehicles on the same line, on three different platforms, with highest possible safety and output standards.
Improved workstation ergonomics and safety
Production capacity at Douai factory was not the reason behind the recent upgrade as output of 60 vehicles per hour prior to the revamp remained unchanged. The primary rationale behind upgrading the plant was to improve efficiency of the production process for enhanced ergonomics of workstations and improved operator safety.
“The best example is how body heights vary according to the type of vehicle. On sections where the interior and exterior panels are mounted, the vehicle is laid on skillets that act as a base. It can be raised or lowered between 20cm and 1.3m high to make it easier for operators to work. A lot has been done to improve conditions for those working on the undercarriages,” Vincent said.
This massive upgrade was a unique opportunity for Renault Group ergonomic specialists to thoroughly improve or optimise workstations so assembly work could be carried out in an easier, more fluid manner.
Said Nicolas: “Tool trolleys have been integrated into the line and follow it much like the parts that are now delivered by auto guided vehicles (AGVs). Operators don’t have to move about as much as they have everything at their fingertips. Less travel and less handling mean less fatigue and more productivity. Without the risk of wrong or damaged parts, quality is improved.
The icing on the cake is that the recent upgrade has also brought energy savings with the installation of LED lights.
The use of comprehensive kits for each vehicle means it is now faster and more efficient to get operators the parts they need.
Only seven weeks downtime
Work took just under two months to complete, from 25 November, 2020, to 18 January, 2021, when production restarted. 1,200 people worked on the upgrade, even right up to the Christmas season.
“We kept everyone motivated by making sure the ambience was friendly. On Christmas Eve, we set up a three metre Christmas tree with the ‘must have’ Christmas lights inside the building,” said Nicolas.
Actual works for the upgrade lasted only seven weeks.
The new assembly line is more compact than the previous one and 20,000m2 of floor space freed up by the works have been reused for a battery assembly shop.
External and internal logistics have also been completely redesigned so the truck depot and parts logistics department are now adjacent to the assembly line. The (now common) use of comprehensive kits for each vehicle means it is now faster and more efficient to get operators the parts the need.
Emotions and nerves were running high when the new assembly line was reopened for the first time since the upgrade began.
“We celebrated the successful re-start by all having dinner together on site. We ordered in 200 pizzas,” Vincent recalled.
However, the line is still being “broken in” and only recently hit the threshold of 60 vehicles/hour.
Since reopening, 3,000 Megane E-Tech Electrics have been built.
“Quality is there, that’s our greatest reward,” Vincent added.