Today’s enterprise is more frequently seen
as a virtual ensemble of different companies. These legal entities can be connected in a
business network and/or are sometimes spread all over the world. This globalization is an
important trend and will continue to become a significant factor for a competitive
Automotive Industry. This Industry supports a market where every customer wants a
customized product and this needs to be reflected in the vehicles offered and the
processes that must produce and deliver them.
Product centrality
Inside each enterprise and along its value chain, the product forms the focus of
every process. It starts from its conception and definition, and continues until its
replacement and/or scrapping by the final customer. It is clear that every business
process: internal production or outsourced fabrication; technical assistance and sales
support; training; installing and maintenance; and traceability for total quality domain,
centers directly on the product that the enterprise supplies.
Fig.1 PDM system
within a manufacturing enterprise
Product definition
Within information systems, product must be defined through manageable data. It
must be built up in a unitary model, and be able to answer to the global needs of
suppliers, customers and the whole structure inside the virtual enterprise as described in
the introduction. In addition, this modeling must be compatible with international
standards like the STandard for the Exchange of Product data model (STEP).
The automotive Original Equipment
Manufacturers (OEMs) and suppliers are themselves changing from conventional functional
structures into process-oriented organizations. They must be capable of reacting to market
changes promptly and adapting to technical innovation. Also, new professional profiles
(such as process owners; a type of product manager with much wider responsibilities) are
sprouting from inside companies. Consequently, automotive OEM’s and suppliers who possess
an information system can steer any engineering review of its business processes.
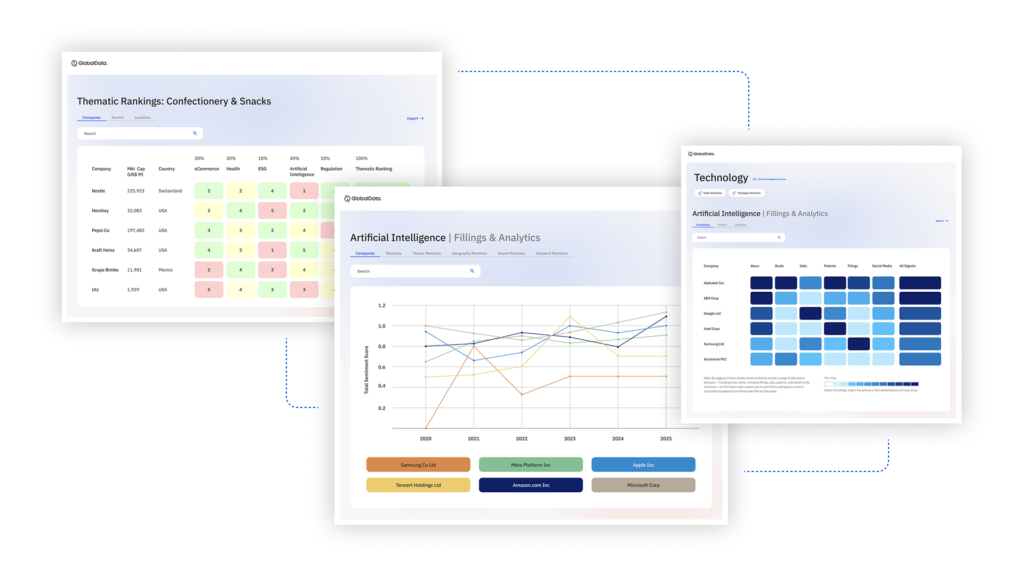
US Tariffs are shifting - will you react or anticipate?
Don’t let policy changes catch you off guard. Stay proactive with real-time data and expert analysis.
By GlobalDataIntegration management
Product Data Management (PDM) is Information Technology’s (IT’s) answer to these
basic needs. PDM acts as a bridge between the Enterprise Resource Planning (ERP) system
and the Computer Aided Design (CAD) system, enriched by its satellite software CAx. These
two different worlds are renowned for not having effective mutual automatic data
interchange. ERP tends to ignore the design and development of the product. However, the
real life cycle of the product begins from its conception, not from its delivery to the
market. OEMs and their suppliers, who want to reduce the product’s time-to-market, must
pass through a PDM approach. Today, the problem is not the maintenance of the product
production and delivery process, but the systematic updating of the product design.
Manufacturers must be able to customize products to customer needs with the help of a
configuration management tool. This is extremely difficult to achieve if the ERP and CAD
worlds do not communicate with each other through PDM interfaces or integration.
Product and process
In the virtual enterprise which connects the OEM and its Tier One suppliers,
common design activities (called ‘co-design’) will become an imperative issue for the
survival of the business relationship. The logistics integration, which has revolutionized
product distribution worldwide (and not only in the automotive sector) might be completed
by a deeper involvement in co-design. It is important to emphasize that the product (in
PDM language) is produced as a result of activities. This is not necessarily the sole
concern of a manufacturer. Even though the manufacturing industry takes a strong lead in
ERP and PDM, product could be a plant, a service network, a process or a project design
for a product, machine, or plant. PDM is therefore a key factor in, and the main guideline
to, Business Process Re-engineering (BPR).
Co-design integration
For an OEM in the Automotive Industry, the product is the vehicle, a complex
system of integrated sub-systems; assembled modules, sub-modules and components; or all of
them. In order to reduce its time-to-market and cut costs, OEMs are now transferring most
of their activities to the Tier One industries along the supply chain. The problem of
integration in co-design between OEM and Tier One is complex. It could be simplified by
the common use of the same software tools, by standard solutions for data management and
by proper communication. This would allow consistency through a process that starts with
sketches, notes and drafts, and ends with three-dimensional models and sophisticated
analysis tools.
Basic PDM concepts and functions
Information repository
All data and information from any source and in whatever form is collected and
organized in a repository, which is the core of a PDM system. This information may
include:
- drafts and technical notes
- product configuration and properties
- part description and specifications
- CAD drawings and models
- functional schemes
- scanned pictures or images
- vocal comments
- any document or message
- catalogue, references or abstracts
Vaulting
Data taken from files or databases of ERP and company business history will be
stored. The setting of the overall information into a secure repository is defined as
vaulting. Vaulting may be considered as a unique and protected store for basic data as
well as a focused and centralized archive to be accessed by authorized users. To qualify
each piece of information is complex, and the capability of usefully retrieving this
information is as important as the information involved and its use.
Workflow management
All the activities and procedures of design and engineering must be reviewed in terms
of new processes in order to build up a highly productive structure. Workflow management
is the consolidated technique that assists business process reengineering through the
restructuring of pre-existing processes. This is another qualifying aspect of PDM that
enables the visibility of every product along its complete life cycle. This is done for
every product and even retrospectively through its recorded history. In this sense, PDM
explores the whole company through space and time with a multidimensional overview.
Concurrent Engineering
Configuration management
PDM accompanies the development of parallel product design up to its final structure.
It can manage different versions of the same product and generate the product Bill of
Material (BOM) automatically from the design BOM. This function directly connects CAD and
ERP. PDM can manage more BOMs (logistic, manufacturing, quality, servicing and so on), and
alternative routings for the different factories that may be responsible for the product.
Configuration management is, therefore, another characteristic PDM issue. Various groups
or parts within the same product can be designed and engineered simultaneously in a
concurrent way.
Competitive analysis
The configuration backbone might be applied to the products under development by the
company. It also may be used for competitor’s products, whose structure and information
might be collected from different sources until it creates several complete models. The
comparison with competitive products could be continually managed in a valuable way.
Different products could be predesigned together, before their customizing for specific
markets. This would enable company growth without much additional cost. The acquisition
via scanner or CAD drafts, drawings and solid models, would allow the designer to view the
product under development. He/she could even ‘mark-up’ on the work station screen
suggestions for improvements or modifications without any further intervention. ‘Scanning
and imaging’, ‘viewing and mark-up’ are the technical definitions of these PDM
capabilities generally used by software.
Managing the product
A concise market overview
The early 1990s might be considered as the birth years of reliable PDM solutions,
generally offered by such companies as Sherpa, Metaphase and Matrix. Even the main
hardware houses developed their own PDM product: Product Manager by IBM and Work Manager
by Hewlett Packard are examples. In order to complete their product lines, many CAD
software companies created their own products: Optegra from Computervision and Workcenter
from Autodesk (the AutoCAD supplier). PDM was then enriched by transnational software
producers such as French Matra, which developed Design Manager inside its CAD family, and
Euclid Quantum, or Italian CADLab with Team Manager.
Design and engineering structure
The growth of PDM products has been accompanied by the evolution of the
organizational model for managing them. Workstation, workgroup and company repository
comprise the three levels of the comprehensive reference structure needed to manage medium
range projects. The capability of operating together on the same project is defined as
electronic collaboration. This could be active inside a company or enlarged to a virtual
enterprise encouraging co-design as an everyday practice. As with workflow management,
groupware has become an outstanding technology for electronic collaboration and Lotus
Notes grows as a widespread product for interfacing CAD and ERP. Project management
discipline and tools have enhanced and qualified the contribution that leaders and process
owners can bring to the job. It is true to say that PDM has become a powerful tool for
concurrent engineering in order to shorten product time to market and to deliver better,
cheaper and more versatile product designs.
Fig.2 The corporate Product systems classification by Ford |
|
Body system | Steering system |
Frame and mounting system | Climate control system |
Engine system | Information, gauge, and warning group |
Suspension system | |
Driveline system | Electrical power supply system |
Brake system | Vacuum distribution system |
Transmission system | Lighting system |
Clutch system | Electrical distribution and electronic control system |
Exhaust system | |
Fuel system | Electronic features group |
The Ford example
A Tier One supplier must find ways of
cooperating in design with OEMs who may have different CAD products or PDM
software.’Co-design’ is a powerful means of integration, real teleworking within the same
network in real time. This can be achieved despite the heavy traffic induced by graphic
data. We foresee the necessity of multi-CAD solutions in order to interact with many
customers.
For example
Ford has launched its C3P program, which stands for CAD + CAM + CAE+ PIM, describing
Computer Aided Design, Manufacturing and Engineering plus Product Information Management,
or PDM. Ford will manage a complete CAD model for every vehicle project. The full car
model should necessarily be exploded into systems and subsystems, modules, sub-modules,
and components. The complete vehicle system has been structured in Figure 2, which shows
the first level of explosion.
The answer from the
‘Super-Tier’
Some questions must be addressed: How can a
supplier cooperate in co-design without having the same CAD model as its OEM? How can the
supplier manage operations properly inside its company without the same software?
Ford has eliminated all CAD software except
for its favorite SDRC I-DEAS, which (through a technology partnership) has become C3P
I-DEAS. Outstanding CAD software, like Computervision CADDS and Pro Engineer, (both by
Parametric Technology,) or simple and widespread ones like AutoCAD have been banished by
all its technical offices (and will also be dropped by those who want to be kept as
suppliers).
It is difficult to foresee a different
solution than that of different CAD software installed on workstations to help different
customers. If this happens (and Ford has established a deadline by 2000), ERP integration
in the automotive supply chain must rely on the connection with PDM versatile solutions.
In the near future, it might be a question of survival.
Conclusion
The challenge for OEM’s, IT solution
providers and suppliers in the future is to seamlessly integrate the PDM processes with
the same success as EDI for the transfer of operational data. The task is demanding, but
the prize is survival.
ERP – CAD integration ERP
alone is a very complex project. BPR has
not yet reached satisfactory results at company-wide levels. Full ERP-CAD integration in a
BPR approach might seem hard to practice by the virtual enterprise. Arguably, it is more
difficult to reengineer a process in an enterprise that has been split into two companies:
the CAD side and the ERP side. It is also more difficult to reengineer something, which
has not been previously engineered, from either side. From this view point, those ERP
systems which possess consolidated options for product structure, (as those derived from
experience and practices in the Automotive Industry), are ready for integration. ERP
systems must have:
- comprehensive product definition management
functionality - integration with functionality that supports
quotations, estimating and prototype phases of new products
These are notable prerequisites inside ERP
systems for proper CAD integration, moving concurrently from both CAD and ERP sides. A
relevant role is played by the proper standard adoption. Among these on a worldwide basis
is the outstanding role played by STEP. It is approved by ISO as 10303, facilitating the
convergence of software products in the CAD and PDM areas. Common database object oriented
and network integration are the guidelines to pursue for the near future.
Fig.3 Network integration
Today, integration might be achieved, from
every proper CAD product towards ERP systems, eventually passing through consolidating
products like Lotus Notes, through a parallel client-server multiple approach (see Figure
3). The CAD or PDM side software system is tied with a server, which connects to a client
that is networked with an ERP system, and vice versa. A redundant connection might be
established between two clients that are mutually connected, and then connected with their
own area server.
The reaction time of the traditional Tier
One and Tier Two suppliers to the OEM new co-design era, opened by Ford in the most
competitive market, is difficult to gauge. It is, however, a consistent advantage to
foresee the framework, to plan the path and develop the information and communication
tools that will be used, to face and embrace the future.