Although the idea of replacing glass with lighter weight plastic sounds like an obvious innovation, it is not new. For over thirty years, auto glass experts have explored the potential for polycarbonate as a replacement to glass. Matthew Beecham reports.
The application polycarbonate glazing to vehicles differs from one region to the next. In the US, current National Highway Traffic Safety Administration standards rule out polycarbonate for windscreens and movable side windows. That leaves just the fixed vent window and rear window. This regulation is partly based on concerns about the durability polycarbonate, specifically its resistance to abrasion and UV light. In Europe and Asia, however, where regulations are less stringent, polycarbonates may be used in almost any glazing application except the windscreen.
Compared to the shape limitations of glass, polycarbonate glazing is lighter, impact resistant and versatile. The Smart car’s rear polycarbonate quarter panel, for example, integrates the weather stripping, moulding and clips into the glazing as a single unit. So when the piece is installed in the factory, it is simply snapped in. There is no need for sealants or other parts.
GE Advanced Materials and Bayer MaterialScience have spent huge sums to promote and develop polycarbonate glazing over the past few years. Their 50/50 joint venture, known as Exatec, has launched its first complete polycarbonate vehicle glazing system. The partners believe their Exatec 900 coating system could open up new styling opportunities for OEMs and form the catalyst for a new tier industry – Polycarbonate Glazing System Suppliers. They report a clear trend toward larger backlights and panoramic roof panels using plastics. Exatec predicts this application is just the tip of the iceberg. “Polycarbonate is about to become a major alternative to glass in future cars,” said Clemens Kaiser, CEO of Exatec. “The introduction of Exatec 900 glazing technology will open up entirely new construction and design options for automotive manufacturers which will help to transform the market.”
Bayer MaterialScience’s plastic glazing material (Makrolon) is currently being applied to various Smart and DaimlerChrysler models. The rear triangular windows of the Smart ForTwo, Smart Roadster and Smart ForFour, for example, are made of Makrolon AG 2677. The transparent roof module of the Smart ForFour is another of the current applications for Makrolon. DaimlerChrysler uses Makrolon for the louver roofs of its A and B class models.
How well do you really know your competitors?
Access the most comprehensive Company Profiles on the market, powered by GlobalData. Save hours of research. Gain competitive edge.
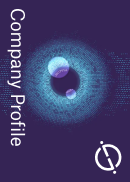
Thank you!
Your download email will arrive shortly
Not ready to buy yet? Download a free sample
We are confident about the unique quality of our Company Profiles. However, we want you to make the most beneficial decision for your business, so we offer a free sample that you can download by submitting the below form
By GlobalDataVolkhard Krause, Global Head of Automotive Glazing at BayerMaterialScience AG
said development with this special grade was focused on finding a balanced ratio between good flow properties and Makrolon’s typical outstanding toughness, even when the surface is coated with different primers and/or hardcoats. An additional challenge was to comply with the specification made by customers and OEMs for especially high product purity in transparent colour shades.
At least three injection moulding machine makers have been investing in technology to support polycarbonate glazing applications. They are Germany’s Battenfeld and Krauss-Maffei and Austria’s Engel.
Battenfeld has partnered with the mould maker Summerer and Exatec (as developers of an external plasma coating) to make plastic glazing. Battenfeld’s so-called IMPmore (In-Mould Pressing) process works by injection-compression because plastic car windows must be virtually free of stress to ensure the necessary weathering resistance and to allow effective anti-scratch coating. An executive of Battenfeld told us: “The main advantage of this process — especially for very large mouldings is that the mould pressure remains very low. So we can achieve mold pressures of about 180 bar whereas for conventional injection compression the mold pressure would be about 210 – 230 bar. The main advantage of the IMPmore process is for making mouldings in excess of 0.7-square metres. For Summerer and Exatec, the mouldings will be 1.4-square metres for a roof module. This is the largest mold for a mass produced car.”
Meanwhile, Krauss-Maffei has sold a 3,200 ton Revolution two-platen press to Freeglass to mould glazing for the Smart car. The unit is located at Freeglass’ site in Schwaikheim, Germany.
Italian Incos Group has established a new division to concentrate on injection-moulded alternatives for the growing market in large-area automotive glazing. The newly formed division, known as InGlass Tooling, will combine Incos’ tooling expertise in multi-component headlamp/tailamp PC/PMMA lenses with the sequential hot-runner feeding experience of its HRS-Flow subsidiary. Inglass will employ for its tool tryouts the latest 2K Glazemelt 2300 tons injection-moulding machinery purchased by Austrian firm Engel. In October 2004, at the K05 plastic show in Duesseldorf Engel in cooperation with INglass demonstrated for the first time the manufacture of a 1,000mm x 800mm polycarbonate sunroof panel with integrated surround using its latest 1,500-ton Duo Combi CleanShot.
Alessandra Bosco, Manager of Global Business Development for Incos group, told us: “Since 1987 we are focused in automotive lighting tooling. We realized that in the future, we expect to integrate more and more rear lighting with the rear window. In order to achieve that, it was very important to find a new technology able to mould large surfaces in plastic but with a very low in-mould stress. The best way to do this was to use the injection compression technology. This technology fits also perfectly to mold 2K large surface window such as panorama roofs where plastics is particularly attractive because it has more safety features and weight advantage compared to Glass. Since we presented a two colour large surface with a very low in-mould stress last year, the market looks like moving more and more in this direction.”
Advantages of Polycarbonate Glazing
![]() |
click table to enlarge |
Styling and design· Shape complexity.· Assembly complexity and functional integration.· Individualisation with colour and tints. Safety and security· Passenger retention.· Anti-smash-n-grab.
Weight saving· Lightweight door designs.· Removable windows.· Lower centre of gravity. Environment· Fuel economy.· Recycling.
On the flipside, the relative cost of polycarbonate compared to glass is still a concern.
A spokesman for BMW told us: “Cost is a factor when looking at alternative materials to glass, however with on-going development in both design and production plastic glazing could become more viable… Aside from the cost issue, optical quality, two-component-moulding, the coating process, bonding and size of panel all still represent hurdles that need to be overcome if plastic glazing is ever to meet BMW’s exacting quality standards and be fitted to a production car.”
Volkhard Krause said: “Cost comparisons between applications of different materials always involve the risk of being based on different requirements. This applies in particular to a comparison between glass and polycarbonate. If we compare a flat sheet of annealed glass with a flat sheet of polycarbonate, glass will always be the cheaper solution. In order to obtain a realistic comparison, it is essential to consider that, when using polycarbonate, all the potential for integration offered by injection moulding and injection-compression moulding can be brought into play. This includes, for example, fixing elements like screw bosses and snap fits, guides for adjacent parts and gaskets, and the direct moulding of different materials like rigid/flexible combinations. By exploiting these integration options, polycarbonate can certainly compete with glass, plus it has the added advantage of weighing appreciably less, which means, for example, lower fuel consumption and improved vehicle handling. In any case, in view of the outstanding impact strength of polycarbonate, any comparison should be made not with annealed glass but with laminated glass.”
Another problem common to plastics in optical applications is scratch resistance. Even the hardest plastics have surface properties significantly inferior to those of glass. Michel van Russelt, Solutia Inc’s market development director, told us: “One of the drawbacks of polycarbonate in general is that it is a material that is extremely susceptible to any kind of chemical agent. So if you were for any reason to chip the coating, the risk is that any kind of intrusion could soon start to attack the polycarbonate in that place and then eventually destroy the mechanical performance of the product. In this situation, some ‘micro crazing’ or small cracks begin to appear in the polycarbonate.” Headquartered in St Louis, Solutia is the world’s largest producer of the PVB (polyvinyl butyral) plastic interlayer that is used to manufacture laminated windscreen, side and rear glazing. Solutia has also developed an acoustic PVB windscreen.
Developments in plasma technology, however, allow the application of coatings that yield surfaces on plastics with comparable long-term scratch resistance. Freeglass, the joint venture between Saint-Gobain Sekurit and Schefenacker AG, says it is developing its own plasma deposition process for achieving scratch-resistant polycarbonate windows. First serial vehicles using the plasma-coated windows are not expected until at least 2008. The company expects to double the number of polycarbonate automotive windows it moulds from 2005 to 2008. Freeglass says it has seven products in series production for DaimlerChrysler, and one each for Porsche and Seat (i.e. rear encapsulated fixed sidelite of the new Seat Leon). Gerald Aengenheyster of Freeglass GmbH, told us: “We feel that our wet coating systems are already perfect for our existing applications concerning scratch resistance and UV resistance. We have now produced several million plastic glazing components. They have been equipped to cars since 1998. So we have a certain experience of in-field use of plastic glazing. Nevertheless, we see two trends. The suppliers of coating systems are developing new systems and showing improved UV and scratch resistance. So that development will continue. In parallel, Freeglass has its own development of plasma coatings and expect a further improvement in scratch resistance.”
A spokesman for DaimlerChrysler told us: “Polysiloxane paints are currently used in series production to make the coatings resistant to weathering and abrasion. We are currently focusing our development activities on improving UV resistance and achieving higher scratch resistance by means of plasma CVD processes.”
Cynics of plastic glazing also claim that the acoustical behaviour of plastic glazing is inferior to glass, especially when it rains. In response, Aengenheyster said: “It is true that rain does sound different on plastic glazing than on glass. It is different but that doesn’t mean it is worse or better.” Dr Klaus Badenhausen, Head of Engineering and Design for the Smart car group, added: “The acoustical behaviour is a little bit different because of the density of the material. But it is not inferior, just different.”
For the past eight years, researchers at Warwick University have been busy looking at alternative glazing materials. Dr Kirwan of the Warwick Manufacturing Group said: “We have concentrated on hybrid technologies, mainly using polycarbonates with laminate skins. We have also looked at directional failure. One of the problems of plastic windows – or beauties of it depending on which way you look at it – is that you can’t break into the car. It is intruder resistant. Conversely, the occupants cannot get out in an emergency. So what we found is a mechanism for directional failure – enabling the window to be broken from the inside but not from the outside. We are now looking at that technology along with some other anti-graphite and anti-scratch technology based upon nano-ceramics in order to develop it for public vehicles such as tubes, buses and coaches. It could also be used for large car applications.”
DuPont recently launched its so-called Spallshield, the company’s first generation plastic composite product for use in car sunroofs. DuPont claims it represents a totally new alternative to pure organic plastic glazing or other existing glass-glass type laminates. Hayati Yarkadas, global marketing manager for DuPont Glass Laminating Solutions, said: “It is a composite of polyvinyle butyral [PVT] and polyethylene terephthalate [PET], with an additional anti-scratch hard coating on the outer surface of the PET, which can be applied to a single, standard layer of glass. The key value Spallshield brings is five to eight times the impact performance versus standard laminated glass, whilst weighing up to 30 percent less.” Spallshield currently features on two vehicles that are already on the road this year. The technology is also being considered for use on some 14 other new vehicles. Beyond sunroof applications, Spallshield is being considered for sidelights and backlights. Yarkadas points out that that the glass-plastic composite provides protection against spalling should the glass be broken. “The PET film, laminated with the glass, serves as a spall protection layer which keeps the dangerous glass shards in place until replacement of the part. Standard laminated glass, consisting of two layers of glass with a plastic interlayer in-between, or traditional tempered glass, are unable to provide this protection.” The technology basically looks like this:
![]() |
click table to enlarge |
It is clear that we should expect to see plastic glazing replacing certain glass applications, market growth will be gradual starting in Europe fuelled by designer’s interests in styling and flexibility. Panoramic roof systems will be the next major application.
|