As carmakers gradually warm to the idea of sourcing door modules, the potential of the total market should not be confined to side doors but sliding doors and rear liftgates. Matthew Beecham reports.
What is a door module?
A door module typically consists of a rubber-sealed carrier made from plastic or metal. Aluminium and magnesium are also being considered by manufacturers to reduce the weight of the carrier still further. A variety of door components are then fitted onto the carrier, forming a ‘cassette’, such as the window lift mechanism, locks, electric motor to operate the wing mirror, wiring harness, various switches, loud speaker and a cable that connects the latch to the inner release handle. The carrier plate is then tested and sealed to the outer door.
Delphi’s modular door systems feature integrated sub-systems, which make up the entire door system. Major door system components include the trim elements, moveable side glass, window lift, electrics and electronics, latching, switches and climate control features. Delphi supplies door modules to a number of vehicle makers, including General Motors, DaimlerChrysler, Isuzu and International. “In our door business, we make the distinction between door modules and power products such as power sliding doors,” said Lon Offenbacher, business line executive, cockpits and interior systems, Delphi Thermal & Interior “For door modules, we offer the whole range from minor component level integration which we call Level 1 — which could see a window regulator connected to a latch – to a fully integrated door module with full functionality of window lift systems, locks, handles, electrical harnesses, and HVAC connections which we call Level 3. This is essentially a type of plug and play module with the window and channel included. It entirely depends on the vehicle manufacturer’s needs and how much integration they allow us. Level 4 is the ultimate where you would ship the entire door system to then hang in place. One of the things that we bring to the marketplace is that we understand the door system first and foremost. Understanding the electrical and mechanical interaction inside out and interface management with customers is absolutely crucial.”
Most of the major suppliers pitching for door module business have their origins in either window regulators or plastic interior trim. For example, ArvinMeritor, Brose, Dura Automotive, Grupo Antolin and Kuester all have a strong tradition in the window regulator business. Brose used last year’s Frankfurt motor show to reveal a number of its latest door system innovations, including power drives for side doors and liftgates, a new latch and window regulator as well as its highly integrated door system with a plastic functional carrier. Kurt Sauermheimer, head of Brose’s door module business, said: “Our door carriers can be made from steel, aluminium and plastic. In some situations, plastic door carriers have clear advantages over metal carriers with regard to weight and integration. For example, we shall soon start production of a plastic carrier integrating the complete window regulator function, eliminating the need for separate guide rails. We have one such contract in Europe and two in the US due to enter production shortly.”
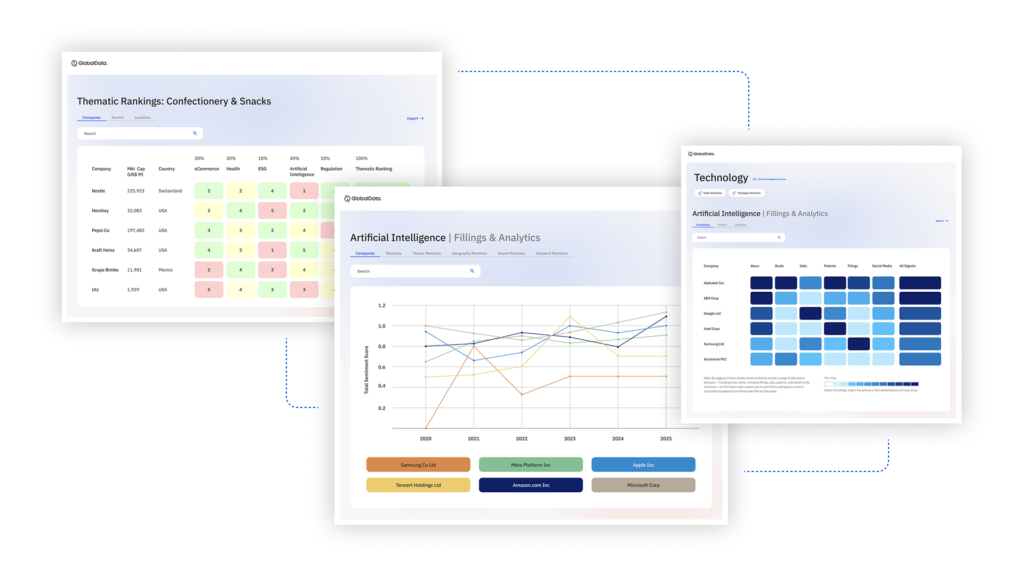
US Tariffs are shifting - will you react or anticipate?
Don’t let policy changes catch you off guard. Stay proactive with real-time data and expert analysis.
By GlobalDataWhat are the benefits?
The benefits to the carmaker from outsourcing door modules centre on cost and weight savings. Some suppliers believe that a move to door modules could save the vehicle maker up to $20 per car, although the actual savings will vary according to the processes, materials and the level of integration already in place.
Faurecia estimates that when a carmaker moves from conventional door assembly to door modules, the time to assemble the door falls from about 25 minutes to just five minutes because only one element has to be assembled as opposed to ten. “We design and produce door panels, door modules and complete doors for carmakers worldwide,” said Heinz Josef Rüsche, sales and marketing director of Faurecia’s door business. “Although demand for complete doors is more focused on assembly than development, the involvement of suppliers in the door design is more and more important. Above all, carmakers are relentless in their pursuit to reduce cost and weight. In respect of door modules, we are able to use our skills in plastic composite technology to meet carmakers’ demands. These modules comprise the door panel and all the mechanical composites such as locks and window-lifts, electric and electronic functions. Plastic cassette door modules typically have the advantage of integration thereby reducing the number of single components that ultimately results in cost and weight savings. For example, a plastic door module can shed 3 – 4 kilograms per vehicle and typically generates a significant saving per vehicle.”
Above all, the carmaker can combine a number of components into one, fully-tested assembly. There is also a health and safety advantage since assembly line workers no longer need to reach through sheet metal to route all the cables.
The power of sliding doors
Manufacturers forecast that the demand for complete door modules will gain greater application as soon as the inherent paint, fit and finish problems are resolved as well as the problems in supplier participation in unionised OEM plants. The potential of the total market, however, should not be confined to side doors, but liftgates and sliding doors. Indeed, the popularity of multi-purpose vehicles in Europe, Japan and the US has spurred many innovations, not least power sliding doors. The first powered closure systems appeared on the automotive market in 1999. They relied on electro-hydraulic drive units but their application was limited due to cost constraints. In 2002, Citroen (C8 model), Fiat (Ulysse), Lancia (Phedra) and Peugeot (807) became the first European carmakers to offer mass production vehicles fitted with an electric power sliding door. More recently, Delphi’s power-operated sliding doors on the new Peugeot 1007 has attracted a great deal of attention. The model was the first ever to boast power sliding doors on both sides of the car.
Figure 1
Power to the people: The Peugeot 1007 is the first small car to feature a single motorized door on both sides, power-assisted throughout the operating range.
![]() |
Source: Peugeot. |
HIP and HIM
Meanwhile, ArvinMeritor’s Light Vehicle Systems Door Systems division headquartered in France has created a new and highly-integrated door module which replaces the traditional steel carrier frame with a composite plastic structure that saves about 25% in weight. The HIP (highly integrated plastic) module is the fourth generation of a design that was begun in the 1990’s. Thanks to plastics moulding technology, the company has designed-in fixtures and attachments for the various components such as the latching system, window motor and audio speakers that greatly reduce assembly complexity. Once OEMs begin buying the technology in around three years’ time, the company estimates they will be able to achieve cost savings per door of around 25-30%. “The HIP is a design and development programme aimed at addressing two main business drivers: cost and weight,” said Mark Lawrie, Chief Engineer, Window Regulators & Modules, ArvinMeritor. “The way we are treating cost and weight within the HIP programme is to try to optimise the integration and utilise low weight materials like plastics. It is an R&D programme because we are trying to gain enough knowledge to be able to provide the market with a range of products. Above all, we don’t believe that there is simply one solution we can sell to everyone. We have reached the point where we have a good knowledge base of what is possible in terms of state of the art technology to make this integration. The next step is looking to implement our know-how on a range of plastic door modules. In fact, we already have projects spun-off from an earlier HIP generation that we are developing with specific customers in mind.”
Figure 2
HIP replacement: ArvinMeritor’s highly-integrated plastic door module.
![]() |
Source: Arvin Meritor. |
Last summer, Faurecia won a contract from Chrysler to supply its Highly Integrated Door Module (HIM) for a vehicle platform in the US. The deal is significant for the French group, enabling it to gain a foothold in the North American door module market. The French group’s HIM combines window controls, latch systems, outer handle, lateral shock absorbers, cables and loudspeakers on a plastic carrier. “While our second generation HIM integrates the rails for window regulators, the third generation excludes them,” added Rüsche. “Both are scheduled to enter production this summer. All three generations focus on cost and weight reduction. The combination and flexibility of the different solutions with and without rails basically allows us to cover 80% of new vehicles. So while we cannot have a standard and common solution for every door, the flexibility of our design and innovation path allows us to cover nearly all of the passenger car market.”
Blossoming Chinese market
Conti Temic believes that the European and Japanese door electronics market is reaching saturation in terms of revenues as motor integrated solutions migrate down the car segments and prices drop significantly over time. In North America, however, the company is predicting some significant growth in the door electronics market as it lags Europe. The Chinese market, however, is even more promising, says Conti Temic. “We believe that China will contribute to our sales growth above average over the next few years,” said Walter Ulke, Head of Development, Body Electronics Business Unit, Conti Temic. “Although the technical content of car door electronics packages in China will initially be lower than seen in Europe or Japan, it will basically depend on what drivers perceive they really need. Overall, we expect the automotive body electronics market in China to increase by about 12% CAGR between now and 2010, compared to about 9% CAGR in North America and 3 – 4% in Europe.” Conti Temic’s door control module modules include the electric operation and heating of the exterior mirrors, and selection of electric seat adjustments with memory function. By May 2003, the company had produced some 20 million door modules.
It’s clear that over the next few years, we’ll see some major changes in the way in which vehicle makers source their doors. The trend in both Europe and the US is toward increasing complexity of the door componentry, adding more and more electronic functions. However, there are still some significant hurdles to cross before the industry sees the complete door in volume production. In addition to power sliding doors, some manufacturers see a number of opportunities in liftgate modules, especially when combined with power product technologies and advancements in lighter materials, such as aluminium and plastics.
|