It may not look like it, but the door is the second most complex system on a vehicle, the most complex system being the cockpit. It must look good, incorporate crash stability and, above all, be fit to open and close more than 50,000 times during the vehicle’s life.
It also hides a myriad of functional componentry such as the window lift mechanism, locks, electric motor to operate the wing mirror, wiring harness, various switches, loud speaker and a cable that connects the latch to the inner release handle.
However, the assembly of all of these parts by hand is expensive and time consuming. In the mid -1980s, the Volkswagen Group was among the early adopters of outsourcing the ‘door module’ or cassette, trimming in-house assembly costs in the process. Global market leader Brose produced its first door module for the Audi Coupé in 1987. A decade later, Brose won its first major order for door modules from Volkswagen, supplying units for the Passat. Production commenced in 1997 and Brose’s door module business almost doubled in 1998. Door modules now account for Brose’s fastest growing component segment.
The trend in both Europe and the US is toward increasing complexity of the door componentry, adding more electronic functions and, in some cases, the glass itself. There are still some significant hurdles to cross before the industry sees the complete door in volume production. Manufacturers forecast that the demand for complete door modules will gain greater application as soon as the inherent paint, fit and finish problems are resolved as well as the problems inherent in supplier participation in unionised vehicle maker plants. Even though many vehicle makers have proclaimed their intentions to buy more and more systems and modules, there are still only two complete door examples in Europe where a supplier either ships a fully assembled door, which is attached to the car body (the Smart car), and a structural door where the OEM attaches the inner and outer panel (VW Touareg/Porsche Cayenne). Nonetheless some predict the industry will begin to see the widespread shipment of complete modular doors – consisting of structural components, glass, sealing and the inner electrical and mechanical workings – by 2006.
What is a door module? There are two types, interior and exterior..
An interior door module consists of a rubber-sealed carrier made from plastic or metal. Delphi’s Superplug was originally thermoplastic whereas Brose’s and ArvinMeritor’s designs are metal. Aluminium and magnesium are also being considered by manufacturers to reduce the weight of the carrier still further. A variety of door components are then fitted onto the carrier, forming a ‘cassette’, such as the window lift mechanism, locks, electric motor to operate the wing mirror, wiring harness, various switches, loud speaker and a cable that connects the latch to the inner release handle. The carrier plate is then tested and sealed to the outer door. Brose’s solution is to seal the carrier plate to the outer door, dividing it into ‘wet’ and ‘dry’ chambers, thereby saving money on waterproofing. Brose claims that mounting electrical and electronic components in the ‘dry’ chamber also increases reliability. The only difference between the front door module and the rear is that the front cassette includes a double guided window regulator (due to the angular shape of the front glass) to help guide the window into the door without any shudder.
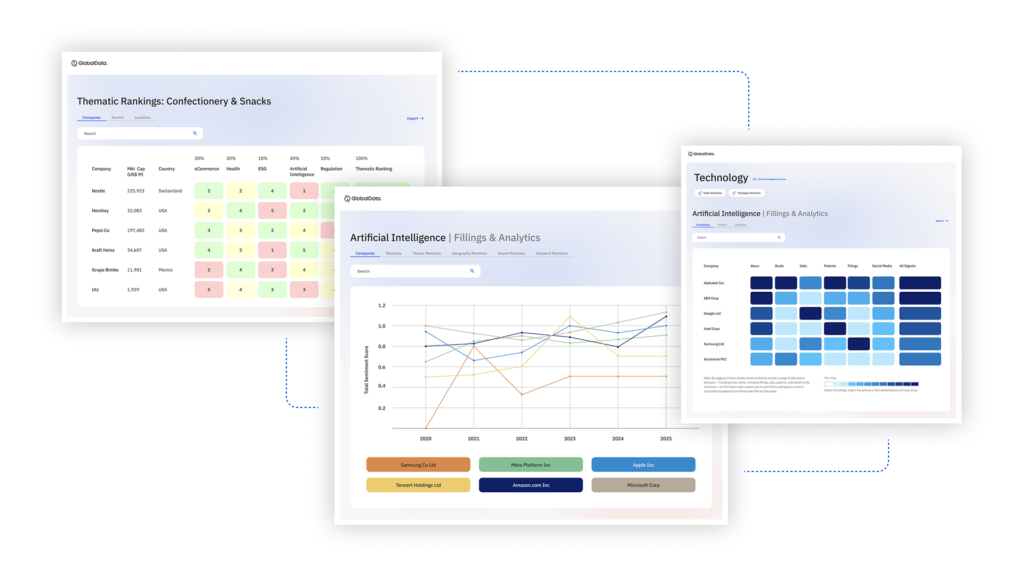
US Tariffs are shifting - will you react or anticipate?
Don’t let policy changes catch you off guard. Stay proactive with real-time data and expert analysis.
By GlobalData![]() |
Delphi’s integrated door module |
The level of componentry, however, can vary immensely from one trim level to the next. Manufacturers typically carry 90 different part numbers for each of the four doors. Whereas one model may offer a manual latch with central locking, another may include an electric latch with super-locking. There are five different types of latch offered for the Golf, for example. There are more than 200 front door module combinations alone, ranging from all-manual to all-electronic.
The door panel itself consists of several component parts that are attached to a substrate by various methods. Specific components of Lear Corp’s door panel include vinyl or cloth-covered appliqués, armrests, radio speaker grilles, map pocket compartments, carpet and sound-reducing insulation. In addition, door panels often incorporate electronic and electrical distribution systems and products, including switches and wire harnesses for the control of power seats, windows, mirrors and door locks.
Exterior or structural door module is in its infancy
While the interior door module market is gaining momentum, the exterior or structural door panel market is still in its infancy. This module consists of a pressed metal frame, impact protection and exterior skin. Although structural doors are typically made from steel, combining extruded profiles, die cast components and pressings, there is a notable trend toward aluminium, particularly in the upmarket car segments. As one supplier said: “Weight savings play a more important role in the sports-utility vehicle (SUV) segment than in any other. The opportunities for using aluminium not only for door structures but also in other areas of car bodies is higher with SUVs.”
Aluminium is also about 40% more expensive than steel so applications on some cars and regions are limited, as the supplier added: “The North American car makers are driven by cost, not weight considerations. Unlike Europeans, they are not prepared to pay more for a lighter door. Our focus is on Europe, with the strongly increasing number of derivatives on one line. I think that there is a big opportunity for structural door modules being implemented on such cars with regard to lower volumes per derivative. We see annual growth rates in the area of 10% – 15%.” Just 10% of exterior side doors are currently made by outside suppliers in North America.
Market trends
As the door module increases in complexity, suppliers are forming alliances in order to offer the necessary design and project management skills. For example, since 1999, Johnson Controls has been working with Oxford Automotive to develop integrated door systems. Johnson Controls defines such systems in three levels:
- A Level 1 door system includes a door hardware cassette and door trim assembly – which could include latch assembly, latch rods, window regulator, glass run channels, speaker, wire harness, glass and carrier – that are shipped to the vehicle maker and installed onto the vehicle as separate components.
- A Level 2 door system combines the trim assembly and hardware cassette into a single system ready for a simple electrical connection and attachment to the door steel assembly.
- A Level 3 integrated door system is a complete door assembly – or module – that includes trim, hardware and exterior body components, fully finished and ready to assemble to the vehicle.
The partners used the 2000 North American International Auto Show to display their Level 2 integrated door system. Johnson Controls designed and developed the trim and hardware module for the door while Oxford Automotive applied its skills in door metal to optimise the exterior door structure by adding strength and reducing weight. “We view supplying door systems as evolutionary not revolutionary,” said Lou Kincaid, group vice president, product and business development for Johnson Controls. “We currently supply automakers with complete seat systems, overhead systems, cockpit systems and door trim systems, so teaming up with a leader such as Oxford Automotive to further develop Level 2 and Level 3 door systems is the next logical step in this evolutionary process.”
|
Oxford Automotive designs and makes a range of door panels and components including closure panels, inner door panels, door assemblies, hinges, latches, locking mechanisms and sliding door mechanisms. The customer base for its door components includes both GM and Ford. Oxford Automotive supplies the door, hood and underbody assemblies for the GM Pontiac Aztec and Buick Rendezvous and the doors and structural components and apron assembly for the Ford Focus and Escort as well as the closure panels (doors, decklids, hoods and trunk lids) for the Saturn LS. In early 2002, Oxford Automotive filed for protection from creditors under Chapter 11 of the US bankruptcy code.
Delphi Corp has also developed a range of modular door systems, dividing their product offering into four levels of integration. Level 1 contains door hardware and trim components, such as latches, connectors and trim. Level 2 sees these components integrated into multi-system door builds. At Level 3, Delphi integrates the door structure components into the multi-system module, based on either hardware or trim. At Level 4, Delphi takes on total responsibility for delivering a complete door to the vehicle maker, from inner trim to outer skin. In November 2002, Delphi announced that it will supply what it terms its modular door to DaimlerChrysler for its new Actros heavy-duty vehicle. Delphi says this module is at Level 3, adding that there is another unnamed vehicle currently being developed that will also feature its Level 3 door module. Delphi perceives that most of the European market is currently at Level 2.