The fragility of the automotive supply chain has been highlighted by natural disasters, particularly in Asia over the past 18 months. This month’s management briefing considers how fragile the supply chains of international manufacturing firms have become and the strategic responses now being formulated in response to the Thai floods. This fourth and final instalment looks at the consequences in Thailand and the wider implications for sourcing and supply chain strategies.
Incentives kick-start sales in Thailand
October 2012 was not the first time the low lands of Thailand have suffered flooding and it is unlikely to be the last. There have been a number of severe floods in recent history and the automotive sector, which had an annual production capacity of about 2m units in 2010, has been one of the most affected industries. This is largely because the vast majority of suppliers, whose number has grown over the past three decades to support Japanese carmakers in particular, are based in those low-lying areas of Ayutthaya and Pathumthani provinces.
Last year’s floods were all the more serious because they not only disrupted local production and supply, there was also a major effect on the regional and global supply of automotive parts and vehicle exports. The domestic market is now back on its growth track as the factories have got back into full production and customers have been spurred by a ‘First Time Buyer’ government incentive.
The government has been keen to kick-start sales as it believes the automotive industry has become a driving force for the Thai economy. The scheme provides tax refunds to first-time car buyers. Those eligible must be at least 21 years old. And they must hold ownership of the cars for at least five years. Their vehicles must not be worth more than THB1m (US$30,000), with engine capacity not exceeding 1.5-litres. The cars must also be manufactured in Thailand. Car buyers are refunded the actual amount of tax they have paid but the ceiling of the refund is set at THB100,000 (US$3,000) per car. The scheme runs out at the end of 2012 but is projected to boost the Thai new car market to 1.2m.
The first-time car buyer programme was part of the government’s policy aimed at raising the standard of living. The finance ministry expects the programme to enable at least 500,000 low-income earners to have the opportunity to own a car.
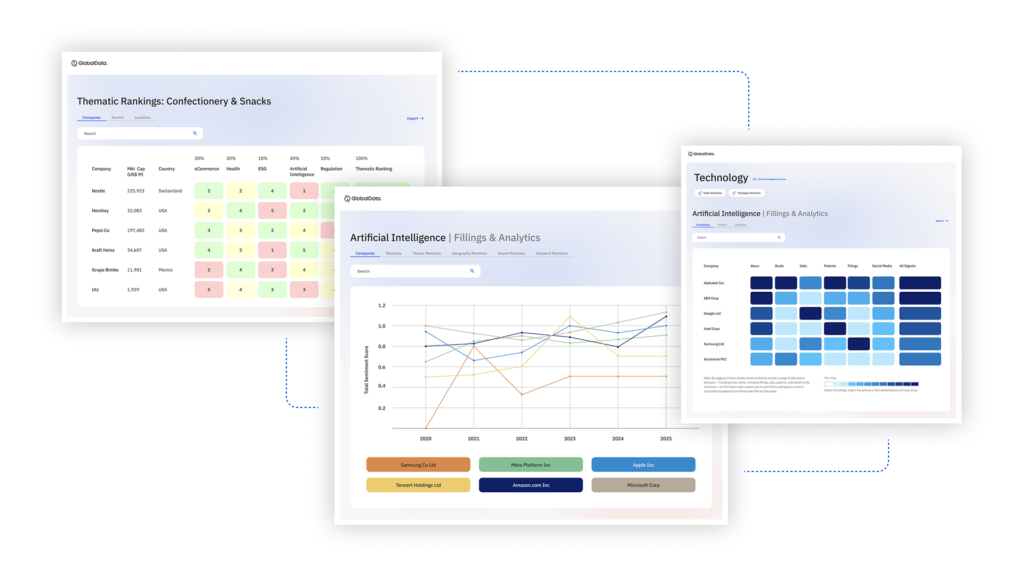
US Tariffs are shifting - will you react or anticipate?
Don’t let policy changes catch you off guard. Stay proactive with real-time data and expert analysis.
By GlobalDataThe government’s car-friendly attitude is one of the reasons automakers have been attracted to the country in the past few decades – and the fact that there is no domestic industry to protect. In 2010, Thailand produced 1.6m vehicles, half of which are exported, the highest ever in the history of Thai auto manufacturing. The figures were skewed last year by the floods but this year production is expected to hit 2m, which is just about the installed capacity. Ford has already opened a second plant, Toyota has a new factory coming on line to build an all-new, Thailand-only model by the end of 2012.
All this has led Thailand’s finance ministry to raise its growth forecast twice this year. Improving manufacturing and higher-than-estimated exports in the first half of the year indicated that the recovery from the floods is almost complete. By July, the finance ministry raised its 2012 growth forecast to 6.2% and said easing inflationary pressure would allow the central bank to hold the interest rate through 2012 while keeping watch on an economic slowdown in China and a deepening debt crisis in Europe.
This is a more upbeat forecast than that of the World Bank which suggests growth this year of 4.5%. The bank notes that Bangkok’s flood recovery and rehabilitation programmes, as well as its income support policies, have helped boost confidence but cautions that the threat of any further floods may affect consumer and investor confidence.
World Bank senior economist for Thailand Kirida Bhaopichitr, says that the country made “considerable recovery from the devastating floods” but still faces the challenge of the global economic slowdown which would dampen exports further. Thailand will need to be prepared in the event of severe global economic slowdown by ensuring adequate fiscal space while quickly improving productivity and competitiveness of Thai exports.”
The automotive sector has been at the forefront in terms of the speed of production recovery to meet demand both for exports and the local market. However the electronics sector hadn’t fully recovered by mid-year as many factories struggled to re-equip.
There is always a danger that the same thing could happen again. Some companies are building new defences to protect multi-billion dollar industrial estates in the country. The events of last year have also made companies look at future risks although according to insurance companies, factory construction in flood-prone areas remains rampant across Asia. July’s flooding in Beijing, China, shows how disaster can hit at any time. Severe flooding in the upper Yangtze river cut off cargo shipments by boat to the inland cities of
Chengdu and Chongqing, affecting the supply chains of Toyota, Volkswagen, Geely, Suzuki, Ford and Changan Automobile.
Insurance companies say the auto the industry is vulnerable to major floods across Asia with the coastal plains of southern China being a particularly high risk area. While rapid – too rapid, it could be argued – industrial development has lifted millions out of poverty in Asia, many factories have been built along coasts without any long-term historical data on floods and storms. Rising sea levels, increasing rainfall, intense storms, growing populations and infrastructure all multiply the risk.
According to the latest assessments by insurance companies, Thailand is ninth in terms of flood risk in the region with China number one. The Thai floods hit nearly 1,000 factories and cost insurers an estimated USD20bn. A recent study by Texas A&M University and Yale University shows the amount of developed land in low-elevation coastal areas in China is rising dramatically, from 13,500 sq km in 2000 to 63,600 sq km by 2030, an area nearly as large as the Netherlands and Belgium combined. In 2010, the journal Irrigation and Drainage, said one third of China’s farmland, two-thirds of its people, more than 60% of its cities and 80% of its GDP were threatened by floods. There is a problem in that Chinese data is often not detailed enough to be useful – and that some government agencies feel information on water flow is too sensitive to share.
Insurers and reinsurers are also worried about dense concentrations of factories in other parts of Asia, particularly in and around the Indonesian capital Jakarta, where floods in 2005 and 2007 hit large areas. It is the nation’s manufacturing base with US, European and Japanese firms operating factories. Cikarang, east of Jakarta, has five industrial estates with more than 3,000 plants employing 1m people.
Despite the floods in Thailand, no-one is looking to walk away from the country and as production quickly ramped up, and more companies still set up there, manufacturers are facing a human problem. A labour shortage is threatening to affect the auto industry’s rapid growth according to the Thai Autoparts Manufacturers Association. It said that parts suppliers are unprepared to meet the drastic increase in automobile production this year. They cannot recruit enough manpower for full capacity.
The association expects 120,000 additional workers will be needed in the parts manufacturing industry over the next five years as automobile output increases to an estimated 2.5 to 3m units.
As the yen strengthens, Japanese investors particularly are looking for new locations overseas for their investments. Thailand and Indonesia are ideal locations, but Thailand badly needs to develop human resources.
It has a high literacy rate – around 95% for men and 90% for women – and unemployment is very low averaging 1.73% from 2001 to 2012; the highest it has been is 5.73% in 2001 and the lowest 0.4% in the middle of last year, according to national statistics.
Against this background it is easy to understand why attracting workers is not just a problem for suppliers, it affects carmakers and other industrial groups as well. Somnek Ngamtrakulchol, vice-president, human resources at GM Thailand, admitted that it has become very difficult to get new people, especially after the floods because everyone wanted to ramp up production very quickly. That problem is compounded by the number of new companies constantly coming in to the country.
“Increasingly we find we have to search further up country to find people and it is an issue that we are talking to the national government about. We have a large requirement for unskilled workers but many young people are moving on into higher education and university so we now have a co-operative with about 15 schools where we take on some 300 students for six or seven months and they then go back to school and are replaced by another 300. This gives them experience in the workplace and also fills our requirement for non-skilled staff, but it is the government which should be coming up with such initiatives.”
The shortage of labour is also putting up employment costs. GM workers have already had a 40% wage increase this year and will get more at the end of 2012 with the government’s introduction of a minimum wage limit set at THB300 (USD10) an hour. According to the Bangkok Post, the momentum of recovery in Thailand has been stronger on the demand side, driven by buoyant private consumption, increased government spending and an increase in private investment linked to business rebuilding activity. Business has also benefited from liquidity fuelled by strong capital inflows, as well as flood related fiscal allowances and subsidies.
These factors have helped offset weaker exports in 2012, reflecting a decline in global trade and a slower return of export orders.The newspaper pointed to three major threats to Thailand’s economic recovery. The first is the expected continued weakness and sharper downturns in the global economy linked to problems in the eurozone, which could put further downward pressure on global and regional growth. Important in this context is the impact on domestic liquidity and an expected Asia-wide slowdown – especially among important regional players such as China and other East Asian economies, which are major trading partners.
The second is the possible recurrence of natural disasters – especially floods – that could affect the economy while the third threat to Thailand’s economic recovery is the domestic political situation. Resurfacing tensions could seriously affect investor confidence and discourage private investment.
Despite the risks, the current market consensus for Thailand is positive and the momentum of recovery is expected to continue into 2013, thanks to the resilience of the economy and positive government policies.
Conclusion: continuous crisis planning is vital
Ironically, as this report was put together, the Federation of Thai Industries (FTI) warned that a drought might be imminent which could cost millions more dollars.
The FTI had been monitoring water levels in Rayong, home to many car plants and the situation was described as “not very pleasant”. The Federation also warned that a drought could hit industry and agriculture. The last major water shortage was in 2005 and cost industry USD30m. At the same time, in China severe flooding in the upper Yangtze river cut off cargo shipments by boat to the inland cities of Chengdu and Chongqing, affecting the supply chains of Toyota, Volkswagen, Geely, Suzuki, Ford and Changan Automobile.
The Yangtze serves as a major transportation link between China’s interior and coastal regions and many key components are delivered to carmakers by boat. At one point, more than 700 boats were moored waiting for the water levels to drop. Trucks were used as an alternative – not an ideal solution in a country notorious for its traffic delays.
As if earthquakes, tsunamis and floods are not enough, how about the biggest power blackout in history which struck half of India at the end of July 2012, bringing industry and transport to a halt and leaving 670m people without electricity?
The blackout stretched from the border with Burma in the north-east to the Pakistan frontier in the west, taking in major industrial areas around New Delhi and Calcutta. While power cuts are frequent in the country, nobody was prepared for three regional grids to collapse.
This serves to prove how anything can go wrong at any time and while automotive production in Thailand was affected short term because of the break down in the supply chain, the chaos caused by the flooding is unlikely to have a long-term effect on the country’s position as an automotive production hub in the ASEAN region. However, companies need to beware of over-reliance on Thailand which now has outsize importance in the global supply chain.
Government policy and investment is critical. The Thai government has set aside THB350bn (USD11bn) for water management and flood prevention programmes. Natural disasters are now recognised as a major risk to business in Thailand, so a credible programme on flood-prevention will help foster confidence and promote further private sector investment.
The reliance on Thailand factories underscores a potential weak link in many companies’ strategies to trim costs and maintain profitability: Manufacturing supply chains sometimes are too narrow to withstand an unexpected disruption. Japan’s massive earthquake and tsunami last March chipped away at second-quarter growth rates in countries around the world as manufacturing of key electronic components and specialised chemical compounds were stopped in their tracks. The year before, a volcanic eruption in Iceland disrupted air cargo and travel across the Atlantic Ocean.
The Thailand disaster revived the debate over whether the lean supply chain concept is being pushed too far. It seems that natural disasters are becoming the ‘norm’ rather than one-off events; witness this year’s summer heatwave and drought in the American mid-west coinciding with floods in northern Europe and the UK.
There are three factors to consider when organising supply chains:
- Capacity;
- Inventory on hand;
- Time needed to adjust production in event of disruption.
Some of the companies caught up in the Thai floods are already rethinking diversifying their supply chains, although the events of October 2011 are generally being viewed as ‘abnormal’. Component procurement may be broadened out but Thai-based manufacturers will stick with the country because that’s where they have invested heavily.
As most of the car company chiefs point out, crises can arise anywhere in the world at any time. They have been highlighted by the earthquake and tsunami in Japan and the floods in Thailand – made worse by the fact that they came so close together. They, of course, followed the global economic downturn in 2008, 10 years before that the Asian bubble burst sending the Japanese and South Korean economies, amongst others, into tailspin.
Currently, the strength of the Japanese yen and the euro currency crisis in Europe are providing the headaches.
It is impossible to predict what may happen next or where, but as the boss of Honda Thailand said, you can’t go around trying to avoid the trouble because you would be on the move every year – and the trouble will catch up in the end. The key is in managing the risk. Whatever that may be.
It’s worth repeating the word of GM Thailand’s human resources chief boss, Samnuek Ngamtrakulchol, who said: “No one was prepared for the flooding and I think that the lesson we take away from this for the future is that contingency plans have to be kept fresh. You can’t put them away in a drawer and think they are done because things change all the time.”
His comment was backed up by GM Thailand president Martin Apfel, who said that the crisis needed a new management mindset, looking much further down the supply chain than previously as well as taking care of the workers close to you.
Communication is also key and many companies complained that they did not receive enough information from the Thai authorities as the flood waters spread.
The next big problem for manufacturers in Thailand is a shortage of labour and Apfel believes that the Thai government has got to be careful.
“Already hiring is not easy and wages are being driven upward. We have to jump through hoops to staff up. The concern is that Thailand may suffocate itself, and by the time it finds out it may be too late. There are plenty waiting in the wings such as Vietnam, Myanmar, Indonesia and Malaysia.
“Attrition across the industry has risen to unhealthy levels in Thailand. Suppliers are also starting to find it difficult to hire and that makes the situation very worrying.”
Japanese carmakers and Tier 1 suppliers, who led the charge into Thailand over the past three decades are increasingly looking elsewhere for components. They are also looking to spread their sourcing while the strength of the yen greatly weakens the export competitiveness of Japan made products.
The 2011 disasters highlight the fact that a crisis can arise anywhere and at any time. The important thing is to have a contingency plan in place, and to continually update that plan.
To compensate for the loss of production OEMs, both carmakers and suppliers, need to have a back-up and the ability to shift short term production to neighbouring countries.
Supply Chain disruptions have been the main reason for many OEMs to stop their assembly lines due to floods. Some of the factors that are likely to be considered by OEMs in the future are:
- Increasing inventory of parts so they have enough stock for at least a month if there are any disruptions related to component supply;
- Multi-sourcing from different suppliers and from different regions, although this could have implications on local content and therefore taxation;
- Making sure that plants and supplier parks are not sited at locations which are at risk of flooding etc;
- Those companies who are in high risk areas need to move vital machinery, if possible, onto a second or third storey and to find back up warehousing in other areas.
To see the other instalments in this series go to: just-auto monthly management briefings