The fragility of the automotive supply chain has been highlighted by natural disasters, particularly in Asia over the past 18 months. Carmakers are looking again at their supply chain strategies in the wake of the earthquake and tsunami in Japan and the massive floods in Thailand last year. This month’s management briefing, written by Interchange Europe exclusively for just-auto, considers how fragile the supply chains of international manufacturing firms have become and the strategic responses now being formulated in response. This first part looks at the evolution of the flood event itself and its devastating effects.
Floods expose fragilities in lean supply chain
The globalisation of the car industry including its supply base over the last 20 years has generally led to greater economies of scale, greater efficiency and – the industry would like us to believe – more nimbleness.
There’s one word they won’t use – and that’s fragility. Just how fragile not just the car industry but other global manufacturers are was severely – and tragically – exposed in 2011 when Japan was devastated by an earthquake and tsunami in March followed by the equally disastrous floods in Thailand a few months later. Economic losses were estimated by the World Bank at THB1.4 trillion (USD45.7bn), which makes the floods one of the top five costliest natural disaster events in modern history. The two combined to demonstrate the inherent risks of narrow supply chains.
Manufacturers from Japan, the US and elsewhere have concentrated on building key production hubs around the world. Thailand emerged as one of these growth hot-spots in the 1980s when the depreciation of the US dollar helped send Japan’s yen soaring. Japanese car manufacturers responded by seeking alternative production hubs overseas.
Many chose Thailand, including Toyota, Honda, Nissan, Mazda and Mitsubishi. They were followed in by Ford and General Motors who wanted to be closer to the emerging markets and take advantage of skilled but low cost labour. They were also lured in part by investment incentives that allowed foreign firms to own the land on which they built their factories. Thailand also had a relatively good infrastructure for the region, some of it the result of heavy US investment during the Vietnam War.
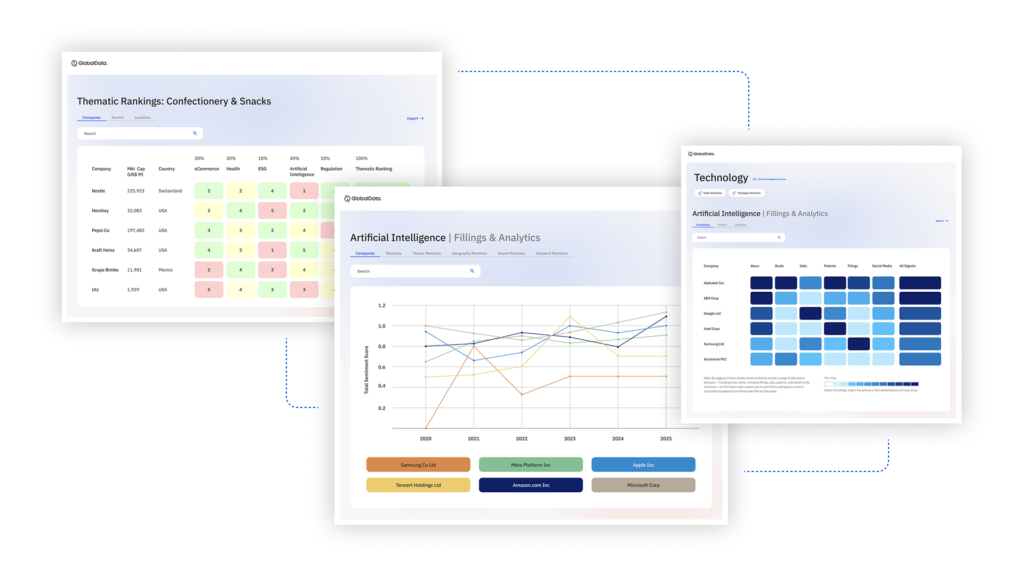
US Tariffs are shifting - will you react or anticipate?
Don’t let policy changes catch you off guard. Stay proactive with real-time data and expert analysis.
By GlobalDataIt wasn’t just the carmakers who beat a path to the country known as the bread basket – or perhaps the rice bowl would be more accurate – of South-east Asia. Other industries followed, notably the burgeoning electronic and computer businesses creating critical mass in terms of hard disk plants, semiconductor factories and food-processing operations. Thailand has now become a major production and export hub.
Around these major industries has grown a huge supplier community and unfortunately for the carmakers, many of these are in Ayutthaya, one of the regions devastated by last October’s floods. Many were completely under water – up to five metres deep. Images of submerged cars at Honda’s plant in Ayuttaya showed the effects of the severe flooding on businesses.
What this meant was that supply lines to the major industries were cut and not just to the factory lines in Thailand. As vital electronic components manufactured in disaster-hit northern Japan impacted on engine management systems globally, so did other vital components made in and exported from Thailand.
Most of the car plants are based outside the worst-hit region, notably Rayong south of Bangkok. But production lines at all of them ground to a halt as the supply and logistics chain suddenly stopped.
The flooding affected 64 of Thailand’s 77 provinces, damaging World Heritage-listed temples in Ayutthaya, destroying 15% of the nation’s rice crop and flooding the homes of almost 19% of the country’s 67m people, according to government data. The death toll totalled more than 800.
The production losses related to the disasters in Japan and Thailand hit company profits, particularly those of the Japanese manufacturers, already struggling with a surge in the yen which has risen 15% against the dollar in the past three years, and with the increasing challenge of its South Korean rivals, which have been gaining ground partly due to the relative weakness of their home currency.
Many of the Japanese makers are shifting more production overseas, but as the Thai floods demonstrated, this doesn’t necessarily ease the problems, it just makes them different. Toshiyuki Shiga, Nissan’s chief operating officer, has said that Japan is losing its competitiveness, and with volumes declining at home the company is shifting more to growing markets like India. In Thailand Nissan has also increased output by taking up some production line slack at Mitsubishi’s plant.
Coming so soon after the earthquake and tsunami in Japan, Thailand’s floods became a major catalyst for companies to reassess their supply chains.
But it could have been worse for automotive companies who were shielded to some degree by having multiple global production hubs. For example, Sony and Nikon digital cameras are solely produced in Thailand causing a shortage of supply and delays to new model launches. Apple faced delays in parts used for Mac computers. Hard disk drives for other computers were also in short supply globally.
But it was bad enough for several car companies. In a paper published by Prof Shigeyuki Abe of Japan’s Dorisha University, and co-written with Pongsak Hoontrakul, it was noted that module production has made it possible to separate production processes into different locations, resulting in the creation of global supply chains.
With this in mind, labour intensive processes were moved to low-wage countries such as Thailand which has been for some time a major, low-cost assembly base for Japanese supply chains. When these were suddenly interrupted it had knock effects in Japan, the US and Europe.
Over the course of this October briefing, we will look at how the car companies in Thailand were affected, how they dealt with the situation, what they learnt and the impact this has on their sourcing policies.
The attraction of Thailand is clear. Vehicle exports from the country were fewer than 100,000 a year in 1997. This year will see around 1m Thai-built models being shipped. This is expected to rise to 1.5m by 2015. Pick-ups dominate, accounting for more than 40% of the vehicle market, hence for many of the manufacturers this is a centre of global pick-up production.
The advantage of Thailand over its south-east Asia neighbours is that it has the deepest supply base, established originally by the Japanese makers some three decades ago. It also has the advantage of being known better outside the region than many of its neighbours. And, of course, it used to have a healthy cost structure.
Now, though, with unemployment at just 1% in the auto industry, the workforce can be choosier about who they work for and companies are struggling to fill skilled vacancies. But our report also uncovers an extremely loyal and caring workforce, characteristics that surfaced in last year’s floods.
How the floods developed
Given the severity of the 2011 flooding it is worth recording how and why it happened and the signs to look out for should it happen again. There are suggestions that communications and reactions to the developing situation were lacking.
The flooding occurred during the 2011 monsoon season although it was triggered by the landfall of Tropical Storm Nock-ten which spread through the provinces of northern, north-eastern and central Thailand along the Mekong and Chao Phraya river basins.
By October floodwaters reached the mouth of the Chao Phraya, the river that runs through the centre of Bangkok, inundating parts of the capital city. The water did not fully recede in some parts of the country for four months and around the country resulted in a total of 815 deaths while an estimated 13.6m people were affected. Of Thailand’s 77 provinces, 65 were declared flood disaster zones, and over 20,000 sq kms of farmland was damaged, seriously affecting the country’s position as the ‘rice bowl’ of South East Asia. In terms of disaster severity it ranks only behind the earthquake and tsunami in Japan some six months earlier, the Kobe earthquake, also in Japan, in 1995 and Hurricane Katrina which hit the southern states of the US in 2005.
The World Bank estimated that around USD45.7bn of economic damage and losses was caused by the flooding; most of this was to the manufacturing industry as seven major industrial estates were inundated by as much 3m (10ft) affecting 230 suppliers. Disruption to supply chains affected car production and caused a global shortage of hard disk drives.
Although the monsoon season generally gets underway later in the year, noticeable rainfalls started from May with the first flash flooding in many provinces beginning at the end of July. Flooding was still ongoing by late August, and water reached 50cm in downtown Nan and became the highest recorded in 16 years in Phitsanulok Province, while large areas in the downstream provinces of Nakhon Sawan, Ang Thong, Ayutthaya – home to the Honda factory which was completely inundated – were affected.
By mid-September almost all lower central provinces were being affected and broken floodgates resulted in water from the Chao Phraya flowing through irrigation canals and inundating large areas of paddy fields. By the beginning of October, most dams were already near or over capacity and being forced to increase their rates of discharge, potentially worsening downstream flooding. As water entered Ayutthaya, people started to be evacuated from their homes. Barriers protecting industrial estates failed, resulting in flooding of dozens of major factories, including Honda, and country-wide disruption of manufacturing supply chains.
The floodwaters drained southwards from Ayutthaya and Bangkok was seriously threatened by mid-October.
Lack of warnings
The government has been criticised for underestimating the extent of flooding, giving mixed or conflicting information, and not giving adequate warnings. Failure of government units to share data and cooperate have been reported as contributing to the problem. Local and national government administrators have been criticised for playing politics and refusing to cooperate at the expense of the general population and industry.
According to many reports there was a critical breakdown in communications between Thai authorities and foreign companies largely because of the lack of information in English. Japanese electrical giant Toshiba issued a statement saying: “It is critical for the government to provide more accurate flood information and implement long-term prevention measures.” Other foreign investors,including the carmakers, share this anxiety. Another Japanese company, Rohm Integrated Systems, which makes semiconductors in Navanakorn, said it received very little information about the flood and could not move critical equipment in time.
Many industrial estates were badly affected by flooding, resulting in manufacturing disruptions and global supply shortages. Damage estimates of at least THB185bn (around USD6bn) by the Federation of Thai Industry includes THB95bn damage to industry, THB25bn damage to agriculture and THB65bn damage to housing and communities. A large part of the damage stems from the effect on the manufacturing industry, with 930 factories in 28 provinces affected and the flooding has been estimated to result in a decrease of up to 1% in economic growth.
Thailand accounts for about 30% of global trade in rice and 25% of the main crop did not survive the flood waters. While many global manufacturers were able to recover, many thousands of small farmers were not.
The country is the world’s second largest producer of computer hard drives, accounting for approximately 25% of global production. Total vehicle production in the country, by comparison is 2m. The floods are estimated to have cost each carmaker up to USD2.5bn.
The knock-on effect hit manufacturing and sales in other countries. Thailand is second only to the US in terms of pick-up production and sales. The top-selling Toyota HiLux and Ford Ranger were two Thai-built pick-ups that were in short supply in export markets, notably Australia and South Africa, as well as in the domestic market. Stocks of the Nissan Navara, Mazda BT-50 and Mitsubishi Triton were also squeezed by production shutdowns.
While Honda’s factory on Ayutthaya was the only car maker completely flooded – it was out of action for six months – the majority in Rayong, south of Bangkok, escaped serious damage. They were affected, however, by the break down in the supply chain as suppliers and logistics were hit.
Supply chain halted
While the effect of the floods in Thailand on carmakers was well documented, their facilities, with the exception of Honda, were largely undamaged. The problems that shut down local production lines and caused major disruption globally were because the supply line came to a halt as Thailand’s component companies were inundated by the rising waters.
Almost all auto parts for local production come from the flood affected regions of Ayutthaya and Pathumthani provinces, home to some 40 Tier 1 suppliers and hundreds more below them in the chain.
In the aftermath of the floods, all companies reviewed their supply chain strategy – as did the suppliers; the scale of the floods caused supply chains to falter and break. The facts speak for themselves: nearly 200 factories, including Honda, had to close in Ayutthaya after an industrial estate run by Rojana Industrial Park was flooded. Some 20 suppliers on the Rojana and Saharat Nakorn industrial estates were affected; those 20 suppliers account for 10% of Thailand’s total parts production.
As the flood waters approached, suppliers rapidly tried moving as much equipment as possible to higher ground in a bid to protect it. There was a race against time to send some tooling overseas in a bid to maintain supplies while some companies needed to import goods to try to maintain the chain.
Thailand’s automotive sector employs around 300,000 people and has up to 3,000 suppliers. The impact of the flooding was all the more severe because production is concentrated in a handful of areas for the sake of just-in-time production and to reduce supply-chain costs. About 14,000 factories were affected by the floods.
Manufacturers trying to maintain production faced enormous challenges in finding alternative suppliers and production locations, and getting parts to their facilities.
Not surprisingly, Thai exports were badly affected, not just because of the production stoppage, but also because the logistics chain was broken. Roads were flooded and as water seeped into Bangkok’s Suvarnabhumi international and Don Muang domestic airports, airlines had to cut their
freight and passenger flights temporarily.
Once the floodwater receded, the real work began with most supplier plants needing three or four months to get back on line. The wait was even longer in the computer sector given the need for absolutely clean facilities.
Tyre maker Michelin suspended some operations at its Thai plants and a Toshiba factory was partially-submerged at Bangkadi industrial park in Pathum Thani province. Car companies reported that they worked closely with affected suppliers to return to production as quickly as possible and to minimize any potential impact in other regions. Michelin said it shut some operations in high-risk areas.
Chinese computer maker Lenovo Group said its supply of hard disk drives was hit as the water swamped suppliers and technology consultancy iSuppli said the availability of hard disk data-storage devices fell by 30% in the last three months of 2011 as a result of the floods; Thailand supplies around 40% of the global output of the devices. Western Digital Corp’s plants in Thailand were closed.
Since the floods, property insurance rates in the country have doubled or tripled and flood cover greatly reduced or even refused in some cases, according to the General Insurance Association of Thailand.
In a bid to counter this some suppliers are moving machinery onto a second floor and even setting up sister operations in neighbouring regions or countries. These include Toshiba on the Bangkadi industrial estate, one of seven parks built on former rice paddies on floodplains north of Bangkok that were inundated affecting companies such as Sony, Canon and Honda.
But Toshiba is not thinking of moving out of Thailand because the supply chain network remains very strong – and it is not that easy to move.
As the supplier industry got back on track towards the middle of 2012 it was faced with another problem: a labour shortage is threatening to affect the auto industry’s rapid growth this year, according to the Thai Autoparts Manufacturers Association. It said that parts suppliers are unprepared to meet the drastic increase in automobile production this year. They cannot recruit enough manpower for full capacity.
This labour shortage is a major problem for the parts manufacturing industry at the moment in terms of both skilled and unskilled workers. The association expects 120,000 additional workers will be needed over the next five years as automobile output increases to an estimated 2.5 to 3m units.The labour force in the automobile parts production industries totals about 450,000.
Coming next: The impact of the Thai floods on the operations of Ford and General Motors