The fragility of the automotive supply chain has been highlighted by natural disasters, particularly in Asia over the past 18 months. This month’s management briefing considers how fragile the supply chains of international manufacturing firms have become and the strategic responses now being formulated in response to the Thai floods. This third instalment looks at the impact of the floods on the local operations of the Japanese OEMs.
Japanese firms hit by double disaster: floods came six months after tsunami and earthquake
About 1,800 Japanese manufacturers operate in Thailand, as well as the car giants Toyota, Nissan, Honda, Mitsubishi, Isuzu and Mazda (in a joint venture with erstwhile owner and partner Ford). The country also hosts big names from other industries including Canon, Nikon, Pioneer and Sony.
Honda: shut for six months
The hardest hit of the carmakers in Thailand was without doubt the Honda plant in Ayutthaya province, some 80kms north of Bangkok. The plantwas totally inundated leading to a six-month halt in production. The plant, along with many of the country’s suppliers, bore the brunt of floodwaters once they had breached the dams in the north of Thailand. Set in the lowlands, the water broke through 5.5m flood defences and further secondary shields Honda tried to build around the factory. The plant stood in almost 2m of water for more than two months before the floods receded. Its two production lines were beyond repair as were 1,055 cars.
Amazingly, the factory took just a further three months to recover. Executive vice president of Honda Automobile Thailand, Pitak Pruittisarikorn, said: “There was complete devastation inside the plant but the building was intact. To get up and running again so quickly is some feat given that it would normally take a year to build a production line and two to construct an entire plant.
How well do you really know your competitors?
Access the most comprehensive Company Profiles on the market, powered by GlobalData. Save hours of research. Gain competitive edge.
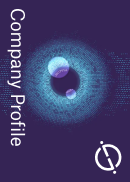
Thank you!
Your download email will arrive shortly
Not ready to buy yet? Download a free sample
We are confident about the unique quality of our Company Profiles. However, we want you to make the most beneficial decision for your business, so we offer a free sample that you can download by submitting the below form
By GlobalData“We did what we could to prevent the flood waters by building sandbag walls around the factory but the amount of water was too great and once it was in there was nowhere to pump it as all the land around us was flooded.
“Once that happened, we immediately started working on how we were going to repair the damage and decided that we would replace the production lines entirely rather than trying to do any repairs – this was the quickest and most cost-effective solution.”
As the flood waters approached, Pruittisarikorn gave the order to start moving completed vehicles out of the factory’s parking area. Around 3,000 were moved to safe ground but there was not enough time for the rest.
There was human cost as well. Some 80% of the 6,000 employees had their homes ruined. They could also not work for three months while the factory lines were re-built. Honda, however, continued to pay 100% wages and guaranteed interest free loans for repair work on homes as most workers were uninsured. The carmaker was insured although Pruittisarikorn said: “As with all insurance cases you only get write-off value so we had to bear around 20% of the cost of replacement.”
Dealers in the country were also affected but although they had no cars to sell, they continued to take orders, Pruittisarikorn said. “Before the flood we had an order bank of 40,000 customers. This grew to 65,000 and even though we are now back in full production the waiting list is still about 70,000.”
During the shutdown, Honda turned to the Thai government for help asking it to relax import duties on cars that would normally be built in the country. Eventually the government relented for two months only during which time the company was able to bring in 6,000 cars from Japan.
Spreading the risk
The Ayutthaya plant is now back at full 240,000 a year capacity. It builds six models, the Accord, CR-V, Civic, City, Jazz and Brio. It also serves as ‘mother plant’ to Honda Siel’s plant in India which also makes the Brio and City. The Thailand operation exports to more than 50 countries as well as sending CKD kits to other Honda factories around the world, hence its importance to the carmaker globally and why the Thai floods had such an impact on the company worldwide. Pruittisarikorn said: “What we have learned is that there is a risk as well as an advantage to manufacturing anywhere. We were already discussing the impact of the earthquake and tsunami in Japan, and how we manage something like that in the future, when the disaster struck here.
“We have certainly learned that you have to spread the risk although nowhere is going to be 100% safe. In terms of sourcing I think you will find most carmakers are looking to make sure their sourcing is not in one place.
“This is a conversation we are having with our suppliers, suggesting to them that they might want to spread their facilities over wider areas or regions.”
What Honda Thailand also learned was that where there is a crisis there is an opportunity. Some media suggested that the company may try to clean up and repair the 1,000 inundated vehicles. Pruittisarikorn said: “Obviously this is something we would not do, but we kept being asked the question. So we brought in a portable scrapper and invited all the media to attend as we destroyed the cars at the factory.
“It was a good story that made all the front pages and the television channels, but it was all about maintaining trust.”
Honda also donated more than USD95,000 to the relief fund and will continue to build a fund for any future disasters by putting aside USD30 for every car sold in the country and USD3 for every motorcycle. Pruittisarikorn said: “This is part of our long-term commitment to Thailand. We have been asked if the flood disaster will make us think about leaving Thailand but we are committed to the future here. As with all our facilities worldwide, Honda is there for the long term no matter what happens.” He added that Thailand remains an outstanding manufacturing site because of the concentration of materials and parts suppliers and its strong infrastructure.
Reports in the Japanese press said that that Honda is even looking to build a second plant, possibly in the southeastern part of the country where the risk of flooding is lower. Japanese business daily Nikkei said Honda wants to bring the new plant, which is expected to have an annual production capacity of 120,000 vehicles, online as early as 2015 making models such as large minivans, for which demand is projected to grow in Thailand. Honda has also recently announced plans to build an Indonesian factory that would triple its output there to 180,000 units annually. Pruittisarikorn said: “We have not announced any plans for another plant as we have been too busy getting our existing one back to full production. If the demand is there then we will consider another factory – but we will probably build it on higher ground.”
Nissan: shortage of parts as 177 suppliers affected
Nissan closed its factory in Samut Prakan, southeast of Bangkok, on October 14 and did not restart until mid-November. Although the plant remained largely unaffected by the flood with all possible measures taken to strengthen the factory’s flood defences, production had to be suspended because of shortages in parts supply. The total production loss in Thailand due to the floods was 40,000 units, although the company said the flood impact to the supply chain did not impact production at Nissan facilities outside Thailand.
The company said it had good visibility to protect production at its major sites in North America, Europe, and China from the flood impact, based on all the countermeasures worked out with suppliers. However, in Japan, Nissan did lose 20,000 units as Nissan teams, together with suppliers, worked to minimise the impact.
Yasuo Shibasaki, senior vice president for production and purchasing at Nissan Motor Asia Pacific, based in Bangkok said that the company’s plant has 20 major suppliers based in Ayutthaya and taking in the second and third tier this number rises to 177.
The floods hit all areas of Nissan’s Thai production, cutting off the supply of stamped parts, electronics, plastics and tyres – in all some 500 parts and commodities. Although flood warnings had been issued, Shibasaki said that there was a lack of communication or information coming from the Thai government about the seriousness of the situation. “This gave us very little time to prepare and we were not expecting such an impact. We had to rely mainly on news from other people on the ground as to how the situation was developing.”
During the month when the production lines were idle, Nissan teams set about the task of outsourcing around the world. Shibasaki said: “It was clear that it was going to be many months before the supply companies could re-start operations and we could not afford to wait that long.
“We had to source components from other regions including Japan, the US, Europe and India which was an extremely expensive operation because everything had to be air-freighted.”
What did Nissan learn from this? Shibasaki said: “It means that we have to be far more pro-active and have the systems in place to fill the gaps when a supply chain goes down. We now have monthly cross-functional and cross-regional video conferences to ensure we can mitigate against any supply losses.”
These meetings look at all upcoming world or economic events and the impact these could have on any region. Nissan is also having ongoing talks with the Thai government about improving communications in the future.
The Nissan factory at Samut Prakan, 21 kms south west of the Thai capital makes the Micra/March – which is also exported to Japan – the Almera and pick-ups which are also exported. Production capacity is 280,000 although this has risen to 300,000 because the company is producing some pick-ups at Mitsubishi’s Thai factory. Nissan employs some 7,000 people in the country.
Nissan was pro-active in its support efforts to the devastated area, donating some USD600,000 in cash, as it believes that the area needs support in the longer term. It worked with its suppliers to resume parts supply and return to production as quickly as possible. It also utilised its Indian production facility in Chennai to export vehicles to markets such as the Middle East.
Nissan’s newly established strategic ASEAN regional headquarters based in Bangkok, has just announced a new six-year business plan, with clear objectives to achieve further growth across the region. A key highlight is the goal to more than triple sales to 500,000 units with 15% market share by the end of 2016, up from 150,000 units and 6% market share in FY2010.
One of the key strategies to realise this growth is the introduction of more than 10 new models during the period, as well as deep collaboration with governmental bodies to gain competitive advantages. The scope of markets for this plan includes Thailand, Indonesia, Malaysia, the Philippines and Vietnam.
This regional plan was developed to support the global direction of Nissan Power 88, the corporate mid-term plan announced at Nissan’s HQ in Japan. This aims to elevate brand and sales, achieve 8% global market share and 8% sustainable operating profit by the end of FY2016.
Toru Hasegawa, president of NMAP, Nissan Motor Thailand, and regional vice president of Asia & Oceania Operations, said: “As car demand in emerging markets has been rising rapidly, we foresee it will soon capture more than half of global sales volumes. ASEAN countries – including Thailand and Indonesia – are among those we have marked as our strategic growth drivers.
“Indonesian total industry volume, in particular, will significantly increase through the government-initiated low cost green car programme. The new ASEAN mid-term plan is to show our strong commitment to the region, with a clear roadmap to realise Nissan’s strategic direction.”
Toyota: staff arrive by boat
Toyota closed its Thai factories for more than a month and coming on top of the disaster at home in Japan six months earlier the closures triggered a shortage of parts at home and abroad. Company president Akio Toyoda said that although Toyota started to get a firm grasp of the situation early on, the floods had forced the closure of some operations in Asia, the US, Canada and South Africa due to a lack of supplies.
Overtime at Japanese factories was cancelled and Toyota also cut back work in Indonesia, Vietnam and the Philippines. Although sited on the outskirts of Bangkok, Toyota’s three Thai factories at Samrong, Gateway and Ban Pho, escaped the flooding. At the Samrong factory in the province of Samut Prakan, employees managed to get to work even though some suffered flooding at their own homes. For some workers this meant chaotic two or three hour commutes – some even by boat.
Toyota’s Thai factories make 10 models, including pickups, and in 2010, they produced a combined 630,000 units.
Kyoichi Tanada, president of Toyota Motor Thailand said that its sales in the country in the first half of 2012 grew 54% over the same period a year ago – before the floods – to 241,245 vehicles, of which 125,457 were pick-ups. It expects total sales for the year to reach 480,000, an increase of 65%.
Toyota’s total production in Thailand, including vehicles for export, is expected to reach 865,000 units in 2012, up from 630,000 in 2010 and 515,000 during the floods last year. Tanada said that the flooding and the earthquake and tsunami in Japan had an impact on production but added that problems had to be managed – and that they can arise anywhere in the world.
He said: “For example, the current problems with the euro currency or the strength of the Japanese yen impacts the auto industry. However, neither of those issues were affecting Thai operations which export mainly to the Middle East and other Asian countries.”
Company boss Toyoda said that despite the problems caused by the flooding the company had no plans to leave Thailand. “Toyota is not considering shrinking its operations here. If anything, we would expand,” he said.
Mitsubishi: shut for a month
Mitsubishi’s factory at Laem Chabang was also closed for a month due to a lack of parts from flood-hit suppliers. The company’s vehicle output in Thailand fell by more than 20,000 units. It assembles pickup trucks and sport utility vehicles in Thailand which is a key source of its one-tonne pickup truck lines and other models which are widely exported, particularly to Asia-Pacific markets including Australia.
Isuzu: local supply chain breaks
Isuzu’s pick-up assembly at Samrong, just 15 miles from Bangkok, was also shut down for a month. The factory normally makes around 170,000 units a year. Although unaffected by the flood waters, the factory’s local content of more than 95% highlighted the problems caused when the local supply chain went down.
Samrong doesn’t have a local supplier park but operates a just-in-time system, with components arriving at the line from its 150+ suppliers based in the devastated region of Ayutthaya, arriving by road as there is no rail link.
just-auto monthly management briefings