What is a front-end module? It depends who makes it and for whom it is made. According to Faurecia, a complete front-end comprises the carrier, shock absorbers, bumpers, cooling fan system, water & engine oil cooling radiators, condenser for the air conditioning system, wiring harness, headlights and various sensors, including the crash sensor which controls the airbag in the event of an impact.
Denso’s front-end modules integrate the radiator, condenser, electric fan, engine inter-cooler and front frame carrier. The world’s fourth largest supplier worked with Daihatsu to develop a light, high-performance, front-end module that is 30% lighter than the conventional component structure for the latter’s light sports Copen model. The front-end module contains the carrier, radiator, electric fan and condenser for the car’s air conditioner, intercooler and air cleaner. Following delivery, Daihatsu installs the bumper and headlights on the Denso-manufactured front-end module. The carrier is made of a light, cost-efficient polypropylene material reinforced with long-fibre glass, which reduces weight and cost. The resin material used to build the carrier is also recyclable.
Plastic Omnium has developed two highly novel front fender and front-end module concepts that offer assembly advantages and the potential to incorporate advanced pedestrian head and leg impact protection systems. The concepts are pre-assembled on a carrier integrating headlamp, wheel arch, air guide, acoustic damping, water tanks and additional lighting such as fog or side marker lights. Apart from offering a reduction in assembly costs, the design also allows carmakers to virtually eliminate gaps where lighting systems and bumpers join. Each of the two modules comprise two integrated modules, one dedicated to the main technical functions and the other carrying parts such as bumper cover, headlamps, sensors, antennae and so forth. The sub-module is made from a new hybrid metal/plastic technology offering high stiffness and good acoustic properties.
The front-end module brings benefits to both carmakers and end consumers. Carmakers are able to reduce the number of operations on their assembly lines, simplify their supply chains, reduce modular weight and improve the ergonomic aspects of the assembly process. It can also help cut tooling costs and improve working capital. The most important potential benefit of modular construction is standardisation, allowing suppliers to offer standard solutions to different manufacturers and hence bring costs down.
Motorists, for their part, gain in terms of perceived quality and repair costs for accidents occurring at speeds below 10mph, as in 80% of cases, since disassembly and assembly are quicker.
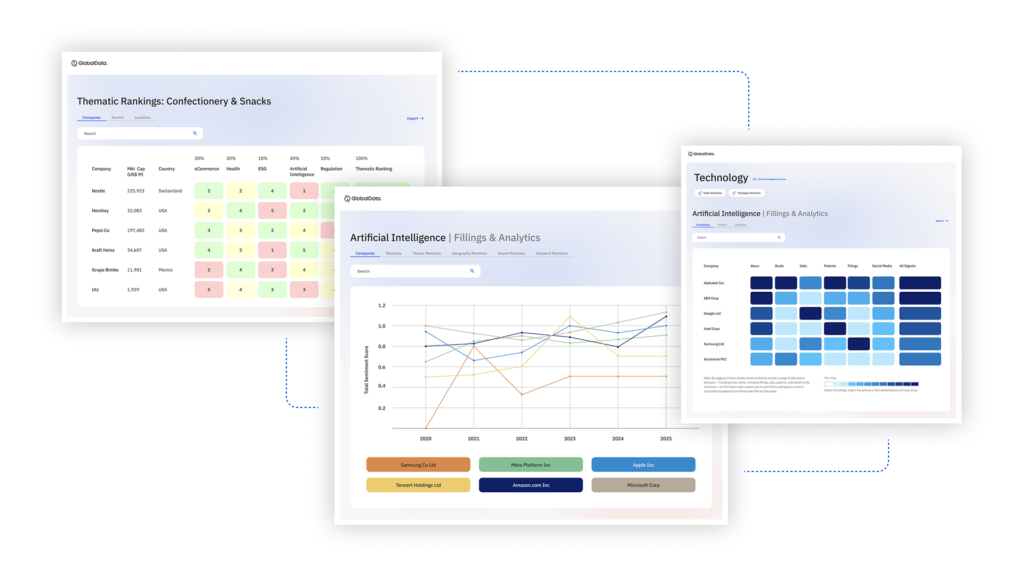
US Tariffs are shifting - will you react or anticipate?
Don’t let policy changes catch you off guard. Stay proactive with real-time data and expert analysis.
By GlobalDataForthcoming regulations to protect pedestrians have created new technical issues amongst front-end module suppliers. New EU laws designed to protect pedestrians and cyclists, effective from 1st October 2005, are set to create major changes in the design of European cars. The new laws are designed to reduce the 8,000 European pedestrian and cyclist fatalities per year by half, and are likely to result in cars with higher, squarer and bulkier front-ends. Manufacturers are speculating that large amounts of foam will have to be used in front-ends and bumpers will have to be lowered. Other ideas being suggested include shock-absorbing, liquid-filled bumper-bags, retractable windscreen wipers and pop-up or pop-forward bonnets.
Figure 1: Front-end module of the Daihatsu Copen (1 of 2)
Source: Denso
Figure 2: Front-end module of the Daihatsu Copen (2 of 2)
Source: Denso
Market players
The main suppliers of front-end modules are Calsonic Kansei, Decoma, Denso, Faurecia, Hella-Behr-Plastic Omnium, Valeo and Visteon. Volkswagen and PSA are among those carmakers developing their own front-end modules.
Calsonic Kansei
Although Calsonic Kansei’s module business is blossoming, the company faces some stiff competition. For the first time in its history, Nissan is to outsource a proportion of its assembly work to overseas automotive component manufacturers. Nissan’s aim is to encourage competition, improve product quality and lower costs. The company has an agreement with Visteon to pre-assemble cockpit modules, which include air conditioning, audio equipment and instrument panels. A similar deal is planned with French supplier Valeo in 2005, which is expected to supply front-end modules for the next generation Serena minivan due in 2005. Production of these modules, which will include parts such as radiators, headlights and bumpers, will probably be handled by Valeo’s Japanese joint venture, Zexel Valeo. Valeo will also supply modules for Sentras built in Mexico for the North American market. The two supply agreements are estimated to amount to the provision of modules for over 200,000 vehicles per year. Until now, Nissan has confined its outsourcing to Calsonic Kansei.
Decoma
Decoma recently introduced its first production front-end module, integrating the vehicle’s bumper system, lighting system and other front-end components. The company believes that front- and rear-end modules represent an important new area of business growth. By 2007, Decoma is aiming to be the global leader in front-end modules. The company believes this market will grow as ‘the drive to modularise becomes as prevalent in North America as it currently is in Europe.’ The company is working with European carmakers as they transform assembly techniques to allow for the integration of increasingly complex modules. In 2003, Decoma strengthened its front-end module presence in Europe with new facilities in Austria, Belgium and Poland.
Denso
Although Denso is a relatively minor player in the front-end module market, the company has potential to strengthen its market position. Denso’s front-end modules integrate the radiator, condenser, electric fan, engine inter-cooler and front frame carrier. The world’s fourth largest supplier worked with Daihatsu to develop a light, high-performance, front-end module that is 30% lighter than the conventional component structure for the latter’s light sports Copen model. The front-end module contains the carrier, radiator, electric fan and condenser for the car’s air conditioner, intercooler and air cleaner. Following delivery, Daihatsu installs the bumper and headlights on the Denso-manufactured front-end module. The carrier is made of a light, cost-efficient polypropylene material reinforced with long-fibre glass, which reduces weight and cost. The resin material used to build the carrier is also recyclable. Traditionally, radiator and air-conditioner condenser products are attached to the front of the vehicle, where they are exposed to the air while in operation for heat exchange efficiency. By optimising the entire front-end thermal component zone, improved heat exchange efficiency not possible through improvements on individual components was achieved.
Faurecia
Faurecia’s front-end module includes the carrier, shock absorbers, bumpers, cooling fan system, water & engine oil cooling radiators, condenser for the air conditioning system, wiring harness, headlights plus a variety of sensors. The French group designs and makes the carrier bumper and cooling fan and buys in the remaining products. Faurecia currently supplies front-end modules to Audi and BMW.
Hella-Behr-Plastic Omnium
In January 2004, Plastic Omnium announced its intention to join forces with Hella and Behr to form the equally owned company, HBPO, to design, develop and produce vehicle front-end modules. The announcement shook the components industry, which sees the venture rapidly becoming a global market leader in the sector. The new company will be headquartered in Lippstadt, Germany but will draw heavily on Plastic Omnium’s Sigmatech R&D facility in Lyon, France. Hella brings its lighting and electronics skills, Behr its engine cooling and air-conditioning knowledge and Plastic Omnium its leadership in European front-end module technology. Hella and Behr have transferred their Hella-Behr Fahrzeugsysteme GmbH joint venture to the new company HBPO. It employs 550 people at eight production sites in Germany, the Czech Republic, Slovakia, Spain, Mexico and South Korea. Its current annual output of 1.25 million front-end modules will be increased to more than 2 million by 2006. HBPO is the only company in the world to be exclusively dedicated to front-end modules. HBPO believes the 5 million unit-a-year front-end module market will treble in size by 2008 and it aims to take a 33% share of that market. The alliance is still awaiting approval from the European Commission.
Valeo
Over the past three years, Valeo has built more than 1 million front-end modules. The French group claims the success of its front-end modules is based on the wide range of expertise shared between the various company branches where the whole front-end module is developed in-house – including bolster, heat exchangers, lighting and wire harness. Valeo is expected to supply front-end modules for the next generation Serena minivan due in 2005. Production of these modules, which will include parts such as radiators, headlights and bumpers, will probably be handled by Valeo’s Japanese joint venture, Zexel Valeo. Valeo will also supply modules for Sentras built in Mexico for the North American market. The two supply agreements are estimated to amount to the provision of modules for over 200,000 vehicles per year.
Visteon
Visteon’s front-end module business is mainly with Ford. The company supplies front-end modules for the Fiesta, Fusion and Mazda 2. Its front-end module integrates the engine cooling system, air conditioning parts, transmission cooling system, power steering cooling system, front-end lighting, air flow management, electrical and electronic systems and bumper systems.
![]() | Expert Analysis | ![]() |
In this second edition reviewing the key market for front-end modules, we broaden the 1st edition analysis from bumpers, thereby extending the market and supplier coverage. Chapter two identifies the main players in the front-end module and bumper market, and their market shares in Europe, North America and South Korea. Our market volume and value forecasts in this study extend to 2008, determining the position in the three largest markets for front-end modules. Chapter three provides profiles of the major bumper and front-end module manufacturers, namely, Calsonic Kansei, Dynamit Nobel, Faurecia, Decoma, Denso, Plastic Omnium, Valeo, Venture Industries and Visteon. Find out more here. |
![]() | ![]() |