The Toyota Manufacturing System has been
admired and to some extent copied throughout the world, but one of its aspects is that it
is constantly evolving. Bob Sliwa interviewed Kosuke Ikebuchi, Senior Managing Director in
charge of production at Toyota in Japan, to find out just how the system is evolving now.
How has the Toyota Manufacturing
System changed over the last few years.
First, our manufacturing system as developed by Sakichi Toyoda and polished by Onno san
and Eiji Toyoda is more than a production method, it is our philosophy, the core of our
company. It has developed gradually over the years but recently there have been several
changes that have greatly effected it.
One major change is the fact that customer
demand is now more sophisticated. It is no longer a market where you make the car you
decide on and customers come to buy it. Basically you must make the car they order – and
build that car to order (custom manufacturing). In this kind of market speed is vital to
success. There are three areas we have to look at to improve delivery lead times:
First of all we have had to speed up what
we call information lead time – that is information collected from the customer at the
time he/she enters our show room and places an order, to when all the orders from all our
dealerships and shops are collected, processed and received at the factory. A good
information system set in place before manufacturing starts is crucial.
Secondly there is the information system in
operation once the car started down the line and the actual physical process of assembly
is underway. We strive to get as high a percent of vehicles through each section of the
line as possible without reworking, but we are realistic. Say 90% make it through the body
line , then 90% the next stage and then say 90% get through the painting line; that leaves
70%. If that 90% drops to 60 or 50%, then it becomes unacceptable. Currently we are
operating at just over 70% total problem free line passage.
Some things can be fixed on the line,
others require the car to be taken off and attended to. This directly relates to the third
and final phase, distributing the finished product. A trailer has four cars loaded and is
waiting for the fifth. Should it wait? When will the car be ready? A boat can only wait
for two hours, will the car be ready?
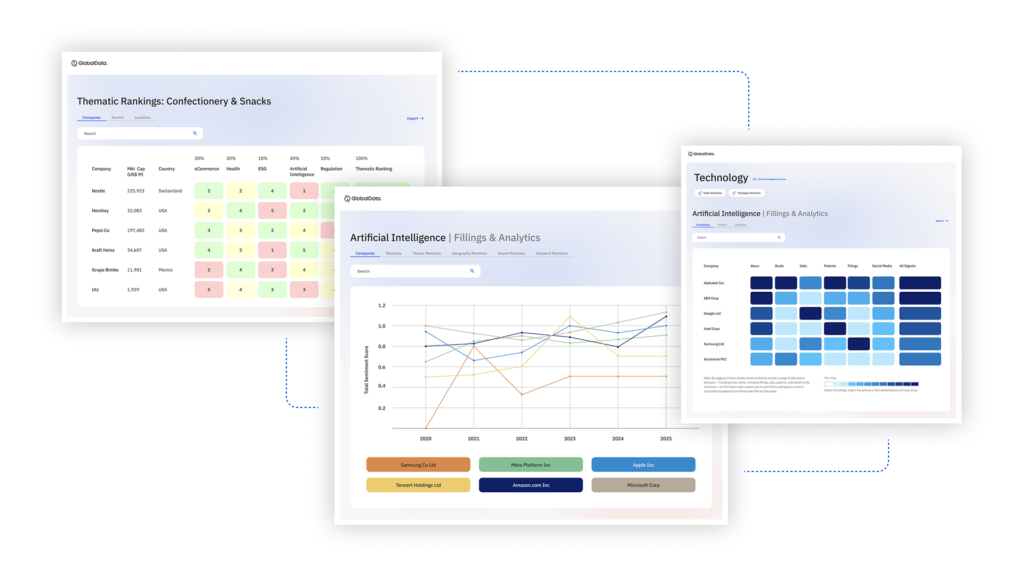
US Tariffs are shifting - will you react or anticipate?
Don’t let policy changes catch you off guard. Stay proactive with real-time data and expert analysis.
By GlobalDataIn the market of the future (if not the
market of today in some cases) the company that can get the car the customer ordered to
them fastest will be front runners.
The second big change has been the setting
up of transplants around the world and the dissemination of information about the system.
Our engineers have worked with and studied other makers, GM and Opel for example and we
have worked with other manufacturers to set up factories. These engineers bring back a
wealth of information on the system as it works abroad and in conjunction with partners.
We really did not know if it would work abroad or not but we have found if their is mutual
understanding of the concept and commitment that it will work.
How does the Toyota Manufacturing
System vary by country?
One big difference is the experience of the workers. It takes time to become familiar and
relaxed with the system. In Japan we have factories where employees have an average of 20
years of experience. These are real veterans. Abroad collective experience might be ten
years or less as turnover is high. What this means is that efficiency is quite different.
For example, we think that producing two cars on one line makes it four times more
difficult for the worker. Three different cars on the same line is nine or ten times more
difficult. Experience helps in these difficult tasks. What does not vary is that we allow
workers, supervised by team leaders, to improve the efficiency of the tasks they are
responsible for by adjusting their own workstations.
While we do allow for differences at the
worker level, the product quality should be the same regardless of country.
What about changes in kaizen?
Kaizen is still done on the line on a day to day basis but what we have increased is the
level of simultaneous engineering on the factory floor that is utilised. This is
particularly true of the new Altezza (IS200) production which started late last year.
When are production schedules set?
Twice a year we send out notices in-house as to production levels for three years from
that time. These are general planned levels. After that specific notices are given one
year, six months and three months before production. During production we send out
confirmation of production figures a month in advance.
What are your current lead in times
and what are your goals for improvement?
I am not sure how you measure lead in time but our Progres (domestic mini LS400) takes
about a day and a half or two days. That is from when the ordered car hits the line until
it is completed. We would like to get this faster but it is not easy and the actual
overall speed is also dependent on volume. I would like to get it to one day.
Are you going to shut down any
plants?
We will not shut down any factories if our sales stay above three million units. We are
all right between 3 and 3.5 million. Over 3.5 million and we will start overtime shifts.
What is the main benefit from you
deepened alliance with Daihatsu?
Of course there are advantages to co-operating in sales and distribution, like Toyota
successfully selling the Daihatsu Storia as the Duet domestically. On the development and
manufacturing side there are also many things to be gained. Daihatsu is basically a small
car manufacturing company whereas Toyota offers a full line up . We are good at producing
full size sedans like our domestic Crown but we are not as good as Daihatsu at producing
small cars cheaply. Daihatsu is as a kei car producer and the company is very competitive
in this segment. In fact all the kei car producers are looking strong in Japan at the
moment – Honda makes motorcycles and kei cars; Suzuki has low operating costs and it too
is a motorcycle and kei car company . We will be co-operating with Daihatsu more in the
future. Indeed, our New Basic Car (called Yaris/Vitz/Echo depending on the market) is an
example of just such a cooperation. The engine is manufactured by Daihatsu, but the car
was developed at Toyota with 20 Daihatsu engineers brought in to the team.
What markets do you see as strong
areas of growth?
It goes with out saying that Asia is a large potential market in the long run. Compared to
500 cars for every 1,000 people in Japan the rest of Asia only has an ownership rate of 12
or 13 per 1,000. Particularly China and India. The main transport may be bicycles in china
now but it is a market with serious potential.
China and India have massive
population so it is natural to look at them but what about the Korean makers who are
entering smaller markets in Asia?
They are very aggressive. I am not sure they really considered the possibility of failure
though. I do not know much about their strategy but they look to be going after niche
markets.
What is the current condition of
keiretsu relationships with suppliers? Is keiretsu a dead word?
Keiretsu is a word you in the mass media brought to the limelight , not one we use. From a
long time ago we made our suppliers independent. Look at Denso or Aisin, they make parts
for other makers though they were once actually part of Toyota. It is only recently that
Delphi and Visteon became separate. Denso sells more than half of its parts to other
companies. Parts makers decide whether to go abroad with us or not. Of course on the other
hand it goes without saying that having your suppliers close to you is advantageous. Look
at America, Honda has grouped its operations in Ohio. Engineers can come and look at a
problem quickly. This is more efficient than Toyota which has plants and offices in
California, Canada and other places.
Has Toyota required its suppliers
to change a great deal recently, asking them to do more sub-assembly, R&D, shorter
response times or increased globalisation? For example, what about what Mr. Lopez started
at VW, basically getting suppliers to construct cars.
There is no way we can do that. Particularly in Japan. It is a matter of scale and
capacity. It would not work for us in the majority of cases, at this moment.
In the computer industry we see
revolutionary technology coming out every year, what about car manufacturing , do you see
revolutionary technology coming out in the future?
Yes, we will see some. For example look at how the borderline between various processes
such as pressing, casting and welding is becoming increasingly blurred. The German
companies are very advanced with their net shape technology. We will see a greater
integration of processes. Europe is more advanced than the US on this front. The
integration of manufacturing processes is going to increase. Another area that will
advance is technology addressing the environmental concerns of manufacturing and operating
cars. Also we will see more plastic in manufacturing , like use in intake manifolds and
such. There will be a revolution in material science. This will be key in increasing
recyclability.
Are you currently including
recycling costs into the your overall calculation of production cost?
Yes. If a new technology is slightly more expensive to employ or manufacture but much
cheaper to recycle we go for it.
This article was kindly provided by World Automotive Manufacturing, an FT Automotive publication.
World Automotive Manufacturing provides clear, concise, impartial and up-to-date
intelligence on the entire vehicle-making process every month. With up to 32 pages of
highly informed analysis and expertly selected material in each issue, World Automotive
Manufacturing will help you anticipate trends, improve productivity and reduce costs,
saving you hours of researching through less focused publications.