Dr. Paul Moller’s Sky Car promises to end airport congestion, reduce travel time, and make gridlock a thing of the past. Crazy at it may seem, it may do just that – and forever change the role and design of the car.
By Christopher A. Sawyer
“There’s no way we’re ever going to build enough new freeway miles to handle all of the growth, so there’s got to be an answer here.”
This isn’t a quote from some telematics guru outlining the need for car-to-car and car-to-infrastructure communication. Here’s another clue. “A highway is a string. It is a one-dimensional world. The three-dimensional world lets you address gridlock if the dimensions and vehicles are integrated. If they are, you can put all of the vehicles currently on the face of the earth in the sky at the same time and they’d be miles apart.”
![]() |
Granted, the Sky Car looks like something the late GM designer Bill Mitchell might have drawn after a Jetson’s cartoon festival, but vehicle creator Dr. Paul Moller (waving) says it’s a three-dimensional answer to travel delays. If successful, it could radically alter the auto industry. |
Intrigued? You should be. If Dr. Paul Moller, president, CEO and chairman of the board of Moller International (Davis, California) has his way, at some point in the future the infrastructure will exist to allow thousands, if not millions, of his Sky Cars to shuttle people from door-to-door on trips up to 900 miles, at speeds approaching 400 miles per hour.
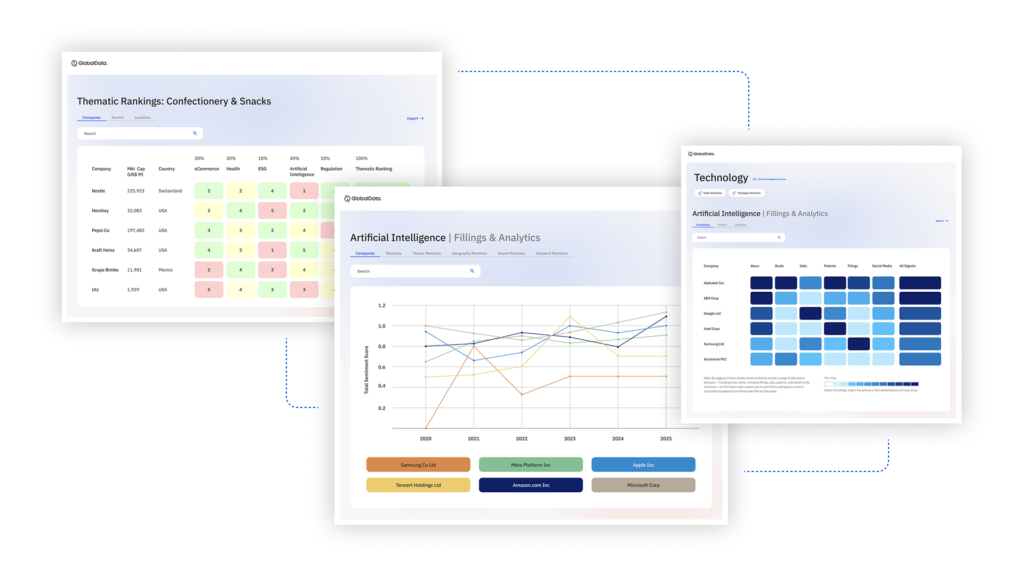
US Tariffs are shifting - will you react or anticipate?
Don’t let policy changes catch you off guard. Stay proactive with real-time data and expert analysis.
By GlobalDataLooking like something George Jetson would fly to his home in the Skypad Apartments, the Moller Sky Car prototype has four sizeable engine nacelles, a large rear wing, and a clear bubble-top canopy. It takes off and lands vertically, and transitions to level flight automatically. Unlike Jetson’s machine, there is no need for human intervention – ever. Sky Car follows an electronic “highway in the sky” that is claimed to keep it at a safe distance from every other airborne vehicle, and unerringly guide it through bad weather and around obstacles like mountains.
Moller envisions that Sky Cars will be on-call as part of an “Air Taxi” service rather than privately owned. Customers will call a dispatcher, wait for the unmanned Sky Car to arrive, load up, and leave for their destination. Different Sky Cars will be used for different passenger loads, from a single-passenger version up to a six-passenger vehicle.
Rotary Club Member
Central to the Sky Car concept is the rotary engine. “Quite frankly, if the rotary engine had never been invented,” says Moller, “the Sky Car would not be a practical vehicle. A Wankel engine has most of the attributes of a turbine engine at one-tenth to one one-hundredth of the cost.”
Cost is important to the Sky Car equation for two reasons. First, the Sky Car uses not one but eight two-rotor engines – two mounted back-to-back in each nacelle driving counter-rotating propellers – for balanced lift and to provide powertrain redundancy. Second, Moller International’s analysis shows that almost every form of transportation is priced at five times the cost of the powerplant. So, if he is to reach the $60,000 to $80,000 selling price he envisions (based on sales of 100,000 vehicles per year), the powerplant must be simple, relatively low-cost, and efficient.
“In today’s dollars,” he begins, “we’ve spent close to $70 million over the past 30 to 40 years just on the engine, which evolved from OMC’s (Outboard Marine Corporation’s) snowmobile design. Each engine has just three moving parts, two rotors and crankshaft. It’s quite simple, which is a good thing when you’re talking about aircraft propulsion systems.”
“The rotary presents a very small surface area to the air,” he continues, “so we can hide it behind the spinner in the center of the duct. Our design doesn’t use oil to cool the bearings. We use air, which means we don’t have to carry around as much oil or the plumbing for oil coolers. This also means our internal surface temperatures are higher because the rotors are air-cooled.”
Higher surface temperatures were not something Moller’s engineers desired. They caused an enormous amount of research into lubricants that work under hot conditions and had the side-effect of promoting more complete combustion. The combustion chamber environment is very air-rich and the rotors have a lot of overlap to promote exhaust gas recirculation. But the development won’t stop here, even though the California Air Resources Board (CARB) says the Freedom rotary is surprisingly clean when running on petrol. “We are moving toward stratified charge in our future designs,” says Moller, “for even greater power and efficiency.”
The reason is simple: It takes a great deal of thrust for vertical takeoffs and landings. Moller claims the current Freedom engine has an installed stall-horsepower of 1.5 hp/lb., though it can produce double that if needed in an emergency situation. This means each of Sky Car’s eight engines produces about 150 hp. “For vehicle use,” says Moller, “Mazda’s rotary engine makes much more sense. Cars spend most of their time at idle or in transient situations. Our engine typically operates at 60% to 70% power, or not at all. So I can do a lot of design simplification because of these operating characteristics.”
simplicity, simplicity, simplicity
Simplicity extends to the rest of Moller’s vehicle as well. There’s no V-22 Osprey-like rotating wing assembly, just four nacelles with computer- controlled rotating vanes to direct the thrust either down or back. The wings are sized for cruising speed, smaller than they would be if Sky Car had to take off and land conventionally. “Our tail creates about 35% of the total lift,” says Moller, “whereas the tail on a normal aircraft exerts a downward force on the plane to stabilise it.” A recent study conducted by Boeing concluded that 75% of Sky Car’s total lift comes from the shape of the nacelles and body, an amount said to be “more than adequate”. (See www.skyaid.org/Skycar/overview2001ALL.htm for more information from the Boeing study.)
![]() |
Ever wonder what happened to the tooling from GM’s ill-fated rotary engine project? It’s being used to produce the Sky Car’s powerplants at Moller International subsidiary Freedom Engines. Without these light, simple, powerful engines the Sky Car would be impossibly expensive and complex. Each Sky Car nacelle contains two twin-rotor, counter-rotating Wankel engines that direct their thrust through variable vanes. Altering the pitch of the vanes directs thrust down for lift-off and landing, or rear ward for forward flight. |
Given the need for a high wing loading, low overall weight, and structural strength and simplicity, it’s no surprise that Sky Car’s structure is made of honeycomb graphite composites. “Weight is a greater concern for Sky Car than for conventional airplanes,” says Moller, “because we have to lift each pound off the ground vertically.” In the case of the four-passenger version, this means a gross weight of 2,400 lb. with almost 800 lb. of payload. The composite materials contribute significantly to Sky Car’s current $1.0 million/unit cost, an amount that actually has the U.S. military excited. Why? It’s less expensive than most conventional combat technologies, and has greater mission flexibility.
Given the extensive technology found in this vehicle, you’d expect that Moller International had a line on powerful design software and heavy-duty computing power. “There’s no design software out there that’ll help us do the job,” sighs Moller. “I’m a computer illiterate myself, so I rely on our independent consultants for advice. They insist we’re faced with designing everything ourselves.” This self-reliance also extends to the design and assembly of the electronic motherboards and flight software.
The Sky Car will rely on a proprietary, quadruple-redundant “voting” type of avionics package similar to the type found on the F-16 and Space Shuttle. “One programmer doesn’t write the entire package,” explains Moller. “If there is a bug in the software, it will end up in one of the four programs, and automatically switch out of that program when the voting takes place.” Machine language is used for the avionics program. “It’s very robust,” says Moller. “It uses a minimal amount of space, and has the least complexity.”
Redundancy
The Sky Car has 26 CPUs on board so that if one circuit fails, there’s a complete backup system ready to take its place. Designing, developing, and building them has taken much time and money, but Moller knows the cost has been small in comparison to what might happen were they unavailable. “I’m trying to show that this is ‘do-able’,” he cautions. “Another corporation can bring the capital – perhaps with government help – necessary to streamline some of these systems.”
A previous concept, which looked like a 1950s-era flying saucer with eight engines nestled in the basic donut shape, had approximately 25,000 lines of software code and dual redundancy. Two independent stability systems triggered back and forth, helping the pilot – Moller – keep the aircraft under control. This was a far cry from an earlier design in which the pilot sat in the centre of the craft while a giant ring rotor, supported by air bearings, rotated around the outside. That version had a single flight control system. “If a ten-cent resistor had burned out,” recounts Moller, “I would have gone down with it.”
Next Steps
Though Moller plans to make the first powered flight of the Sky Car about the time you read this, there’s still more work to do before he’s ready to test Sky Car’s estimated 350 mph cruising speed. Expensive full-scale wind tunnel tests that put the vehicle through a complete flight profile are necessary before attempts are made to gain Federal Aviation Administration (FAA) certification of the Sky Car’s forward flight characteristics. It’s possible the onboard parachutes might come in handy during the testing phase, though Moller thinks they will have a more psychological than actual need once production is reached.
Most important in Moller’s estimation is the need for a proper infrastructure. The first steps toward that goal are being pursued by NASA’s AGATE (Advanced General Aviation Transports Experiment) consortium. AGATE uses GPS satellites, Local Area Augmentation Systems (LAAS) and Wide Area Augmentation Systems (WAAS) to track each aircraft at all times.
The next step, currently in the prototype phase, uses this information to define a specific path or “highway” in the sky that allows pilots to fly a given distance apart at the same speed, and in the same direction. “It would be like a train in the sky with an uncoupled series of cars,” enthuses Moller, “only there will be no need for a pilot because the passengers will have no discretion to change anything once they’re in the air.”
Moller sees Sky Car as part of an “air taxi” infrastructure that sends a one-, four-, or six-passenger vehicle to your door, and then drops you at your destination. Because it doesn’t need lengthy flight time at low levels and full power, it can depart and land from any residential or commercial area with a stable, 35-foot diameter landing pad, on a roof top or at street level – day or night, rain or shine. If successful, it has the potential to radically change where people live and work, and alter the transportation infrastructure.