
Battery technologies for powertrain applications have become a focus of attention as OEMs seek to improve performance and reduce the costs of electrified vehicles – both hybrids and pure EVs. Matthew Beecham talks to industry participants to gauge the bigger picture and efforts to cut costs in this summary article from just-auto/QUBE.
Overview
Not so long ago, the automotive industry was protecting an old technology yet nowadays it has embraced the need for hybrids and the use of advanced battery technology. Macroeconomic, political and environmental events such oil dependency, new competition and increasing carbon emissions have all contributed towards the new move to electrification of transportation.
Yet some industry observers argue that the emerging electric vehicle (EV) and plug-in hybrid electric vehicle (PHEV) markets could flatten out due to unproven technology. They reckon that these markets will be initially bolstered by heavy subsidies to automakers, battery makers and consumers but that sustained growth will depend on yet-to-be-proven battery technology as well as on supporting government policies.
In response, Jay Chmelauskas, Western Lithium’s president told just-auto: “Once you move beyond the early adopters, we expect that the first big market for these vehicles will be fleets due to their greater understanding of the total cost of ownership model. This will ultimately be the proving ground for the vehicles on a large scale. If the technology proves itself and range increases due to early innovations, and we expect that it will, the future could see an increase steeper than all predictions.
“There are many other driving forces such as increasing energy prices, need for energy independence, competition for dominance in a paradigm shift in the automobile industry, and air pollution in major new wealth centres like Beijing to support the electrification of the automobile.”
How well do you really know your competitors?
Access the most comprehensive Company Profiles on the market, powered by GlobalData. Save hours of research. Gain competitive edge.
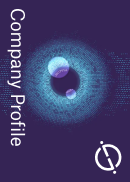
Thank you!
Your download email will arrive shortly
Not ready to buy yet? Download a free sample
We are confident about the unique quality of our Company Profiles. However, we want you to make the most beneficial decision for your business, so we offer a free sample that you can download by submitting the below form
By GlobalDataMeanwhile, the stubbornly high cost of battery packs remains a hurdle for battery producers. For its part, A123 Systems anticipates significant cost reductions in its products over the next several years and these will come from a combination of manufacturing efficiencies and technology advances.
Jeff Kessen, director of automotive marketing, Automotive Solutions Group, A123 Systems, told us: “We believe that it will not be possible to remain competitive in our market by only relying on manufacturing scale to drive cost reduction. Our R&D portfolio benefits from numerous research partnerships and we anticipate that technology advances will contribute to steady cost improvements over time.
“A variety of industry sources are projecting that industry-wide, battery cost could be cut in half over the next five years. By about 2015, industry analysts estimate that costs should be below $500/kWh, with some saying that costs will drop below $400/kWh. Unfortunately many cost analyses don’t state the underlying assumptions and therefore may not be comparable but we find these projections to be in a reasonable range based on what we know today.”
Whichever way you look at it, electric vehicles remain expensive to purchase and give motorists range anxiety with just 100 miles between charges.
“While we don’t want to minimise the issue of range anxiety,” added Kessen, “it is important to note that according to the US Department of Transportation, roughly 80% of US drivers log 50 miles or less per day. There are of course periodic long range trips which an EV won’t support but it’s not reasonable to expect that an EV can replace every vehicle in the market. Rather, we expect that different segments of the automotive market will gravitate to different vehicle types over time. For example, households which have two vehicles may be well suited to enjoy the benefits of an EV in the vehicle predominantly used for work commuting.
“It’s also important to have reasonable expectations for build out of a charging infrastructure. After a home charging location, the next most logical will likely become workplace charging and A123 is actively planning this for its own facilities. We look forward to other employers showing similar leadership as electrified vehicles become more accessible to the consumer.”
Dr Joachim Fetzer, executive vice president, SB LiMotive concluded: “Electric vehicles need batteries that have a high energy density, since a great amount of energy needs to be stored in the battery for the vehicle to travel long distances. Range, which depends in large part on the energy density of the battery cell, is a factor that is crucial to the success of electric vehicles.
“Currently, a state-of-the art lithium-ion battery for a vehicle with a range of 60 to 90 miles would be the size of the trunk of a VW Golf. In other words, a battery with 35 kilowatt-hours of capacity would have a volume of roughly 350 litre and a mass of some 350 kilograms. Customers are demanding a range of 125 miles. To meet their demands, engineers are looking to increase energy density. In raising energy and power density, the focus is on improving the chemicals used in the cells. Improvements in energy density will also make it possible to reduce the weight and size of lithium-ion batteries. Both aspects, reducing battery weight and improving energy density, will help to extend the range of EVs.”
Batteries for alternative drive vehicles
For alternative electric drive vehicles, there are basically three battery technologies available: lead-acid, nickel, and lithium-ion.
The strengths of lead-acid batteries in the automotive sector lie in cost, reliability/safety, recycling and industrial production consideration. Although the basic design of the lead-acid battery is the same as that of the starter battery, the combination of materials and the cell design are specially adapted to the particular requirements of traction operation, says Bosch.
Nickel-cadmium batteries and, increasingly, nickel-metal hydride batteries with an alkaline electrolyte are used in many electrical appliances, says Bosch. As cadmium is harmful to the environment, it is likely that the nickel-cadmium system will be replaced by the nickel-metal hydride system in the foreseeable future.
Lithium-ion technology scores with regard to performance and energy density. On the flipside, such batteries can overheat and catch fire. Lithium is said to be a popular choice for use in batteries because it has the highest electromechanical potential. There are two types of lithium battery technology: lithium-ion and lithium-polymer. According to Bosch, a lithium-ion battery stores lithium ions in electrically reversible form on the negative electrode in a graphite lattice. Lithium-polymer batteries consist of a positive film electrode made primarily of vanadium oxide. Lithium-ion batteries are expected to replace nickel-metal hydride batteries used in today’s hybrid vehicles.
According to Johnson Controls Power Solutions, hybrid systems allow new potentials for reducing power consumption to be achieved through the recovery of braking energy, the temporary shutting-off of the internal combustion engine (ICE) or the operating point displacement of the ICE. The battery plays a central role here: it must provide and deliver as required the electrical energy for starting and accelerating. It must also be able to reutilise the energy recovered during the deceleration process.
Varta says that hybrid electric vehicles (HEVs) use a combination of an ICE and one or more electric motors for the drive. In the full hybrid version they consume up to 40 percent less fuel than a conventional model propelled solely by the combustion engine. The mild hybrid version, meanwhile, still allows a fuel saving of 15-20 percent to be made. Hybrid drive concepts combine the great range and quick refuelling of conventional vehicles with the energy and environmental benefits of electric vehicles. Batteries are an essential part of hybrid vehicles, as they do not only supply the auxiliary components but also power the vehicle.
With the micro-hybrid, says Varta, which is based essentially on the use of a start-stop function, fuel savings of 5-8 percent in urban traffic can be made at relatively little cost. With a mild hybrid, the integrated starter generator supports the vehicle’s starting procedure. On braking, the hybrid is also able to recover electrical energy, which is then stored in the battery. Full hybrid vehicles use a broad technical spectrum of energy-saving options and so require a much more powerful battery than micro and mild hybrids. A plug-in hybrid is a vehicle with a hybrid drive, the battery of which can also be charged externally via the electricity network. Because the drive battery is designed to be larger, it can cover a great distance without the need for a recharge. It therefore represents a cross between a pure hybrid and an electric car.
Battery costs
The stubbornly high cost of advanced automotive battery packs remains a hurdle for battery producers. For its part, A123 Systems anticipates significant cost reductions in its products over the next several years and these will come from a combination of manufacturing efficiencies and technology advances.
Jeff Kessen, director of automotive marketing, Automotive Solutions Group, A123 Systems, told us: “We believe that it will not be possible to remain competitive in our market by only relying on manufacturing scale to drive cost reduction. Our R&D portfolio benefits from numerous research partnerships and we anticipate that technology advances will contribute to steady cost improvements over time.
“A variety of industry sources are projecting that industry-wide, battery cost could be cut in half over the next five years. By about 2015, industry analysts estimate that costs should be below $500/kWh, with some saying that costs will drop below $400/kWh. Unfortunately many cost analyses don’t state the underlying assumptions and therefore may not be comparable but we find these projections to be in a reasonable range based on what we know today.”
SB LiMotive envisions a price of EUR350 per kilowatt-hour by 2015, falling to EUR250 by 2020. Nonetheless, at prices between EUR6,000 and EUR12,000 each, the battery will continue to make up the lion’s share of the cost of an electric or hybrid vehicle in the future.
Alliances for cost sharing
One approach that the industry is adopting to reduce cost is to collaborate. The collaborations take a number of forms.
Nissan, for example, has formed a joint venture with Sumitomo to commercialise lithium-ion batteries previously used on electric cars. The recycling venture, known as 4R Energy, is owned 51 percent by Nissan and 49 percent by Sumitomo. Nissan estimates that vehicles fitted with Li-ion batteries at the end of their useful life still retain up to 80 percent of their residual capacity and can be reused and resold to various industries. Second-life lithium ion batteries previously used in Nissan Leafs can form the basis for mid-sized electricity storage systems for commercial and public facilities. 4R Energy Corporation has now installed a “large-scale power storage system” using sixteen second-life Leaf batteries to create what’s called a “smoothing effect” on the power output of a nearby solar farm by storing excess energy generated by the panels during sunny days and sending it back into the system when the sun does not shine. If the second-life battery technology takes hold, it could provide a positive feedback loop for lowering battery costs.
More conventionally, Chongqing Changan Automobile is working with LG Chem to develop lithium-ion batteries for new energy vehicles. LG Chem started delivering batteries to Hyundai Motor and affiliate Kia Motors in 2009. It has since signed supply contracts with General Motors and Eaton.
SmartBatt international collaboration
The development of cost-effective, lightweight, high energy density and safe battery technologies is widely considered to be a crucial enabler for the successful and widespread take-up of pure battery-electric vehicles.
In order to address this challenge the SmartBatt project – a collaboration between nine research partners from five European countries – has sought to develop battery pack design and optimization processes capable of delivering a 20 kWh, 200-400 volt pack with a 15 percent reduction in weight compared with current state-of-the-art systems, while delivering a continuous power rating of 36 kW, and a peak performance of 70 kW for up to 30 seconds. The battery pack delivered by the project exceeds the capacity target by in excess of 10 percent, providing a total of 22.92 kWh of energy storage.
The objective of SmartBatt is to develop an innovative, multifunctional, light and safe concept of an energy storage system which is integrated in the pure electric car’s structure. The main challenges of this smart integration are the combination of lightweight design with a high safety level against all kinds of hazards, the optimisation of functions and the intelligent design of interfaces to various on-board systems.
The consortium members include AIT Austrian Institute of Technology GmbH, Axeon Technologies Ltd, Fraunhofer IFAM, Fraunhofer LBF, Impact Design, Ricardo UK Ltd, SP Technical Research Institute of Sweden, Vehicle Safety Institute and Volkswagen.
This article was extracted from just-auto/QUBE’s batteries research service, Global light vehicle OE batteries market- forecasts to 2029