GM has an engine plant in what some might think an odd location in Eastern Europe, a place best known for paprika and inexpensive labour, but there’s more to Opel Hungary than one might first expect-like the fact that it’s one of the most productive engine plants in the world.
On the way from Budapest to Szentgotthárd (the home of Opel Hungary), the van I was in passed a gigantic suburban shopping centre on the side of the freeway. “Wow, IKEA,” I observed, surprised. For those that don’t know, IKEA is a Scandinavian furniture company that’s popular enough in the States to be satirized on The Simpsons, yet has such a limited number of stores that people drive great distances to shop in them: Detroit doesn’t have an IKEA. The closest one is in Chicago. But here I was in an Eastern European country that’s still identified as “formerly communist” in many travel guides and it has an IKEA.
The point is that Hungary is fundamentally as “Western” as the rest of Western Europe (and more “American” than a lot of it; I’d also seen plenty of Pizza Huts and Burger Kings). Despite this, my initial inherent American biases prevented me from considering a possibility that Hungarians take for granted. Why shouldn’t Hungary have an IKEA? (Actually, they have two.) But enough about IKEA. This story is about Opel Hungary, a very successful operation that manufactures with an efficiency that they take for granted, but might surprise some of us Americans.
Conventional wisdom says that automakers build factories in places like Hungary (or Mexico), because labor is very inexpensive. Conventional wisdom says that this cheap labor means low-tech, low investment operations. Conventional wisdom carries a “move along, nothing to see here” attitude. But in this case, conventional wisdom is wrong. Opel Hungary is a model facility-lean, agile, and well managed.
(And it’s not that far from IKEA.)
How well do you really know your competitors?
Access the most comprehensive Company Profiles on the market, powered by GlobalData. Save hours of research. Gain competitive edge.
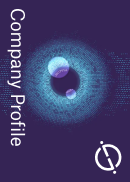
Thank you!
Your download email will arrive shortly
Not ready to buy yet? Download a free sample
We are confident about the unique quality of our Company Profiles. However, we want you to make the most beneficial decision for your business, so we offer a free sample that you can download by submitting the below form
By GlobalData Opel Hungary produces this 1.8-L
16-valve ECOTEC 4-cylinder
engine, among others.
Numbers
Engine production began at Opel Hungary in mid-1992; that year, the plant built just 20,500 engines; nothing to write home about. But by 1995, the plant had surpassed its scheduled capacity of 230,000. To further increase productivity, a continuously moving assembly line was introduced, and in 1996 Opel Hungary produced 310,000 engines. In 1997, a heavily automated agile cylinder head plant was added to the facility, building 135,000 heads in its first year. The next major change came in 1999, when a four-shift system was deployed in engine assembly, pushing production up to 511,800 engines. By this time, the cylinder head plant was producing 352,500 heads. The plant is currently building Opel’s 1.4-, 1.6- and 1.8-L 16-valve ECOTEC engines and heads and is both QS 9000 and ISO 140001 certified. Welcome to the big leagues.
Opel Hungary isn’t just an engine plant, however. From 1992-1999, it was “knock-down” assembling Opel Astras and Vectras-until those frequently changing European trade tariffs changed again and the assembly line went down. But this loss of business turned out to be a boon for the plant, as two significant new projects are now in the works. An Allison Transmission plant is being installed in the former paint shop area; this June, it will start producing 18,000 truck trannys per year. Next June, GM’s first continuously variable transmission (CVT) plant will begin operating in the former car assembly area. This CVT plant will supply GM vehicles worldwide, to the tune of 250,000/year.
One of the reasons Opel Hungary got this new transmission business comes from its reputation. In a recent independent study of engine plant productivity, Opel Hungary’s 2.64 hours/engine score ranked best in its class. However, there was also a little serendipity involved. Opel Hungary managing director Albert Lidauer happened to bump into an Allison exec at a GM leadership seminar, which led to the initial idea to locate the Allison plant in the Hungarian facility. (Will direct flights from Indianapolis to Budapest be far in the future?) While this is just idle speculation, I’m willing to bet that the Allison and GM honchos that had to sign off on this deal (and the CVT deal as well) were more impressed with Lidauer’s attitude and management practices than anything else.
Philosophy
Lidauer will fire off his four management principles like they’re tattooed on the back of his hand: (1) Focus on people; (2) Focus on quality; (3) Focus on core business; (4) Focus on lean manufacturing. While these aren’t revolutionary ideas, the big difference between hearing them come from Lidauer and hearing them bandied about by others is that Lidauer is absolutely believable. He doesn’t just mouth these ideas like buzzwords, but can point to direct examples of how they are implemented in his plant. As he explains, he wants Opel Hungary to be a “development center for new ideas.” Admittedly, he says, the inexpensive labour advantage will disappear-but when it does, he wants the success of the organization to continue.
Opel Hungary’s agile cylinder
head machining line includes 90
identical machining centres
organized in cells of five. The
floors of this area of the plant
were coated to make the surface
flat, thereby making it easier to
move and rearrange equipment.
One of the most significant things that Opel Hungary did was when it moved engine production to a 24-hour, 7-day schedule last year. This “four-shift” production means that employees now have a great degree of flexibility in their schedules. It also means that Opel Hungary doesn’t pay any overtime. Lidauer claims that knowing well in advance when they have time off means that employees can plan their lives better. He claims this is preferable to the old way, which frequently resulted in employees being told on Friday that they had to work mandatory overtime on Saturday.
Of course, this move to four-shift production means that there’s no time for catch-up on the weekends, which means that machines can’t be allowed to break down. “Traditional” maintenance at Opel Hungary had involved 50% scheduled maintenance and 50% reactive maintenance. Now they run two maintenance shifts per week and 100% of it is scheduled. (Yes, they still fix things when they break.)
Of particular interest is that Opel Hungary has outsourced central maintenance and tool management, as they have been deemed non-core businesses. With respect to tool management, Lidauer says that he is not concerned about his competitors learning any of Opel Hungary’s secrets; as he points out, this type of information flows in both directions. Many other operations have been outsourced as well: fluid management, waste management, rail service, payroll, mail service, security, training, cafeteria, travel agency, bank and pool car management . . . Material handling will be next, Lidauer says.
Opel Hungary only has four job classifications and there are no distinctions made between hourly and salaried workers. If required, engineers work on the line. Lidauer practices an “open door” management policy, and does not allow “status symbols” (big offices, perks, etc.) for management. By removing as much of the bureaucracy from management as possible, communication is much improved and things get done faster and better.
Of course, it helps to start with good people. Opel Hungary benchmarks companies in all industries to makes sure that its pay and benefits are among the best, thereby attracting and retaining only the best workers. Over half of the workforce at Opel Hungary comes from a technical high school or has a university education. Once in the fold, continuous improvement is stressed through on-going training programs. All employees-including those in administration-are required to make at least 15 suggestions for operational improvements per year. Of these, over 90% are implemented. Some workers have contributed as many as 80 suggestions in a year.
Lean & Agile
While Opel Hungary takes great pride in its skill at managing things within its walls, sometimes it becomes necessary to fight management battles that extend further than Szentgotthárd. Further than Europe even. Sometimes as far as, say, Detroit. When it was decided that Opel Hungary would begin producing cylinder heads, for instance, there were a large number of people who had pre-decided that the new plant would machine them on a transfer system. Lidauer, however, wanted to employ an agile system of machining centres. This did not sit well with those who pointed to the 20-30% greater cost of machining centres. Without disclosing any further details, Lidauer explains that he made his business case and won. This was largely based on the fact that machining centres have a higher rate of up time than transfer lines. This means that fewer machines are needed to achieve the same level of production.
Opel Hungary uses visual
management techniques,
including the displays above
the line shown in this picture.
While you can’t see them here,
standardized work descriptions
are posted at each operator
station. Besides written
instructions, these include
pictures of the correct
procedure.
Once the decision was made, a fleet of 90 identical Hüller Hille machining centres was installed in cells of five and split into two lines of nine cells each. The system is completely flexible and produces nine different cylinder heads. Load and unload are fully automated, as are tool change and in-line process control. The heads share a common fixture to which they are attached with different adapters. The fixtures each contain a computer chip that uses a radio signal for tracking and data acquisition for quality purposes. Other quality control measures include two Leitz CMMs, one for each line, on which critical tolerances of test parts are measured, and a laser system to check torque values on bolts, based on how deeply they are recessed into the head.
Operators are responsible for fixing their own operational problems, as well as performing line-side TPM. Additionally, an on-the-floor “Kaizen shop” has tools to allow operators to make whatever small changes needed during production. The lines begin and end in the same location, so a single operator can both feed and destack the line. All of the operators are trained to monitor all of the stations and a single operator may handle as many as three cells.
The results of the program? In 1999, the agile system ran greater than 90% of the time and produced as many as 2,000 cylinder heads per day. Defect rates as high as 2,000 PPM at launch in 1997 dropped to 200 PPM in 1999; next year’s goal is just 50 PPM. The forecast also calls for hitting their capacity of 460,000 units in what will be their fourth year of production, just as the engine plant maximized initial capacity in four years. What then? Well, they’re still only running three shifts in the cylinder head plant and there are all those suggestions from the employees . . .
By Jeff Sabatini, Instigator.