Did you feel the earth move? Did you sense the shifting of the tectonic plates? The tsunami engulfing the whole of the world’s motor industry? I did when I read an interview with Burkhard Göschel on the Autosport.com website, writes Karl Ludvigsen.
Though the bespectacled Professor has just stepped down from his post as management-board member at BMW for development and purchasing, he remains a senior advisor to the board. Thus when he speaks we can consider his views authoritative.
‘What we are doing in the car industry,’ he said, ‘and you can see this at BMW, is that we are shifting over to turbocharged engines with a high point of efficiency. In the future we will have downsized engines with turbochargers.’
This is a shift of galactic proportions on the part of the automaker that has earned the reputation of thinking more about engines than any other. Hitherto BMW has been a staunch and committed advocate of the naturally aspirated engine, favoured for its smooth and confident throttle response. The Munich firm has been a leader in advancing the state of the unblown-engine art with its masterful in-line sixes, precise foundry techniques, Vanos variable valve timing and innovative Valvetronic power control. Now BMW has taken up the technology it has hitherto scorned, the turbocharged engine, and placed it at the heart of its future programmes.
Of course BMW hasn’t altogether ignored the turbo. Its previous flirtations with exhaust-driven blowers for its road cars were the 2002 Turbo of 1974 and then turbo sixes for the 7 Series from 1980 to ’86, at a time when it hadn’t yet perfected its eights and twelves and needed more power to compete with Mercedes-Benz. From 1980 to 1987 BMW was a supplier of turbocharged engines to Formula 1 teams. First
raced in 1982, their potent four — producing up to 1,200 bhp for qualifying — took Brazilian Nelson Piquet to his world championship in 1983. They also powered entries from Benetton and Arrows.
How well do you really know your competitors?
Access the most comprehensive Company Profiles on the market, powered by GlobalData. Save hours of research. Gain competitive edge.
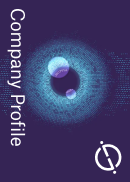
Thank you!
Your download email will arrive shortly
Not ready to buy yet? Download a free sample
We are confident about the unique quality of our Company Profiles. However, we want you to make the most beneficial decision for your business, so we offer a free sample that you can download by submitting the below form
By GlobalDataNone of this prepared us for the total commitment of BMW to smaller-capacity turbo engines across the board for its future production models. Burkhard Göschel explained the rationale: ‘As everyone already knows the engines are losing two-thirds of the energy by heat. One of the ideas is: how do we bring that back?’ BMW has concluded that the exploitation of exhaust-gas energy to drive a centrifugal compressor is perhaps the best way to make use of heat energy that’s otherwise wasted.
BMW is confident that this new approach will appeal to its customers. After decades of steadily increasing power, acceleration and speed, a certain plateau has been reached. That’s the feedback that BMW is getting from some of its markets. ‘Some customers are saying that the performance is enough,’ said Klaus Borgmann, senior vice president for engine and gearbox development. ‘They are downsizing, so we are focusing on fuel consumption. They want performance and fuel economy.’
Poster boy for this revolution in Bavaria is the twin-turbocharged six that powers BMW’s latest 3 Series Coupe. Punching out 306 bhp at 5,800 rpm from 2,979 cc (89.6 x 84.0 mm), the Coupe’s top-ranked six delivers 295 lb-ft of torque — a proud 400 Nm — all the way from 1,300 to 5,000 rpm. To get comparable output from a normally aspirated eight, says BMW, you’d need one displacing 4.0 litres and weighing 155 pounds more than the turbo-six’s 412 pounds.
The new engine’s high output means that it needs a more rugged block than BMW’s less-potent sixes, which is why it’s cast entirely of aluminium instead of the composite magnesium/aluminium that BMW has pioneered. The pistons run directly in its high-silicon-alloy bores. Uniquely in this 3.0-litre six the bores are 1.6 mm bigger and the stroke 1.0 mm shorter. The result is that with its cylinder centres spaced at 91.0 mm there’s only 1.4 mm of solid aluminium between adjacent bores. This is a tribute to the precision of BMW’s foundry methods that suggests technology transfer from its Formula 1 engine program.
Fabricated of high-nickel steel sheet, two three-cylinder manifolds pipe exhaust straight into the close-placed turbines of tiny Mitsubishi-IHI turbochargers. Having two chargers means that each can be very small, which gives low rotary inertia for excellent throttle response. This is a prerequisite for BMW, which is proud of the eager attack of its engines. The mini-turbos rev to an astonishing 201,000 rpm, delivering wastegate-controlled boost to a maximum of 8.5 psi.
The turbos are so close to the exhaust valves that IHI had to develop a special ultra-high-temperature alloy for their turbine wheels. Primary catalysts are close by in the downstream exhaust flow. Pressure air is piped forward and through an intercooler to the inlet manifolding on the six’s left-hand side. Good economy when the engine is off-boost is assured by its base 10.2:1 compression ratio.
Fuel enters the Coupe’s turbo-six through tiny nozzles set into the centres of its four-valve combustion chambers, a scant 10 mm from the spark plug. This is the business end of a fuel injector developed jointly with Siemens. Instead of old-fashioned solenoids to operate its spray valve each injector contains a crystal-like ceramic that reacts to electricity by deforming slightly, just enough to open the valve to release 200 atmospheres of fuel pressure.
The effect, called “piezo-electric” after the classical Greek word for pressure, works both ways: squeezing such a crystal generates electricity. In this case a peizo-responsive material like lead zirconium titanate is used to control the injector, opening only 0.03 mm when electrically triggered as many as three times if necessary during every power stroke. Extremely precise, the injector forms a fine conical spray of fuel in the combustion chamber, burning with high efficiency.
The new injection system lends itself to a lean-burn operation mode. Installed experimentally in a naturally aspirated in-line six of 2,996 cc (88.0 x 85.0 mm), the result has been a dramatic 10 percent reduction of fuel use on the EU’s test cycle. Consumption in relaxed driving on normal roads is niggardly, easily in excess of 200 miles per gallon. ‘We have never seen fuel economy like that on the road before,’ said Klaus Borgmann. ‘We expect real advantages against the competition.’
In a test drive in a 3 Series sedan over a variety of roads on the north side of Munich the six’s air/fuel ratio ranged between Lambda=2.0 and 2.5 when full power wasn’t demanded, inhaling more than twice the air of a standard mixture. The system delivers up to Lambda=3.0, a true lean-burn engine. Yet the six retained typical BMW smoothness and free-revving characteristics, producing 272 bhp at 6,750 rpm and 232 lb-ft of torque at 2,750 rpm.
After the lean-burn engine’s control system is optimised it will be introduced in ‘relatively high volumes’ in a new BMW model. Sales will initially be in Europe because the system needs a catalyst to cope with its high generation of oxides of nitrogen (NOx) at Lambda=1.1-1.2. Such catalysts are degraded by sulphur, which is still present in petrol outside Europe. The engine will run on fuel with sulphur, but its NOx catalyst will need more frequent regeneration.
Next step, say BMW’s engine men, will be to marry the twin-turbo and lean-burn technologies. This could bring them even closer to the diesel’s low fuel consumption. A key difference is that the gasoline engine is boosted at lower pressure, which is why it doesn’t require a two-stage turbo system like that recently introduced by BMW for a diesel six. The latter is boosted at up to two atmospheres, almost 30 psi, which means that it benefits from the higher efficiency of a two-stage layout. Series instead of parallel blowers don’t yield significant efficiency benefits at lower boost pressures.
The concept of boosted small engines won’t be unique to BMW. Information exchanged at the monthly meetings among the engine designers of the German-owned auto companies means that they’ll all be heading in that direction. Audi has introduced a new four which in turbo form will be powering many future models. VW is pursuing its marriage of a turbo with a positive-displacement blower in a two-stage system to give optimum throttle response.
The bottom line? Paradise awaits for makers of turbochargers and suppliers of the high-temperature materials that such systems need. Will this be another instance where non-European suppliers benefit from the failure of indigenous producers to meet their industry’s demands? Let’s hope not.
– Karl Ludvigsen
Karl Ludvigsen is an award-winning author, historian and consultant who has worked in senior positions for GM, Fiat and Ford. In the 1980s and 1990s he ran the London-based motor-industry management consultancy, Ludvigsen Associates. He is currently an independent consultant and the author of more than three dozen books about cars and the motor industry, including Creating the Customer-Driven Car Company