Renault has unveiled its long-awaited ‘€5,000 car’, and has revealed ambitious plans to build close to a million of the cars a year worldwide by the end of the decade. Mark Bursa takes a detailed look at the project.
The car, previously codenamed X90, is a four-door sedan based on the new Renault-Nissan B platform. It has been named Logan, and will be built initially at Renault subsidiary Dacia in Romania. It will be sold under both Dacia and Renault brands, depending on the market. Dacia will be used in Central and Eastern European markets as well as Turkey and North Africa, where the brand has traditionally been sold; in Russia, South America and the Middle East it would carry Renault badges. The car is homologated for Western Europe but there are no initial plans to sell it there.
On the face of it, the plan looks similar to Fiat’s ‘Project 178’ world car of the mid-1990s, which spawned a variety of vehicles including the Palio hatch, Siena sedan and Strada pick-up. But Renault executives claim there are key differences between the two. Firstly, the Logan is based on Renault’s latest technology – Palio used some componentry from the Uno. And secondly Logan will be cheaper – whereas Siena is seen as a premium Fiat in Central Europe, Logan will be the entry point for Dacia as soon as production of all old Dacia models ceases next year.
Renault Logan and Fiat Palio projects are similar
But really the two projects are similar. The biggest difference is timing – Renault has also got the timing right. Palio sales suffered because of the collapse of some of its key markets, especially in South America, in the late 1990s. Logan is being focused more heavily on Central and Eastern Europe, and with EU enlargement these markets are ripe for growth. And China in the 1990s was a largely stagnant market, not the rapidly growing powerhouse it has become over the past couple of years.
From the start, the X90 project was referred to as a “€5,000 car”. However, the promised €5,000 retail price will not be available when the car goes on sale in September – Renault is holding back the budget-priced base model until next year in order to avoid conflict with the current Dacia Solenza model, which will cease production in 2005. Initial Dacia Logans will be higher-specified models – the top priced model will cost around €8,000. And the €5,000 price tag will not be available outside Romania – import duties in neighbouring states have put paid to that.
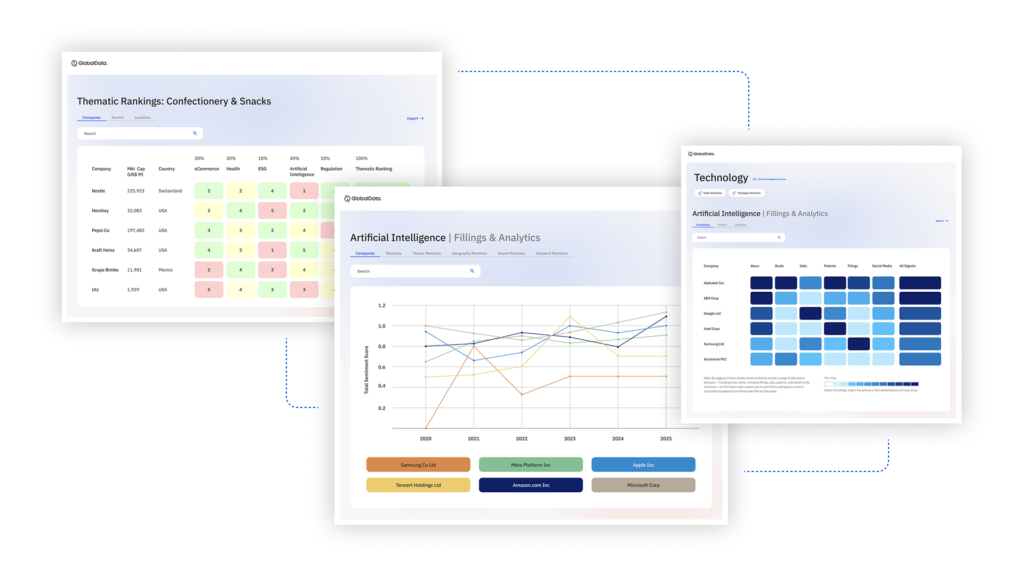
US Tariffs are shifting - will you react or anticipate?
Don’t let policy changes catch you off guard. Stay proactive with real-time data and expert analysis.
By GlobalDataNevertheless, Logan extends the reach of Renault’s product offering into the all-important lowest segment. In Poland, for example, Renault does not at present have a car that competes in lowest price bands that account for 30% of the local market.
Apart from Romania, Renault is eyeing five assembly sites for Logan. It plans to build the car from CKD kits in Russia, Morocco and Colombia, and is exploiting traditional strong French business relationships in the Middle East by planing a massive 300,000-unit joint-venture facility in Iran. And an agreement to build the car in China under a 50:50 JV with partner Dongfeng Motor is due to be signed in the next few weeks.
The car is part of a grand plan by Renault to increase worldwide sales to 4 million units a year by 2010 – a goal that could only be achieved through “vigorous expansion into new markets outside Western Europe”, according to Renault chairman Louis Schweitzer. His target is to sell 25% of Renault’s global annual production outside Western Europe.
Engineering challenge
The challenge for engineers at Renault’s Technocentre south of Paris, where the car was developed, was to build a car that was price-competitive against the kind of cars customarily on offer in emerging markets – Russian Ladas, Iranian Paykans – and Dacia’s own old Renault 12-derived models.
Logan uses as many existing components sub-sets as possible, while simplifying elements of design and minimising the numbers of parts. The dashboard, for example, is a one-piece moulding; the front suspension from Clio and the rear suspension is from the Modus. Many trim and interior parts are carried over from Solenza, a Dacia-designed car dating from the early 1990s but heavily re-engineered by Renault since it took over Dacia in 1999. Instrument panel, door handles, steering wheel and column switches come direct from Clio. Some parts, such as the air vents and gear lever knob, are from the Espace. Original Logan parts have been designed for simplicity – even the plastic rubbing strips on the outside of the doors are reversible, so the same part can be used on near and offside.
Third car for ‘B’ platform
Logan is the third car to be built on the Renault-Nissan Alliance’s B platform, following the Nissan Micra and just-launched Renault Modus. The Logan will be launched with a choice of K7 series eight-valve petrol engines: the 75hp 1.4 litre and 90hp 1.6 litre. Both engines are combined with the five-speed manual gearbox also used in the Laguna and Mégane.
The engines have been well proven in several Renault vehicles, and are still used in the Clio saloon and Kangoo van. A 65hp 1.5 dCi diesel option will be available in 2005, as well as a 107hp 1.6 litre 16-valve petrol unit. Part of the logic for using slightly older engines was their ability to run on fuel of widely differing quality. They have also been approved for use with 87-octane and 91-octane gasoline as well as 95-octane fuel. The engines comply with EU Euro 4 emissions standards and the body meets European standards for front and side impacts.
The B platform has been stretched dimensionally to the limit – the Logan is close to C-segment in terms of length (4,250mm), width (1,735mm) and height (1,525mm). The boot volume of 510 litres is claimed to be the best in the class. A right-hand drive version is planned as Renault wants to assemble Logan in South Africa, where Nissan has a plant.
From early 2007 other body styles will be launched on the same platform, including an estate, a small van and a pick-up. But there will be no hatchback version – with Clio, Modus and the forthcoming new Twingo, Renault believes another hatchback is not necessary. The Clio Symbol four-door sedan will continue to be built, however, and will be pitched as a more upscale vehicle than Logan.
Maintenance costs, a key criterion for car buyers in emerging markets, have been kept low. Service intervals have been made as long as possible – in some markets the oil, spark plugs and air filter are changed only every 30,000km. There was also a focus on simple, practical techniques for easy servicing. The headlamp bulbs can be easily reached from the engine compartment, so customers can change them themselves.
The heating system is the same one that will be used in other Renault B-segment vehicles, such as Modus. The single-part design approach, using simple pipework and short circuitry, ensures high mechanical reliability and helps to make savings on design costs without sacrificing thermal performance, which is among the best in the segment.
Electronic functions are grouped together in a central cabin unit based on the one used in Clio and Twingo. Logan has the same engine compartment as Clio, designed using the same interfaces so proven assembly procedures can be used.
The final development budget for the Logan was €360 million, a relatively low figure achieved through use of the “design to cost” method; use of carry-over parts to optimise reliability and manufacturing costs and the application of digital design. “The ‘design to cost’ method was introduced at Renault in 1992 with the Twingo project, and underwent a decisive development with the launch of the X90 project in 2000,” said engineering project manager Odile Panciatici.
Logan was a pilot project for using digital simulation in designing vehicles and production tooling, as well as for adjusting manufacturing processes. Calculating vibrations and testing acoustics on digital models helped designers predict noise levels in the vehicle without using a physical model. The advantage of using digital techniques, especially in defining and developing the body structure, is that costly prototypes of vehicles and tooling did not have to be built, so many physical stages in the design process were eliminated. The total cost saving is estimated at about €20m.
Industrial investment
As well as the cost of developing the car itself, the Logan is part of a major industrial investment in Renault’s global manufacturing capacity. The company may have spent €360m on the car, but is spending far more on production facilities – €205m in Romania; €230m in Russia; €22m in Morocco; €16m in Colombia, and a massive €300m in Iran. The China plan is likely to become part of the $2bn JV between Dongfeng and Nissan.
Schweitzer said Dacia’s Pitesti plant had been completely renovated – “only the exterior walls are the same”. Certainly the plant had suffered from neglect since the fall of the Ceaucescu regime – a visit in 2001 revealed a sprawling, gloomy, low-tech complex, with thick layers of grease and grime on the factory floor and dark industrial deposits on the roof cutting out natural light to the shop floor.
However, the renovation had started, and the cleaned-up parts of the plant, such as the engine line, showed the potential of the plant, built originally in the mid-60s to make the Renault 8. Many powertrain parts are now machined at the site, such as the cylinder head cover, mounting brackets, engine mountings and oil sump.
Suppliers have been heavily involved in the programme: altogether the Logan project uses 143 first-tier suppliers, 43 of which are located in Romania, nine in Turkey, five in Eastern and Central Europe and 10 in Western Europe. Eight Tier 1 suppliers have located facilities at Pitesti in existing former Dacia buildings. These are: Valeo, Johnson Controls, Faurecia, Euro APS (a joint venture between ADPlastic and Simolder), ACI, Piroux, Iri, MCI Ingénierie and Metal Impex. In order to improve the capacity of Dacia’s partners, the number of suppliers has been cut from 200 for the Dacia Berlina (Renault 12), which will be phased out towards the end of 2004, to 143 for Logan.
Schweitzer said he expected the business to turn in a profit next year. It will build 200,000 complete Logans and 150,000 CKD kits. The Pitesti site covers about 2.9m square metres, including over 623,000sq m of buildings. Most of the investment was allocated to updating production facilities at the Pitesti site.
Six stamping lines have been upgraded, with 30 presses (five per line) replaced or renovated. Some of the “new” stamping lines use reconditioned machinery from Renault’s Sandouville plant, itself upgraded three years ago for the new Laguna, Vel Satis and Espace. The body-in-white assembly shop has been totally restructured and flows rationalised, taking account of very competitive labour costs which put the emphasis on manual operations – the workshop has only one robot.
In the powertrain department, the aluminium foundry and machining shop for powertrain components have been completely modernised. This has made it possible to transfer assembly of the 1.9-litre diesel engine from the Cléon plant, where it was built until the end of 2003, to Pitesti.
New facilities for surface treatment and cataphoresis have been installed in the paint shop. Ovens have been built to the same standards as those at Renault’s most modern plants. Added together, the improvements brought the plant’s capacity up to 32 vehicles an hour by 2004. An increase the number of shifts from two to three will take place in 2005, depending on demand for Logan.
Satellite assembly plants will be designed to have highly competitive costs. Renault has decided to take a labour-intensive approach for assembly, with low automation levels. Because of the mainly manual assembly process, the engineers have tried to optimize the use of materials and have not developed any large body panels. They have also managed to avoid using laser butt welding technology for sheet metal assembly.
The plants that will produce Logan will use the Renault Production System (SPR) – itself based on Nissan’s approach to production. This system, introduced in 1998, brings together everyone involved in the production process – purchasers/suppliers, logistics experts, engineers and manufacturers – to focus on common targets and procedures. One aspect has been the setting up of “dexterity training” or “patterning”, which helps operators to perform movements more easily and effectively.
SPR makes the workstation the focal point of industrial organisation and standardises the movements made at each workstation in great detail. This approach optimises plant productivity, product quality and workstation ergonomics.
Renault is investing €230m to make Logan in Russia from mid-2005. The production unit, to be installed in the Moscow plant of Avtoframos, a subsidiary jointly owned by Renault and Moscow City Authorities, will have capacity of 60,000 vehicles per year.
The investment involves setting up production lines and developing the dealer network and support functions. With body-in-white, paint and assembly workshops, the Moscow production site will employ up to 2,000 people when operating at full capacity. It will gradually bring in local subcontractors. The plant is currently handling final assembly of Clio Symbol saloon at the rate of eight vehicles per day, and this will continue until Logan goes into production.
An even larger investment of €300m is being made in Iran, a new market for Renault but one where French-band cars are commonplace, with Peugeot assembling 405 and 205 models there. Renault and IDRO (Industrial Development & Renovation Organization – the Iranian public body responsible for the automobile industry) set up a joint company, Renault Pars, in May 2004.
Iran’s two leading automakers, Iran Khodro and Saipa, will produce and market Logan from 2006, with initial capacity of 300,000 units. Some of this production is scheduled for export. The vehicles will be assembled from sets of imported parts and components supplied locally by Renault Pars. The company will be responsible for all the operational functions of an automaker, including engineering, quality, purchasing and logistics, as well as coordinating sales policy, marketing and aftersales.
Logan will be distributed under the Renault brand by Iran Khodro and Saipa’s dealer networks. Iran, with a population of 68 million, has seen its car market put on a spurt of growth in the past three years. In 2003 it totaled 700,000 passenger cars plus LCVs.
Other investments include €22m to make Logan at the Somaca plant in Morocco from the second half of 2005. Production of 30,000 vehicles a year is envisaged, with some going for export; and €16m in Sofasa of Colombia, which assembles LCVs for Toyota and Renault Twingo, Clio and Mégane passenger cars). Sofasa also exports vehicles to other Andean Pact countries, and to a few Central American countries for Renault.
Perhaps most important for Renault, an announcement for Logan production in China is expected later this year. This will be a joint venture with Dongfeng Motor Corp, which set up a wide-ranging $2bn JV with Nissan last year.
According to sources in China, the Dongfeng-Renault JV will be set up in Shenzhen, in the Guangdong province of southern China, rather than close to Dongfeng’s base in the central Hubei Province. “Both parties will have a 50% stake in the joint venture with a planned annual capacity of 300,000 Renault cars,” reported China Daily. No official details have been revealed, and it is unclear whether the 300,000 units would all be Logan-derived cars or include other models.
After a false start a decade ago, the move is further evidence that Renault is getting its act together in China, both independently and via Nissan, in which it has a 44% stake. In January, Dongfeng and Renault agreed to create a JV based on the former’s affiliate in southern China’s Guangxi Zhuang Autonomous Region to make Renault trucks. Dongfeng also has diesel engine JVs with both Renault and Nissan in China.
Renault set up a JV in 1994 in Hubei with another Chinese partner to assemble its Trafic minibus. But the partnership has almost come to a standstill as a result of sluggish sales over the past years. Renault and De’long, an industrial and investment firm registered in Shanghai, were in talks last year about attempting to revive the venture by introducing Renault’s Kangoo light van and MPV models. De’long was also pitching for the Logan project, but Dongfeng is a much more powerful automotive force – one of the ‘Big Three’ Chinese auto makers that are set to dominate the rapidly expanding Chinese market.
Renault/Dacia Logan -production capacity | |
Romania | 200,000 |
Russia | 60,000 |
Colombia | 44,000 |
Morocco | 30,000 |
Iran | 300,000 |
China | 300,000* |
South Africa | 20,000* |
Total | 994,000 |
* to be confirmed