Not satisfied with theoretical exercises, BMW Technik set out to see whether or not drive-by-wire systems lived up to their promise. the best way to determine this, it reasoned, was to build a drivable technology demonstrator. six years later, the Z22 is still teaching the company about the promise inherent in electronic vehicle control. By Christopher A. Sawyer, Executive Editor, Automotive Design and Production
In 1995, BMW Technik, the automaker’s in-house technology division, began work on project Z22. The idea behind it was to determine which technologies–from carbon fiber structures to drive-by-wire systems–were feasible, the approximate time it would take to bring them to production-ready status, and to determine the steps necessary to ensure the technologies were ready for prime time. Z22 didn’t become visible to the outside world until 2000.
Speaking about his area of interest, Dr. Jürgen Guldner, project manager, Drive-By-Wire Systems, says, “Initially, it was thought that we should see if it was feasible to electronically control a vehicle. To do that, we needed to see what had to be changed in the vehicle infrastructure, especially in terms of power generation, storage, and supply; data communications; sensors; and actuators.”
Protocol Search
Drive-by-wire systems must interact seamlessly if they are to perform as expected, so Guldner says a common data communications protocol is of paramount importance. Researchers at the Vienna University of Technology have created a Time Triggered Protocol (TTP), which follows activities based on time: each of the by-wire nodes on the in-vehicle network share a common time reference and is given a slice of time (divided into milliseconds) so that there is no overlap.
However, a group consisting of BMW, DaimlerChrysler, Phillips, Bosch, and Motorola are, Guldner says, becoming increasingly interested in Flexray, an event-triggered protocol. He observes, “It looks like the industry is rapidly converging on the Flexray protocol,” both in Europe and North America.
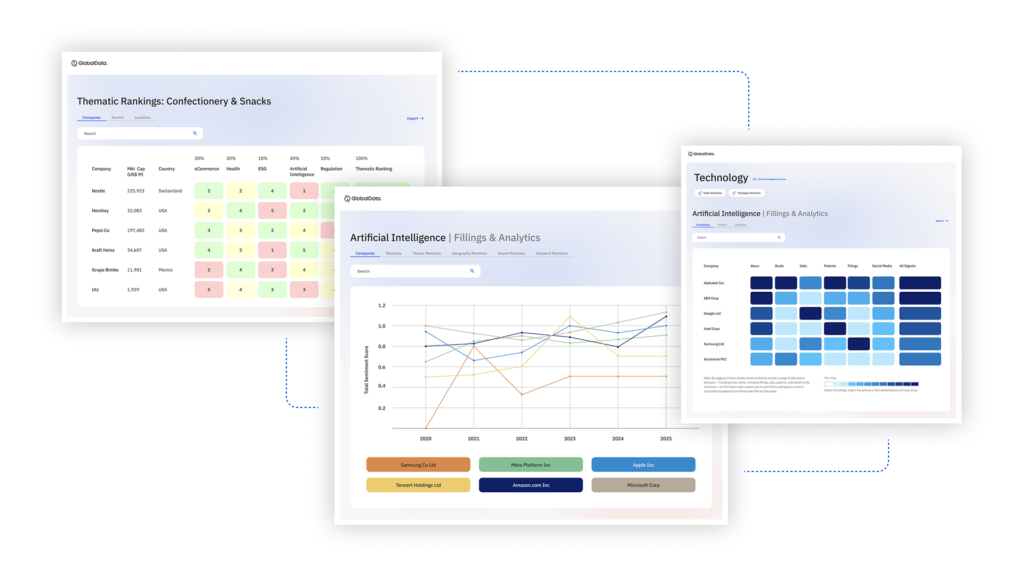
US Tariffs are shifting - will you react or anticipate?
Don’t let policy changes catch you off guard. Stay proactive with real-time data and expert analysis.
By GlobalDataWorking for Reuse
It’s also convinced some components, and the basic software, will have multiple uses. “The actuator will need to be available in different sizes,” says Guldner, “but it’s not a big deal to put a bigger motor in place to make it vehicle-specific, though the motor itself will probably be off-the-shelf.” So while Guldner doesn’t see common actuators stretching from BMW’s yet-to-be-built 1 Series small car to the 7 Series luxury sedan, he expects a reasonable overlap for the rest of the system. “I can see using common pieces within the 1 Series and 3 Series, the off-road vehicles, and the 5 Series and 7 Series,” he remarks. “At least, that’s what we’re shooting for.”
In addition, automakers are working to standardize the interface between sensors and the vehicle. “In cars right now,” says Guldner, “we have three yaw rate sensors that measure practically the same thing. One is used for navigation, another feeds the stability system, and the third has various uses.” Instead of using sensors that are system-specific, Guldner says the plan is to create sensors that, while a little more expensive, cover the complete range of measurement. “We might still want two sensors for redundancy,” he says, “but definitely not three.”
In Action
“The steer-by-wire system on the Z22 was my area of responsibility,” notes Guldner, “and we measured the forces through the tie rods, which gave us a pretty accurate picture of what was happening at the contact patch.” This information was used to control the torque from the electric motor, and replicate the feel of a purely mechanical steering system. Work is continuing on this system to filter out the extraneous tactile information.
“In a mechanical system,” says Guldner, “you either have good feedback–you feel everything–or you have poor feedback. The truth, however, lies somewhere in the middle.” For example, when a tire comes close to its handling limit, the torque felt through the steering wheel decreases by an amount too small for most drivers to detect. Only when the tires begin to squeal and the amount of steering lock increases, do most drivers begin to take notice.
“This physical phenomena is suppressed by the hydraulic assist in a conventional system,” states Guldner, “but we can enhance it electronically and amplify the effect at the steering wheel.” Should the driver still add, or subtract, too much steering lock for the situation, the steer-by-wire system would change the angle of the front wheels based on information from the vehicle stability system, and independent of the driver’s input.
“By tying into the other systems, you can cause the vehicle to respond much more quickly, and draw on a combination of systems to react to the situation,” he says. “It’s much like the way stability systems work today, except that you can draw on all of the vehicle’s dynamic control systems to provide the safest, most efficient course of action.”
In addition, Guldner expects drive-by-wire to provide features and functions not possible with conventional systems. One example he gives is a speed-dependent variable ratio steering ratio. At low speeds the steering wheel would be easy to turn, and small inputs would create large changes in the angles of the front wheels. Parallel parking could, for example, take as little as 20°º of wheel movement in either direction. As road speed increases, the relationship between input and response would trend toward conventional values. “With an integrated system,” says Guldner, “you can create a very agile, very responsive vehicle–even if the vehicle is a large one. So your limousine can feel like a sports car.”
Then again, you might want to modify the pedal box in order to reduce foot and leg injuries. “If we don’t need the vacuum booster right behind the pedal, and the pedal doesn’t need to be where it is today,” Guldner points out, “the pedal’s length of travel can be lessened significantly. It becomes a variable-output switch.” In addition, he suggests it would be possible to retract the steering wheel (remember, no column) in an accident, while adjusting the force of the airbag. “The opportunities are there,” he says.
Building on the Advantage
Though Z22 was designed to show how a full drive-by-wire system would work, this three-dimensional concept also has altered the way BMW engineers look at the production process. “Because steer-by-wire systems will not have a steering column, this will not be the first item to go in once the body and chassis go together,” Guldner explains. “Up until now it has been one of the determining factors in determining when this merger happens. Now we may be able to keep these sections apart longer and bring them together when they are nearly complete.”
The steering wheel and column will become part of the instrument panel, needing no more than a quick mating of connectors to make the union complete. The steering actuators, on the other hand, will be added to the body after the engine is installed, or be included in a rolling chassis that includes the powertrain, wheel assemblies (brakes, axles, dampers, etc.), and other underbody components. Either way, a quick electrical connection would be all that is necessary to enable a fully tested system.
“We haven’t finalized how much this production method might save us,” states Guldner, “or exactly what we might do differently in production, but we see a big chance to simplify production and greatly extend the phase where major systems and assemblies run down the line in parallel.” BMW feels this will increase the value-added work, lower total production time, and reduce production costs when viewed on a systems basis.
It Takes Time
Despite all of the apparent advantages, Guldner says BMW will not move from conventional to fully electronic systems overnight. “For safety reasons,” he explains, “we have decided to follow a step-by-step procedure when it comes to drive-by-wire systems.” Though BMW has a fully electronic throttle-by-wire system in production, the next generation of the company’s vehicles will test the waters with hybrid electro-mechanical systems.
The first is a conventional steering system enhanced through the addition of a planetary gearbox between the steering wheel and road wheels. A small electric motor adjusts steering angle on demand, or in response to commands from the vehicle stability system. If the system fails, the conventional steering connection remains.
The second is an electro-hydraulic braking system. “We will be controlling the hydraulic actuator through electronics because we believe that there are advantages in the upper ranges to this type of system,” says Guldner. He also states that in smaller vehicles like the 1 Series and 3 Series, direct electronic brake actuation might be the preferred technology, but with a big caveat: “We will need at least one level of redundancy for sensors and computation with a fully electronic system. It’s similar to the aerospace model,” he deadpans, “but without the seven layers necessary to get a stricken plane across the ocean.” In limp-home mode the trip may be slower, but “it should be no less safe.”
“This is a conservative industry,” he says, “that will not go by-wire overnight. But we will get there.”
Driving-By-Wire
SKF’s Filo (Italian for “wire”) boasts a Bertone body, an Opel Zafira drivetrain, full drive-by-wire systems, and was built in 12 months. Though best known for its bearings, SKF avionics and aerospace arm in Italy provided the by-wire expertise necessary to make the Filo a reality.
Working with Brembo on the brake-by-wire system, and alone on the steer-, clutch-, and shift-by-wire, SKF set out to produce a pure drive-by-wire vehicle that showcased the advantages of this technology. As a result, the controls are a bit unusual, and the interior of the subcompact four-door is huge.
Filippo Zingariello, vice president of SKF’s Drive-By-Wire business unit, says the technology allowed Bertone to rethink the vehicle’s architecture. “By eliminating the steering column, or the need for a conventional set of pedals, we could place all of the driving controls on the steering wheel,” he says. “That meant we could have right- or left-hand drive in the same vehicle by mounting the wheel on a central arm that moves in an arc from one side to the other.
|
It also meant that the throttle–two rotating grips on either end of the wheel–and brakes–activated by squeezing the grips while rolling off the gas–would be a bit awkward to use. That’s why the wheel rotates a maximum of 20º in either direction, which makes the Filo a bit skittish at first glance.
Moving off is fairly straightforward: press the “start” button, select first gear via the “+/-” button on the upper right of the wheel, roll on the throttle, and wait for the clutch to grab. Steering, however, is something else entirely. Turn the wheel a small amount–and I do mean small–and the Filo darts in the chosen direction. Then it darts back as you correct. After a series of left-right feints, everything calms down. In a matter of feet, the car is tracking true, and turns come with ease. Braking takes a strong squeeze.
As a technology demonstrator, the Filo is rough but impressive. Like all prototypes, it’s far from production ready, but it shows the promise its makers intended.