Gary Hebert is an attorney with McGlinchey Stafford PLLC, a US-based commercial law firm. In this guest article, he describes the legal framework and the process for building a defence in product liability matters in the US.
Automotive product liability litigation in the US is big business. Plaintiffs’ lawyers typically take as their fee a third or more of any recovery, plus expenses. As such, plaintiffs’ lawyers tend to be highly motivated and, in many instances, quite sophisticated in the relevant fields. This article provides an overview of the process for building a foundation for a cost-effective and successful defence for product liability matters.
Product liability theories
Product liability lawsuits are typically governed by the law of the US state where the accident occurred. Manufacturers from other countries should not assume that the law of their own country will govern.
The applicable law varies from state to state, but the variances largely fall within known parameters. There are four primary product liability theories. These theories are not mutually exclusive, so that a given plaintiff may assert as many theories as he thinks viable.
The first theory relates to manufacturing defect claims, also known as “mis-manufacture” claims. Mis-manufacture claims focus on errors in the manufacturing process that result in one product, or perhaps a batch of products, that are alleged to be defective because they do not conform to the design. For example, a plaintiff seeking to prove a defect in a chair under this theory would claim that just his chair, or maybe a finite number of chairs, is defective because it failed to conform to the manufacturer’s design specifications. Claims of this type typically would not allege that every chair produced by the manufacturer was defective.
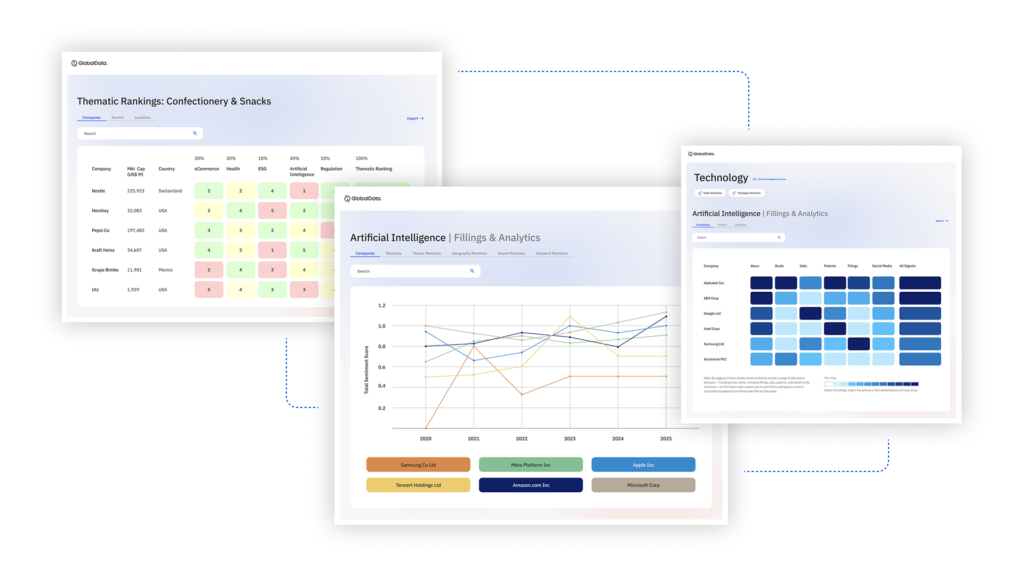
US Tariffs are shifting - will you react or anticipate?
Don’t let policy changes catch you off guard. Stay proactive with real-time data and expert analysis.
By GlobalDataThe second, and most expensive, theory to defend concerns design defect claims. Because these claims focus on all products of a given design, these suits usually cover a far greater number of products than mis-manufacture claims. With more units implicated, the economic risk to the manufacturer is magnified.
Many states require plaintiffs pursuing design defect claims to identify an alternative design that is capable of performing the same task without substantially detracting from the product’s utility or substantially increasing the risk to others. For example, an automobile passenger injured in a massive rear impact that caused his vehicle to burst into flames may claim that the fire would not have occurred if the fuel tank had been located elsewhere. But under the law, he must identify a feasible alternative location; simply claiming that the location of the tank resulted in the fire is not enough.
Design defect claims are the most expensive to defend for a number of reasons. To start with, manufacturers have employed teams of bright, hard-working engineers to develop their designs, and these engineers have likely considered (and rejected) many alternative designs, including the alternative design urged by the plaintiff. For this reason, manufacturers and designers typically believe that their design is superior to others, and are willing to go to great lengths to defend their design. Equally important, however, is the consequence of suffering even a single adverse verdict on a design claim. Because a design claim necessarily implicates every product incorporating a similar design, a single loss can be devastating to a particular model or even an entire product line. For these reasons and others, manufacturers are often willing to employ significant resources to defend design claims.
The third theory that may support a product liability claim involves allegations of inadequate warnings or instructions. A plaintiff may assert that a different warning or instruction would have (a) led him not to use the product or (b) caused him to use the product in a different way that would have reduced or eliminated the harm that occurred.
The fourth and final theory concerns claims that a manufacturer has violated some express warranty that accompanied the product. A claim of this type might allege that a chair designed and warranted to support up to 500 pounds failed when subjected to a 150-pound load.
Developing an effective defence through investigation
Developing an informed defence should start as soon as possible after an accident occurs. Securing the evidence and learning as much as possible about the occurrence – and the product – forms the basis of an effective defence.
Preparing an informed defence requires close coordination with the lawyer who will be defending the product at trial. When possible, the manufacturer should identify one in-house employee or executive who will be most closely involved in assisting outside counsel. This in-house liaison need not be expert on all issues relevant to the product or the claims, but the liaison must be able to command the attention of those company employees who have the technical knowledge and experience to develop the defence and to locate all potential evidence within the company. The appropriate liaison should be effective not only in assisting counsel, but also should be capable of responding to the American court if questions arise concerning the manufacturer’s processes for preserving and collecting materials and information that may be relevant to the lawsuit. American Courts are empowered to impose sanctions on a defendant who fails to respond adequately to requests for materials and information, even though some requests may seem unreasonably intrusive to a manufacturer not accustomed to discovery procedures used in American Courts.
1. Documents
American courts require that defendants (and potential defendants) take steps to preserve evidence as soon as a reasonable expectation of a lawsuit arises. A decision to take no action until a suit is filed is often imprudent. Evidence that should be secured includes all potentially relevant evidence in the company’s control, both hard copy (e.g., drawings, manufacturing records, etc.) and electronically stored information (e.g., emails, draft documents, Word documents, etc.). US Courts expect specific, concrete steps to have been taken to preserve the potentially relevant evidence. US Courts may be especially vigilant about the preservation of electronically stored information, known as “ESI.”
In today’s world, ESI includes not only documents and drawings that form the substance of electronic files; ESI also includes “metadata,” that is, information that is embedded in many electronic files. Metadata, which is often generated and stored with no affirmative action by the user, includes such information as the creator of the document, the date on which it was created, and the dates and creators of various edits. The capture and review of all potentially relevant ESI frequently requires the services of an expert in the field who can assist with gathering and processing the ESI and then be available to testify concerning the methods used to ensure that appropriate procedures were employed at every step.
2. Witnesses
With the close cooperation of the company liaison assigned to assist, key witnesses within the company should be identified and interviewed. Depending on the issues involved, the list of key witnesses may be as small as 10 or 12 people or it may involve many individuals.
Interviews of company employees will serve two purposes: (a) facts of the case and potential defences will be developed and (b) materials and information that must be preserved will be identified. To ensure that all potentially relevant ESI is identified for preservation, a representative of the manufacturer’s IT group should also be present. Often, the IT representative will have the background knowledge necessary to discuss databases, prior versions of databases, back-up methods and server locations that outside counsel cannot know going in.[1]
Working with the in-house liaison, outside counsel should develop a thorough outline of topics relevant to the accident, the product and the allegations made or expected. A thorough outline will ensure that the interview process is meaningful and efficient.
If the issues and the potential verdict range justify the expense, face-to-face interviews of key personnel are preferred. The lawyer attending the interviews should take detailed notes, both to preserve the attorney-client privilege that is widely recognised in the US and to inform later strategy discussions with the client.
Conclusions
Automotive product liability litigation in the United States often involves substantial risk for the manufacturer. Employing tested processes to identify, preserve and collect relevant data and to interview key witnesses will inform the foundation needed to develop and refine defence theories for trial. To succeed, the process must be developed in close cooperation between the manufacturer and outside counsel.
[1] Although beyond the scope of this article, careful attention must be given to the European Privacy Laws, which are not identical across Europe. Workers’Agreements should also be considered.
Gary Hebert is an attorney with McGlinchey Stafford PLLC. He practices primarily in the area of products liability defence, and he regularly represents foreign and domestic manufacturers in the automotive, machinery, medical and consumer products industries. He can be reached via email at ghebert@mcglinchey.com.