Back to the late 1990s, the auto industry had great expectations for gasoline direct injection (GDI) systems. The technology was heralded as the panacea for fuel economy and emissions, with a potential 20% improvement in both compared to conventional gasoline engines. At the time, manufacturers predicted that GDI engines would represent 25% of the total European engine market by 2004. But where are the results? Matthew Beecham reports.
“It seems that GDI has been the victim of some over zealous predictions and the customer realised benefits have fallen short of the expectations of many,” said Mark Garrett, director of gasoline engines for Ricardo. “Some of this is the inevitable compromises required to manufacture a durable consistent product and the other is that fuel economy is heavily influenced by driving style. GDI will continue to be a weapon in the technology armoury of the OEMs in their fight to reduce CO2, but its application will be less widespread in stratified form than originally predicted.”
Gasoline engine experts also believe that the current downsizing trend and the use of boosted engines in Europe will increase the demand for direct injection. By 2010, Ricardo expects to see 15% of gasoline engines in Europe. But that’s woefully short of the initial predictions made in the late 1990s. So what is holding back progress of GDI? “GDI systems are inherently more expensive than PFI systems and manufacturers must find some way to recover this incremental piece cost,” adds Garrett. “It is hard to convince gasoline customers that fuel economy is worth paying extra for unless it is accompanied by performance gains. Field results from lean aftertreatment systems have been poor, leading to high warranty and low customer satisfaction in Europe. Lean NOx trap technology, NOx sensor costs and fuel quality all need to improve for lean aftertreatment to be seen as comparable to today’s stoichiometric aftertreatment.”
So are we likely to see more applications of cheaper, homogeneous GDI technology in smaller engines? Ricardo believes that such homogeneous applications of GDI will be dominant over the next five years and will become more closely associated with boosting (turbo or supercharged) to achieve high levels of engine capacity downsizing. Mark Garrett said “The target for this is naturally reduced CO2 emissions and GDI technology is a natural partner to boosting due to the injection flexibility and octane requirement benefits it brings.”
Denso is waiting to see which type of GDI — lean burn GDI and stoichiometric — will be most acceptable by the carmakers. Masahiko Miyaki, managing officer of Denso Corp, said: “In terms of emissions, stoichiometric GDI can reduce emissions to the same level as port injection. Although the lean-burn GDI has a higher potential to reduce fuel consumption, it will need an improved after-treatment system to meet future strict emission regulations. We will carefully watch which system will be employed by car manufacturers.”
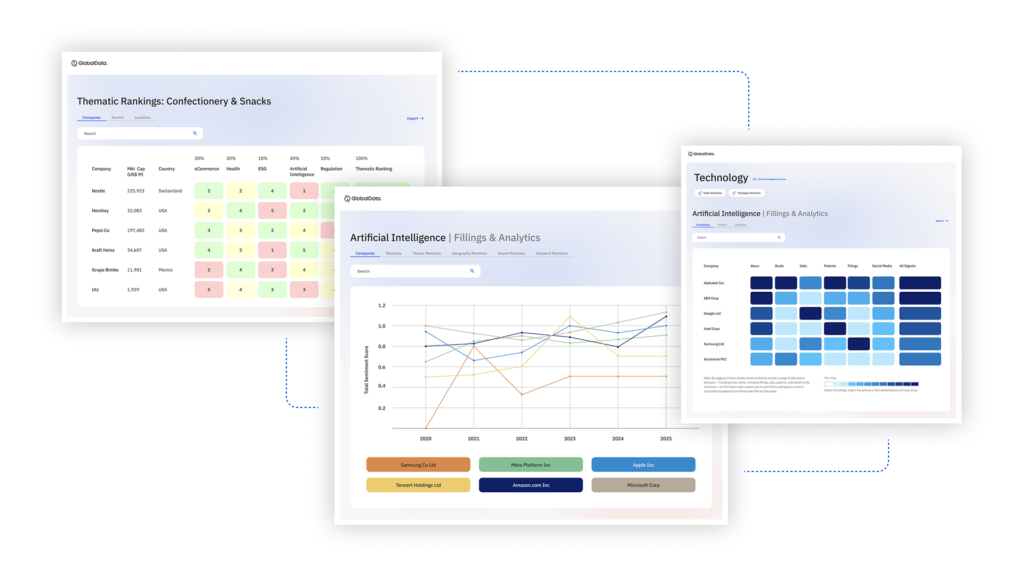
US Tariffs are shifting - will you react or anticipate?
Don’t let policy changes catch you off guard. Stay proactive with real-time data and expert analysis.
By GlobalDataThe North American market, however, still has some way to go. “I would expect to see 5 – 10% of the North American newly-registered vehicle market fitted with GDI by 2012, probably in combination with other technologies such as variable valve train,” said Mike Frick, chief engineer for Delphi’s direct injection gasoline systems. “Of course, that assumes VW roll out their homogeneous GDI engines in the US as planned, followed by other carmakers.”
Turning to the diesel market, Ricardo predicts that while a number of new diesel models in the US have been introduced in 2004, the introduction of the California LEVII emissions standards will mean that diesel sales volumes remain flat at least until low sulphur fuel is introduced in 2006. Beyond 2006, further new product introductions are considered likely and with diesel acceptance growing particularly in the light truck sector, Ricardo predict a diesel market penetration in the region of 6% by 2010.
But changing consumer opinions and perceptions of, dare we say it, ‘dirty diesels’ will take some time. “The lack of growth in the US diesel market is as much due to a poor perception amongst consumers as anything else,” added Delphi’s Mike Frick. “Today’s common rail systems have noise characteristics and driveability that many more people would find far more acceptable than past systems. Although modern diesel technology has improved and helped cut emissions, the absolute fuel economy difference between gasoline and diesel has narrowed. So in deciding between the two fuel types, the end consumer will typically make a trade-off between how much extra he or she will have to pay to acquire a diesel-powered car against the amount it costs them to fill the tank up each week. But if the absolute difference in fuel economy is not there, they’ll favour gasoline.”
Siemens VDO and Bosch both unveiled their new common-rail diesel injection systems in 2003, both of which use piezo-hydraulic technology for injector speeds four times faster than traditional solenoids.
Siemens VDO’s third-generation common-rail diesel injection system centers around a newly-designed piezo actuator integrated directly into the valve shaft. A hydraulic compensator between the actuator and the nozzle transmits the force from the underside of the actuator to the servo valve and accommodates manufacturing tolerances, temperature-induced changes in length and any wear in the system. The new PCR3 system has a pressure of 1800 bar, though Siemens says pressures of up to 2000 bar are possible. Julian Dench, head of Siemens VDO’s diesel operations in North America, said: “We will be the first to market with a piezo injector in North America. It is an evolution of the current systems we are using in Europe with PSA and Ford. We’re now adapting that system for the US market. The first application will appear in 2007 model year for International and Ford applications.”
Bosch has also launched production of its third generation common-rail injection system with piezoelectric inline technology. The first units were installed on the Audi A8. With previous generations of common-rail, Bosch made a point of emphasising the injection pressure — for the first generation it was 1,350 bar, for the second 1,600 bar. The focus of the German supplier’s third generation has shifted to the technical specification, with the injection pressure remaining at 1,600 bar, although the company says that 1,800 bar will follow by the end of 2006. The special feature of this third generation are the inline injectors with their piezoelectric actuator built into the injector shaft and lying very close to the needle of the injector jet. Dr Ulrich Dohle, director of Bosch’s diesel systems division, said: “The new injectors have 75% fewer moving parts and 75% less mass. This allows them to switch twice as fast as conventional magnetic and piezoelectric injectors.” Bosch claims its third generation technology can lower diesel engine emissions by up to 20%, increase engine power by 5 – 7%, reduce fuel consumption by 3% and reduce engine noise by 3 decibels. Bosch also says it is currently looking at ways in which to improve its common-rail systems by raising the injection pressure to more than 2,000 bar by means of a kind of pressure gearing, without having to increase the system pressure itself.
For its part, Denso has launched its new high-pressure 1,800 bar common-rail diesel injection system in Europe, and is aiming to sell 1 million units worldwide by 2005. The higher pressure reduces particulate matter and improves engine performance, and the system delivers no less than five injections to each stroke for better combustion control. A short pre-injection shortens ignition delay and reduces NOx gases and a post- injection dose re-burns any remaining particulate matter. A further injection helps manage the temperature of the exhaust gases better and provides a dose of hydrocarbons to act as a NOx reduction agent. The interval between the first and last injection is a mere 0.4milliseonds, the shortest in the industry, and Denso says it will reduce this further in future by using piezo-injectors.
![]() | Expert Analysis | ![]() |
Report coverage To find out more about this report and to order your copy, please follow this link. |
![]() | ![]() |