GM’s Lansing Grand River plant is testing GM’s new manufacturing system and some of the lessons learnt there could well be used elsewhere. The plant is also playing an important part in Cadillac’s upcoming new product offensive, cranking out the new CTS sedan and soon to add the SRX. Greg Keenan took a tour exclusively for just-auto.

Among the first thing that grabs your attention at the new Lansing Grand River plant operated by General Motors Corp. are the vending machines a short distance from the assembly line. It’s typical of any North American assembly plant to see machines offering soft drinks, chocolate bars or sandwiches within easy distance of the workers, but these ones are different – they’re dispensing earplugs, gloves, small tools and arm protectors. The machines are close to the assembly line so workers don’t have to trudge 30 metres to a central storage area to get new gloves or other safety paraphernalia.
![]() |
Architect’s model |
It is, in the grand scheme of things at a 150,000-car-a-year assembly plant, a small item. But it indicates how methods at GM’s first new assembly plant in 15 years have changed from past practice and how the vehicle maker is determined to improve the way it manufactures cars and trucks.

At other factories, says plant manager Bob Anderson, a 35-year GM veteran, “it was such a pain to go the storeroom that you bought [gloves] by the dozens” and took them to the workers to save them the walk. Now, they’re right across the aisle.
The emphasis at Lansing Grand River is on the workers, Anderson says, and there are fewer of them here than in most other GM assembly plants in North America – just 1,500 employees when the plant reaches full production capacity of 130,000 vehicles a year.
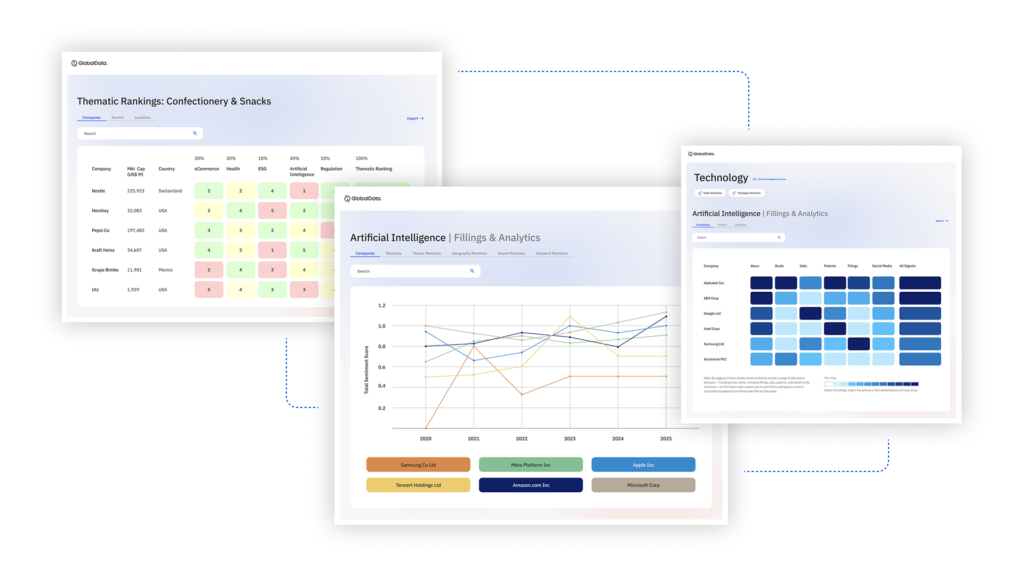
US Tariffs are shifting - will you react or anticipate?
Don’t let policy changes catch you off guard. Stay proactive with real-time data and expert analysis.
By GlobalData“They’re the only ones that are adding value for the customer. … If we minimise the waste, we’ve minimised the cost of the assembly slice of the cost of a car.”
![]() |
Powertrain carts |
There’s much more at stake in Lansing, however, than a test of whether GM’s new manufacturing system will work and how lessons learned here can be used elsewhere. This plant is critical because it’s churning out a new flagship car to replace the [Opel-built] Cadillac Catera and other vehicles for Cadillac as GM seeks to restore the shine to the tarnished image of its fabled luxury brand. Lansing Grand River is cranking out the new CTS sedan and will soon add the SRX, a so-called hybrid that is designed to combine the ride of a car with the usefulness of a sport utility vehicle.
Those are just two of a flood of new products coming from Cadillac in the next few years.
“Cadillac is of extreme importance to General Motors,” says Bob Lutz, vice-chairman of General Motors Corp. and head of product development for the world’s largest vehicle maker. “Cadillac is getting a very large proportion of our engineering and product resources. Cadillac is going to be over-nourished.”
One of the ironies is that the renaissance of Cadillac is occurring in a city that for more than 100 years was the home of Oldsmobile, a division GM is slowly killing off. It was here that Ransom E. Olds began tinkering more than 100 years ago.
Olds Avenue runs alongside the Lansing Grand River plant. Pictures of classic Oldsmobile models adorn the walls of a nearby fast-food outlet.
![]() |
Body drop |
It’s a GM town, where more than 8,000 workers toil for the General.
All the workers at Lansing Grand River asked to be transferred to the plant when GM began hiring in 1999, says Art Baker, shop committee chairman for local 652 of the United Auto Workers.
Baker points to a great working relationship between his local and GM management as one key factor that should make the new manufacturing system work.
There are just two grievances outstanding at the plant, he says. That compares with hundreds at other GM plants in Canada and the United States. He makes no bones about this local’s [union branch’s] different attitude.
“This is a worldwide economy. They’ve got to make money or you’re out of a job,” he says bluntly. All the workers were aware of the new rules before signing up, he says, including the fact that they would work in teams – in this case six people instead of a dozen or more at other GM plants.
Before deciding who would get jobs in the new plant, officials set up a simulated work environment where the principles of GM’s global manufacturing system were used, showing workers what to expect.
In one simulation, a team was told to add a side marker lamp to vehicles destined for export markets. No single member of the team had time to install the light, but there was enough time overall, so workers were left to decide how to best manage their time so the light could be installed.
![]() |
Sunroof installation |
In another simulation, one worker was given a nearly impossible task while another was given much less work. They were given the power to change the situation so that the work was balanced. Anderson says teams are told what they need to do, but they’re allowed to work out for themselves how to do it. They rotate jobs, for example, so that no one spends an entire shift doing a job that puts pressure on his or her right arm and shoulder. They’ll switch between those jobs and others that involve bending movements or use of the other side of their body.
“It’s up to the team to decide how often to make the switch,” he says. The general assembly building is T-shaped with 37 loading docks so parts can be brought as close to the assembly line as possible. This reduces inventories of parts, which makes for a smaller factory, but it has another strong safety element – reduced traffic.
In fact, forklifts in the general assembly building are prohibited – parts are carried to the assembly line on small guided vehicles or by employees tugging carriers by hand. “Forklifts are our biggest source of risks for accidents,” says Anderson.
“In a collision between a pedestrian and a forklift, the pedestrian always loses.”
The shift in attitudes goes right down to the belt buckles on workers’ pants. Their pants are fastened with Velcro so there are no metal buckles to scratch the cars.