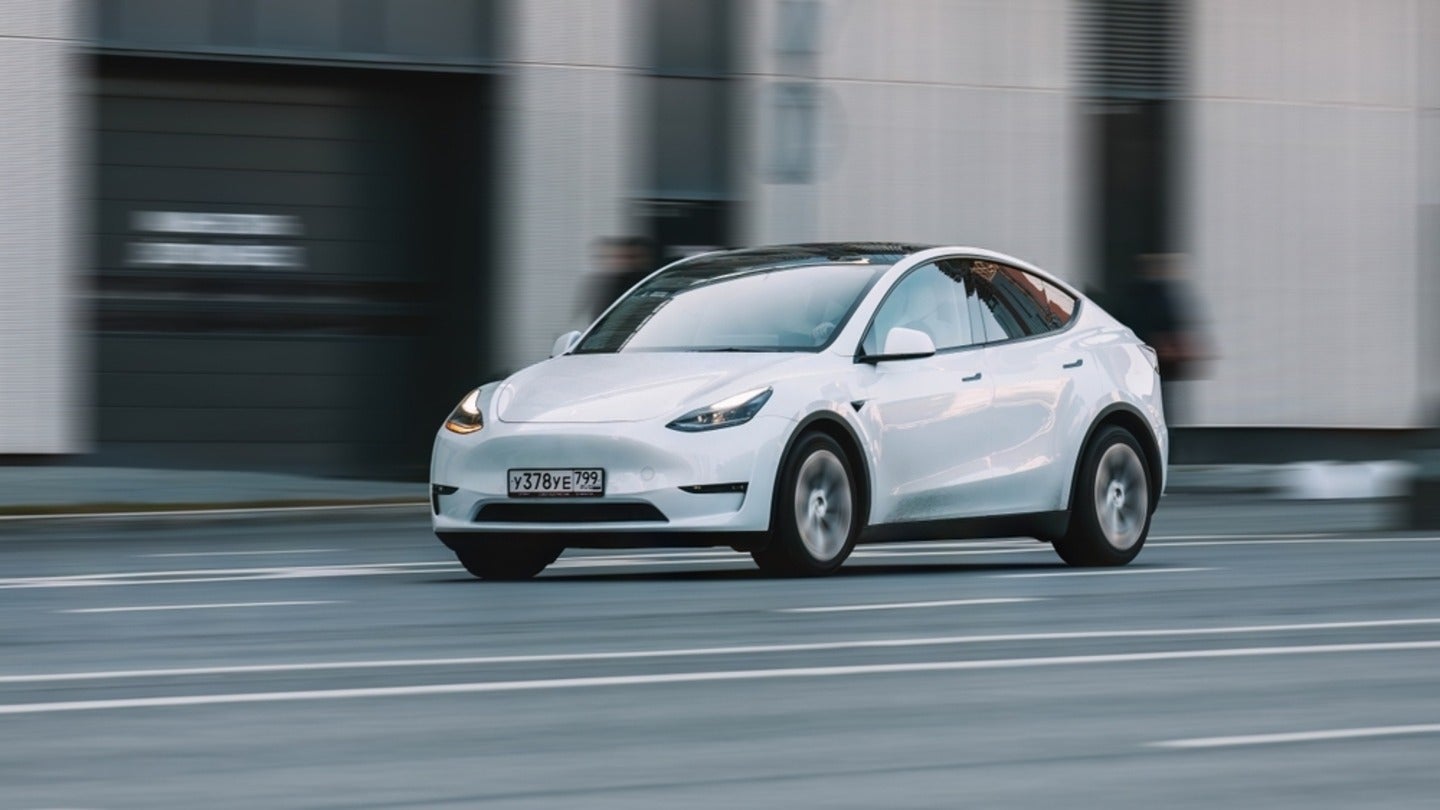
Initiated by Tesla back in 2020, the new gigacasting “megatrend” has now caught on amongst automakers such as Toyota and China’s Geely, NIO and Xpeng, fueled by the technique’s putative benefits, as well as by increasing aluminium usage in light vehicles.
The Aluminium Association and Ducker Carlisle’s 2023 North American Light Vehicle Aluminium Content and Outlook study confirms that aluminium use will continue to grow in the automotive market through the end of the decade, driven by light-weighting and the accelerating electrification of vehicles. Aluminium usage has now surpassed 227kg per light vehicle in North America and 180kg per vehicle in Europe.
These new casting technologies, spearheaded by companies such as LK Group, Bühler and Haitan, have even caused the likes of JFE Holdings – Japan’s second-biggest steelmaker – to worry about repercussions for steel consumption amongst automakers.
“The amount of crude steel used will obviously decrease,” President of JFE Holdings, Koji Kakigi, told reporters in the summer, describing gigacasting as a “very big problem”.
The economic advantages of gigacasting cannot yet be reliably estimated, says metal casting expert Professor Volk
Professor Wolfram Volk, the department head for forming technology and casting at the Technical University of Munich, takes a more a cautious view of the technique’s possible future in auto manufacturing, telling Just Auto that until its technological problems are controlled, the economic advantages of gigacasting cannot be reliably estimated.
He points to the fact that the production of large structural components is “a multidimensional boundary value problem”, which relates to “process control” and “applicable aluminium alloys”. The long flow paths of the melt, he says, cause inhomogeneous cooling behaviour, which can lead to warpage and cracks of produced castings, while thermal management of the large moulds remains a challenge.
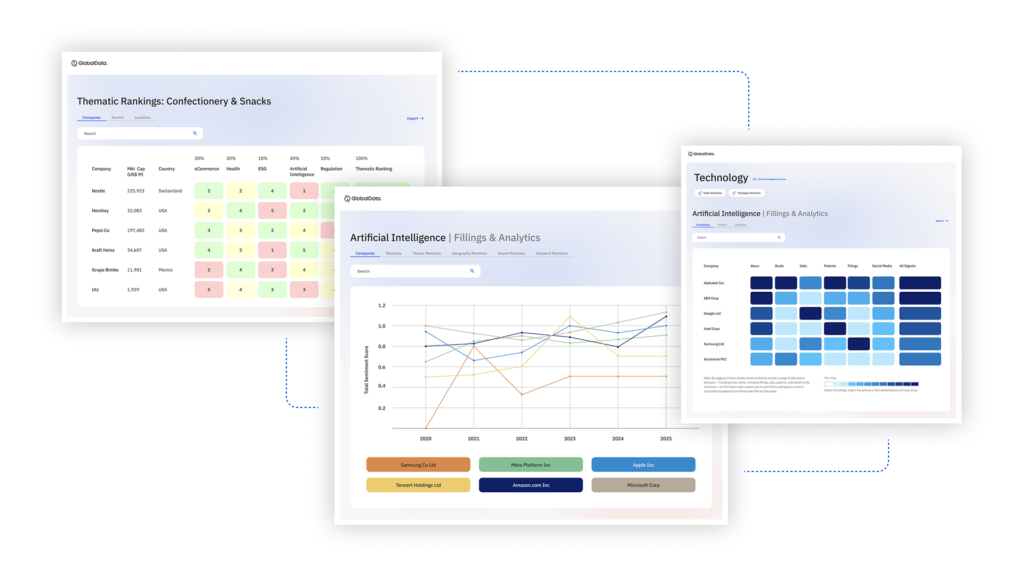
US Tariffs are shifting - will you react or anticipate?
Don’t let policy changes catch you off guard. Stay proactive with real-time data and expert analysis.
By GlobalData“Also, the risk of air entrainment during casting prevents subsequent heat treatment, which is why naturally hard alloys have to be used,” he adds. “However, the high copper content, due to a desired mechanical material behaviour, reduces corrosion resistance.”
Indeed, Tesla has attempted to get around the problem of air entrainment by developing an aluminium alloy that allows it to “skip the heat treating traditionally used to increase the strength of the cast part” – a concern that may exacerbate the company’s pre-existing quality control issues.
“In addition, the production infrastructure, available die-casting machines, and high die costs must be mentioned,” Professor Volk says. “The high tooling costs require innovative prototyping technologies during the engineering cycle in order to design HPDC dies “first-time-right”.”
Professor Volk has previously said that for manufacturers located in brownfield sites, it would be “operationally nonsensical” to adopt the new technology. This is because of the typical time frames for cost-depreciation of the welding robots and forming processes used for existing vehicle generations.
“A middle ground of conventional body construction and gigacasting may well become established,” he suggests. “For example, already existing plants could realise hybrid construction methods by inserting formed components into the die-casting mould and casting around them to form the end product. This approach, called ‘joining by casting’, would also leverage the potential to reduce joining operations.”
Professor Volk also raises gigacasting’s oft-mentioned implications for repairability and the insurance industry: “Weldability of the cast components would be given at relatively low void contents. However, this requires high-quality and therefore pore-free cast components, which is already a major challenge in conventional pressure die-casting.”
The more cynical, of course, have suggested that low repairability may well be in the interests of automakers, some of whom have been known to campaign against consumers’ rights to repair their own property.
Back in 2020, the Alliance for Automotive Innovation, which represents nearly every automaker in the US, began funding a campaign against a ballot measure in Massachusetts that would expand the scope of the state’s right-to-repair law. Only a few months ago, the group filed a court document to prevent the enforcement of the law – an indicator of the industry’s strength of feeling on this topic.
And if gigacasting blocks repair more effectively than traditional metal sheet fabrication, perhaps more automakers will be awakened to the mighty Giga Press’ appeal…