Around the world, automakers and their suppliers are working to make motor vehicles environmentally friendlier. The strictest standards have been set for markets in Europe and the United States. The general goal of not polluting is the same in both regions, but the paths toward reaching this goal are different. In Europe, the focus is on the self-imposed industry requirement of reducing fuel consumption measured by carbon dioxide emissions (CO2). The US-government is focusing requirements on reducing the emission of toxic substances. As a rule, these goals are the same for spark ignition and diesel engines. At the 55th International Automotive Press Conference held last month in Boxberg Dr. Rolf Leonhard, Executive Vice President Development, Division Management Systems for Gasoline Engines of Robert Bosch GmbH, delivered a speech looking at future developments for spark ignition engines. We reproduce it here.
With its injection systems for spark ignition engines, Bosch has made significant contributions toward advancing engine technology. For example, there was the first gasoline direct injection system in 1952, the first electronically controlled injection system in 1967, the oxygen sensor as basis for effective exhaust gas aftertreatment in 1976 and gasoline direct injection with charge stratification in the combustion chamber in 2000.
Even though the diesel engine is gaining market share because of its favorable fuel savings and torque characteristics and the hydrogen-driven fuel cell, with its “zero emissions” appears as the ideal power source, the spark ignition engine still has enormous development potential. Bosch wants to utilize this further through innovations. Thus, the spark ignition engine will remain the most important power source of the automobile for a long time to come.
Several criteria decide the competitiveness of each powertrain type:
- Achieving minimum emissions values, in the USA in accordance with “SULEV” limit values (SULEV stands for Super Ultra Low Emission Vehicle) or in Europe in accordance with threshold values per the EU5, which is still in the final definition phase.
- Reducing energy consumption measured by CO2-emissions according to
– The Acea requirement by 2008 140 grams CO2 per km
– The Acea target by 2012 120 grams CO2 per km
The requirements of the European Union Parliament go even further:
By 2005 120 grams CO2 per km
By 2010 90 grams CO2 per km
- Driving pleasure is based on comfort and acceleration capacity.
- Customer-friendly infrastructure to obtain fuel.
- Low cost.
Development Path to Reduce Emissions
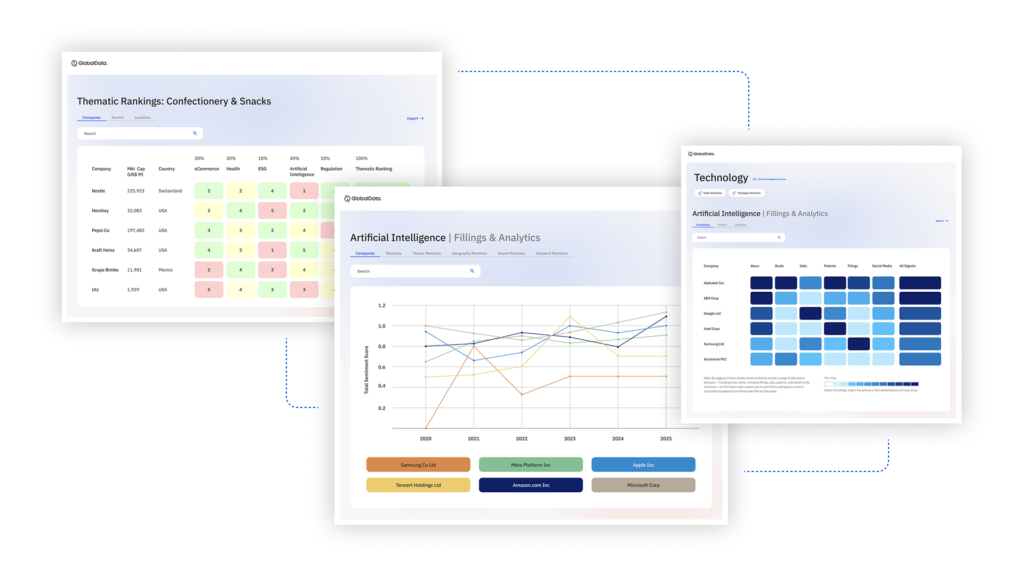
US Tariffs are shifting - will you react or anticipate?
Don’t let policy changes catch you off guard. Stay proactive with real-time data and expert analysis.
By GlobalDataThe new challenge for the American market is called SULEV. These threshold values of 0.010 grams NMOG (non-methane oxygen gas) per mile and 0.02 gram nitrous oxide (NOx) per mile stipulate 75% lower hydrocarbon (HC) emissions and 90% lower nitrous oxide emissions compared to regulations in effect since model year 1994. In addition, the lowest evaporation emissions must be fulfilled per SULEV. Government legislators require fulfillment of these values for emissions-related components for 150,000 miles or 15 years of operation. US-law recognizes SULEV as a replacement for the zero emissions vehicle requirement (ZEV).
Bosch engineers have an entire assortment of technical measures to achieve the SULEV emissions level. Raw emissions values – the exhaust values before treatment with catalysts – drop especially due to an optimized engine start and uptake. The faster heating of the catalyst and a control strategy adjusted to optimized catalyst operation also reduce the emissions values. In addition to the secondary air pump for better post combustion in the exhaust tract, Bosch also provides oxygen sensors in planar technology, which reach their operating temperature within a very short time period and can measure the fuel/air mixture in a broad range.
More difficult than reaching a low emission level is the vehicle’s own permanent control per onboard diagnostics (OBD). Using further-developed, model-supported algorithms and improved oxygen sensors, Bosch engineers have been successful in providing reliable diagnostics.
Development Path to Reduce Fuel Consumption or CO2 Emissions
The Emissions Level EU4 will be in effect in the European Union (EU) starting in 2005. The threshold levels in the EU4 have been so low that the German Environmental Protection Agency in Berlin that is normally quite critical has certified an air-purifying effect. To some extent, the threshold values for harmful emissions from vehicles lie below the values measured in ambient air. For the modern spark ignition engine, EU4 is no longer a hurdle. In Germany, 65% of all newly registered vehicles with spark ignition engine fulfilled the threshold values per EU4 or the comparable D4 standard in 2000.
With its gasoline direct injection DI-Motronic, Bosch was able to set the standard regarding fuel consumption and CO2 emissions in the Volkswagen Lupo FSI. The vehicle was on the market in 2000 in a pre-series version. Thanks to direct injection stratified charge technology and other technical measures, consumption in this car was reduced 15% compared to conventional manifold injection. These are savings that will be surpassed in the future. With this first step toward gasoline direct injection, European manufacturers have once again passed up Japanese manufacturers, who a few years ago held the lead.
Designers have several more tasks to solve in order to reduce fuel consumption and CO2 emissions further:
- The new injection nozzles from Bosch make it possible for the spark ignition engine to make the transition from wall- or air-guided to a spray-guided combustion process like the diesel engine. The engines thereby achieve better efficiency. The challenge is to find the correct fuel/air mixture under all operating conditions. In addition to modified fuel injectors, Bosch is also developing improved ignition systems for the combustion process.
- In the 2nd generation, Bosch will supply a high-pressure fuel pump, which is integrated in the cylinder head. The energy requirement to create pressure is regulated via a control device.
- In order to further reduce NOx emissions, Bosch is working on optimizing the return of exhaust to the manifold tract. Experts are developing a fast, electrically actuated exhaust return valve for this purpose. Compared to earlier versions, it operates faster and can be adjusted finer. As a result, engine management measures the exhaust return more precisely.
- Manufacturers of catalytic converters are taking up the task of expanding the operating range of the NOx reservoir catalyst.
With the help of these improved technologies, the sum of consumption values of future spark ignition engines will drop up to 20% below the values of engines with conventional manifold injection. For a compact car weighing 1350 kg with a 90 kilowatt engine, which is representative for the vehicle fleet today, this signifies reduced CO2 emissions from 185 to 150 grams per kilometer.
130 grams of CO2 per kilometer can be achieved for spark ignition engines via further engine measures such as raising the specific engine power through supercharging, thermal management, variable valve control and start/stop strategies. Thus, the ACEA requirement for 2008 (140 grams CO2 per kilometer) is undercut and the ACEA-target for 2012 (120 grams CO2) has almost been reached.
These lower CO2 emissions values for spark ignition engines can be reduced even more. 90 grams per kilometer can be reached with optimized spark ignition engines operated with natural gas. Even zero emissions of CO2 can be reached with spark ignition engines operated with hydrogen. Compared to the fuel cell, these offer considerable cost advantages.
More Driving Pleasure with the New Spark Ignition Engines
Engine designers have a good starting point to improve the responsiveness and torque characteristic of the spark ignition engine in a significant way. Gasoline direct injection by itself or even combining this process with supercharging and variable valve control make this possible, while at the same time reducing fuel consumption. Bosch will make significant contributions in this area through more innovations.
The Spark Ignition Engine Offers Long-Range Cost Advantages
Compared to the alternatives such as weight reduction of vehicles or a transition to electric powertrains with fuel cells as energy converter, the described engine measures offer a clearly better cost/benefit ratio. For this reason, Bosch is assuming that engine modifications in regard to emissions and fuel consumption will prevail on the market and the role of the spark ignition engine will remain long-term as the most important powertrain system for passenger vehicles.
Important Development Steps for the Spark Ignition Engine
| Nikolaus Otto invents the four-stroke gas engine as basis for the present spark ignition engine. |
| Robert Bosch creates the foundation for developing high-speed and high power spark ignition engines with the design of the high voltage magneto; he lays the cornerstone for developing his company into a global enterprise. |
| The Gutbrot Superior 600 is in series production as first passenger vehicle with gasoline direct injection. Compared to traditional engines, fuel consumption is reduced 20 per cent and power raised 20 per cent for the two-stroke engine used. |
| The legendary wing-door Mercedes 300 SL is equipped with the gasoline direct injection system of Bosch. Due to its extraordinary power capacity, the 300 SL was successful in several car races. |
| The first global electronic gasoline injection system – the D-Jetronic of Bosch – comes to market in the Volkswagen 1600 E. |
| The first gasoline direct injection of Bosch with Lambda control is used for effective exhaust after-treatment. |
| The gasoline direct injection or DI-Motronic from Bosch with charge stratification is in series production in the VW Lupo FSI. With reduced fuel consumption of 15% and the EU4 emissions level, this technology sets the standard. |
| The SULEV emissions level (Super Ultra Low Emission Vehicles) is a requirement in the USA for newly registered passenger vehicles. |
| The Association of the European Automobile Industry wants to voluntarily reduce CO2 emissions for the newly registered passenger vehicle fleet to 140 grams per kilometer (25% less compared to values in 1995). |
Gasoline direct injection
|
| ||||||
Combustion Systems – Gasoline direct injection
![]() |
Exhaust-Gas Aftertreatment – SULEV System
![]() |
To view related research reports, please follow the links below:- IMS Corporate Profile – Robert Bosch GmbH |