Ford’s been taking some pretty big hits lately. A guarded left hook came its way the other day from another website, thetruthaboutcars.com. Bob Elton, author of the piece, was tough on Ford’s pace of innovation. “In Ford’s latest ads,” he said, “Mr. Bill touts The Blue Oval as a tireless automotive innovator. In reality, Ford has seldom, if ever, taken the technological lead.” This statement doesn’t pass the ‘truth’ test. It falls to me to enlighten Mr. Elton about some of Ford’s Better Ideas, writes Karl Ludvigsen.
Ford’s forays into the structure of the automobile began with its exploitation of better materials. “Without question,” wrote Henry Ford’s colleague Charlie Sorensen, vanadium-alloy steel “furnished the real impetus for abandoning the sensational success of Model N for the evolution of Model T and ultimate realization of Henry Ford’s dream of a car for the masses.” Legend has it that American discovery of this improved alloy occurred on Florida’s Palm Beach in 1905 when an inquisitive engineer picked up steel shard left there by a French racer’s engine. According to Sorensen, however, its origin was Britain, “a country which had been in the forefront of steel development.”
Early in 1906 an English metallurgist paid a call on Ford, bearing samples of vanadium-alloyed steel. Small amounts of vanadium, as little as a quarter of a percent, more than doubled steel’s tensile strength and increased fatigue and shock resistance without degrading ductility. Once he was convinced that the alloy could be produced consistently and machined easily, Ford went all out to design a new car to exploit it. “We can get a better, lighter and cheaper car out of it,” he told Sorensen, who recalled, “It was the great common sense that Mr. Ford could apply to new ideas and his ability to simplify seemingly complicated problems that made him the pioneer he was.”
Exploitation of the new alloy in the frame and other major parts of the Model T accounted for its ruggedness and resilience in spite of components that other engineers thought flimsy and fragile. The improved steels, worked out by C. Harold Wills in many experiments at Ford’s Piquette Avenue plant, were used throughout the Model T. Another striking feature was the T’s use of steel pressings for such major parts as the rear-axle housing and the sump beneath both the engine and the transmission. Later Ford would acquire the Buffalo, New York plant that made them and — even before that — the lanky Danish mechanic who supervised the pioneering stamping job, William “Bill” Knudsen.
Henry Ford had less success with his next major structural innovation. At the end of the 1930s he was building plastic-bodied prototypes with steel tubular frames. Engineer Robert Boyer led the creation at Ford of a plastic sheet made from agricultural products such as soybeans, wheat, hemp, flax and ramie. Using panels fabricated from this plastic, in April 1941 Henry Ford revealed his prototype with a complete plastic body supported by a tubular space frame. Recalled engineer C. J. Smith a decade later: “They made molds and made the whole car. It had a welded, tubular [steel] frame because this type of frame is strong, but it cost too much to make. Nowadays, since they have [automatic] welders, it wouldn’t cost so much. Then, it had to be all welded by hand.” Ford’s vision for this vehicle even embraced a rear-engined version using a transversely mounted V-8.
How well do you really know your competitors?
Access the most comprehensive Company Profiles on the market, powered by GlobalData. Save hours of research. Gain competitive edge.
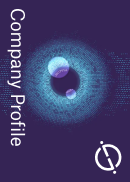
Thank you!
Your download email will arrive shortly
Not ready to buy yet? Download a free sample
We are confident about the unique quality of our Company Profiles. However, we want you to make the most beneficial decision for your business, so we offer a free sample that you can download by submitting the below form
By GlobalDataAfter World War II the rebuilding of Ford’s engineering cadre including its luring from GM of Earle Steele MacPherson, a man remembered by an associate as “an engineer’s engineer, an idealist, self-centered and very usually right.” MacPherson was 56 in 1947 when he jumped ship to Ford. His last project at GM had been the design of a small car for Chevrolet, the stillborn Cadet. Features that MacPherson sought to give the Cadet appeared instead on Ford’s cars in Europe and America.
Clutch and brake pedals suspended from the firewall marked one MacPherson innovation. They appeared on new British Fords in 1950 and American Fords two years later. Most profound, of course, was his introduction of what has become known as MacPherson front suspension — using a strut instead of an upper wishbone to guide the wheels and provide springing, damping and turning. This was first used on the British Consuls and Zephyrs introduced at the Earls Court show in the autumn of 1950. “When the Ford organization produces an entirely new model,” said London’s The Motor about the Consul, “one can expect to find evidence of original thinking.” In this MacPherson’s pathbreaking suspension didn’t disappoint.
Moving from structure and suspension to body innovations, Ford broke ranks with others in its price class in 1928 when it made laminated windshield safety glass standard in its new Model A. Henry Ford had seen once too often the injuries that ordinary glass could cause. Safety was also behind the design of the interiors of 1956 Fords, with padded instrument-panel cowls, a recessed-center steering wheel and optional lap belts. These were innovative and welcome safety features whose merits would soon be proven. It proved premature, however, to promote them as positive features of a new-car design.
A remarkable body innovation came to the Ford range in 1956 for the 1957 model year. This was the Sunliner, a retractable-hardtop convertible. Originally developed in support of Lincoln’s Continental Mark II program, the all-electric folding top was launched on a Ford model instead. The innovative convertible — obvious forerunner of the many retractable hardtops of today — remained in the Ford range through the 1959 model year. In all, 48,394 were produced.
Nineteen fifty-five saw Ford launch an innovative model in its two-seat Thunderbird. Its heart wasn’t in this project, however, and even before the two-seater was introduced its four-passenger successor was on the drawing boards. This turned out to be the more innovative car, for the idea of a modern close-coupled 2+2 “personal car” had legs. With its dedicated seating for four and deep central console (which was also structural) the 1958 Thunderbird was the envy of Ford’s competition and soon imitated, especially by GM with its Buick Riviera.
In 1964 Ford unveiled its affordable personal car, the Mustang. This became an object lesson — arguably the industry’s first in the modern era — in the exploitation of a volume platform to permit the production of an appealing derivative. The ingenious conception of the Mustang broke open the floodgates to alternative body styles and configurations having a stronger appeal to specific groups of customers, a trend that still hasn’t run its course.
Bodies of Ford cars were better protected during these years by a 1958 innovation by Ford’s manufacturing engineers. They developed electrocoating or E-coating, immersing a complete body in a bath of primer with an electrostatic charge that persuaded the primer into every nook and cranny. This was quickly taken up for Ford’s European models, whose unitized body-frame construction benefited greatly. In America it was phased into Ford’s Wixom plant in the early 1960s to the benefit of the unitized Thunderbirds produced there. Adopted as it was by Ford’s rivals, E-coating earned the Blue Oval handsome royalties payable against its patents.
Ford’s drive-train innovations are traceable back to the ingenious planetary transmission of the 1908 Model T. Though planetary drives weren’t unknown, none matched Henry Ford’s in compactness, simplicity and ease of operation with its unique combination of pedal with lever controls. Thought it had its limitations — only two forward speeds — the unique planetary drive was one of the T’s most endearing features.
Near the end of the century Ford found itself pioneering in drive trains again with the offering of a continuously-variable transmission or CVT in its European Fiesta. Although delayed from its hoped-for 1984 introduction, Ford’s launch of a CVT-equipped car in April 1987 was the first ever in Europe, followed by Fiat. Ford’s engineers had been working with Van Doorne, inventors of the push-type belt for CVTs, since 1976. From its first “CTX” units, which were supplied by Van Doorne, Ford later moved to its own manufacture of the compact transaxles at its Bordeaux factory.
In power units the Model T helped establish Ford’s reputation for innovation at the service of the car owner. Thought through from first principles, its engine marked a break from all past practice and set new guidelines for the future. In 1908 its use of a one-piece cast-iron block with a detachable cylinder head was unique for a car in volume production at a time when individual or paired cylinders with integral heads were the norm. It did without an oil pump altogether, instead using its flywheel to deliver oil through a pipe to the cam-drive gears, from which it flowed back through the pressed-steel oil pan, and its troughs for con-rod lubrication, to the sump below the transmission.
The Model T engine abounded in ingenious detail, such as its pioneering use of clamps to retain both the inlet and the exhaust manifolds. Water jacketing was provided over only the upper one-third of the cylinder. Excess metal was absent. In 1925 Murray Fahnestock would write, “The Ford crank shaft is relatively small for the piston displacement as compared with the crank shafts or other-than-Ford cars.” Indeed, exploiting vanadium-alloy steel, the forged crankshaft resembled more a bent wire than what we’d think of as a crankshaft today.
Two decades later Henry Ford’s team, including Joe Galamb and Charlie Sorensen, brought their skills to bear on the volume production of a V8 engine. Here again they made significant breakthroughs in design and production. One claim that Sorensen made for the new eight didn’t hold up, however. “All previous V8s had been case in more than one piece,” he wrote. Most indeed used separate blocks on a crankcase or a block cast in two halves. In 1929, however, GM’s Oldsmobile introduced a V8 with a one-piece block for its new “companion car,” the Viking. With the block of the 4,252 cc Viking needing only its cylinder heads added, it was called “a rather remarkable casting” by Automotive Industries.
It wasn’t the Viking that survived, however, but the Ford. In volume terms, of course, Ford’s challenge was far greater. Its V8’s one-piece block was designed as much for manufacturability as for performance. “When they found me making changes in design so as to fit the foundry and machine needs,” Sorensen recalled, the designers “actually believed I would ruin the engine.” A major coup in the V8’s production was the development of a two-ton molten-iron furnace that followed molds moving continuously down a pouring line at a rate of 100 per hour. Cooling of the castings was carefully controlled to create an iron structure that was compatible with high-speed machining. From 1934 Ford’s V8 also broke with convention in its use of cast instead of forged crankshafts.
Seen at the time as a radical departure for a low-priced car, Ford’s V8 was one result of a program of exploration of unusual engine types that Henry Ford conducted personally. Henry had the will and the resources to build and test unusual engines to see how they worked. Included were flat opposed twins and fours, an L-head in-line five and an overhead-cam V10, many versions of the V8 including air-cooled and overhead-cam variants, overhead-cam sixes and an aluminum-block overhead-cam V12 of only 2.1 liters. A particular obsession was an X-pattern eight-cylinder engine with four sets of paired cylinders, made in both liquid- and air-cooled versions. Henry had high hopes for this but it proved difficult to package.
After World War II Henry Ford II’s engineers in Europe were his company’s point men in engine innovation. First in Germany in the 1950s, its in-line fours began using three-bearing crankshafts cast of nodular iron that looked massive but in fact were impressively light yet stiff by virtue of being cast hollow. This type of crankshaft was used by Ford of Britain in the new 105E overhead-valve four it introduced in 1959. Its “80-bore” nickname was off only slightly because its 3 3/16-inch bore equated to 80.96 mm, which with its ultra-short stroke of 48.4 mm gave 997 cc. The short stroke allowed its iron cylinder block to be only 7 ¼ inches high.
Better known later as the Kent engine, powering the popular Fiesta, Ford’s four was a breakthrough in combining performance with efficiency and simplicity. When enlarged to 1.5 liters it retained the same bore with a longer stroke and taller block and required five main bearings. This provided a firm base for the 1.6-liter Lotus Cortina version with a special twin-cam cylinder head designed by Harry Mundy and, later, for the four-valve-per-cylinder BDA engine built by Cosworth for Ford’s Escort RS1600. As tweaked by Cosworth the Kent four was a winner in Formula Junior and also a sound base for Formula Ford, perhaps the world’s most popular single-seater racing format.
In a joint effort between Ford’s Dearborn engineers and those in Germany, a different approach was taken for a new family of small-car engines in the late 1950s. Launched in Europe in 1962, the first of the new breed used a 60-degree V4 engine of 1,183 cc to power a front-drive small car, the Taunus 12M. While the four’s 60-degree vee provided compatibility with a V6 sister engine, as was implemented in both Germany and Britain, it posed the challenge of a high primary horizontal imbalance. This was overcome by the use of a contra-rotating balance shaft running at engine speed, the first use of such a shaft in the modern era and the first use ever for a vee engine.
With reduced emissions and low fuel consumption on their agenda in the later 1960s and early 1970s, Ford’s Dearborn engineers developed a series of engines using direct fuel injection to achieve charge stratification in a bowl-in-piston combustion chamber. These pioneering efforts led to the development of Ford’s Programmed Combustion Process or PROCO system. This showed great promise in both conventional and military vehicles, using a fuel-injection system developed by American Bosch. Although PROCO was overtaken by other technologies and especially by advances in electronics, it was an important attempt to encourage the engine itself to reduce emissions without resorting to aftertreatment.
Further research toward achieving optimum combustion-chamber design in Dearborn during the 1970s led to the creation of Ford’s Compound-Valve Hemi or CVH engine. With its low surface/volume ratio the semi-spherical chamber outperformed wedge-type and Honda-patent CVCC chambers both in the laboratory and on the road. Ingeniously, Ford found a way to marry the hemi head and its inclined valves with a single overhead camshaft and hydraulic lifters. Mutually inclined at an included angle of 45 degrees, the valve stems were also rotated seven degrees in the chamber’s plan view. Accounting for the “Compound-Valve” appellation, this cleared space for pressed-steel rocker arms to operate the valves from a single low-placed camshaft.
Ford launched its innovative CVH engine in displacements from 1.1 to 1.8 liters in 1980 in both Europe and America in its first front-drive Escort, jointly engineered as the “Erika” program to gain “world car” economies from a sharing of technologies. The CVH served manfully in a wide range of products on both sides of the Atlantic into the 1990s, being both fuel-injected and turbocharged successfully. More recently similar research into optimum valve and chamber designs led to Ford’s adoption of a standard layout, its four-valve “modular” chamber, for families of North American engines.
Like Henry himself between the wars, the modern Ford Motor Company has never been slow to explore alternative prime movers for its cars. Gas turbines and Stirling engines have both been on its agenda. Electrics have been pursued from Britain’s Comuta of the 1960s to the bought-in Th!nk project of the 1990s. Where fuel cells and hybrids are being developed, Ford is in the thick of it. Strong leadership in on-board electronics was signaled by Ford’s “Continental 90” concept car and its series of powerful EEC power-train control systems.
This is a pretty compelling list of Ford’s Better Ideas. To his credit, Mr. Elton allowed as how Ford has made consistent and effective use of one innovative technology: air suspension, introduced on the Lincoln Mark VII in 1984. It then migrated to the Continental in 1988 and later to the Town Car and Mercury’s Grand Marquis. Air springing also benefits Ford’s sport-utilities and models from Jaguar and Land Rover. Bob Elton rightly suggested that it would be a Better Idea for Ford’s trucks as well.
So Ford’s record for innovation is pretty good. But in the car business the question is, “What have you done for me lately?” It’s time for its engineers in Dearborn, Cologne, Dunton, Coventry, Gaydon and Gothenburg to reach out for radical new solutions to the immediate challenges facing car makers: reducing both cost and weight at the same time. Henry did it. Now it’s Bill’s turn.
– Karl Ludvigsen
Karl Ludvigsen is an award-winning author, historian and consultant who has worked in senior positions for GM, Fiat and Ford. In the 1980s and 1990s he ran the London-based motor-industry management consultancy, Ludvigsen Associates. He is currently an independent consultant and the author of more than three dozen books about cars and the motor industry, including Creating the Customer-Driven Car Company.