In a world exclusive, AWKnowledge reveals that Ford’s US management has committed to using CGI material for future diesel engine programmes. John Mortimer reports.
For the first time in the company’s history, Ford has cast Compacted Graphite Iron (CGI) components in its own foundry. This puts the company one step ahead of its long-time competitor, General Motors.
According to insiders, in July 2005, Ford’s Cleveland Casting Plant (CCP), Cleveland, Ohio, began casting CGI on a trial basis as a precursor to going on line to cast major engine components in the material for volume production. Up to now, Ford has relied entirely on independent foundries to produce its CGI engine parts, including for example, Brühl in Germany and Grainger & Worrall in the UK – both foundries for prototype parts. Ford uses Tupy SA in Brazil to produce CGI cylinder blocks for its 2.7-litre V6, and 3.6-litre V8 cylinder blocks.
However, Ford’s management in the US has decided to bite the bullet and commit to CGI material for future diesel engine programmes. By 2007 it will have a foundry of the future.
Ford’s CCP facility first poured CGI experimentally in early 1998 in an attempt to perfect the process on one of its cylinder block lines. The most recent attempt, however, is in line with plans to convert some of the company’s bearing caps to CGI ‘in the near future’. The tonnages involved will be small, but will give Ford’s foundry men experience of achieving specification perfect CGI material in readiness for more ambitious plans to use the material.
Late last year, 19 December, SinterCast announced that a Mini System 2000 would be installed at the CCP to support prototyping and product development of CGI engine components. This technology is essential to produce volume amounts of CGI. The new capability would enable CCP, the largest iron foundry in the Ford group with an annual production of over 300,000 tonnes of shipped engine castings a year, to independently support CGI engine developments within the Ford group.
How well do you really know your competitors?
Access the most comprehensive Company Profiles on the market, powered by GlobalData. Save hours of research. Gain competitive edge.
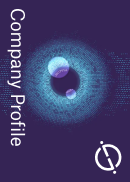
Thank you!
Your download email will arrive shortly
Not ready to buy yet? Download a free sample
We are confident about the unique quality of our Company Profiles. However, we want you to make the most beneficial decision for your business, so we offer a free sample that you can download by submitting the below form
By GlobalDataAlthough the Mini System 2000 has been installed in the jobbing and development area of CCP, it is widely recognised that this is but a step away from volume production of engine cylinder blocks and heads.
According to insiders, the CCP has cast five tons of CGI material since July – roughly one ton a month.
Significantly, as part of its CGI evaluation programme, Ford’s process engineers trialled two CGI process control technologies: that from SinterCast, and the rival, but less widely used, NovaCast technology. It was as a result of these back-to-back trials that Ford management opted for the SinterCast technology, helped along the way no doubt by the positive feedback they received from colleagues at Ford’s Dagenham Diesel Centre in the UK.
The Dagenham Diesel Centre is machining V6 blocks cast by Tupy in Brazil, and will assemble the new 3.6-litre V8 diesel engine. Both have CGI blocks. Significantly, Tupy uses the SinterCast CGI process control technology to supply cylinder blocks to Audi and Ford/PSA.
SinterCast officials admit privately that they have performed well with the Ford/PSA V6 Lion engine programme featured in both Land Rover and Jaguar vehicles. This work has given Ford confidence in both the SinterCast process control technology route, and CGI as an engineering material.
Insiders at CCP note, however, that work at the foundry on CGI is proceeding somewhat modestly at first. Although the foundry has a reputation for producing cylinder blocks – it can produce between three and four engine million equivalents a year – its first steps along the CGI road are in the area of bearing caps.
According to insiders, bearing caps fit into CCP’s plans to prove out its ability to use CGI. Bearing caps are simple in design and also easy to make. They will also generate cost savings and tooling is available to make the parts. But the longer-term aim is to produce vee-shaped cylinder blocks for diesel engines as the vehicle manufacturer capitalises on the inroads it has made in using CGI for V6 and V8 diesel engines in Europe.
Managers at CCP are only too aware that Ford’s competitors in Europe – Audi, BMW and Mercedes-Benz – all use CGI for blocks, though not all from the same source. It is known too that by 2007, Ford expects to have a ‘state-of-the-art’ melting department at CCP which, according to insiders, has to be supported by state-of-the-art mould lines. It is also expected that the new melting department must be capable of supplying different types of metal required, including CGI. Insiders note that the CCP must further develop its CGI technology if the company is to be a worldwide supplier of quality engine components.
The decision by Ford to allow its CCP foundry to join the CGI race means that every major cylinder block foundry in North and South America now has a SinterCast license with the one exception of the GM foundry in Defiance, Ohio. However, SinterCast claims it is supplying, from two other foundries, Sinter-Cast-based CGI cylinder blocks to GM for NASCAR motor racing. At least one of these foundries is also supplying cylinder blocks for a potential 4.5-litre production vehicle diesel engine. This leaves GM several steps behind Ford in its use of CGI for diesel engines.
This world exclusive from AWKnowledge appears in the latest edition of World Automotive Manufacturing, a dedicated round-up of all the latest global happenings and analysis specific to the manufacturing activities of the world’s light vehicle manufacturers. For more details, follow this link: https://www.just-auto.com/store/products_detail.asp?art=38033&lk=sup