Ford Australia plans to sell only 250 right-hand drive Mustangs in Australia each year from this month. But that hasn’t stopped it investing about $A4 million ($US2.1 million) in a two-year development programme during which nine prototypes were built, including one crash vehicle and one durability vehicle. Several ‘virtual’ prototypes were also engineered, incorporating data from the US Mustang development programme.
Like neighbouring New Zealand, Australia drives on the left and its government has long banned the registration of newly imported left-hand drive cars so Ford Australia had no option but to convert the Mustang to ‘right hook’ or do without adding the premium-priced American sports car to its range.
The Mustang already has a strong following in Australia, with an owners club boasting about 1500 members and an estimated 4000 privately-imported Mustangs on the road.
![]() |
The Mustang has a strong following in Australia |
Exports have not been announced but it’s likely some of the Australian converted cars will eventually take a trip across the Tasman Sea to New Zealand as the famous ‘pony car’ has a strong following there, too.
The Australian arms of both Ford and General Motors (Holden) are no strangers to selling right-hand drive versions of American designs.
Large American Fords such as the Fairlane, LTD and the early Bronco SUV were all engineered for RHD and assembled Down Under while Holden once used to assemble Chevrolet Bel Air and Pontiac sedans to offer alongside its indigenous Holden models, the first of which was based on a small Chevrolet in any case. Holden currently offers six RHD versions of the Chevrolet Suburban, all locally modified, and exports Chevrolet-badged left-hand drive versions of its locally-produced Commodore to the Middle East and South America.
How well do you really know your competitors?
Access the most comprehensive Company Profiles on the market, powered by GlobalData. Save hours of research. Gain competitive edge.
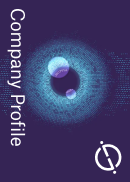
Thank you!
Your download email will arrive shortly
Not ready to buy yet? Download a free sample
We are confident about the unique quality of our Company Profiles. However, we want you to make the most beneficial decision for your business, so we offer a free sample that you can download by submitting the below form
By GlobalDataThe RHD project for the Mustang is, however, slightly different from those previously developed by Ford. The car is custom-built to Australian specification in the United States, but with left-hand drive, and only converted to RHD on arrival in Australia by Tickford Vehicle Engineering (TVE), a third-party supplier that has long worked in partnership with Ford Australia to modify standard production cars produced at the nearby Broadmeadows assembly plant.
Along with converting Mustangs to RHD, TVE also takes stock examples of Ford Australia’s unique, rear-drive, six-cylinder and V8 model Falcon, Fairmont, Fairlane and LTD ranges straight from the Melbourne assembly line and puts them through its own factory, from which they emerge as heavily modified sports sedans, station wagons and even pick-ups (known in Australia as ‘utes’ or ‘utilities’).
TVE also fits ‘factory options’ such as electric sunroofs for Ford.
The Australian Mustang has a 4.6 litre quad-cam V8 and its specification includes hydraulically-operated hood, traction control, anti-lock brakes, dual airbags, air conditioning, power windows and locks, remote keyless entry system and a high-performance sound system with in-dash CD stacker.
![]() |
Tickford Vehicle Engineering |
The re-engineering of the Mustang to right hand drive is the most complex manufacturing process TVE has so far undertaken with tooling costs alone more than three times those for the latest XR Falcon sports sedan programme.
The process involves the manufacture of 150 major new components and 200 minor components such as brackets, as well as the modification of a further 50 existing parts. More than 250 documented processes are involved.
“We basically had to develop an entire engineering and manufacturing process. In the end, that is what sets us apart from traditional conversion operations. This is a defined production process, rather than a cut and weld conversion,” TVE managing director David Flint said.
The process involved extensive use of computer aided design to produce unique components, as well as the manufacture of templates to ensure that each vehicle was modified to identical specifications.
The total investment in the two-year programme was about $A4 million ($US2.1 million) and nine prototypes were built, including one crash vehicle and one durability vehicle. Several virtual prototypes were also engineered, incorporating data from the US Mustang development programme.
About 25 engineers worked on the initial project, with six others joining for the launch phase. Twelve production personnel carry out the modification work with each vehicle taking 55 man-hours. TVE managed the whole programme for Ford Australia, drawing on resources in the US.
“For us, it was the best of both worlds. We could be right on top of the development and add a personal, Tickford flavour, while making use of the vast resources of Ford in the States,” Flint said. “That assistance was particularly helpful in terms of testing engineering concepts and running crash data. “We were able to crunch the numbers on the Cray computers in the States and move forward with confidence that the engineering solutions we had put in place were fundamentally sound.”
![]() |
Re-engineering the Mustang to right hand drive is complex and expensive |
The programme produced a number of challenges. One of those was the manufacture of the instrument panel facia which TVE designed in Australia but has manufactured in the United States.
“Because of the low volumes involved it didn’t make economic sense for the Ford plant that produces the Mustang to do the Australian instrument panel. There aren’t many economies of scale with 250 units a year,” Flint said.
The solution was to use the US supplier that had produced the prototype instrument panels during the original Mustang development programme.
“We found that the deal made economic sense to them and it gave us the added advantage of having the IP produced by a small boutique operation,” Flint added.
Left hand drive Mustangs arrive in Australia with some minor modifications already made by the US assembly plant. The vehicles’ tail and head lamps are Japanese market specification, which are closer to meeting the stringent and, in certain cases, unique Australian design rules (ADRs) and the headlamp beams are, of course, oriented for right hand drive. The tail lamps are further modified in Australia to meet the ADRs, while the head lamps are supplemented by a set of high beam lamps.
This process involves the first change to the Mustang’s sheet metal. The front bumper cover is removed and cut to allow the new lamps to be fitted, while the steel beam is also removed and the lamps attached to it on brackets. Two new bezels are fitted over the lamps and new side indicator lamps are also fitted.
Another modification carried out in the US is to install the electric driver’s seat on the right hand (LHD passenger’s) side on the Detroit production line. Other US modifications include the installation of an ADR-compliant windscreen, seatbelts and a Japanese-specification exhaust to meet local drive-by noise requirements.
The conversion process begins with the removal of the engine, gearbox and tailshaft. Inside the car, the seats, instrument panel, carpet and sound deadening material are removed to allow for the necessary modifications to the firewall.
![]() |
Australian Mustang interior |
CAD-generated templates are used to ensure accuracy in the openings cut in the right hand side of the firewall for the pedals and steering column. Openings in the left hand side of the firewall left after removing the steering column and pedal are covered by panels which are bolted and riveted. A structural adhesive and bonding material is also applied to reinforce the structural integrity of the panel. The firewall was extensively tested using CAD tools prior to the final physical crash testing. The repositioning of the steering column and pedals creates a domino effect under the Mustang’s bonnet.
The air-conditioning and heating system has to be moved to the left hand side of the car, which requires a major reworking of the system by an Australian supplier, and the hoses and wiring that serve the air-conditioning system are re-routed to suit its new position. The instrument panel also needs to be disassembled, with the instrument cluster, air ducts, controls and air vents all re-positioned. The passenger’s airbag is also repositioned and tested.
Other modified cabin items include power window switches and bezels, power mirror controls and the mirrors themselves (the concave glass would otherwise be on the wrong side), the sunvisors (for ADR compliancy) and the seatbelt and child restraint anchors, the latter a mandatory fitting in Australia. Once installed on the prototypes, the anchors were subjected to stringent safety testing. The instrument panel fascia was designed by Tickford to be a mirror image of the US LHD instrument panel.
“The fact that we designed the IP ourselves allowed us the luxury of being able to ‘finesse’ the vehicle more as we assembled it. We’ve also added more sound deadening material,” TVE’s Flint said. (This should reduce tyre roar on Australian roads which are mostly finished with a layer of coarse chips thrown onto a coat of bitumen; the resultant tyre noise is the nemesis of many a foreign NVH engineer.)
The carpet requires minor modifications, while the three foot pedals are Australian designs.
“We’ve recognised that often one of the areas that suffers in an RHD conversion is driver comfort, so we’ve designed the pedals specifically for this car,” Flint said.
The central gearbox tunnel is also modified to allow for a footrest for the driver.
“The left footwell in the US Mustang is larger than the right to improve driver comfort, so we have had to modify the right hand side,” Flint said.
![]() |
A test drive and quality review is conducted before a new Mustang is signed off and delivered |
The engine and gearbox in the US-specification Mustang are offset slightly to the right to accommodate the bigger driver footwell, which means more TVE modifications. In order to move the engine and gearbox to the left, the vehicle’s cross member is modified, with brackets repositioned to retain necessary clearances in the engine bay. The steering column itself is untouched, but a new steering rack is sourced from Germany and modified in Australia. The sump also requires modifications to allow for sufficient clearance from the new steering rack, while the brake master cylinder and booster are moved and hydraulic lines re-routed.
Once the engine is installed, the vehicle’s driveline is re-balanced to take into account the re-positioning of the engine and gearbox. Wheel alignment checks are also carried out. The car is quality tested by TVE engineers at each step of the modification process, before moving to Ford’s assembly plant in the Melbourne suburb of Broadmeadows for a final squeak and rattle test.
Finally, a test drive and an “eye of the customer” quality review are done before the new Mustang is signed off and delivered to the dealer.
“The process has been complex and challenging, but we believe that the final product sets a new standard in terms of low-volume right hand drive conversions,” Flint said.