Five years ago, a landmark in automotive engineering went into series production: the Electronic Stability Program (ESP). With this invention, Mercedes-Benz made a major contribution to active vehicle safety. ESP reduces the risk of skids and slides during cornering and keeps a car on track even in extreme conditions, for example on wet or icy roads. Today, this system is standard specification on all Mercedes passenger cars. The foundations were laid by Mercedes-Benz back in the seventies when it developed the anti-lock braking system (ABS) and acceleration skid control (ASR). This led as early as 1987 to the first trials with vehicles equipped with a so-called “transverse slip control” system. Since then, this joint invention by Mercedes-Benz and Bosch has proved itself millions of times over in practice and is also available to other manufacturers. The new C-class is fitted with a third-generation ESP system with extended capability and even more sensitive response.
Arjeplog, northern Sweden, March 1994: on the ice flats of Lake Hornovan, two Mercedes test cars are being put through their paces. One of them is steering a neat and steady course round the circuit. But the second vehicle is having a hard time – the tail keeps breaking away on the treacherous surface, and each time the driver has to countersteer and accelerate to stay on track.
At the edge of the test site journalists from all over the world are looking on. They are witnessing the world debut of an automotive landmark jointly developed by Mercedes-Benz and Robert Bosch GmbH: the test car staying firmly on track is equipped with the active safety system ESP (Electronic Stability Program).
Barely a year after it was presented to the press in Arjeplog, this trailblazing technology went into production at Mercedes-Benz in the S 600 coupé, the first ESP-equipped car in the world. The S-class saloon and the SL roadster followed a few months later. Today – five years on – ESP is standard specification on all Mercedes-Benz passenger cars and is playing an important part in preventing accidents. No other automotive brand equips its range so comprehensively with active safety technology.
The first beginnings: Mercedes patent of 1959
ESP went into production following eight years of intensive research and development. And if the concept phase is taken into account, the total realisation time was more than three decades. As long ago as 1959, Professor Fritz Nallinger, Chief Engineer and Member of the Board of Management of Daimler-Benz, patented a “control device” designed to prevent spinning of the driving wheels by intervention in the engine, transmission or brakes.
The idea was good, but for a long time it remained just theory. Sensors and control systems capable of performing the necessary stabilising operations with split-second speed were not available. Only later, with rapidly advancing microelectronics technology and with the anti-lock braking system (ABS) proving itself in the field, was the way gradually opened for Professor Nallinger’s vision to become reality. Based on ABS technology, Mercedes-Benz now developed acceleration skid control (ASR). ASR intervened in both the brake system and the engine to regulate the play between the longitudinal forces at the tyre and the road surface. This system operated not only during braking but for the first time also when accelerating. ASR made its debut in a standard-production Mercedes in 1981. It was followed by the automatic locking differential (ASD, 1985) and the innovative 4MATIC full-time four-wheel drive (1985).
The common characteristic of these systems is that by monitoring and limiting wheel slip with the aid of state-of-the art microelectronic and hydraulic systems they improve the “longitudinal dynamics” of the vehicle. But the Mercedes engineers were not content with their achievements for long. Soon they were aiming to improve active safety in all situations, for example during cornering, evasive manoeuvres or other vehicle movements which affect transverse dynamics and involve a high risk of skidding.
How well do you really know your competitors?
Access the most comprehensive Company Profiles on the market, powered by GlobalData. Save hours of research. Gain competitive edge.
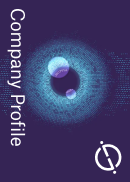
Thank you!
Your download email will arrive shortly
Not ready to buy yet? Download a free sample
We are confident about the unique quality of our Company Profiles. However, we want you to make the most beneficial decision for your business, so we offer a free sample that you can download by submitting the below form
By GlobalDataA logical progression: ABS, ASR and ASD followed by ESP
Thus they embarked on yet another ambitious development project, entitled “transverse slip control”. The aim was to look for ways of identifying skidding movements of the vehicle and combating them by selective intervention in the chassis, engine and transmission. Following extensive computer simulations and preliminary research, the first trials of this system in test cars began in 1987 and in the course of the next few years thousands of kilometres were covered. At the same time the system was also being tested in the Berlin driving simulator: eighty drivers were asked to drive at speeds of 100 km/h on an imaginary road. Tricky icy situations were simulated on four bends, where traction was reduced by more than 70 per cent without prior warning. The result: without ESP , 78 per cent of the drivers were unable to keep their car on track and during the course of the test suffered up to three accidents due to skidding. When the simulations were carried out with ESP however, none of the drivers suffered skids or accidents. Not surprisingly therefore, the Mercedes engineers decided it was time to put ESP into practice. Development of a standard-production version began in 1992. More than 40 engineers from Mercedes-Benz and Bosch took part in the ground-breaking project.
Elaborate sensor system detects every movement of the vehicle
ESP operates by monitoring and comparing: sensors record driver and vehicle behaviour. They send their data to a high-performance microcomputer in which a mathematical reference model is stored. The vehicle’s actual status is compared with what the reference model indicates is appropriate in the given situation, thus identifying any risk of a skid or slide.
In physical terms, skidding is simply a turning of the vehicle about its vertical axis. The faster this rotation, the greater the skidding movement and the greater the risk of accident. In order to accurately measure this rotational speed however a yaw sensor is required, complex technology which, before ESP, was used only in the aerospace industry and which was too expensive and too prone to malfunction for use in the automotive sector. For the Electronic Stability Program, the developers therefore came up with a similar measuring device based on a small hollow steel cylinder. Quartz crystals generate defined oscillations in the cylinder, the pattern of which is displaced under the influence of the rotational movement of the vehicle. This displacement can be counteracted by an electrical voltage, and the electrical voltage can then be used as a measurement of the rotational speed.
As well as rotational speed, the ESP microcomputer processes additional sensor inputs concerning the driver’s intended direction and the car’s actual track:
- The steering angle sensor measures the steering angle as an indication of the direction the driver intends to take.
- The wheel speed sensors register the speed selected by the driver.
- The lateral acceleration sensor detects any sideways drift.
- The yaw sensor is the heart of the Electronic Stability System. It measures the rotational – that is to say the skidding – movement of the car.
- The pre-pressure sensor measures the brake pressure.
The ESP control unit is also connected via CAN (Controller Area Network) data bus with the engine and automatic transmission, and can thus receive current data about engine torque, throttle position and transmission ratio at all times. Via the same databus, ESP can then intervene in the electronic engine and transmission management. In this way, for instance, it can prompt the automatic transmission to switch to winter mode when the vehicle is moving off on a slippery surface.
Permanent surveillance: ESP is operational in all situations
The ESP computer continuously compares the actual behaviour of the vehicle with the pre-programmed ideal values. The moment the car deviates from its ideal line, a specially developed control logic causes the system to intervene with split-second speed, bringing the car back on track. It does this in two ways: by precisely controlled braking at one or more wheels and/or by reducing engine power.
ESP in this way both corrects driver errors and stabilises the vehicle in the event of skids due to wet, icy, gravelly or other adverse road surfaces where normally drivers would have little chance of maintaining control by steering or braking manoeuvres. Unlike acceleration skid control the system is operational under all conditions: when braking, accelerating or coasting.
Rapid intervention: briefly applied braking pressure keeps the car on track
![]() |
Reduces skidding in curves by means of automatic braking intervention. |
One of the strengths of the Electronic Stability Program is the speed with which it works: the sensing of oversteer and understeer, and the automatic braking intervention, are all completed within fractions of a second. For example if the rear of the car starts to swing out when taking a corner too fast, the ESP microcomputer first of all reduces engine power, thus increasing the lateral forces at the rear wheels. If this is not enough to eliminate the skidding tendency, the system also applies the brakes to the outer front wheel. The braking counteracts the critical rotational movement and restores stability. The simultaneous reduction in speed has further benefits for safety.
When ESP corrects the vehicle’s course, it is not a one-off event which is completed after a brief application of the brakes. The stabilisation is an ongoing process which is continuously adapted to take account of situational changes in the dynamics of the vehicle, until the risk of skidding is eliminated. This adaptive control requires the sensors and actuators in the Electronic Stability Program to react and adapt with extreme speed. The system has to cope not only with fast lane changes or patches of black ice, it must also function whatever the carload or tyre tread depth.
ESP was developed and tested with the aid of the most advanced techniques available, which systematically evaluated all potential malfunctions. Using these techniques, every conceivable system error was analysed and methods were developed to eliminate the risk of malfunction. Amongst other things, the individual ESP components carry out self-checking routines at regular intervals. For example the vitally important yaw sensor is checked each time it supplies information, at intervals of just 20 milliseconds.
First generation: complex hydraulic system develops braking pressure
The central control unit of the first-generation ESP system comprised two microprocessors, each with 48 kilobytes of memory, and the hydraulic system consisted of a pressurising pump, a charge piston and a central hydraulic unit. The pressurising pump was required for fast and reliable development of braking pressure under all temperature conditions. The hydraulic unit distributed the pressure individually to the wheels.
Split-second coordination: how ESP works
Since the start of production in spring 1995, the Mercedes engineers have continued to refine and develop the ESP system. One of the first modifications, in 1996, was to increase the microprocessor memory from twice 48 kilobytes to twice 56 kilobytes. In the current version, which went into production in early 2000, the two ESP microprocessors each have a memory of 120 kilobytes and now also control the standard-fitted Brake Assist system.
Second generation: Brake Assist and ESP working together
In 1997 the second-generation ESP system, project name ESP 1.3, went into production. For rapid development of braking pressure, the Brake Assist system was now used. This made it possible to dispense with the pressurising pump and charge piston unit, bringing a weight saving of more than 50 per cent.
Also new was a control logic which further enhanced safety when cornering and braking at the same time: using information supplied by the sensors, ESP 1.3 identifies such a situation and stabilises the vehicle by precise control of the braking pressure at the rear axle. To counteract oversteer when braking on a corner, the microcomputer reduces the braking force applied to the inner rear wheel.
Third generation: fine modulation for enhanced comfort
The third generation of the ESP system, project name MK 20, went into production in May 2000 in the new Mercedes-Benz C-class. Once again the engineers had developed the system a stage further and numerous previously separate components were now combined. For example the electronic control unit and the hydraulic module now form one unit. In future the yaw sensor and lateral acceleration sensor too will be brought together in one unit.
![]() |
ESP components |
The most notable feature of the third-generation ESP is that the response is fast but almost imperceptible to the driver and the brake pressure is extremely smoothly modulated. This is due to new software programming and the use of switchable restrictors in the four inlet valves of the hydraulic unit which allow smoother regulation of the brake pressure. Added to this, the brake booster is now selectively actuated in two stages. In concrete terms, this means that in the event of less severe vehicle instability, when finely modulated small quantities of braking pressure are required, the hydraulic unit alone is sufficient. Only when faced with more serious skids or very fast steering inputs from the driver is more pressure required, in which case the brake booster goes into action to bring the vehicle back under control. During fast cornering, third-generation ESP even takes into account the lateral stiffness of the tyres, giving even more sensitive control.
The Mercedes engineers now also use the yaw control to enhance safety when braking on ice or snow or on surfaces which are slippery on just one side. The anti-lock braking system makes use of the information provided by the ESP yaw sensor to proportion the brake forces at the front and rear axle during cornering in such a way that opposing, stabilising yaw forces are produced. This “ABS plus” braking system is used on the Mercedes-Benz C-class.
Fourth generation: ESP provides platform for hydraulic Brake Assist
The next generation of the Electronic Stability Program is already undergoing testing at Mercedes-Benz and will soon be making its debut in the A-class. In this fourth-generation product, the engineers have further improved the interaction between ESP and Brake Assist and have decoupled both functions from the brake booster. The brake pressure is developed instead by a new two-stage high-pressure pump in the ESP hydraulic unit. On the one hand this pump provides the precise, smooth control required for the Electronic Stability Program and on the other it is so powerful that it can act as a Brake Assist system which and can carry out an emergency braking operation at a maximum pressure of up to 200 bar with split-second speed.
The necessary signals are supplied by the wheel speed sensors, the brake light switch and two pressure sensors in the hydraulic unit, which are already used for the Electronic Stability Program. The diaphragm travel sensor and the brake booster solenoid are no longer required. In other words, like ESP, Brake Assist too will in future operate hydraulically, using the existing ESP infrastructure. This will bring further weight savings – an important consideration not only for compact vehicles like the Mercedes-Benz A-class.
Active safety: ESP makes an important contribution to accident prevention
The invention of the Electronic Stability Program ESP by Mercedes-Benz and Bosch has made an important contribution to active safety. This unique system is able to defuse potential accident situations by identifying delayed or inappropriate reactions on the part of the driver and then efficiently correcting these steering or braking errors. It does this even under extreme conditions, although it can never go so far as to suspend the laws of physics. What’s more, sensor signals and simulations allow the system to identify hazards even before the driver has a chance to react. The system can therefore intervene extremely quickly in an emergency – much more quickly than even the most experienced driver. Thus with ESP, accident prevention is firmly anchored in the safety strategy of the Mercedes-Benz brand.
To see related articles in our Knowledge Store, please follow the links below:-
https://www.just-auto.com/store/products_detail.asp?art=10595
https://www.just-auto.com/store/products_detail.asp?art=10872