
Moving to a 48V architecture in hybrid and electric vehicles offers plenty of promise. It provides about four times the energy recuperation – from regenerative braking – than is available on the traditional 12V system. In this month’s management briefing, Calum MacRae takes a closer look at the emerging technology platform.
Over the past 2-3 years there has been an acceleration in 48V activity from both suppliers and OEMs. The increased activity stems from a development in mid-2011, at the 15th Automobil Elektronik Kongress in Ludwigsburg. At the event Audi, BMW, Daimler, Porsche and VW announced that they would instigate a common electrical architecture standard for their vehicles’ on-board power networks in order to establish a 48V supply to supplement the current 12V supply. As part of the initiative both 12V and 48V subnets were to be connected through a DC/DC converter.
The OEMs hoped that the announcement would precipitate development of systems and components by automotive suppliers and semiconductor manufacturers for the 48V subnet – and as demonstrated by recent activity the move has had the desired effect. In October 2011, the five OEMs further detailed their 48V specification, called LV148 (and aligned to the 12V system’s LV124). LV148 has continually been updated and honed since then.
What’s behind 48V?
As with many automotive technical developments in the past decade – hybrids, electric vehicles, downsized engines, advanced turbocharging, increasing number of transmission ratios, adoption of lightweight materials etc. – the main driver is to reduce CO2 emissions/improve fuel economy in order for OEMs to comply with increasingly stringent legislation.
Moving to a 48V architecture in hybrid and electric vehicles provides about four times the energy recuperation – from regenerative and friction braking – than is available on the traditional 12V system. Moreover, 48V allows for more advanced stop-start – particularly the introduction of coasting/sailing functions that can potentially be used for up to 30% of the time a vehicle is in motion, which, in a virtuous circle, also provides energy recuperation from regenerative braking. Finally, 48V is also offered up due to the increasing loads on 12V supplies caused by the rising electrical power requirements from systems in modern vehicles and particularly those in the premium classes.
How well do you really know your competitors?
Access the most comprehensive Company Profiles on the market, powered by GlobalData. Save hours of research. Gain competitive edge.
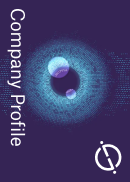
Thank you!
Your download email will arrive shortly
Not ready to buy yet? Download a free sample
We are confident about the unique quality of our Company Profiles. However, we want you to make the most beneficial decision for your business, so we offer a free sample that you can download by submitting the below form
By GlobalDataAt one point, it was thought that 48V hybrid systems would also require a lithium-ion battery or supercapacitor to store up to 15kW of energy in the short-term or an average of 0.5kW over the long-term, requirements that couldn’t be met with a lead-acid battery. But with 48V mild hybrids idealised as low-cost hybridisation, the failure of lithium-ion battery costs to reduce as expected has brought lower cost solutions to the fore. Uppermost among these now seems to be the lead-carbon battery – which according to the ALABC (Advanced Lead Acid Battery Consortium) costs in the range of US$150-200 kWh compared to lithium-ion’s US$500-650 kWh range.
Excuse me 48V, but you look very familiar…
Yes; back in the 1990s there was a similar move by the German OEMs – and joined by others – to migrate to a 42V system driven by the increased loads on the 12V electrical system (Note: a similar driver was present in the 1950s when vehicles began switching from 6V to 12V). But, by the early 2000s momentum was lost – although some developments did make it through, such as the 42V power for the power steering in GM’s dual-mode hybrid SUVs and Toyota’s Crown 42V mild hybrid – as means were found to limit the power consumption of certain components. Such solutions included intelligent power control and the application of buffers, which largely negated the need for the higher capacity, higher cost 42V system.
According to Controlled Power Technologies (CPT) the on-cost for 42V versus 12V was approximately EUR1,000. Furthermore, at the time 42V would have entailed much more added weight than would be required today – back when there was a 42V push three-lead acid batteries would have been required for energy storage but today there are higher power density lithium-ion and lead-carbon batteries.
Now, judging from activity and circumstance this time the promise of a higher voltage is for real. Absent in the aborted move to 42V was the presence of Europe’s CO2 regulations that mean the current 48V proposition is viewed on a very different commercial basis.
The fleet average to be achieved by all new cars is 130 grams of CO2 per kilometre (g/km) by 2015 – with the target phased in from 2012 – and 95g/km by 2021, phased in from 2020. A short phase-in period applies to the 2021 target of 95g/km: 95% of each manufacturer’s new cars will have to comply with the limit value curve in 2020, increasing to 100% in 2021. To achieve 95g/km most manufacturers will need to introduce more electrification or hybridisation to their fleets than has been demonstrated thus far. Furthermore, there are penalty payments for any manufacturer exceeding its limit value, which from 2019 increases to Eur95 for the first gram exceeded.
In the current legislative circumstances the estimated EUR1,000 on-cost associated with a higher capacity electrical system with the potential to improve CO2 emissions by around 15% looks a very good deal indeed.
This article was extracted from just-auto/Qube‘s engine technologies service: Global light vehicle engine technologies market- forecasts to 2029