Joined at the seam
In the final part of this three-part series looking at the trends in global manufacturing, Julian Buckley examines the different joining methods available to carbody specialists to determine if traditional spot welding has had its day
No one seems to know exactly where the term body-in-white originated, although popular wisdom says it relates to the practice of painting parts white in order to prevent corrosion. Having moved on since the early 20th Century – automotive body parts now rely on advanced coatings rather than paint to keep rust at bay – the term has stuck and body-in-white (BIW) remains the name given to the process of constructing a carbody in advance of paint and assembly.
Despite the push to improve fuel economy and cut related emissions through vehicle lightweighting, the majority of global vehicle production still relies on steel for BIW production. This is not to say that cutting overall vehicle weight has been ignored; the research carried out by steel providers to the automotive industry such as ArcelorMittal, ThyssenKrupp, Tata Steel and Nippon Steel has resulted in material grades which are both lighter and stronger. This has in turn made it possible for carmakers to use thinner parts while still improving chassis rigidity and crash performance.
Other characteristics, such as the comparatively low cost, wide availability (of at least common grades) and formability, make steel the default choice for production of car bodies. But in terms of BIW, ease of joining is steel’s strongest selling point. Whether the BIW process is set up to use a manual or automated joining system, steel parts are easily put together using resistance spot welding, a reliable, time-tested process which in most cases results in a bond stronger than the original material.
This is the positive for spot welding, but the methodology also has its downsides. To start, spot welding uses a lot of energy, which clearly adds to overall production costs. Further, despite such automated routines as weld tip checking, cleaning and replacement, spot welding equipment still requires human maintenance. Then there are the issues of accessibility, as weld tips must be able to ‘pinch’ the material to create the weld and related to this, weld flash, which occurs due to the incorrect alignment of the material and weld tips.
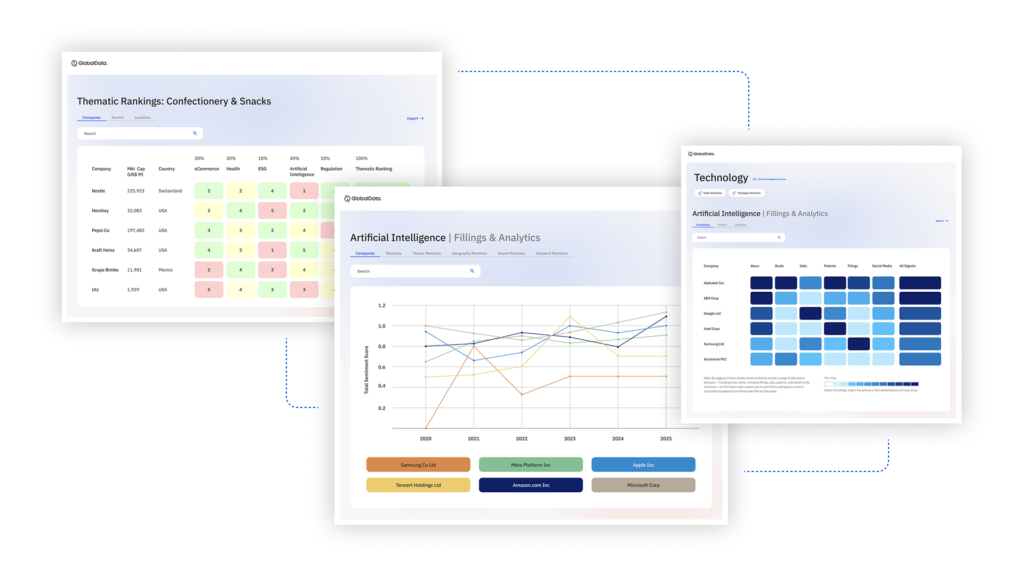
US Tariffs are shifting - will you react or anticipate?
Don’t let policy changes catch you off guard. Stay proactive with real-time data and expert analysis.
By GlobalDataAs covered in the first article of this series, adaptive welding can solve problems related to weld flash, but there is another joining technique which can address each of these problems – laser welding.
Light fantastic
Laser welding has been used in automotive production for about two decades, but over that time the hardware and control technology has been vastly improved. Although the initial capital investment to install a laser welding installation remains high, the quality of the welds and related benefits can serve to offset the initial cost.
Such is the case at the Ford Otosan plant in Kocaeli, Turkey, which uses laser welding to join various steel parts including floorpan assemblies. While there are a variety of options available to BIW specialists using spot welding as a joining solution, such as nugget size (the standard weld is approximately 6mm in diameter, but this can be made larger or smaller as required), a laser-based system can complete welds in a virtually unlimited selection of designs; the design of the weld is directly related to the stresses such as shear and tear which a part will subjected to over its working life. According to Güner Demirural, engineering manager for body manufacturing at Ford Otosan, in analysing the completed floorpan, which in this case is used to support the driver and passenger seats in a Ford Transit commercial vehicle, he found that using a specific laser weld design resulted in a join four times stronger (in the specific direction of stress) than that made using standard spot welding.
This strength delivers a series of benefits, including improved chassis rigidity and crash cell integrity. Additionally, the remote laser welding platform installed at Ford Otosan is able to complete individual welds from a distance of up to 140cm. Instead of moving to and along the work piece to complete each individual weld, this system projects the laser along the seam with only incremental movements of the robotic head. This results in shorter process times when compared to traditional spot welding, while also avoiding accessibility issues as the weld can be made with access to only one side of the part.
Laser brazing
The basic principle behind spot welding and laser welding is the same, in that a pool of melted base material hardens to create the join. Laser brazing is a different kind of joining technique which uses a soldering flux to make a join between two separate parts.
Many carmakers have adopted this method in areas of the BIW process where achieving a smooth final joint is critical to a vehicle’s exterior appearance. In the case of PSA Peugeot Citroën, the French carmaker uses laser brazing in production of the Peugeot 508 sedan and estate models to join the roof section and bodysides. A spot-welded join in the same position is usually hidden using a plastic overlay styled to resemble a roof rail or act as a rain gutter. In the case of the 508, the use of laser brazing has meant that there is a smooth transition between the joined parts, which once the weld is made only requires a minimal amount of rework before being sent through to the paint shop.
Other joining alternatives
Two other joining solutions are available to BIW specialists: riveting and adhesives. These techniques are most commonly used where steel comes into direct contact with aluminium; with the correct catalyst – road salt, for instance – an unsealed joint between the two metals would be a corrosion hotspot. To avoid this situation, BIW specialists building the Range Rover Evoque use rivets to join the aluminium roof and steel bodysides, with the addition of a double coating of sealant between the parts. As Graham Miller, Evoque launch manager explained, the process is not a technological leap but a solid solution to combining the two materials.
Adhesives have the flexibility to be used in conjunction with other joining technologies, or they can be used to bond a complete chassis. An example of the former is being used in production of the BMW X3 SUV at the carmaker’s plant in Spartanburg, South Carolina, where sub-assemblies are both bonded and welded in order to achieve the required level of chassis stiffness and improved driveability.
The ultimate use of adhesive as a joining solution can be found at the Aston Martin production facility in Gaydon, UK, where every model features an aluminium chassis bonded using an epoxy resin adhesive. Using this solution the luxury carmaker is able to build a very stiff chassis, which is most apparent when driving the convertible versions of the cars. In most cases a carbody must be suitably reinforced to make up for having the roof removed. However, a convertible Aston Martin requires minimal reinforcement to control flex and ‘scuttle shake’, such is the inherent rigidity of the bonded chassis structure.
So why don’t all OEM’s use adhesive to assemble carbodies? The short answer is time. Each chassis produced by Aston Martin must be cured in a dedicated oven, a process which while achievable over a total annual production of approximately 6,000 units is impossible to scale up to the needs of volume producers.
The other reason for using adhesive in this particular BIW process is directly related to the use of aluminium as the subframe build material. Although welding aluminium is possible, it is a difficult and time consuming process due to the low melting temperature of the metal. While portions of an Aston Martin chassis are riveted together with fixings that are designed to resist loosening, adhesive bonding is still the joining solution of choice.
Production of the Rapide sports saloon is now scheduled to be relocated back to the carmaker’s Gaydon headquarters in 2012 after two years of manufacturing the model at a dedicated facility within the Magna Steyr plant in Graz, Austria. Like the main manufacturing facility, the Austrian site had a sealed, negative pressure BIW area. This kept dust and other particles to an absolute minimum, which assured technicians that each adhesive joint would be free of imperfections.
The future for spot welding
Does the proliferation of these joining solutions mean that BIW production based on spot welding is nearing the end of its useful lifecycle? In the short- to mid-term, the simple answer is no. While laser welding is a very flexible and very fast joining solution, the capital investment required to install the equipment means that the cost-per-weld is still prohibitively high. That said, as new technology has been introduced the cost of laser welding equipment has been falling and once in place, it’s hard to argue with the speed and reduced energy. Five years ago, a laser welding enclosure within a car plant was a rarity. Now, most large car plants feature at least one laser-based application. A case in point is tailor-welded blanks, which are often fabricated using laser welding, before the panels are pressed and delivered to the BIW hall.
The increasing use of carbon fibre will most likely mean a proportional increase in the use of adhesive as a chassis-to-body panel bonding solution, although curing times will have to be addressed. A move in the right direction are adhesive products which cure at room temperature, but while initially attractive, joints made using this bonding solution are generally inferior to those made using a heat-reactive product cured using dedicated ovens.
As it is, the comparatively low cost and versatility of steel and the improved products being offered by steel producers mean that spot welding and its related solutions will remain a core part of the BIW process. But for the future, as the price of laser technology continues to fall, spot welding technology will have to advance if it is to remain the default solution for joining in automotive production.
See also: Parts 1 & 2 of this series looking at quality (manufacturing processes) and globalisation strategies
February 2012 management briefing: key trends in global automotive manufacturing