Automotive production looks to go global
In the second part of this three-part series covering trends in vehicle manufacturing, Julian Buckley looks at the problems related to building a ‘global’ vehicle before deciding that production plants are the truly global force behind world cars
The World Bank estimates that losses related to the 2011 floods in Thailand will amount to US$45bn. This figure puts the disaster fourth in terms of overall cost, behind such infamous events as the Japanese earthquake and tsunami disaster of last year, the earthquake in Kobe, Japan (1995) and Hurricane Katrina (2005).
The flooding was caused by unusually heavy monsoon rains being joined by a tropical storm, which together were compounded by the influence of the La Nina global weather system. The heavy rains initially caused flooding in the north of the country before spreading southwards to eventually inundate parts of Bangkok. In total, 65 of Thailand’s 75 provinces were declared disaster areas due to the floods; the same provinces where a considerable portion of the country’s manufacturing infrastructure is located.
One of the companies worst affected by the flooding was Honda, which operates motorcycle, vehicle and part production plants in Thailand. At the height of the disaster, the Honda facilities located in the Rojana Ayutthya industrial park were under three metres of water. Such was the nature of the flooding that it took weeks for the waters to recede, at which point it was announced that virtually all of the equipment at these plants would have to be replaced; a six-month timeframe was outlined with regards to a production restart.
The flooding had a knock-on effect at Honda manufacturing sites around the world. According to Rajeev Wasan, senior vice-president of manufacturing at Honda Siel, the joint-venture operation which builds, imports and distributes Honda vehicles in India, parts shortages due to Thai flooding had a severe impact on local production; at one point, part supply issues reduced vehicle output to less than 25% of capacity. The effects of the flooding extended beyond India and south-east Asia. At the Honda plant in Swindon, UK, production volumes were reduced by 50% due to part supply issues related to the Thai flooding, while production at the Honda plant in Alliston, Ontario was also affected.
How well do you really know your competitors?
Access the most comprehensive Company Profiles on the market, powered by GlobalData. Save hours of research. Gain competitive edge.
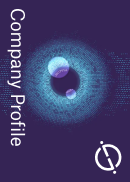
Thank you!
Your download email will arrive shortly
Not ready to buy yet? Download a free sample
We are confident about the unique quality of our Company Profiles. However, we want you to make the most beneficial decision for your business, so we offer a free sample that you can download by submitting the below form
By GlobalDataThis, then, is the reality behind global production. While companies such as Ford claim to be making ‘global’ vehicles, in that Focus models built in China, Germany or the United States are largely the same vehicle, the global descriptor refers to the body, chassis and powertrain. Within this, vital electronic components are still sometimes delivered from a single, centralised source. Should that supply chain be interrupted for any reason, multiple lines around the world would slowly grind to a simultaneous halt.
Broken supply chain
The Japanese earthquake and tsunami caused a series of part supply issues for international OEMs, but one particular case serves to highlight the fragility of some part supply deals. As a direct result of the disaster knocking out power and water supplies, work at Hitachi Automotive Systems’ Sawa Works, located north of Tokyo, was understandably brought to an immediate halt. In addition to other parts, including motors and invertors for hybrid models, the plant also delivers engine airflow sensors – at that point in time, Hitachi was reported to control a staggering 60% of the global engine airflow sensor market, delivering the components to a series of major OEMs around the world.
As inventories of the sensors quickly dwindled over the days following the disaster, carmakers were forced to slow production in order to conserve what parts they had in stock. In the US, GM reduced output at its pickup plant in Shreveport, Louisiana. On the other side of the Atlantic, PSA Peugeot-Citroen elected to reduce output by up to 50% at its plants in Vigo, Spain and Aulnay, France, in order to extend its standard 10-day inventory of the air-freighted parts.
Companies such as Siemens and Robert Bosch make similar sensors, but as anyone familiar with the automotive industry will confirm, there’s no part in a car that’s redundant, which makes testing a vital and time-intensive process. Speaking before the disaster about plans to adopt locally-sourced parts, Ismail Sumer, executive factory manager at Honda Turkiye, noted that it would take a minimum of six months to test and validate a given part.
The Japanese disaster happened on March 11, 2011. On April 4, the Hitachi Sawa plant restarted production at a reduced 70% output – two weeks later, the plant was back up to pre-disaster output levels. The moral of the story is this: While building the same model around the world can offer reductions in terms of manufacturing cost, supplying parts via a single supply stream to each of these production locations is simply asking for trouble. It’s worth stating again, as cars have no redundant parts, then all parts are vital. From strikes to the world’s most expensive natural disasters, part supply disruption is a one of the greatest risks to achieving true global production. As a final note, two regions of PSA production, South America and China, were unaffected by the production problems at Hitachi Sawa, as engines produced there use different standards. Such is the value of diversification.
What is global?
If the term ‘global’ is still too broad a definition to apply to full vehicle production at any OEM, are there any elements of the automotive manufacturing process which can be called global?
In a recent interview, Michael Larsson, group vice-president, global product group, robotic systems at ABB, said that two different forces are at work when it comes to the increasing globalization of robotics. First, when an otherwise international OEM moves into a new region, perhaps as a JV partner to a national carmaker, the incoming OEM will immediately look to replace the current production processes with those that are in place at sister plants in other regions. This is largely due to OEM policies which insist that plants, whatever the location, use the same production processes, which enables easy adoption of the OEM’s production system.
The other mechanism driving such cross-plant similarity is cost. Larsson stated that while companies still order single installations, savings can be achieved by installing the same system across a number of facilities; the initial investment would be higher, but proportionally less than ordering a series of bespoke units.
Safety is a second area which is benefitting from the global nature of automotive production. Sick Sensor Technologies, headquartered in Freiburg, Germany, has built up a catalogue of over 25,000 safety-related products which are used across a range of industries. For automotive, the big sellers are light curtains, primarily used to restrict access to cells and laser scanners, which have various uses including part identification and motion detection.
Like ABB, Sick has a series of offices around the world which offer regional support to various industry sectors – in fact, safety related consultancy work represents 15% of the company’s turnover. In terms of automotive, the benefit is that safety – essentially accident prevention – is the same everywhere. The system needed to stop an employee inadvertently entering a cell where an active robot is working is the same whether the factory is in China or the Czech Republic. In terms of that particular parallel, whether a national company in China would be required to install an advanced safety system is debatable, but by most accounts safety issues are gaining a higher priority in the Chinese workplace.
True globalisation
So in today’s world market, is there such as thing as a global car? The launch of the second-generation Fusion saloon in the United States, which is the forerunner of the next-generation Mondeo due to be launched across Europe in 2013, and the existing Buick Regal and Opel/Vauxhall Insignia model share both point to the idea that global cars are already here. But while these and other vehicles appear to be global, even down to the chassis structure, there remain a series of minor differences which set them apart by region.
Although it’s exciting to suggest that a car is global, it is not the products but where they are built that deserve this description. The Toyota Production System and others formulated around the same idea offer a blueprint for vehicle build processes which can be endlessly copied. In fact, production systems result in such commonality between plants that it’s a point of pride amongst production experts that they can walk into any company operation and immediately understand the manufacturing set-up, to the point of even knowing how that day’s work is progressing. Then there are individual elements, such as the tooling sets used in stamping press lines, which can be reproduced to incredibly fine tolerances using the original CAD diagrams, which could have been developed next door or 11 time zones away. And as mentioned, this cookie-cutter theme translates through to robotic installations and beyond, defining such activities as the timings for lineside part delivery and even the ideal number of steps an employee should take within a production line cell to complete a given task.
Then there is the customer. While it’s beneficial to deliver nearly the same product in every region, do people really want to drive identical cars? In one word the answer is ‘no’. European drivers value vehicle handling as much as those in China and India prefer – and need, due to road conditions – a softer suspension set up. While it might be good marketing to put forward the claim of a ‘global car’, there should be no shame associated with marketing the idea of the ‘global factory’.