Building in vehicle quality
In the first of a three-part series on automotive manufacturing, Julian Buckley looks at the ways international OEMs are using process automation to improve overall vehicle quality to grow sales and retain existing customers
The perceived quality of a finished vehicle has always had a disproportionate influence in the vehicle buying decision. Elements such as how the interior plastics feel to the touch and the sound of a closing door play a critical role in convincing a prospective buyer to sign on the dotted line. Move beyond the buying decision and how well a vehicle ages can influence whether or not the customer would consider buying another car from the same brand. ‘I’d rather push a Ford than drive a Chevy’ is not just a saying, it’s a way of life for Ford aficionados, based on the perceived power and longevity of the vehicles.
Carmakers can achieve this level of satisfaction by delivering vehicles which exceed customer expectations and this can be traced back to how well a given vehicle is designed and manufactured. As new technologies have been introduced into each area of automotive production, both perceived and actual quality levels have increased to where quality is not simply wanted, but expected. Failure to surprise and delight over a period of ownership could mean multiple future sales lost due to quality issues.
While interior materials have an immediate effect with regards to perceived quality, a customer will only know if the body of a given vehicle meets a sufficient standard many years after the original purchase. In fact, it is very likely that the second or third owner will ultimately judge whether a car’s bodywork could be considered fit for purpose. Of course, extended bodywork non-perforation guarantees can go a long way to reassuring a new car buyer that the OEM has confidence in the vehicles it is building, but to do this OEMs must minimise the the opportunity for corrosion to develop, and this starts in the body shop.
There are a series of joining technologies available to body shop technicians, but laser welding and brazing, adhesives and others are either expensive or simply unsuitable for the selected material or production timeframe. This means that cars, SUVs and pickups are still largely made from steel parts, which are joined using standard resistance spotwelding techniques. Over the recent past, little has changed in the area of spotwelding, but in order to improve vehicle body quality, Mercedes-Benz in Tuscaloosa, Alabama has installed a new system, as Markus Schaefer, CEO and president, Mercedes-Benz US International (MBUSI), explains: “We have installed a new welding process, adaptive welding. It’s very good. There are no more sparks. It eliminates the dirty jobs associated with welding and you get a better quality, more stable weld.”
A standard spot weld is made when a concentrated electrical charge is passed through two sheets of metal. The current heats the material to create a melt pool and as the melt solidifies, the join is created. If the sheet metal doesn’t have a perfect fit or the weld gun is not exactly aligned to the material surface, additional material is sometimes destroyed in the welding process. This creates the familiar shower of sparks, which is referred to as ‘weld flash’. Although spectacular, the flash can leave a small area of burn around the weld. The dirty work Schaefer referenced was the grinding process needed to remove these deposits as if they are left on the body they can promote premature corrosion.
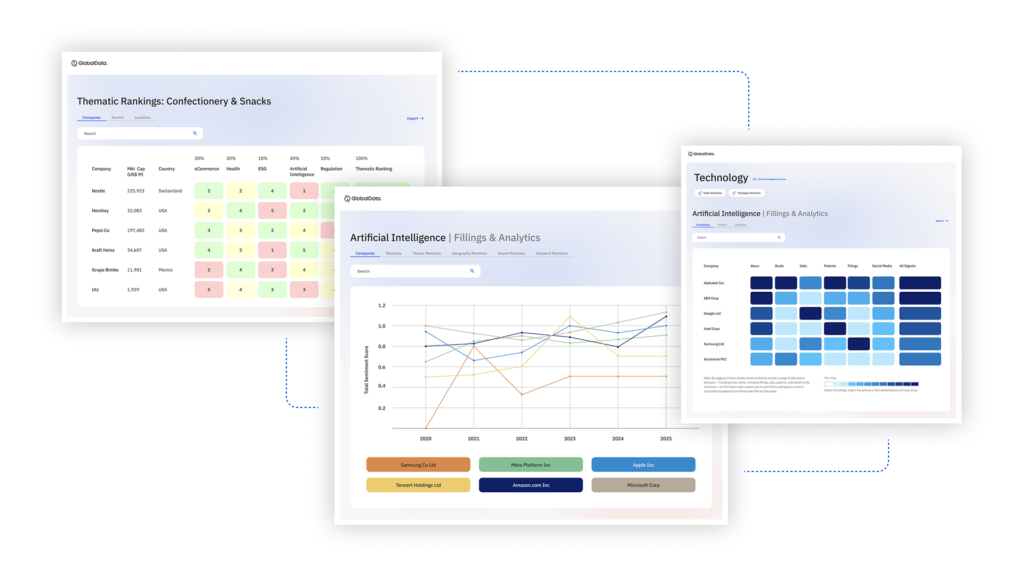
US Tariffs are shifting - will you react or anticipate?
Don’t let policy changes catch you off guard. Stay proactive with real-time data and expert analysis.
By GlobalDataThis is where adaptive welding offers the greatest benefit. As the name suggests, it is a self-calibrating system which employs sensors to adjust the weld parameters. This is a fully-automated system which all but eliminates weld flash, to the point where it’s unnecessary to wear safety goggles in the weld shop. Norbert Wagner, senior series planner at MBUSI, states that the original goal was to have adaptive welding reduce the occurrence of weld flash to 5% of all welds. By late last year the shop had far exceeded this target; now just 1.4% of all completed welds require rework due to weld flash.
It’s simple to understand where the benefits can be realised in terms of quality using adaptive welding. Whereas a car body manufactured using standard spot welding might show the first signs of corrosion due to weld flash deposits after perhaps only four or five years, the new system could potentially eliminate rusting due to weld flash over the operational lifetime of a vehicle. Adaptive welding has been put in place for production of the new M-Class SUV, but it is probably going to be used in production of the next-generation C-Class, due to start at MBUSI in 2014. While a customer might expect that their Mercedes-Benz to be rust-free over the lifetime of the vehicle, there can be no doubt that adaptive welding represents a step change in ensuring that a delivered vehicle remains in peak condition for as long as possible.
Automation matters
As the depth, or amount, of automation increases across a car plant, there is a proportional increase in the quality of the vehicles produced. This is not to say that all plants should be 100% automated, as it would be impossible to reproduce the craftsmanship involved with working the leather or wood elements that come together to create vehicles such as the Bentley Mulsanne using automated systems. Balancing the cost of increased automation versus manual labour is also a main concern, which is why at India’s Maruti Suzuki up to 80% of all joins in the body shop are completed manually.
Yet at both these very different OEMs, the depth of automation is slowly increasing, driven by the need for improved quality. In the case of Bentley, the carmaker has installed a brand new body shop at its facility in Crewe, UK, for production of the new Mulsanne. The new body line is arranged in a ‘fishbone’ pattern, where preassembled subassemblies are delivered down shorter lines to the main line for addition to the body. There is a still a lot of manual work involved in producing a Mulsanne body – the hand-brazed and finished join on the C-pillar is a highlight – but the depth of work completed by robots is on the rise. In adding this automation, Bentley is looking to improve torsional chassis stiffness to achieve improved vehicle crashworthiness. The test figures highlight the success of the programme so far: roof crush performance: +200%; side pole crash: +24%; front-end crash: +36%; and side barrier crash: +32%. It goes without saying that a stiffer chassis also improves the driving experience, which in of itself is a key factor when determining vehicle quality.
Meanwhile in New Delhi, India, Maruti Suzuki will further increase the depth of automation on various production lines, notably those producing the new Dzire saloon and the Suzuki Alto and its derivatives, the Mitsubishi A-Star and Nissan Pixo. It had long been anticipated that Maruti Suzuki, which commands almost 50% share of the new car market in India, would stick with manual labour at its plants until rising wages made a stronger case for further process automation. But the company has been forced to bring these plans forward due to two key reasons – the availability of foreign brands in the Indian market has made the local car-buying population more demanding in what it expects from a new vehicle, while exports to markets outside India have also demanded the same related increase in quality.
What Maruti is looking to achieve with this added automation is process repeatability. With the best will in the world, operations completed using manual labour are likely to be affected by any number of skill-related inhibitors; what makes us human also makes us terrible at repetitive tasks. Completing processes using even the most basic robotics can mean vast improvements in part quality, which ultimately translates to a better vehicle. Despite the prohibitive level of capital investment needed to purchase and integrate a robot or robotic cell into a production line, there are savings to be made. Consider this – robots don’t need ventilation or lighting to continue working. Further, using robots to construct vehicles eliminates the ‘built on Friday’ problem, where overall quality could be affected by a worker not concentrating on the task in hand.
Cost concerns surrounding the implementation of automation must be set aside in order to achieve the required level of quality. In the case of Bentley, production director Dave Hudson says that he weighs up the benefit of each new automation addition in terms of process efficiency and what it can improve on the final product. Despite this commitment to achieving the best value through automation, cars produced by Bentley should represent the pinnacle of quality. As such, if a gold-plated robot would improve the vehicles, surely this would have to be considered?
In the case of Maruti Suzuki, would Nissan or Mitsubishi have been willing to take delivery of their respective models – cars which would be distributed to various markets around the world – had Maruti maintained its pre-robotic build quality? Although it’s impossible to calculate an exact quantitative response, in all likelihood the answer is no.
Commercial success
Automation is underwriting the same drive for quality at the Ford Otosan joint-venture in Kocaeli, Turkey. The plant, which produced its last passenger vehicle in 1999, now exclusively manufactures Transit and Transit Connect commercial vehicles. While some plants producing passenger vehicles can boast a relatively high number of model derivatives, most can’t compare to the approximately 700 different variants produced on just the Transit production lines. Quality is a top-level concern at Ford and it is the ever-increasing depth of automation that has helped to improve overall finished vehicle standards in relation as the number of vehicle variants has increased. According to Güner Demirural, engineering manager for body manufacturing, the first production line installed in 2000 was 40% automated. This has risen to 45% with the installation of the latest line producing Transit Combi versions, and the percentage of automated processes will further increase when a new plant, located adjacent to the existing facility, is put in place in 2014 for production of an all-new commercial vehicle.
While the overall quality of modern vehicles has benefitted from the addition of automated processes, it is not the only driving factor. In a factory such as that operated by Ford Otosan, an enormous number of individual parts must be delivered to the assembly line and any mistake would clearly affect quality. As an example, Demirural points out the complexity behind airbag installation. In addition to being a safety-critical part, airbags have different specifications related to regulations in the destination market, standard and staggered inflation rates and plastic and leather covers in all trim colours.
“If possible we will sequence the airbags. If not, the operator uses a barcode reader. There are boxes by the line and each has a light on top of it. As the vehicle enters the station, a light over a box starts blinking and the operator takes a part from that box. They apply the part and read the barcode on the part and the vehicle identification number. If they match, the vehicle can move. If not, it won’t move.” It’s an error-less system which beyond safety, assures that an airbag with a blue plastic cover isn’t fitted to a vehicle with a brown leather instrument panel, which while obviously vital to the customer is equally important to internal metrics as any rework adds to the final production costs.
Automated sound reduction
Interior cabin noise – or the lack of it – is a critical factor when determining a vehicle’s overall quality level. In order to reduce cabin noise, most models have a number of carefully-placed sound insulation pads positioned around the bare metal chassis in order to reduce vibration and related sound. At the Peugeot Citroën plant in Rennes, France, paintshop director Stéphane Gélas says that the 607 sedan incorporated up to 15kg of sound insulation material in order to achieve the required cabin ambience.
The 508 range, which replaced both the 407 and the 607, is the first to benefit from a new type of sound insulation. Instead of pads, this model uses an epoxy-type material which is automatically applied to the chassis during the course of the paint process. In addition to being a better material in terms of noise reduction it is also lighter, which means that the 508 has a shed a few excess kilograms, reducing emissions and improving fuel economy.
Gélas says that it is important that passengers in the 508 are unaware of how PSA achieved such a quiet cabin – in his words it should be “an unknown application”. But once again, a premium quality level can only help in convincing a customer to stick with the same brand when it comes time to trade-in their current vehicle.