According to Modern Casting magazine’s annual survey (www.moderncasting.com), world production of metal castings was expected to exceed 100 million metric tons in 2007, the latest year for which good estimates are available. Industry guru, Kevin Kirgin – founder of Stratecasts Inc., Fort Myers, Fla. – puts 14m metric tons of this production in the United States (US) at a value of approximately $32.3bn. Kirgin says the value is expected to have risen to $34bn in 2008 and will rise to $42bn by 2017. SupplierBusiness reports.
Official figures from Eurostat (epp.eurostat.ec.europa.eu) put a value of approximately €31bn ($45.5bn) for European castings production in 2004, the latest year for which EU-wide figures are available. Applying the same growth to this figure as projected for the US total, gives a forecast of €33.5bn ($49.2bn) for European production in 2008 and €40.3 ($59.2bn) by 2017. Of this total, the most important global metalcasting market is the Automotive Sector.
For example, according to the United States’ Department of Energy, automotive takes up 35% of all US metalcasting production. If you add to this, the figure for Internal Combustion Engine manufacturing, the sector accounts for 40% of casting end-use in the United States. Applying this percentage to the above total values makes the automotive metalcasting sector in 2008 in the US worth $13.6bn and in Europe €13.4bn ($19.7bn).
Looking globally, US production represents about 14% of the total. A simple calculation therefore gives a very rough estimate for the total value of world metalcasting production of $230.7bn in 2008. And if the global automotive sector percentage of this total is the same as the US (40%), it values the Automotive Metalcasting sector at $92.3bn in 2008. Although these calculations are little rough and ready, they are still sound enough to make the point that automotive casting is a significant business sector – the total being about the same as the GDP of Kuwait.
It is not surprising that automotive is the single largest sector for metalcasting usage. A high proportion of a modern car is built using metalcasting processes. Components such as cylinder heads, crank cases, engine blocks, transmission housings, pumps, bearings, suspension & body work parts and wheels are all produced using casting methods Consequently, metalcasters’ businesses across the globe are very sensitive to changes in the automotive market.
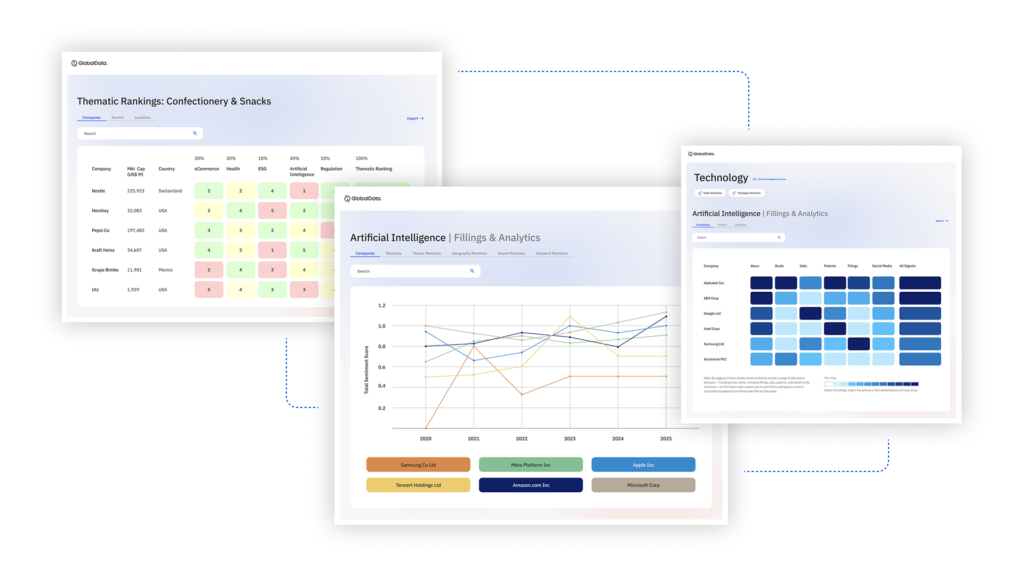
US Tariffs are shifting - will you react or anticipate?
Don’t let policy changes catch you off guard. Stay proactive with real-time data and expert analysis.
By GlobalDataAnd considerable change is underway. The production map of the global automotive industry is re-focusing on emerging markets and production in lower-cost countries. At the same time, global legislators are requiring the automotive sector to find solutions to the environmental problems posed by greenhouse gas and carbon dioxide emissions. And all of this in a highly competitive and price-sensitive context, where customers are demanding more equipment, better performance and greater fuel economy from their vehicles.
The situation was highlighted by Joseph Carpenter Jr. of the US Department of Energy at the American Foundry Society’s May 2008 CastEXPO in Atlanta, Georgia. “There’s a demand by the consumer for a better performing vehicle. At the same time, the consumer is demanding more goods, values, in the vehicle – DVDs, power windows, these sorts of things – and they all add weight. Most people are surprised to see that since about 1985, the average weight of a light weight vehicle has actually risen. You would think well, no, no cars have come down and got smaller – ah… but the weight has gone up. And at the same time we’ve demanded more performance from the manufacturers in our vehicles. We actually want a 6500 pound SUV to be able to accelerate from 0 to 60 in ten seconds. Any of those that lived through the seventies and ever saw a Volkswagen bus accelerating – it took about 30 seconds! That was the norm. But we wouldn’t stand for that these days. We want that performance. Now all those things add weight and they cost energy!”
As a result of these pressures, OEMs and their suppliers have in the past engaged in research and development to find ways of increasing power and reducing weight of the car’s core components. And so performance improved, and the overall weight of the vehicle climbed only relatively slowly despite the extra equipment.
But the automotive sector today is operating in a new context. Soaring oil prices, legislation to cut emissions and penalties if fuel economy targets are not met are driving the market. As a result, the need to reduce vehicle weight and improve fuel economy has intensified. New engine technologies, new production methods, new ways to meet changed consumer demands, and new vehicle designs & concepts are being explored and introduced by the OEMs.
For example, GM vice chairman Bob Lutz has said that: “The company will be making much greater use of lightweight metals in upcoming models. GM’s strategy is to be able to maintain the relative size and functionality of today’s vehicles, which are popular with consumers, while improving their fuel economy by new technology and using lightweight materials such as magnesium and aluminium.” This strategy is part of GM’s desire to find a way of offering consumers big, powerful vehicles with the same utility and space of current SUVs, whilst at the same time delivering dramatic improvements in fuel economy and emissions at reasonable cost.
And this is causing a new round of innovation by the OEM’s suppliers in the metalcasting sector. Engineering solutions are being developed which will produce thinner, lighter-weight, more-sophisticated castings and more complex parts created in a single process. One such effort is the FreedomCAR programme sponsored by the US government. (see: www1.eere.energy.gov/vehiclesandfuels).
Joseph Carpenter Jr again: “The FreedomCAR partnership is a partnership between the traditional US-based manufacturers (GM, Ford and Chrysler) and the energy supply industry (Shell, BP, Chevron, Texaco and so on) on the fuel side.” Alongside the fuel-related research, is work on “…the light-weighting of materials, and casting is, and will continue to be, a major part of this effort. The casting of aluminium, magnesium or zinc. These are the major light-weighting materials.”
Carpenter then went on to talk about why casting is central to this research.
“Why casting? Well primarily cost. If you look at the goals of the FreedomCAR programme, we are looking for a 50% reduction in weight. A 50% reduction in weight of the structural components, not the propulsion components, at the same cost, at the same performance and life-time. And the real issue is that cost.” In Carpenter’s view, the best way of hitting these cost targets is by developing advanced materials, casting technologies and processes. The drive for weight reduction has also led to the development and successful introduction of crash-resistant structural components from cast metal.
These targets are not just desirable goals for US OEMs. All manufacturers need to achieve such results if they are to gain success in the evolving global passenger car market. The way forward therefore is to use new light-weight alloys of magnesium, zinc, and aluminium to reduce weight in new areas and applications, such as in structural components. Consequently, considerable research and development has been, and will continue to be, done. As a result, structural components of lightweight cast metal are now appearing in mass market passenger cars.
High-end vehicles such as the Audi TT have recently been seen with cast structural parts and others are following. Turning from the materials involved to casting processes and manufacturing techniques, new technologies are also emerging. These enable complex features to be cast into a part in a single process, rather than having to add these later at extra cost in time, weight and money.
Metalcasting innovation has become a key factor for suppliers and OEMs alike. A further result of the change in the passenger car and the technical developments needed to fit vehicles into today’s market and legislative framework, is a climb in the price of raw materials.
Magnesium, for example – which is mainly sourced from China – has seen a steep rise in price from below $1 per 450gm (1 lb) in 2003 to nearly $2.5 per 450gm in July 2008. This increase is forcing manufacturers and suppliers to look for new sources and casting techniques to reduce the cost of cast magnesium parts.
This impact on OEMs, their suppliers and customers is likely to continue. So yet again there is a need for companies in the sector to work hard to find technical responses to minimise the effect of this trend.
One final area of concern facing Automotive Metalcasters (AMs) lies in the environmental impact of their operations. Metal casting and foundry work is energy intensive and generates contaminated waste and regulated emissions in significant quantities. In today’s context of tightening legislation and soaring energy costs, suppliers and OEMs need to develop effective ways of reducing both their environmental impact and energy costs. And this is yet another area where innovation is needed to create a commercially viable way ahead.
Clearly, Automotive Metalcasters are facing a challenging future with problems on many fronts which need to be solved. But considerable opportunity is also there, as the figures above show. Also, the global market for automotive roducts is projected to grow significantly. And since a large proportion of a vehicle’s components are made by metalcasting, new business and market share are there to be taken.
A number of strategies are emerging which will enable the AM industry to move ahead with confidence. This report looks at the industry, describes the issues and market context in more detail and outlines some of the solutions being developed to meet these challenges.
SupplierBusiness