Amerityre Corp’s full-size non-pneumatic [no air] passenger car tyre has passed the Federal Motor Vehicle Safety Standard (FMVSS) 129 testing. The tyre is made from a proprietary polyurethane elastomer compound. In April 2005, the company said its temporary/spare tyre for compact to mid-size vehicles had passed the same standard.
FMVSS 129 is the applicable US safety standard for new, non-pneumatic tyres that must be met before the tyres can be offered commercially. As a result, its tyres are now eligible for use as spare tyres on about 90% of all passenger cars produced.
Amerityre was founded in 1995 by Richard Steinke. Prior to starting Amerityre, Steinke was involved in developing polyurethane technology for ski boots, running shoes, skateboard and roller blade wheels, wheelchairs and scooter tyres. Amerityre’s first major breakthrough was closed cell polyurethane foam – a lightweight material with load bearing capabilities. The company currently manufactures and markets a range of ‘flat free’ closed cell polyurethane foam tyres for bicycles, wheelbarrows, hand and utility carts, ride-on lawn mowers and golf carts. Its polyurethane elastomer automotive tyre development began in 2001.
Amerityre believes the newly developed tyres will provide consumers with a more reliable temporary/spare tyre. The company says drivers won’t need to worry about losing air pressure in these tyres. They will always be ready in the event of a flat tyre.
In an interview with just-auto, Matthew Beecham talked with Elliott N Taylor, executive VP/general counsel for Amerityre Corporation about the company’s innovations and prospects.
How well do you really know your competitors?
Access the most comprehensive Company Profiles on the market, powered by GlobalData. Save hours of research. Gain competitive edge.
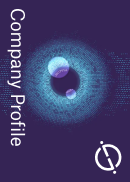
Thank you!
Your download email will arrive shortly
Not ready to buy yet? Download a free sample
We are confident about the unique quality of our Company Profiles. However, we want you to make the most beneficial decision for your business, so we offer a free sample that you can download by submitting the below form
By GlobalDatajust-auto: With FMVSS 129 under your belt, when can we expect to see your non-pneumatic fitted as spare to a production vehicle?
Elliott N Taylor: “Our plan is to take our prototype tyre to the OEMs so that they can conduct their own testing. That would be testing in addition to the FMVSS standard, probably relating to wet/dry traction, stopping and a series of other tests. They would want to ensure the tyre meets their tyre performance characteristics before they would offer it as an OE feature. Our expectation is approximately 18 – 24 months to get the car companies on board and have it available potentially as original equipment.”
just-auto: Where does Goodyear fit in?
Elliott N Taylor: “It doesn’t fit into it anymore. Four years ago, we were involved in a joint development project in which Goodyear was testing our compounds for use in a pneumatic passenger car tyre. Two years ago they elected to give us a friendly release from the development. Although we believe Goodyear was pleased with the performance of those materials, we elected to proceed alone and continue the development of the pneumatic polyurethane passenger car tire.”
just-auto: I read somewhere that you expect your system to be able to meet the FMVSS 139 standard?
Elliott N Taylor: “Yes. We believe that our first prototype tyres were very close to meeting that standard and we’re current working on that standard.”
just-auto: How will you actually enter the market in two years time?
Elliott N Taylor: “With respect to the passenger car tyres, we believe that consumers are interested in a tyre with run-flat performance characteristics. Therefore, we believe that whoever we license the manufacturing technology will want to promote those benefits to the consumer. We have a couple of trade names – Arcus and Elastothane that are important to the technology.
“Arcus is the tyre designed patent that permits the tyre to run without air and Elastothane is the name we have given to the polyurethane material. Although a tyre manufacturer may give the tyre a different name, we would expect them to promote the fact that they are using Arcus technology or Elastothane technology in manufacturing the tyres. We believe that our manufacturing process will give the consumer a well-tuned and balanced tyre to promote a smoother ride. We believe that we can engineer the compound to give them the tyre performance they want. The tyres are safe and can be recycled.”
just-auto: Another clear benefit to the consumer is the fact that the spare tyre doesn’t lose pressure.
Elliott N Taylor: “We had a bet at our plant that if we went out and checked our spare tyre, it will be low if not flat. Most of the tyres in the trunks of the vehicles at our plant were at around 18 – 20 psi so they had lost more than 10psi, given that 32 psi is the average. Most people are going to have a spare tyre that has some air in it but it will be low. The truth of the matter is that people aren’t checking their air pressure. They need a tyre that will compensate for them not checking their tyre pressure.”
just-auto: The benefits are very clear and well publicised, but there are always sceptics. What are your sceptics saying about your tyre?
Elliott N Taylor: “The sceptics are basically those who had experimented with polyurethane when tyre companies tried to make polyurethane car tires several years ago. They are concerned about the material melting at high temperature and wet-dry traction. It is true that a lot of the polyurethane materials they used early on had problems.
“We have engineered our polymers to run at high temperatures. However, in testing, our polymers run at temperatures at lower than rubber. We have been able to engineer this polymer to run cooler than rubber for a couple of significant reasons. One, we believe, is based on the formula we have developed and the other is based on the amount of air you have within the material. We are not talking about huge amounts of air, but microscopic pockets of air that develop during the manufacturing process. They may be microscopic, but all of those air bubbles are potential heat sources. We believe that the more entrapped air you are able to remove from your polymer, the cooler it is going to run. And heat is a big enemy to rubber. We’ve been able to show that our polymer consistently runs coolers. This is basically because we get a lot of the encapsulated air out of the material prior to manufacture.
“The concept of a polyurethane tyre is already accepted. How viable that concept remains is conditioned on satisfying some skeptics. But we believe we have developed the concept to the point where the sceptics can be convinced. As more and more people learn about the technology, more and more manufacturers experiment with it and look at our new manufacturing technique, I think that you will see a lot of conversion.”
just-auto: Do you have forecasts for this technology?
Elliott N Taylor: “We know that it will take time for people to embrace this technology. I believe that as we come up with some prototypes that meet the FMVSS 139 standard, we will have more companies wanting to license it.”
|