Toyota expects to train up to 1,000 employees a year at its new EUR16.3m pan-European production training centre – dubbed E-GPC (for European Global Production Centre) – which was officially opened on Thursday.
The centre, adjacent to the automaker’s Corolla and Avensis manufacturing plant in Burnaston, Derbyshire, is Toyota’s fourth world-wide. The first opened in Toyota City, Japan, in 2003, a second now operates in Kentucky, US, handy to the main Camry factory there, the third is now up and running in the UK and a fourth, outside Bangkok, Thailand, where Toyota now bases Hiace light pickup truck production and is rolling out a range of utility vehicles specially designed for Asian markets, opens “shortly”.
With 52 manufacturing sites in 26 countries, Toyota established its Global Production Centre (GPC) system in Japan to create a more uniform training system and, initially, to rapidly train mid-level managers. The UK GPC, employing 16 trainers out of a total staff count of 18, will train at all levels, beginning mainly with plant line operators.
Toyota officials at the official opening said GPCs – the Kentucky facility is actually called the North American Production Support Centre (NAPSC) – have supplemented, not replaced, the original ‘mother plant’ training and quality management approach.
Under that system, used by most Japanese automakers, a new model goes into production at a key domestic plant, and workers from other plants that will make that vehicle train initially in Japan and then take that knowledge back to the foreign facility.
How well do you really know your competitors?
Access the most comprehensive Company Profiles on the market, powered by GlobalData. Save hours of research. Gain competitive edge.
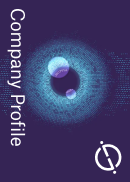
Thank you!
Your download email will arrive shortly
Not ready to buy yet? Download a free sample
We are confident about the unique quality of our Company Profiles. However, we want you to make the most beneficial decision for your business, so we offer a free sample that you can download by submitting the below form
By GlobalDataBut Japanese trainers and those in the domestic plants charged with liaising with overseas plants, faced time pressures and could not always give foreign production issues the time required.
Toyota Motor Europe president Shinichi Sasaki said that the GPC system gives trainers more flexibility and autonomy to adapt training locally to better suit their own plants. He noted that plants abroad may build multiple models built by several different Japanese ‘mother plants’. Burnsaston, albeit in two separate assembly halls, builds both the Corolla hatchback and full Avensis line, for example, and that can add problems if help is required from multiple domestic plants.
Trainers from the overseas plants can now learn new processes quickly, in Japan if necessary, quickly adapt their new knowledge to suit their own plants and then ‘cascade’ that knowledge from their strategically placed GPCs to local workers, supervisors and managers.
In Europe that includes Burnsaston and its associated engine plant on Deeside, the Yaris plant in France, the Corolla sedan, wagon and Verso plant in Turkey and an engine and gearbox factory in Poland but not yet the Aygo joint venture plant with PSA in the Czech Republic. It has not been decided if the UK facility’s training will extend to the Camry assembly plant in Russia scheduled to open in 2007.
“Training could be difficult to manage at times,” Sasaki said of the original mother plant system. “The GPC idea is more efficient support globally.”
But he added: “GPC is not the opposite of the mother plant system. It will support the mother plant concept, reinforcing the efficiency of the training.”
To adapt a phrase once used by US president John F Kennedy about divided Cold War Berlin, “If any man doubt that contemporary automotive assembly is a highly-skilled business, let him come to Burnaston.”
The 8,000m2 facility replicates most things you might want to learn before attempting to weld, paint, assemble and inspect a shiny new Corolla or Avensis rolling off the line at a rate of up to 300 a day.
It also trains those who assemble, dress and test engines, maintain production equipment, ‘train’ robots, programme vehicle and component sequencing equipment, or work in the formidable logistics system that uses ‘just-in-time’ techniques to ship parts in from suppliers and get them to the right part of the plant without using an on-site warehouse.
Two skill areas stood out during just-auto’s tour. One is the six-grade inspection process for freshly-pressed steel body panels – with a conveyor belt moving at the same rate as those bringing panels from the stampers in the car plant next door.
Not one journalist could spot a single defect on a level five panel (one is the easiest to see with a naked eye). No new employee is allowed near the plant till he can consistently pick defects at level four. Trainees are also taught to weld (gas and spot) and affix panels such as doors using body shells and line-side jigs and tools fully representative of those in the adjacent assembly plant.
Paint inspection training is done in a full-size bay lit up like the sun; training for paint spraying the few areas no Toyota robot yet goes (like under the bonnet) is done by applying water to a clear acrylic panel – this apparently is very close to doing the real thing and avoids the cost and risk of using actual paint and fume extraction in the training facility.
The second impressive skill is visual gap measuring – does that bonnet line up with the adjacent front guard? A clever machine varies panel gaps and alignment and trainees don’t get a ‘pass’ grade till they can accurately determine a gap is plus or minus 0.2mm of specification (4.5mm) 10 times in a row. In the plant they have 30-40 cars an hour to eyeball, averaging 15 seconds of inspection time per item. Hence the two hours maximum time per shift on any one inspection item.
Elsewhere in the GPC we saw trainees learning to insert and tighten various fastenings on moving trolleys designed to simulate a car on a moving assembly line – the tools and parts they need for the tasks attach to the car’s support carrier and move along the line with it.
Other trainees learn to drive forklifts and other material conveyances, operate complex plastic moulding and bonding machines (Burnaston does its own dashboard and bumper plastics in-house) and assemble engines.
Plant maintenance people learn to programme robots to handle, place, install parts, paint and weld, and how to operate complex hydraulic and pneumatic equipment and set up complex parts and vehicle sequencing.
We also noted an encouraging interest in line worker health. Car assembly is a repetitive-task business so, before a E-GPC training session begins, employees learn to manipulate a handful of golf balls to ‘warm up’ key arm, wrist and hand muscles. In the plant, special devices using wax and paraffin are available for similar pre-shift warm-ups.
During a plant tour, Toyota officials were also keen to point out such labour saving devices as seats that swing operators into car bodies to best position them for installing parts (Nissan’s UK plant also uses these), and the boxes of pre-sorted small parts and fastenings that are placed in a car early during its trip down the trim line so the operator doesn’t have to keep reaching out to line-side bins.
Graeme Roberts
Images: Graeme Roberts