The automotive industry is literally awash with new techniques and processes
for painting cars better. Each development is more ingenious than the last yet
few have succeeded in gaining widespread adoption. Trends are just starting
to emerge, however, and they are largely driven by the industry’s need to clean
up its plants. Anna Kochan reports.
Regulatory driver for clean paints
The driving force in Europe is essentially new EU legislation that comes
into effect in 2007 and that places stringent demands on automakers to reduce
VOC (volatile organic compound) emissions from paint plants. As a result, automakers
have been changing over, en masse, from solvent-borne coatings to water-borne
coatings, at least for the colour coat of the three-coat automotive paint process.
Also known as the base coat, the colour coat is responsible for the bulk of
the undesirable VOC emissions and has thus been the target of the most effort.
The change from a solvent- to a water-borne base coat does not require particularly
ingenious solutions, although investment is likely to be involved because of
the longer drying times of the water-borne materials and the need for equipment
made from stainless steel. Local regulations in Germany mean that all automotive
paint plants in Germany already meet the forthcoming EU standard, says Dr Thomas
Lueb, head of OEM marketing europe at BASF Coatings. He estimates that only
a few paint plants, perhaps around 10, still have to comply with the new EU
rules, and these are mainly in France, Spain and the UK.
Two of the first ingenious ‘clean’ paint concepts to attract interest from
the automotive industry were based on powder paint material and both are now
looking to have a future. Powder paint is the most environment-friendly of all
coating materials because it is completely solvent-free whereas a water-borne
paint still contains 10% solvent. In 1996, BMW began operating a highly innovative
paint line at Dingolfing that uses powder paint for the top coat (also known
as clear coat) of the 3-, 5- and 7-series models. The main suppliers involved
were Durr (for equipment) and PPG (for paint materials). And shortly afterwards,
Mercedes’ Rastatt plant implemented a similarly innovative process for a powder
slurry top coat with the introduction of the A-class.
How well do you really know your competitors?
Access the most comprehensive Company Profiles on the market, powered by GlobalData. Save hours of research. Gain competitive edge.
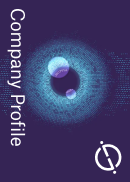
Thank you!
Your download email will arrive shortly
Not ready to buy yet? Download a free sample
We are confident about the unique quality of our Company Profiles. However, we want you to make the most beneficial decision for your business, so we offer a free sample that you can download by submitting the below form
By GlobalDataBASF developed the powder slurry material. Although neither of the solutions
appears to have attracted interest from other automakers, both BMW and Mercedes
have announced further investments in their powder paint technologies within
the last 12 months. BMW has indicated that it will adopt the powder paint process
at its new Leipzig plant. And Mercedes is expanding its powder paint application
at Rastatt with the introduction of the new A-class. BASF claims to have developed
a second generation powder slurry process for the new A-class that resolves
all the previous issues of appearance and scratch and chemical resistance. “The
quality of finish is now among the best that exists in the automotive industry,”
claims Dr Lueb.
Powder paint is by far the most environment-friendly coating material and could
dominate the automotive coatings market one day. As discussed above, proven
solutions for the top clear coat exist. For the primer coat, several applications
are also operating, particularly in GM and DaimlerChrysler plants in North America.
However, the technology to change colours with powder coating systems is not
yet fully proven. Paint specialist Haden is working on a solution but until
they have the answer, powder is not yet a real option for colour base coats
or for primers that are colour-matched to the base coat.
Colour changeover is a challenge
One of the challenges that continue to bug the automotive industry is how
to deal with mixed coloured cars coming down the line. The problem is that by
cleaning out the equipment to ensure that one colour of paint does not contaminate
another, a certain amount of paint is lost. Yann Vincent, manager of Renault‘s
Douai plant, estimates that a colour changeover costs €10. Because of this
cost, the plant paints vehicles in a minimum batch size of five that are all
the same colour. By processing vehicles in batches, the paint shop represents
a major exception for the Douai facility because in all the other areas, the
focus is on adhering to a production sequence that matches customer orders exactly.
With many OEMs moving over to build-to-order concepts, the cost of colour-changeover
has become a more important issue. In answer to this, Toyota and ABB Japan have
collaborated on a paint cartridge system that can paint every car a different
colour without any wastage. It is one of the industry’s new and ingenious technologies
that are starting to gain some success. Toyota obviously had a head start with
the technology and has installed it at several plants around the world including
the Inabe factory in Japan and the Valenciennes facility in France.
Two years ago, ABB started marketing the solution to OEMs other than Toyota
and has since made sales to Proton and to PSA. The French company is to install
the innovative CBS (cartridge bell system) at its Poissy plant over the next
two years on a new paint line it is building to complement the two existing
ones. The basic principal of the CBS concept is that each cartridge contains
enough paint for one coating operation on one vehicle. The painting robot, which
is a standard ABB model equipped with a special spray gun, automatically changes
cartridges between vehicles, and the cartridges are automatically refilled.
This all takes place within the cycle time of the production line. For colours
that are common the cartridges are dedicated. For others, the cartridges are
cleaned out between one colour and the next. PSA will use the CBS concept for
applying colour-matched primer and colour base coats, both of which are water-borne.
|
Chapter three
highlights recent technical advances in coating technology and manufacturing
processes. A combination of environmental and cost pressures is
driving new coatings technologies. As all vehicle makers are looking
to reduce the cost of painting a vehicle, coatings suppliers are
re-thinking the ‘total package’ rather than the cost of
a gallon of paint. New materials used in the manufacturing process,
low temperature cure, water-based and powder coatings are also influencing
their research efforts in North America and Europe.
Chapter four
provides you with brief profiles of the major paint manufacturers,
BASF, DuPont and PPG. Click
here to learn more.
![]() | ![]() |
CBS also solves one of the problems associated with water-borne paints, which
is that they conduct electricity whereas solvent-borne paints do not. This is
important because, for the electrostatic spray painting process in current use,
the paint has to be electrically charged. According to ABB’s Philippe Alluyn,
PSA has shown that the insulated design of the CBS gives a 3% increase in application
efficiency and requires less maintenance compared to the alternative solutions
for applying water-borne paints. This, he adds, is in fact the main reason behind
PSA’s decision to opt for the new technology.
Evolving role of the supplier
Alongside the barrage of new paint materials and processes, one very strong
trend that is emerging is the evolving role of the supplier. OEMs are increasingly
subcontracting the management of paint materials to their paint suppliers. “Core
competence is the issue here,” comments BASF’s Dr Lueb. “Combining
our competence in the area of chemicals with the OEM’s expertise in building
cars is the most efficient solution,” he believes.
Since the end of the 90s, BASF has been entering into system supply agreements
with its European customers, a practice that has been recently spreading to
China, Japan and South America, and is also beginning in the NAFTA region. “New
plants in particular are awarding these forms of contract as they do not already
have teams of personnel employed in paint management functions,” Dr Lueb
reports. While the OEM is responsible for running the paint process, it is the
role of the supplier to take responsibility for the paint materials, the material
handling and logistics functions, the quality control lab and all paint-related
consulting services. In most cases, BASF is paid according to the number of
cars painted rather than according to material consumed. The OEM and its supplier
set annual cost reduction targets for the total process varying from 0.5% to
5%, depending on the paint shop.
Eisenmann, the German equipment company, has taken the paint shop supplier
role even further. At Smart’s Hambach plant, Seat’s Martorell facility and Volkswagen‘s
factory in Brazil, Eisenmann operates contracts whereby it retains ownership
of the paint shop. It operates the facility and is paid per unit.
It is clear that paint shop concepts are in constant evolution.